Is the choice between hot dip galvanized and galvanized impacting metal projects? Yes, selecting either hot dip galvanized or galvanized can significantly impact metal projects.
As a specialist in metal fabrication, I bring years of experience and insights to this topic.
Hot dip galvanized processes offer a thicker, more durable coating, ideal for harsh environments, whereas standard galvanizing provides a thinner, more flexible coating, suitable for a variety of general applications.
In this article, we’ll dive into the pros and cons of each method and how they affect your business operations.
So read on to learn more!
1. Importance of Galvanizing
Galvanizing coats metal with zinc to protect against rust and corrosion, especially in harsh environments. The growing importance of this process is reflected in market trends; according to IndustryArc, the Galvanizing market size is forecast to grow at a CAGR of 4.9% during 2022-2027, indicating its increasing demand. This growth is expected as more industries recognize the benefits of galvanizing in material preservation.
The importance of galvanizing in modern industry cannot be overstated. It’s a cost-effective way to significantly extend the life of metal structures and products, reducing the need for frequent replacements and maintenance. For example, this process not only saves money in the long run but also contributes to environmental sustainability by reducing waste and the need for new raw materials.
2. Defining Hot Dip Galvanized
Hot dip galvanized is a method where steel or iron is coated with zinc to protect against corrosion. This technique involves dipping the metal into molten zinc, creating a robust and durable finish.
Features
- Corrosion Protection: The zinc coating provides a protective barrier against environmental factors that cause rust. This shield is especially effective in preventing corrosion in metals used outdoors, and I’ve seen it work wonders on everything from garden gates to industrial machinery—it’s like a superhero’s shield for metal.
- Longevity: A hot dip galvanized coating can significantly extend the life of steel or iron products. The durable nature of the coating means less need for maintenance and replacement, often lasting for decades without significant deterioration.
- Complete Coverage: The dipping process ensures the entire surface, including joints and recesses, receives a uniform coating. This comprehensive coverage is critical for the integrity and longevity of the metal, providing steadfast protection even in hidden areas.
- Bond Strength: The metallurgical bond that forms between the zinc and the base metal during hot dip galvanizing is stronger than other coating methods. This bond ensures the coating remains intact even under mechanical stress.
Applications
- Infrastructure: Used in bridges, street lamps, and guard rails, hot dip galvanizing protects these structures from corrosion and weathering. It’s not just about longevity but also safety; a galvanized structure can better withstand the rigors of nature and heavy use.
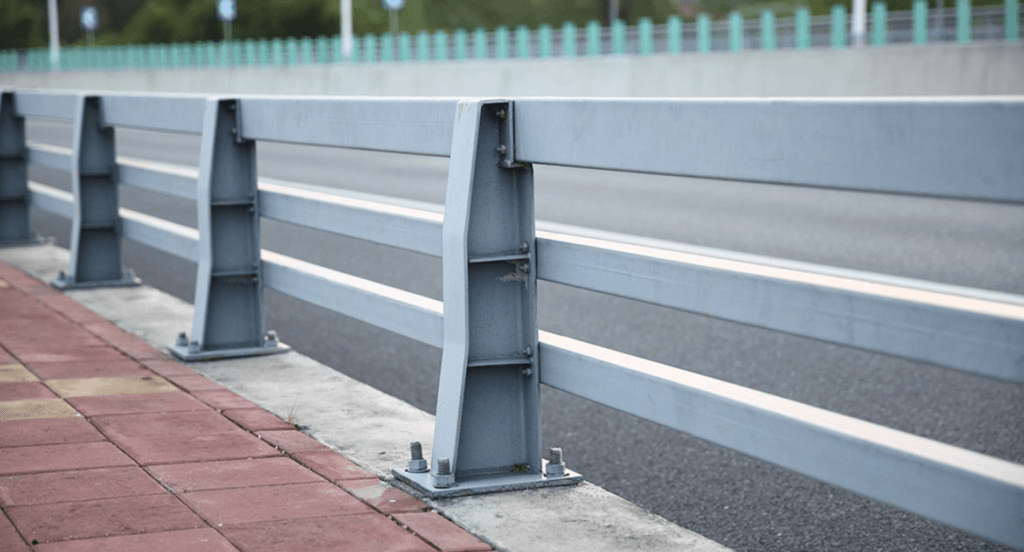
- Automotive Industry: Many car and truck parts are hot dip galvanized to prevent rust and extend the vehicle’s life. Zemetal’s advanced galvanizing process ensures maximum durability for these automotive components.
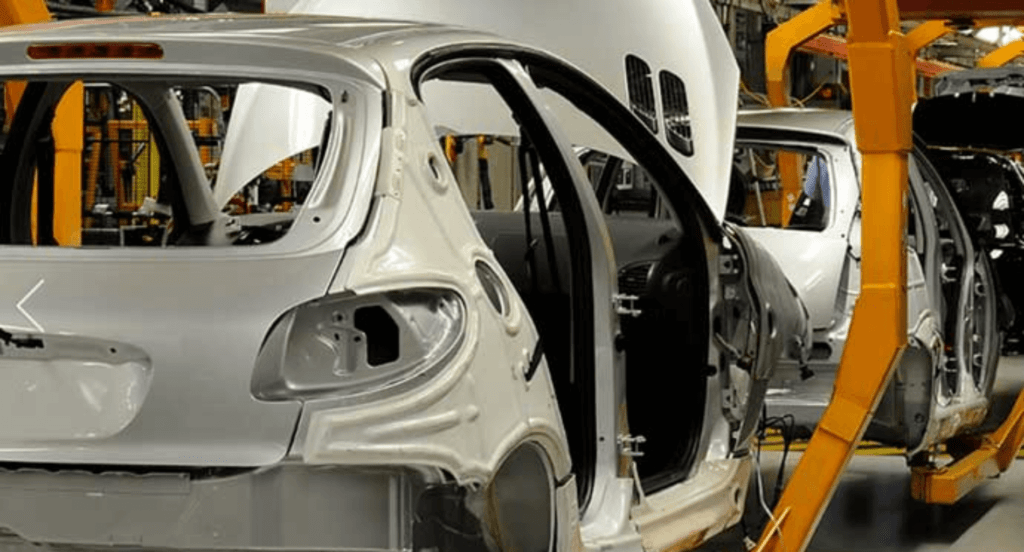
- Agricultural Equipment: Farm machinery benefits from galvanizing as it is often exposed to harsh conditions and materials that can cause equipment failure. This protection is crucial for equipment that must endure soil abrasion and aggressive chemicals like fertilizers and pesticides.
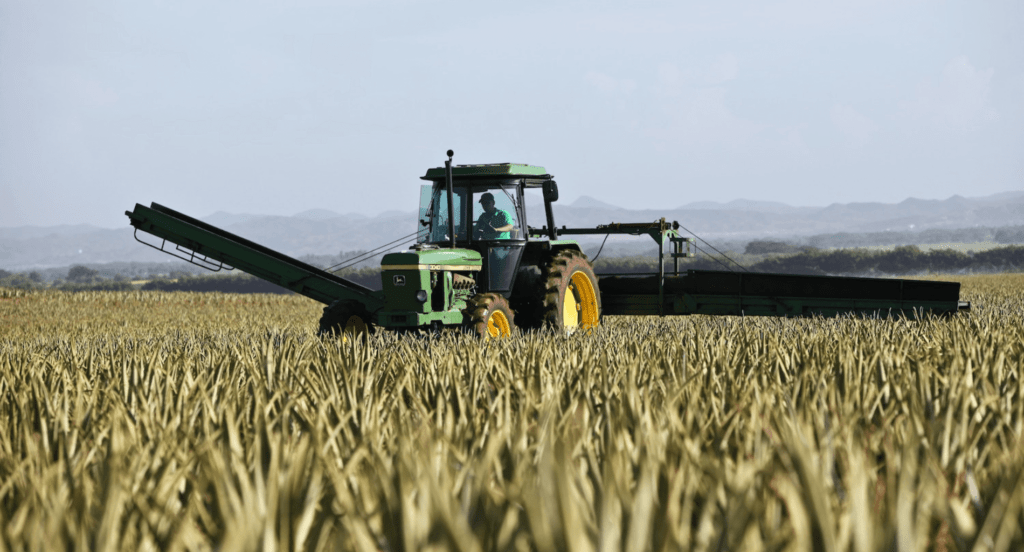
- Building Frameworks: Steel frameworks for buildings are galvanized to ensure structural integrity over decades of use. In areas prone to severe weather, such as coastal regions, galvanizing is critical for safeguarding the building’s framework against corrosive salt-laden air.
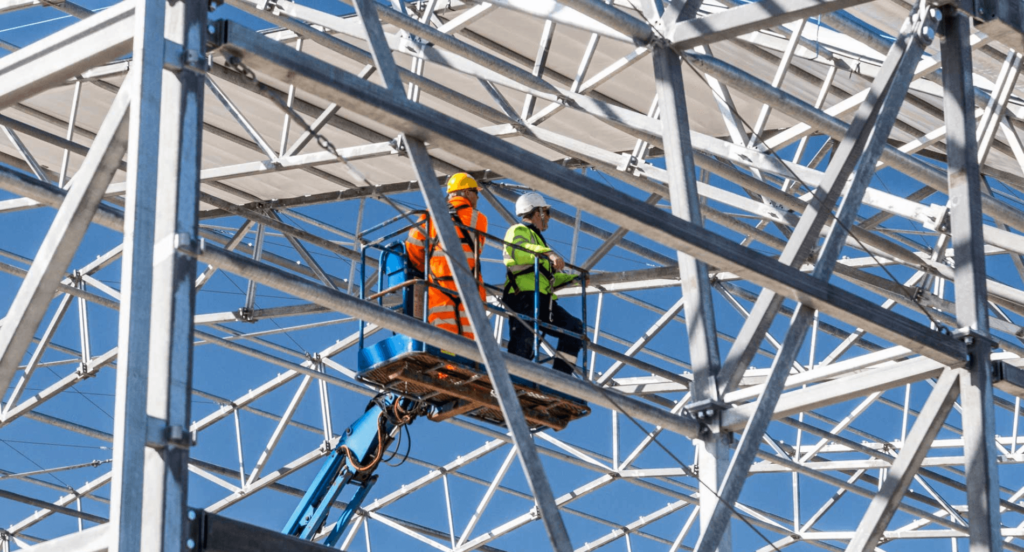
3. Exploring Galvanized
Exploring Galvanized delves into the various aspects and applications of galvanized materials. This process, vital for protecting metals from corrosion, offers a range of benefits and applications across different industries.
Features
- Enhanced Corrosion Resistance: Galvanized materials are coated with zinc, which acts as a protective barrier against rust and corrosion. This layer not only guards the base metal but also self-repairs minor scratches, maintaining the integrity of the coating.
- Longevity: The galvanization process significantly increases the lifespan of metal products. It does so by providing a durable layer that withstands environmental factors, reducing the need for frequent replacements and repairs.
- Aesthetic Appeal: Besides its protective qualities, galvanized steel has a unique, bright metallic appearance. Over time, it develops a matte patina, which is often sought after for its industrial aesthetic. This distinctive look makes it a popular choice for modern architecture and design projects.
- Easy Inspection: One of the advantages of galvanized coatings is their ease of inspection. The coating’s condition can be easily evaluated visually, without the need for complex testing methods. This simplicity helps with regular maintenance checks, ensuring long-term protection and quality.
Applications
- Construction Industry: Galvanized steel is widely used in building structures, roofing, and fencing. Its strength and resistance to corrosion make it ideal for both internal and external architectural elements. Its versatility allows it to be shaped and utilized in a variety of architectural designs and functions.
- Transportation: Galvanized materials are crucial in the manufacturing of vehicles, including cars, trucks, and ships. They provide the necessary resilience against weather and road conditions. Their use in vehicle manufacturing contributes to safety and longevity, reducing the impact of wear and tear over time.
- Utility and Telecom: Galvanized steel is used in utility poles, transmission towers, and other telecommunications infrastructure. Its durability is essential in ensuring the longevity and reliability of these structures.
- Agriculture: In agriculture, galvanized materials are used for equipment, storage tanks, and fencing. They withstand the rigors of outdoor conditions and exposure to chemicals, making them ideal for farm environments.
4. Comparative Analysis: Hot Dip Galvanized vs. Galvanized
After exploring various galvanizing methods, understanding the distinct differences between hot dip galvanized and standard galvanized techniques becomes imperative. Here are the variations of these galvanizing methods:
Aspect | Hot Dip Galvanized | Standard Galvanized |
Process Description | Involves immersing the metal in molten zinc. | Involves applying a zinc coating via electroplating. |
Coating Thickness | Generally thicker, providing better protection. | Thinner compared to hot dip method. |
Durability | Higher durability due to thicker coating. | Less durable than hot dip galvanizing. |
Corrosion Resistance | Excellent resistance due to complete immersion. | Good resistance, but not as robust as hot dip. |
Application Time | More time-consuming due to immersion process. | Quicker application process. |
Cost | Typically $0.50 to $3.00 per square foot. | Usually around $0.30 to $1.50 per square foot. |
Suitability | Ideal for large structures and harsh environments. | Suitable for small parts and less severe conditions. |
Aesthetic Finish | Rougher, thicker finish. | Smoother and more uniform finish. |
Environmental Impact | Higher energy consumption and emissions. | Lower energy use and emissions. |
5. 5 Tips for Choosing the Right Method For Your Needs
After the comprehensive comparative analysis, it’s essential to know how to choose the right method for your specific needs. Below are the tips for choosing the right galvanizing method for your needs:
#1 Assess the Environmental Conditions
Consider the environment where the metal will be used. If it’s an outdoor or corrosive setting, hot dip galvanizing’s thicker coating offers better protection. In less harsh conditions, standard galvanizing might suffice. Additionally, factor in the potential for physical wear and tear, as this can also influence the choice of galvanizing method.
#2 Evaluate the Project Size and Complexity
Hot dip galvanizing works well for big, uneven, or heavy items because it covers them evenly when they’re dipped. For smaller, fragile parts, methods like electroplating or spraying are better because they’re more precise. It’s also important to think about how complex the item is. Complex designs might need a different method.
#3 Consider Long-Term Maintenance and Cost
While hot dip galvanizing has a higher initial cost, its low maintenance and longevity can be more economical in the long run. For example, standard methods might have lower upfront costs but could require more frequent maintenance. Weighing the long-term costs versus the initial investment has always been a crucial part of my planning process.
#4 Check Regulatory and Industry Standards
Some industries have specific requirements for metal coatings. Ensure the chosen galvanizing method meets these standards for safety, quality, and environmental impact. Compliance with these standards not only ensures durability but also avoids potential legal and regulatory issues. Zemetal’s expertise in adhering to these industry-specific standards makes them a reliable partner for your galvanizing needs.
#5 Consult with Experts
When in doubt, consulting with a metal fabrication specialist or a galvanizing expert can provide valuable insights. Their experience and knowledge can guide you towards the most suitable method for your project’s specific needs. My advice to clients always includes considering expert opinions to enhance decision-making. Experts can also offer alternative solutions that you might not have considered.
Conclusion
In conclusion, this guide has provided a comprehensive understanding of the differences and applications of hot dip galvanized versus standard galvanized methods. It’s designed to help you make informed decisions for your specific metal fabrication needs.
If you’re looking for expert advice or services in metal galvanizing, Zemetal is your go-to source for quality and reliability. For more information or to discuss your needs, feel free to contact us.
Dive Deeper Into Our Resources
Looking for more diverse service options? Browse through our handpicked selections:
For some insightful reads, we’ve curated a list of recommended articles just for you:
Still haven’t found what you’re looking for? Don’t hesitate to contact us. We’re available around the clock to assist you.