Has anyone ever wondered how detailed metal shapes are so precisely cut? The answer lies in the innovative water jet CNC technology, transforming metal fabrication with its precision and versatility.
With years of experience in the metal fabrication industry, I bring a depth of knowledge and insight into the transformative power of advanced technologies.
Water jet CNC is more than a tool; it’s a game-changer in the fabrication world. Its ability to cut various materials with precision makes it vital for competitive, innovative businesses.
In this guide, you’ll delve into the workings, advantages, and practical applications of water jet CNC, gaining a comprehensive understanding that will inform and enhance your operational decisions.
Read on to navigate the depths of water jet CNC technology.
1. Overview of Water Jet CNC
Water jet CNC technology, renowned for its precision engineering capabilities, is witnessing significant market growth, reflecting its increasing importance across various industries. Technavio’s market analysis predicts a robust 6.52% CAGR increase from 2022 to 2027. This surge underscores the method’s high-pressure precision and ability to cut various materials, from metals to composites, without compromising their integrity.
Technology’s cold-cutting nature, avoiding heat-affected zones, is crucial for industries like aerospace and manufacturing, where material preservation is paramount. As the market continues to expand, water jet CNC’s blend of versatility, precision, and material conservation is set to further transfrom quality, efficiency, and innovation in precision engineering.
2. The Mechanics of Water Jet CNC
Having explored the broad benefits and applications of Water Jet CNC in various industries, it’s crucial to understand the detailed mechanics that enable its precision and versatility. Here are the key components that drive this powerful technology:
High-Pressure Pump: The Power Source
The heart of any water jet CNC machine is the high-pressure pump, which propels water at speeds capable of cutting through steel and stone. This pump generates pressure up to 90,000 psi, transforming ordinary water into a precise cutting tool. The intensity and consistency of the pump not only determine the cutting speed but also the thickness and intricacy of materials that can be handled, making it a critical component in the process.
Abrasive Delivery System: The Cutting Edge
The abrasive delivery system is what truly amplifies the water jet’s cutting power. By precisely feeding abrasive particles like garnet into the water stream, it allows for the meticulous slicing of tougher materials. This system’s precision ensures that the right amount of abrasive is used for each cut, optimizing efficiency and quality.
CNC Software: Guiding Precision
Behind every precise cut is a sophisticated CNC software, directing the jet’s path with exacting accuracy. This software translates detailed designs into reality, allowing for complex patterns and shapes with minimal material waste. The precision of this system is not just about following a path; it’s about replicating detailed designs consistently and efficiently, essential in custom manufacturing and design projects.
3. Advantages of Water Jet CNC
Water Jet CNC technology is not just about cutting through materials; it’s about redefining precision and efficiency. Let’s explore the key advantages that set it apart in the metal fabrication industry:
No Heat-Affected Zones (HAZ)
One of the standout benefits of Water Jet CNC is its cold-cutting method, which eliminates heat-affected zones. This means the integrity of the material remains intact, preserving its strength and properties. The absence of HAZ not only ensures a superior finish but also reduces the need for secondary finishing processes, enhancing overall efficiency and productivity.
Exceptional Precision and Versatility
Water Jet CNC technology is renowned for its exceptional precision, capable of producing detailed designs that other cutting methods can’t achieve. It can handle a wide range of materials, from metals to glass, without compromising on accuracy. This versatility ensures that Zemetal, can cater to diverse customer needs and complex projects with ease, maintaining high standards of quality and precision.
Enhanced Operator Safety and Environmental Sustainability
Safety and sustainability are at the forefront of Water Jet CNC technology. Its operation does not produce harmful gases or dust, making it a safer choice for operators and reducing the environmental impact. Furthermore, the lack of heat generation ensures a safer workplace and minimizes energy consumption, aligning with the eco-friendly practices of companies committed to a greener future.
4. Materials Compatible with Water Jet CNC
Water Jet CNC technology is celebrated for its wide-ranging compatibility with various materials. Here’s a look at some materials that this versatile cutting tool can handle with ease:
- Titanium: Known for its strength and lightweight properties, titanium is often used in aerospace and medical industries. Water Jet CNC can cut titanium without altering its intrinsic properties, making it ideal for producing aircraft parts and medical implants.
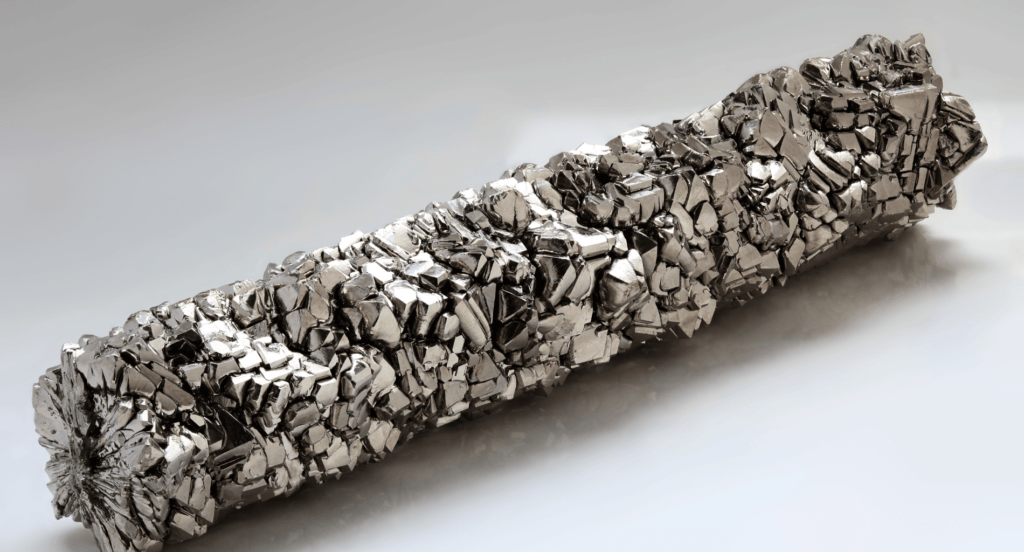
- Carbon Fiber: Used extensively in automotive and aerospace industries for its high strength-to-weight ratio, carbon fiber can be cut cleanly by Water Jet CNC without fraying or delamination.
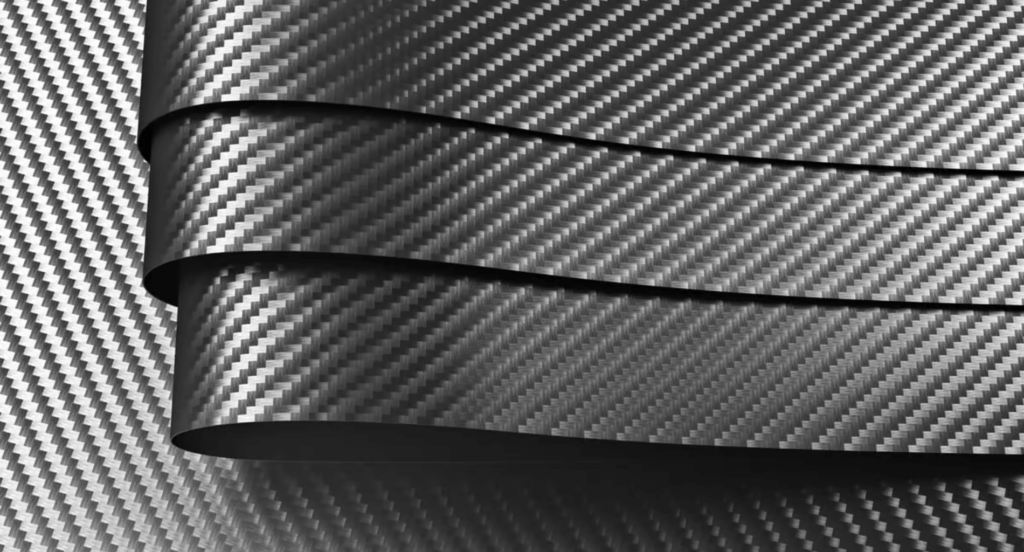
- Alloy Steels: Water Jet CNC cuts through alloy steels without heat-affected zones, maintaining the metal’s hardness and strength. This capability is particularly beneficial in the manufacturing of machinery and automotive components, where maintaining the steel’s properties is critical.
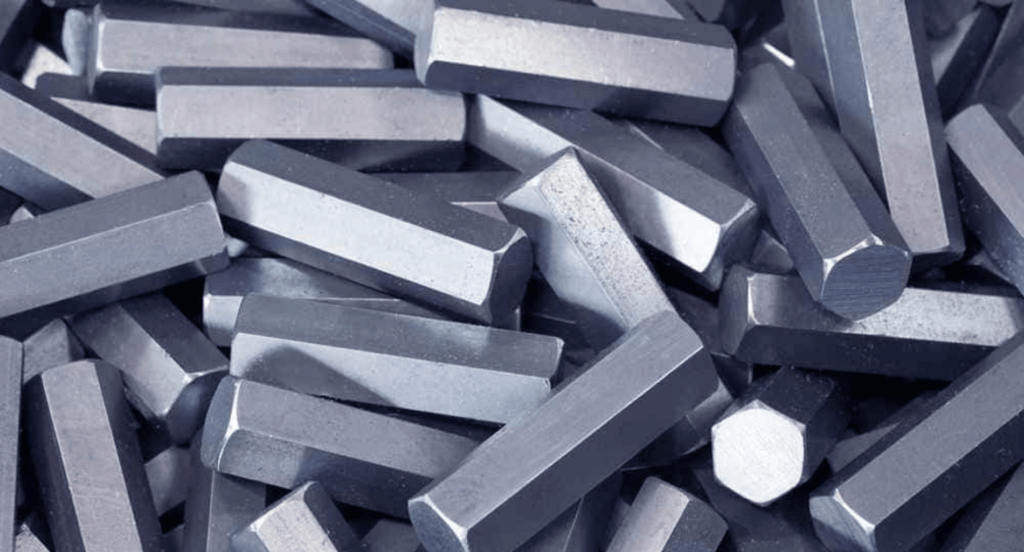
- Glass: Cutting glass requires precision and a gentle touch. Water Jet CNC can slice through glass cleanly and accurately, making it ideal for creating custom windows, mirrors, and artistic installations.
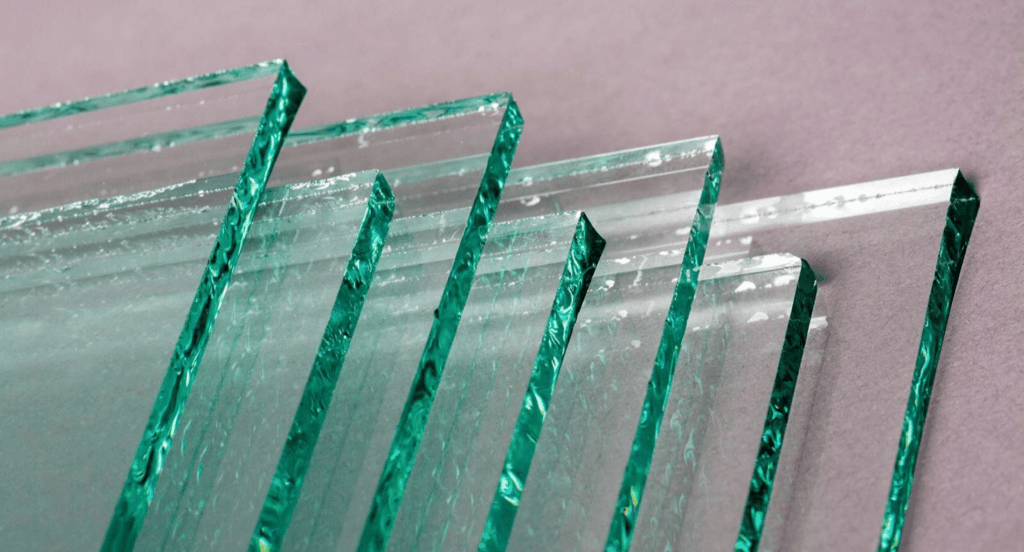
- Ceramics: Ceramics are challenging to cut due to their brittleness, but Water Jet CNC can handle them with ease, producing precise cuts without cracks or chips, often used in the production of tiles and decorative elements.
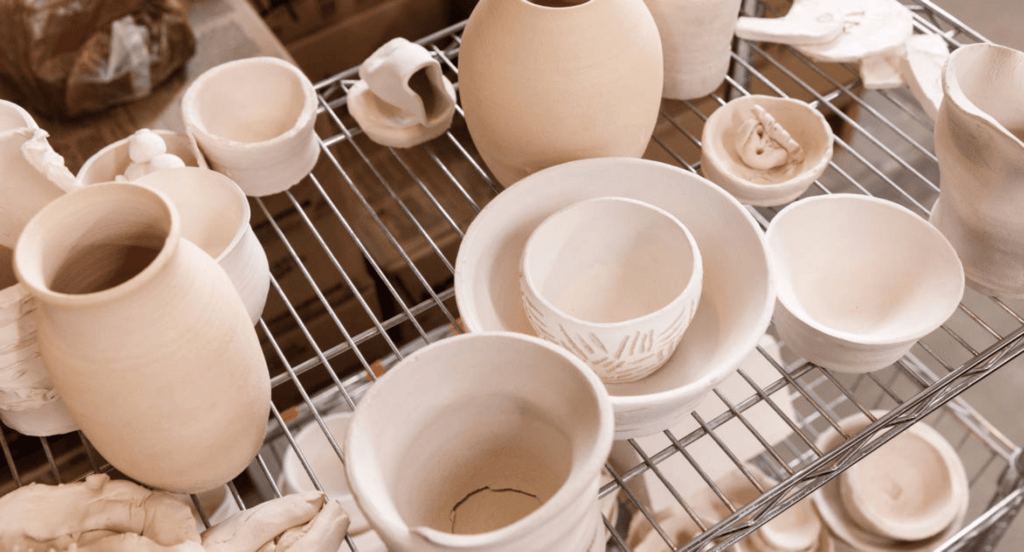
5. Applications of Water Jet CNC in Various Industries
Building on the diverse materials compatible with Water Jet CNC, this technology’s applications extend into various sectors, each benefiting from its precision and versatility. Let’s explore the specific industries where Water Jet CNC is making a significant impact and driving innovation:
Manufacturing and Fabrication Industry
In the world of manufacturing and fabrication, Water Jet CNC’s ability to handle a vast range of materials is invaluable. It’s used to cut parts for machinery, create custom tools, and produce detailed components for electronics. The technology’s adaptability and precision ensure that regardless of the project’s scale or complexity, the end result meets the highest standards of quality and performance.
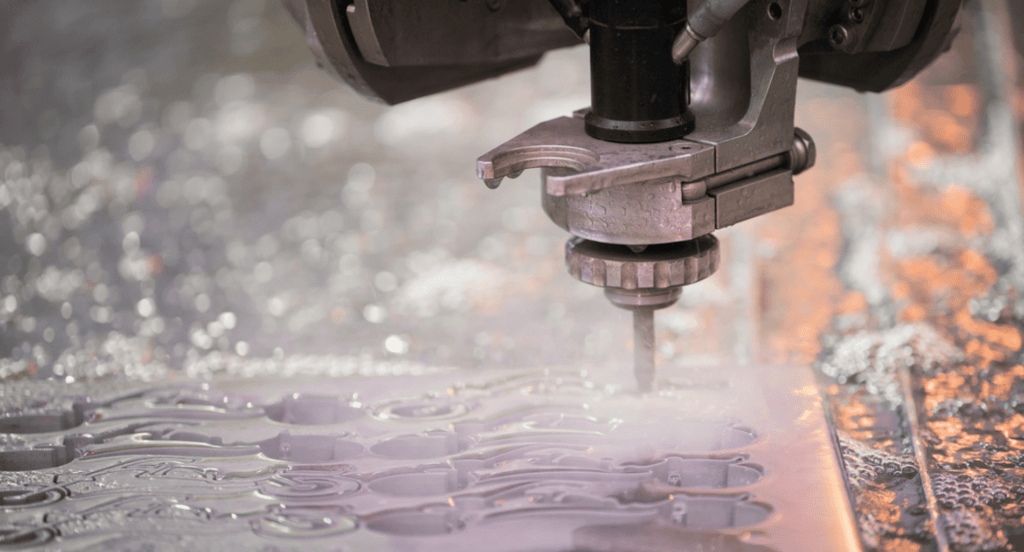
Architecture and Construction Industry
The architecture and construction sectors benefit greatly from Water Jet CNC’s ability to cleanly cut through stone, metal, and glass. Zemetal utilizes this technology to create detailed designs and patterns for building facades, custom tiles, and ornamental features. The precision and versatility of Water Jet CNC allow for the realization of complex architectural visions.
Aerospace and Automotive Industry
In the aerospace and automotive industries, precision is paramount. Water Jet CNC is used to cut, shape, and form parts with exact specifications, from detailed engine components to custom interior designs. The technology’s ability to cut without inducing heat stress is crucial for maintaining the integrity of high-performance materials used in planes and vehicles.
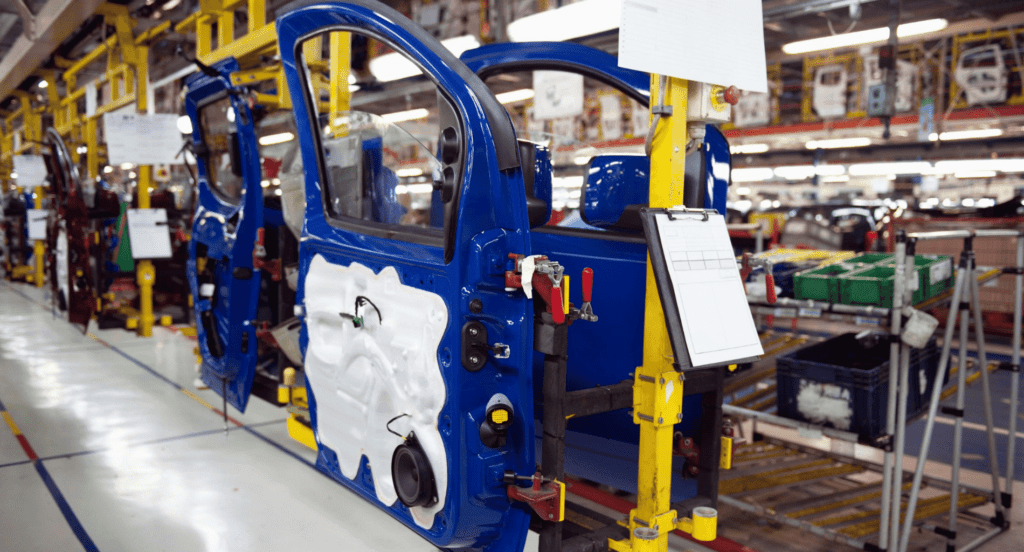
6. Challenges and Limitations of Water Jet CNC Technology
While Water Jet CNC technology offers numerous advantages, it’s also accompanied by certain challenges and limitations. Here’s a closer look at these issues, along with potential solutions to mitigate them:
Initial Investment Cost
The initial investment cost for Water Jet CNC machinery can be challenging for many small to mid-sized businesses. The cost includes not just the machine itself but also installation and infrastructure modifications. To overcome this, businesses can explore financing options, grants, or subsidies available for technology upgrades. Leasing equipment or purchasing rebuilt models can also be more cost-effective.
Maintenance and Upkeep
Regular maintenance is crucial for Water Jet CNC machines to operate at their best. High-pressure parts and abrasives degrade over time, leading to expensive, frequent servicing. To address this, establishing a routine maintenance schedule can prevent unexpected breakdowns and prolong the machine’s life. Training in-house staff to perform basic maintenance tasks can reduce the need for external services.
To maximize the efficiency of Water Jet CNC machines and minimize frequent servicing costs, regular maintenance is essential. The table below outlines key maintenance practices:
Maintenance Task | Frequency | Benefit |
Inspect high-pressure parts | Bi-weekly | Identifies wear early, prevents major failures |
Replace worn abrasives | Monthly | Ensures cutting precision, reduces waste |
Check water quality | Weekly | Protects against corrosion, maintains efficiency |
Lubricate moving parts | Monthly | Prevents mechanical wear, extends lifespan |
Train staff in basic upkeep | As needed | Reduces dependency on external services |
Operational Expertise
Water Jet CNC technology requires a certain level of expertise to operate effectively. Skilled technicians are vital to manage the machine’s complexities, making it challenging to find and retain qualified staff. Investing in comprehensive training programs for existing staff can build the necessary expertise within the organization. Additionally, manufacturers can provide detailed guides and support to help businesses quickly adapt.
7. Innovations and Future Trends in Water Jet CNC
As we navigate the challenges and limitations of Water Jet CNC technology, it’s exciting to look ahead at the innovations and trends shaping its future. Here’s a glimpse into what’s on the horizon for this dynamic field:
Advanced Materials and Abrasives
Innovation in materials and abrasives is set to enhance Water Jet CNC’s capabilities. New composite abrasives are being developed to increase cutting speed and efficiency. For example, experimenting with different garnet grades or synthetic diamonds could offer faster, cleaner cuts, reducing operating costs and improving outcomes for industries like automotive and aerospace, where precision and material quality are paramount.
Integrated Systems and IoT
The future of Water Jet CNC sees it becoming more integrated with the Internet of Things (IoT) and smart factory setups. This integration will allow for real-time monitoring and adjustments, significantly improving efficiency and predictive maintenance. For example, a CNC machine might detect a wear issue and recalibrate its settings in real time to maintain optimal performance.
Compact and Portable Systems
Another trend is the development of compact, portable Water Jet CNC machines. These smaller units will offer the same precision and versatility but in a more accessible format, ideal for small-scale workshops or on-site projects. This advancement will open up Water Jet CNC technology to a broader range of users and applications, from small businesses to educational settings.
Conclusion
Navigating the details and potential of Water Jet CNC technology, it’s clear that its precision, versatility, and evolving nature make it an essential tool in modern fabrication. This guide aims to illuminate its capabilities and future, helping you understand how it can enhance your operations.
Consider Zemetal your partner in harnessing the full potential of Water Jet CNC for your business needs. To learn more or to discuss your specific requirements, feel free to contact us.
Dive Deeper Into Our Resources
Looking for more diverse service options? Browse through our handpicked selections:
For some insightful reads, we’ve curated a list of recommended articles just for you:
Still haven’t found what you’re looking for? Don’t hesitate to contact us. We’re available around the clock to assist you.