Why anodize aluminum? This common question arises when considering the finishing options for aluminum products. Anodizing aluminum enhances its durability and appearance, making it a popular choice for various applications.
In crafting this comprehensive guide, we meticulously analyzed industry standards and consulted with material science experts. Our focus was on practical benefits and technological advancements in aluminum anodizing.
Here is a sneak peek at 2 of the reasons why anodizing aluminum is beneficial:
- Cost-Effective
- Low Maintenance
In this article, we’ll dive deeper into the fascinating world of aluminum anodizing, exploring its wide-ranging advantages and applications.
So keep reading to learn more.
1. Cost Effective
Anodizing aluminum is not just about enhancing its appearance; it’s a smart financial decision too. Here are the key reasons why anodizing aluminum is cost-effective:
- Extended Lifespan: Anodized aluminum lasts longer due to its increased resistance to wear and tear. This durability means less need for replacements or repairs, leading to significant savings over time. Think about it like investing in a high-quality tool that doesn’t need constant replacing.
- Low Maintenance Costs: The anodized layer is incredibly tough and resists damage from environmental factors like UV rays and corrosion. This means less money spent on upkeep and maintenance, freeing up budgets for other important tasks.
- Increased Efficiency in Manufacturing: The anodizing process can be integrated smoothly into existing production lines. This efficiency reduces labor costs and speeds up production, lowering the overall manufacturing expenses. Zemetal leverages this efficiency to provide cost-effective and high-quality anodized aluminum products.
2. Low Maintenance
Anodized aluminum is renowned for its low maintenance and durability, making it perfect for applications needing minimal upkeep. Here are the reasons why anodized aluminum is a low-maintenance material:
- Resistance to Corrosion: The anodizing process gives aluminum a protective layer, making it highly resistant to rust and corrosion. This is especially beneficial in humid or salty environments, where other metals might worsen quickly. You won’t have to worry about frequent touch-ups or rust-proofing treatments.
- Surface Hardness: Anodized aluminum has a significantly harder surface compared to untreated aluminum. This enhanced hardness makes it less susceptible to scratches, abrasions, and wear from daily use. It’s tough enough to withstand the hardness of daily activities without showing signs of distress.
- Color Stability: The color of anodized aluminum does not fade over time, even when exposed to sunlight. This means that the visual appearance remains consistent, reducing the need for repainting or refinishing to maintain its aesthetic appeal.
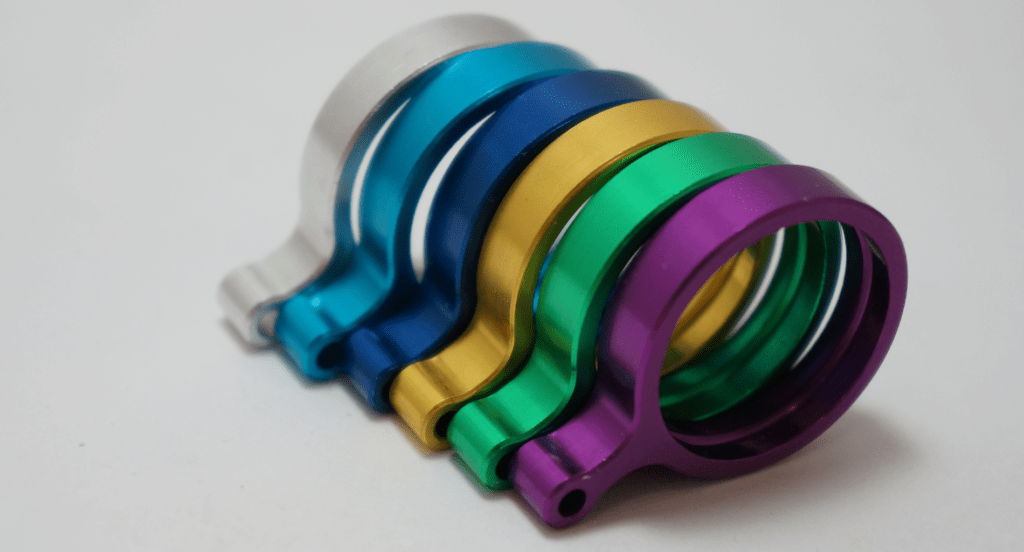
- Easy Cleaning: Dirt and stains on anodized aluminum can be easily cleaned with water and mild detergents. There’s no need for strong chemicals or abrasive cleaning methods, simplifying the maintenance process and saving time and resources.
3. Thermal Insulation
Anodized aluminum excels in durability and thermal insulation, making it ideal for efficient heat management in diverse applications. Here are the reasons why anodized aluminum is good for thermal insulation:
- Reflective Properties: Anodized aluminum reflects a significant amount of radiant heat, making it an excellent choice for applications requiring heat deflection. This reflective ability helps maintain temperature stability in environments exposed to varying heat conditions.
- Conductive yet Controllable: While aluminum is a good conductor of heat, the anodizing process modifies the surface, making it less conductive. This controlled conductivity is beneficial in applications where heat dissipation is necessary but needs to be managed effectively.
- Compatibility with Insulating Materials: Anodized aluminum can be easily combined with other insulating materials to enhance its thermal insulation properties. Isn’t it great how versatile it is? This compatibility allows for flexible design options in thermal management systems.
- Stability Under Temperature Fluctuations: Anodized aluminum maintains its structural integrity and insulation properties even under extreme temperature variations. This stability ensures long-term performance in applications that experience wide temperature ranges.
4. Increased Durability
Anodizing greatly enhances the durability of aluminum, making it a robust choice for numerous applications. Here are the key ways in which anodizing aluminum contributes to its increased durability:
- Hardened Surface: The anodizing process creates a layer of aluminum that is harder than a lot of steel. This hardened surface is highly resistant to scratches and wear, ensuring that products maintain their integrity and appearance over time.
- Protection Against Corrosion: By anodize aluminum, it gains a protective layer that is highly resistant to corrosion. This is particularly beneficial in environments that are harsh or have high moisture levels, for instance, extending the life of aluminum products significantly.
- Improved Weather Resistance: Anodized aluminum withstands environmental elements, including UV rays and extreme temperatures, without deteriorating. It’s like having a superhero shield for your materials! This makes it ideal for outdoor applications where other materials might weaken or degrade.
- Enhanced Structural Rigidity: The anodizing process not only adds a protective layer but also can increase the structural rigidity of aluminum. This additional strength is crucial in applications where mechanical stress and impact resistance are important.
5. Eco-Friendly and Safe
Anodized aluminum is not just about strength and aesthetics; it’s also a green and safe choice. Here are the reasons why anodizing aluminum is eco-friendly and safe:
- Non-Toxic Process: The anodizing process is a safe procedure that doesn’t involve any heavy metals or toxic chemicals. It’s reassuring to know that choosing anodized aluminum means making a responsible choice for our planet and its inhabitants.
- Recyclability: Anodized aluminum stands out for its 100% recyclability and enduring properties, maintaining its quality without degradation. As Building Enclosure Online notes, aluminum is the third most plentiful element on earth, and anodized aluminum, in particular, holds a higher dollar value than scrap painted aluminum, underscoring its durability and economic value.
- Longevity Reduces Waste: The increased durability of anodized aluminum means products last longer, reducing the frequency of replacement and the associated environmental impact. This longevity is a key factor in sustainable manufacturing and consumption.
- Safe for Food Contact: Anodized aluminum is safe for food contact, as it doesn’t leach harmful substances into the food, making it ideal for cookware, utensils, and food processing equipment. This safety aspect is essential for consumer health and well-being.
6. Enhanced Aesthetic Appeal
Anodized aluminum isn’t just about functionality; it also offers a distinct aesthetic appeal. Here’s how anodizing enhances the visual allure of aluminum:
- Variety of Colors and Finishes: Anodizing allows for a wide range of colors and finishes on aluminum surfaces, enhancing aluminum uses in architecture. This versatility means that anodized aluminum can be tailored to suit specific design preferences, making it ideal for decorative and architectural applications.
- Uniform and Consistent Appearance: The anodizing process ensures a consistent and uniform coating, providing a sleek and professional finish. It’s truly amazing how this process can transform the look and feel of aluminum. This uniformity is crucial for applications where appearance is as important as performance.
- Improved Surface Texture: Anodizing can alter the surface texture of aluminum, giving it a more refined or distinct touch, for example, creating a smooth matte finish or a sleek glossy one. This improved texture can enhance the tactile experience and overall perception of quality.
- Light Interplay and Reflection: The unique properties of anodized aluminum allow it to interact with light in interesting ways, whether reflecting or diffusing it. This characteristic can add a dynamic element to its appearance, changing subtly with the lighting conditions.
7. Better Adhesion for Coatings
Anodized aluminum is highly regarded for its ability to bond well with coatings, enhancing both functionality and aesthetics. Here are the reasons why anodized aluminum offers better adhesion for coatings:
- Porous Surface Structure: The anodizing process creates a porous surface on aluminum, which allows coatings to adhere more effectively. This strong adhesion ensures that paints, sealants, and other coatings stay intact for longer periods, maintaining their appearance and protective qualities.
- Improved Paint Retention: Anodized aluminum’s surface enables better retention of paint and other coatings. This means that the coatings are less likely to chip, peel, or fade over time, ensuring a long-lasting finish that requires less frequent touch-ups. Imagine the satisfaction of seeing your project stay vibrant and fresh-looking year after year!
- Enhanced Protection from the Elements: Coatings on anodized aluminum bond deeply with the surface, providing superior protection from environmental factors like UV rays, moisture, and temperature fluctuations. This enhanced protection is crucial for outdoor or harsh environment applications.
- Compatibility with a Wide Range of Coatings: The anodized surface is compatible with various types of coatings, including powder coatings, liquid paints, and adhesive films. This versatility allows for a wide range of applications and design options, catering to different industry needs.
8. Enhanced Electrical Insulation
Anodized aluminum is highly valued for its enhanced electrical insulation properties, making it suitable for various electrical and electronic applications. Here are the key reasons for its effectiveness in electrical insulation:
- Non-Conductive Layer: The anodization process forms an oxide layer on the aluminum surface, which is non-conductive. This layer significantly increases the electrical resistance of the material, making it an excellent insulator for electrical applications.
- Stability in Electrical Environments: Anodized aluminum maintains its insulating properties across a range of electrical conditions. It performs consistently in various voltages and frequencies, ensuring reliability in diverse electrical applications.
- Heat Dissipation Properties: While providing electrical insulation, anodized aluminum also effectively dissipates heat. This dual property is crucial in electronic components, where both insulation and heat management are necessary to prevent overheating and ensure the longevity of the devices.
- Durability in Electrical Applications: The robust nature of the anodized layer means it can withstand the rigors of electrical environments, including exposure to electromagnetic fields and fluctuating currents, without degradation of its insulating properties. This resilience is what sets anodized aluminum apart in the world of electrical applications.
This table presents the key aspects of anodized aluminum’s durability in electrical applications, emphasizing its resilience and suitability in challenging electrical environments.
Aspect | Description | Significance in Electrical Applications |
Resistance to Electromagnetic Fields | Unaffected by electromagnetic interference | Ensures stable performance in electrical systems |
Stability Under Fluctuating Currents | Maintains integrity despite current variations | Critical for reliability in power applications |
Insulating Properties Preservation | Insulation remains effective over time | Essential for safety and efficiency |
Corrosion Resistance | Withstands harsh environments without corroding | Prolongs lifespan in outdoor applications |
Mechanical Durability | Resists physical stress and wear | Suitable for high-use electrical components |
9. Improved Corrosion Resistance
Anodized aluminum is renowned for its enhanced corrosion resistance, making it a resilient choice in challenging environments. Here are the key aspects that contribute to its improved corrosion resistance:
- Oxide Layer Barrier: Anodizing creates a thick oxide layer that acts as a barrier against corrosion. This layer is much thicker and more durable than the natural oxide layer that forms on untreated aluminum, offering superior protection against corrosive elements.It’s like giving aluminum a super-powered shield against the elements!
- Resistance to Harsh Chemicals: The anodized surface is highly resistant to many harsh chemicals, making it ideal for use in environments where chemical exposure is a concern. This resistance helps prevent deterioration and maintains the integrity of aluminum over time.
- Suitability for Marine and Industrial Environments: The corrosion resistance of anodized aluminum makes it particularly suitable for marine and industrial settings, where exposure to saltwater and industrial pollutants is common. This property extends the lifespan of components and structures in these harsh conditions.
- Sealing Process Enhances Protection: After anodizing, the aluminum can be sealed, further enhancing its corrosion resistance. This sealing process closes off the pores in the oxide layer, adding an additional level of protection against corrosive agents. Zemetal offers expert sealing services to ensure maximum durability for your anodized aluminum products.
Conclusion
In conclusion, this guide highlights the remarkable benefits of anodized aluminum, showcasing its versatility and value in various applications. From enhanced durability to eco-friendliness, anodized aluminum stands as a superior material choice.
If you’re looking to harness these benefits for your projects, consider Zemetal for top-quality anodized aluminum solutions. For more information or to start your next project, feel free to contact us.
Dive Deeper Into Our Resources
Looking for more diverse service options? Browse through our handpicked selections:
For some insightful reads, we’ve curated a list of recommended articles just for you:
Still haven’t found what you’re looking for? Don’t hesitate to contact us. We’re available around the clock to assist you.