Are you exploring the most effective methods to enhance your product’s identification and branding? Understanding the key differences in laser marking and laser engraving can transform your approach.
In an industry where precision and quality are essential, being well-informed about these technologies ensures you stay ahead in the competitive market.
While laser marking slightly changes the material’s surface for identification or aesthetic purposes, laser engraving goes a step further by cutting into the material, offering depth and and long-lasting effects in its application.
In this guide, we will dive into laser marking and laser engraving, detailing their unique advantages and considerations, to provide a clear comparison between these two vital techniques.
Read on for a comprehensive comparison.
1. Overview of Laser Technology in Material Processing
Laser technology is a key player in today’s material processing, known for its accuracy and flexibility. It operates by focusing a high-intensity light beam to manipulate various materials, including metals. This method transformed traditional processing techniques, offering unmatched precision and efficiency.
The primary appeal of laser technology is its adaptability to diverse applications, including laser marking and engraving. While both processes utilize the concentrated power of lasers, they differ significantly in their approach and impact on materials. Understanding these differences is essential for selecting the most suitable method for specific industrial needs.
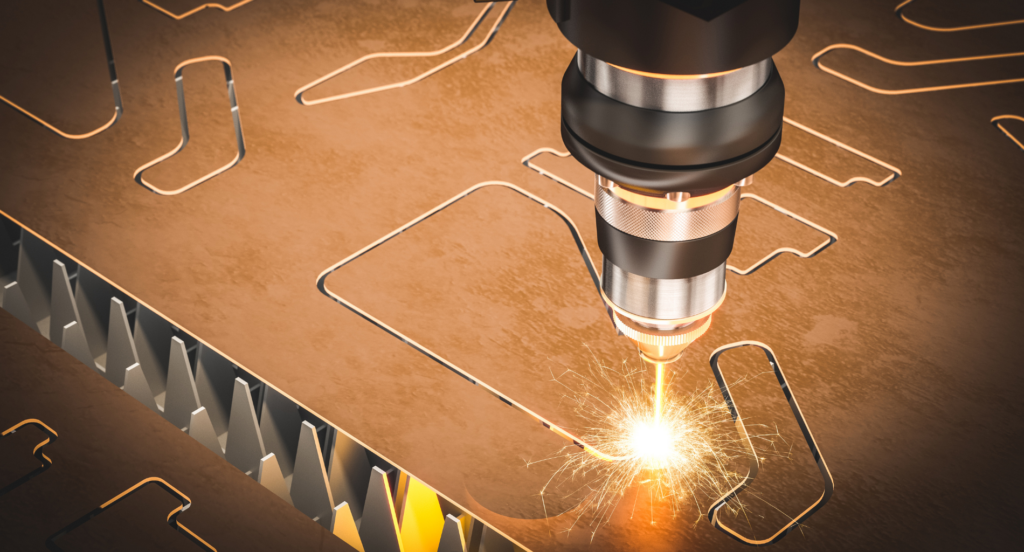
2. Understanding Laser Marking
Laser marking is a precise and efficient method used to apply permanent marks on metals. It involves changing the material’s surface through a non-contact process, producing high-resolution marks and maintaining material integrity. As per Mordor Intelligence, the laser marking market’s 5.8% CAGR (2023-2028) results from industry applications and enhanced marker functionality through R&D.
Types of Laser Marking
- Deep Laser Marking: This method engraves deeply into metal, creating durable and highly visible markings ideal for industrial environments where resistance to extreme conditions is needed.
- Surface Annealing: This is a technique that changes the color of the metal surface, like stainless steel, without actually engraving it, making it perfect for applications where surface integrity, such as in medical devices or kitchenware, is vital.
- Polishing Marking: Polishing marking creates a contrasting, shiny effect on metal surfaces. The laser selectively melts the surface, resulting in a smoother and slightly polished area that stands out against the matte background, commonly used in jewelry and high-end consumer electronics.
- Black Marking: Black marking is specifically for creating high-contrast, black marks on metal surfaces. This method is in high demand for creating barcodes and QR codes, as it ensures excellent readability. It’s particularly useful for tracking and identification purposes in automotive and aerospace industries.
- Frosted Marking: Frosted marking produces a matte, frosted appearance on metal surfaces, offering a unique aesthetic appeal. This technique is achieved by adjusting the laser to lightly etch the surface, creating a subtle, textured effect, ideal for decorative purposes in items like personalized gifts and awards.
Advantages of Laser Marking
- High-Resolution Markings: The high precision of laser marking allows for the creation of extremely detailed and clear markings, ensuring that even the smallest texts and complex graphics are legible, which is essential for traceability and branding.
- Durability and Resistance to Wear: Marks made by laser are naturally resistant to fading, wear, and environmental conditions, allowing the markings to remain readable and intact over an extended period, even under harsh operational conditions.
- Eco-Friendly Process: Laser marking is a non-contact process that doesn’t require inks, chemicals, or additional supplies. This minimizes waste and environmental impact, aligning with sustainability goals and reducing the need for consumables.
- Efficient and Cost-Effective for High Volume: Laser marking systems are capable of marking parts quickly and consistently, which is particularly ideal for high-volume production. This efficiency leads to reduced processing time per part, translating to lower operational costs and greater production capacity.
Disadvantages of Laser Marking
- Limited to Surface Marking: Laser marking does not engrave or etch deeply into materials. This limitation means it may not be suitable for applications requiring more than surface-level marking.
- Cost of Equipment: Initial investment in laser marking equipment can be high. This cost factor may be a consideration for smaller businesses or those with infrequent marketing needs.
- Material Restrictions: Not all materials are suitable for laser marking, with some metals potentially reacting negatively. This necessitates careful selection of materials for the process.
- Training and Safety Requirements: Operating laser marking equipment requires trained personnel and strict adherence to safety protocols. The need for specialized training and safety measures adds to operational considerations.
3. Exploring Laser Engraving
Laser engraving involves a high-precision process where parts of the metal surface are removed to create enduring and visible designs or text. This method is particularly valuable for producing detailed, permanent markings on items such as tools, components, and promotional materials. Its deep etching ability in diverse metals like aluminum and stainless steel ensures lasting, precise engravings, ideal for durable applications.
Types of Laser Engraving
- Ablation Engraving: This involves removing thin layers of coated or anodized metal to reveal the underlying material. It’s commonly used for labeling and branding on anodized aluminum, offering high contrast and excellent readability, making it ideal for creating QR codes and detailed graphics on various metal surfaces.
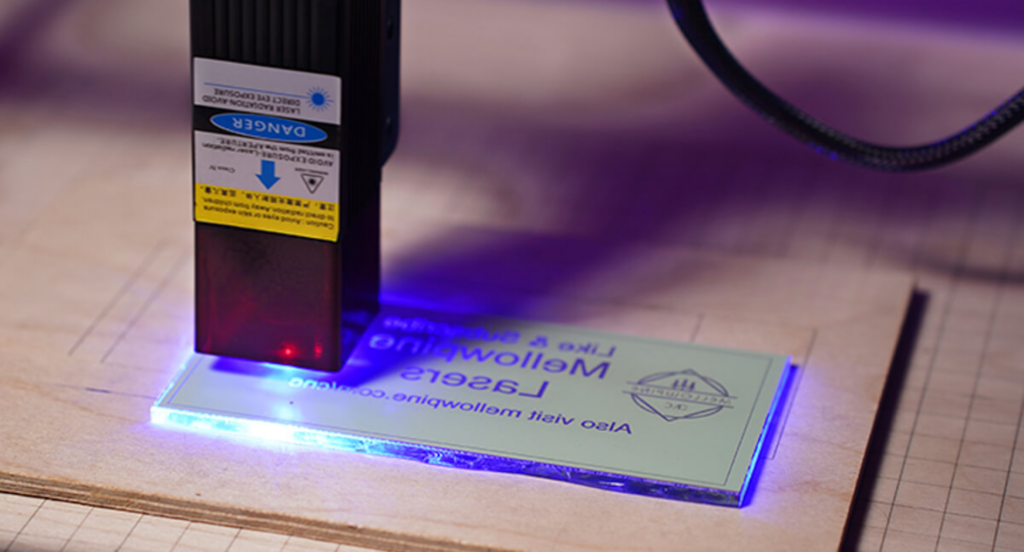
- Mirror Engraving: Mirror engraving involves creating reflective, mirror-like engravings on metal surfaces. This method is ideal for decorative and branding purposes, where a high-impact, eye-catching finish is desired. For example, it is commonly used in automotive parts, trophies, and premium promotional items.
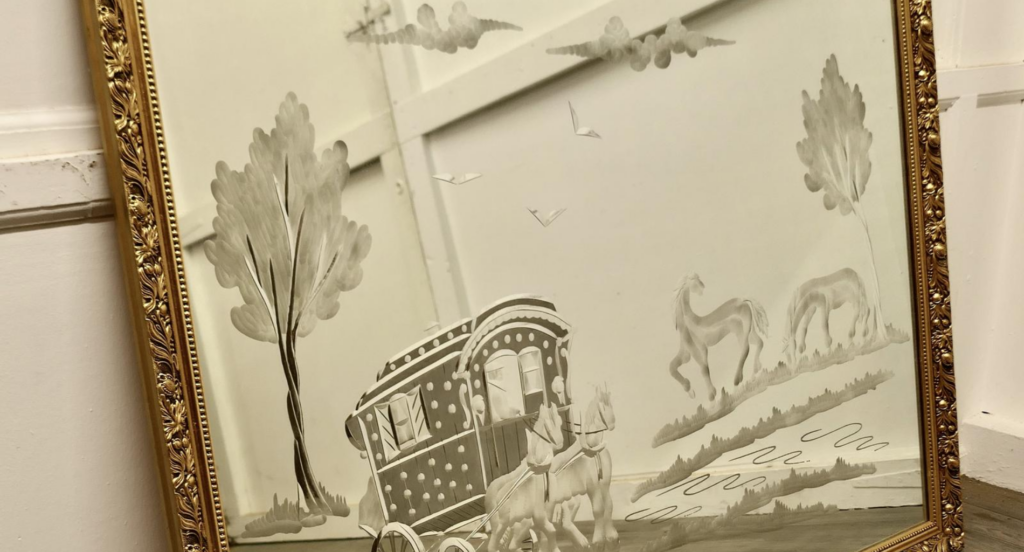
- Textured Engraving: Textured engraving creates a tactile, textured pattern on the metal surface. This method not only adds a visual element but also a physical dimension to the engraving, making it suitable for grip enhancements on tools, custom metal panels, and artistic installations.
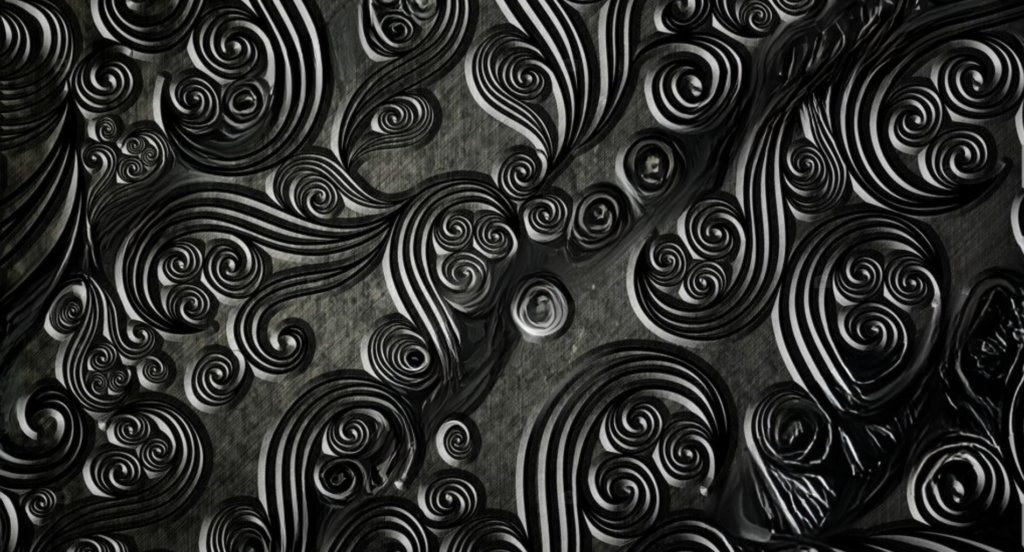
- Rotary Engraving: Thisis designed for cylindrical metal objects, where the laser system engraves around the circumference of the part. This is ideal for pipes, rings, and cylindrical components, commonly used in manufacturing machinery parts and custom jewelry for uniform surface designs.
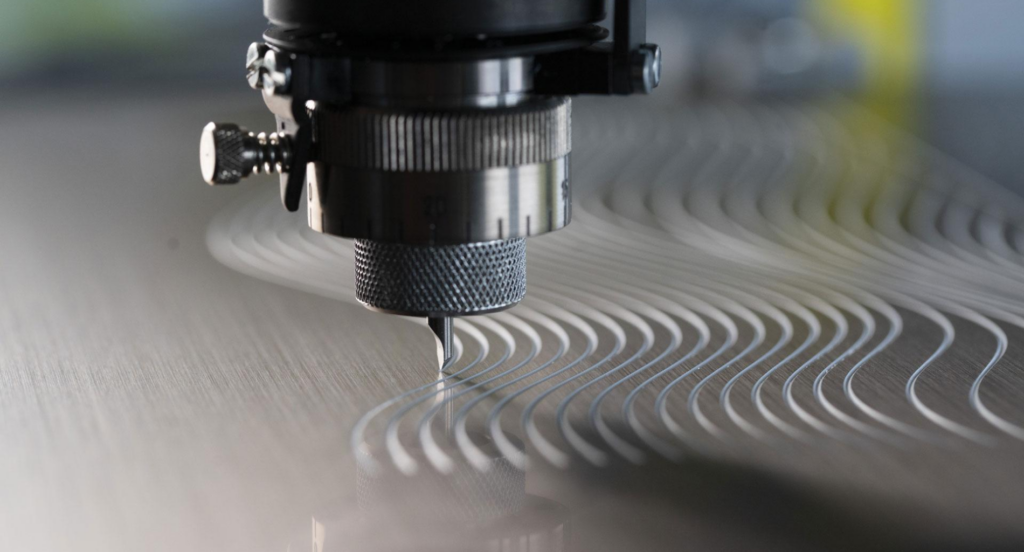
Advantages of Laser Engraving on Metal
- No Physical Contact: Laser engraving eliminates the need for physical contact with the metal surface, reducing the risk of material distortion or damage. This feature is especially beneficial for delicate or thin metal sheets.
- High-Speed Operation: Compared to traditional engraving methods, laser engraving is significantly faster, making it an efficient choice for high-volume projects. This speed ensures quicker turnaround times for engraving tasks.
- Consistency and Reproducibility: Laser engraving provides consistent results, ensuring that each engraving is identical. This consistency is crucial for businesses requiring uniformity across multiple items.
- Minimal Maintenance: Laser engraving machines generally require less maintenance than traditional engraving tools. This lower maintenance requirement results in reduced downtime and cost savings over time.
Disadvantages of Laser Engraving on Metal
- Surface Alteration: Laser engraving can change the surface properties of some metals, potentially affecting corrosion resistance or causing color changes. This aspect needs consideration, especially for applications where surface integrity is vital.
- Limited Depth: For applications requiring deep engraving, lasers may not achieve the same depth as mechanical methods. This limitation can be a drawback to certain industrial applications.
- Heat Impact: The intense heat generated during laser engraving can sometimes lead to warping or microstructural changes in the metal, which might not be suitable for all metal types or applications.
- Safety Considerations: Operating laser engraving equipment requires strict adherence to safety protocols to protect against potential hazards like eye damage or burns. This necessitates additional safety training and equipment.
4. Comparing Techniques: Marking vs. Engraving
After exploring both laser marking and engraving, it’s crucial to further examine their differences to understand how each technique affects the material, its applications, and outcomes. Here are key aspects to consider:
Depth of Interaction
- Laser Marking: This method gently interacts with the surface of metal, changing its look without deeply affecting it. It excels at creating surface-level marks, perfect for things like serial numbers or logos, all while preserving the thickness and strength of the material.
- Laser Engraving: Laser engraving dives deeper into the metal, physically carving out a portion of the surface. This method is ideal for creating more tactile and visually striking designs, offering a three-dimensional effect that marking cannot achieve.
Precision and Detail
- Laser Marking: Renowned for its precision, laser marking is capable of producing extremely fine, detailed work on metal. This is particularly beneficial for complex designs where every detail counts, such as in high-precision industries.
- Laser Engraving: While it also offers precision, laser engraving excels in creating bolder, more pronounced details. The depth achieved by engraving enhances designs, making them more visible and noticeable on metal surfaces.
This table highlights the key features and benefits of laser engraving, focusing on its ability to create pronounced details and enhanced visibility on metal surfaces.
Feature | Description | Impact on Metal Surfaces |
Precision in Detail | High accuracy in creating intricate designs | Ensures intricate designs are flawlessly replicated |
Depth of Engraving | Achieves greater depth compared to other methods | Enhances visibility and texture of designs |
Boldness in Details | Creates more pronounced and distinct designs | Makes designs stand out on metal surfaces |
Durability of Engraving | Engravings are long-lasting and resistant to wear | Ensures longevity of the design |
Versatility in Applications | Suitable for a wide range of metal types and designs | Adaptable to various industrial needs |
Durability of the Mark
- Laser Marking: Marks made through laser marking are known for their durability, resisting wear and tear over time. This is particularly advantageous for industrial applications where long-lasting identification is essential.
- Laser Engraving: Engraving, because it goes deeper, makes marks on metal that last longer. These marks don’t fade or wear out easily, making them ideal for high-use metal items.
Process Speed
- Laser Marking: Generally faster than engraving, laser marking is the go-to for efficiency, especially in high-volume applications. Its ability to quickly produce clear, legible marks makes it suitable for fast-paced production environments.
- Laser Engraving: The engraving process takes more time due to the depth of material removal. However, the extra time spent on this is usually worth it because the engraving lasts a long time and stands out. At Zemetal, we ensure that this precision and durability are at the core of our engraving solutions.
Application Suitability
- Laser Marking: Excelling in applications where maintaining the original weight and balance of the metal is crucial, laser marking is often used for functional industrial components and delicate electronic parts.
- Laser Engraving: More suited for applications where a bold visual impact is desired. For example, it’s the preferred choice for decorative metalwork, commemorative plaques, and functional items where clear, lasting visibility is required.
5. 4 Tips for Choosing the Right Technique for Your Needs
Building from the comparison between laser marking and engraving, considering factors before choosing the right technqiue is crucial to ensure the best fit for specific needs. Here are some tips to guide you:
#1 Consider the Material Type
For metals, it’s essential to consider their properties like hardness and heat resistance. Laser marking is often preferred for softer metals as it’s less invasive, while laser engraving is ideal for more durable metals, allowing for deeper, more permanent etchings. The choice depends on the metal’s composition and the desired outcome of the marking or engraving process.
#2 Define the End-Use of the Product
The intended use of the marked or engraved metal plays a significant role. If the metal component is part of a larger mechanism where precision and minimal changes are key, laser marking is advisable. However, for aesthetic purposes or where long-term durability of the marking is crucial, like in outdoor environments, laser engraving is more suitable.
#3 Assess Durability Requirements
Consider the environmental conditions and physical demands the metal will face. Laser engraving is the better choice for metals that will undergo significant wear and tear or exposure to harsh conditions, as it provides deeper, more enduring marks, while laser marking suits items with less stress exposure. Zemetal offers both laser marking and laser engraving options to provide tailored solutions for varying durability requirements.
#4 Production Efficiency and Cost
Efficiency and cost are critical, especially for bulk or industrial-scale projects. Laser marking is generally faster and more cost-effective for large batches of metals, making it a preferred choice for high-volume, less detailed work. However, for specialized, high-quality engravings, investing in laser engraving might be more beneficial despite its higher cost and slower speed.
Conclusion
Knowing the difference between laser marking and laser engraving is crucial for precise and efficient material processing. This guide has provided essential insights to help you differentiate and choose the right technique for your offerings, improving your decision-making process.
For those seeking expert guidance in adopting these laser technologies, Zemetal is your ideal partner. Contact us to see how our tailored solutions can precisely meet your business needs.
Dive Deeper Into Our Resources
Looking for more diverse service options? Browse through our handpicked selections:
Still haven’t found what you’re looking for? Don’t hesitate to contact us. We’re available around the clock to assist you.