Is your business seeking a reliable method for protecting metal products from corrosion? Cold dip galvanizing offers a durable and cost-effective solution.
As seasoned experts in metal fabrication, we offer insights and solutions grounded in years of experience and successful applications.
Cold dip galvanizing is a transformative treatment that coats metal with tough zinc, enhancing longevity and reducing maintenance for reliable business operations.
In this guide, we’ll explore the ins and outs of cold dip galvanizing, detailing its benefits, the process, and why it’s an economically sound choice for your business.
Read on to unlock the full potential of cold dip galvanizing.
1. Understanding Cold Dip Galvanizing
Cold Dip Galvanizing is a crucial process where metal is submerged in molten zinc, forming a robust layer that shields against corrosion and wear. This method not only prolongs the life of metal structures but also promotes sustainability by reducing the need for frequent replacements. The zinc’s reactive nature creates a tightly bonded alloy coat, ensuring comprehensive coverage and long-term protection.
In fact, according to ehzlindia, zinc-rich paints, commonly containing 92-95% metallic zinc in dry film, are applied in similar corrosive atmospheric environments as cold dip galvanizing, such as refineries, power plants, and bridges, further emphasizing the method’s relevance and effectiveness. Cold dip galvanizing combines tradition and innovation for effective, durable metal protection.
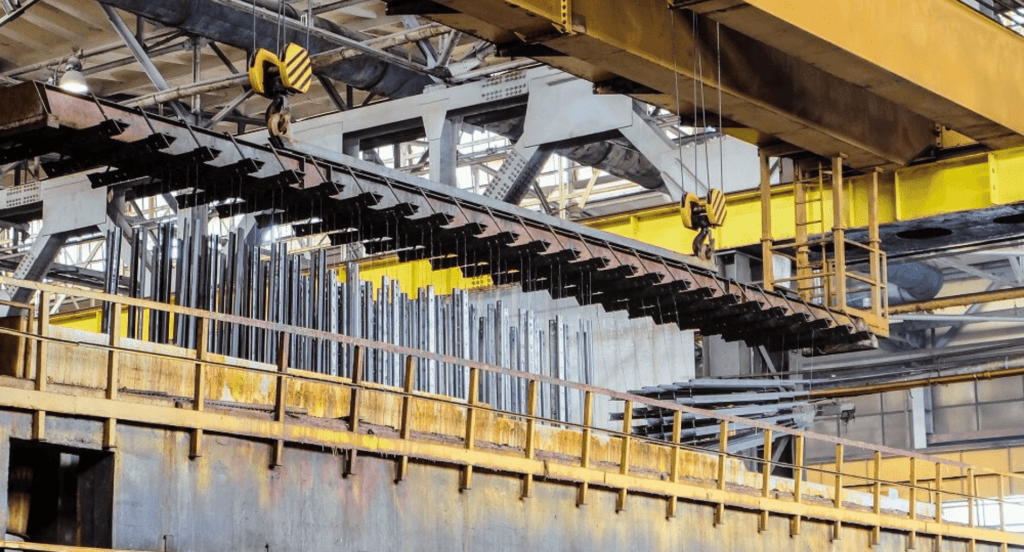
2. Key Benefits of Cold Dip Galvanizing
Building on the understanding of Cold Dip Galvanizing, it’s clear that this method offers more than just surface-level advantages. Here are some additional key benefits that highlight its importance and effectiveness in the industry:
Uniform Protection
Cold Dip Galvanizing provides a uniform, thorough coating that covers the entire surface, including edges, corners, and hard-to-reach areas. This comprehensive coverage ensures that every part of the metal is equally protected against corrosion, significantly enhancing the overall structural integrity. Unlike other coatings, galvanizing provides complete, even coverage, protecting against uneven wear and vulnerabilities.
The table below summarizes key aspects of Cold Dip Galvanizing, highlighting its uniform coverage and enhanced corrosion protection.
Feature | Description |
Uniform Coating | Ensures entire surface, including edges and corners, is covered. |
Comprehensive Coverage | Reaches hard-to-reach areas, providing complete protection. |
Enhanced Structural Integrity | Protects every part of the metal, increasing durability. |
Protection Against Corrosion | Offers significant resistance to corrosion and wear. |
Even Coverage | Prevents uneven wear and vulnerabilities in metal surfaces. |
Long-Term Performance
One of the most compelling advantages of Cold Dip Galvanizing is its long-term performance. The zinc coating acts as a sacrificial anode, protecting the steel beneath even if the surface is scratched or damaged. This self-healing property ensures continuous protection, extending the metal’s service life for decades without the need for touch-ups or additional coatings.
Speed and Efficiency
The process of Cold Dip Galvanizing is not only effective but also incredibly efficient. The entire treatment can be completed in a relatively short time, allowing for quick turnaround and minimal downtime. This efficiency is crucial for businesses that cannot afford long delays or interruptions in their operations. By choosing this method, industries gain quick processing and enduring protection, ensuring a seamless workflow.
3. Materials Suitable for Cold Dip Galvanizing
Cold Dip Galvanizing is versatile, catering to a wide array of materials. Let’s explore the most suitable candidates that benefit significantly from this protective process:
- Low Carbon Steel: Highly receptive to cold dip galvanizing, low carbon steel forms a strong bond with zinc, resulting in a durable and protective coating. It’s ideal for general construction materials.
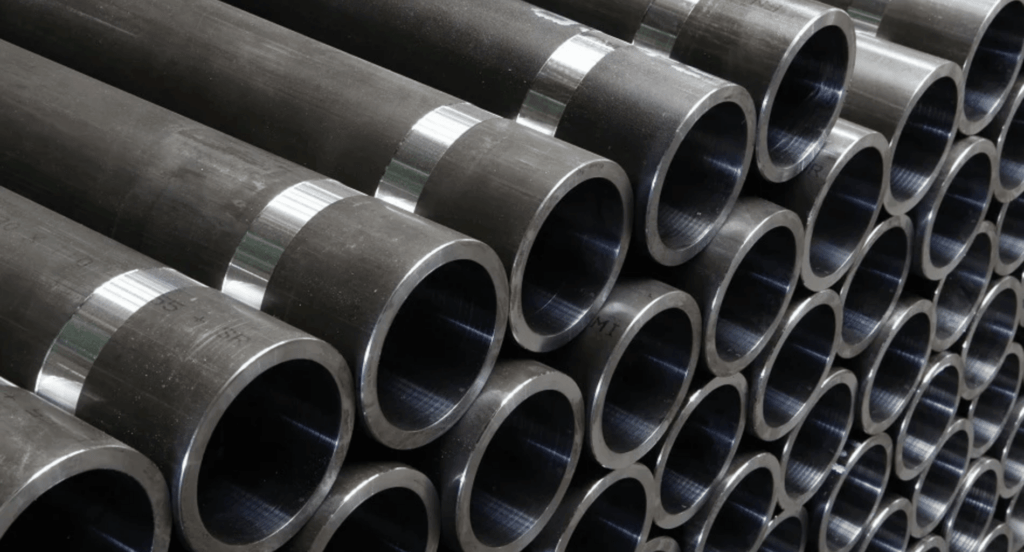
- Cast Iron: While slightly more challenging due to its composition, cast iron can be successfully galvanized. The process enhances its resistance to rust, making it suitable for decorative and architectural applications.
- Aluminum: Aluminum can be galvanized, but it requires careful preparation due to its lower melting point. The result is lightweight yet robust protection, ideal for automotive parts.
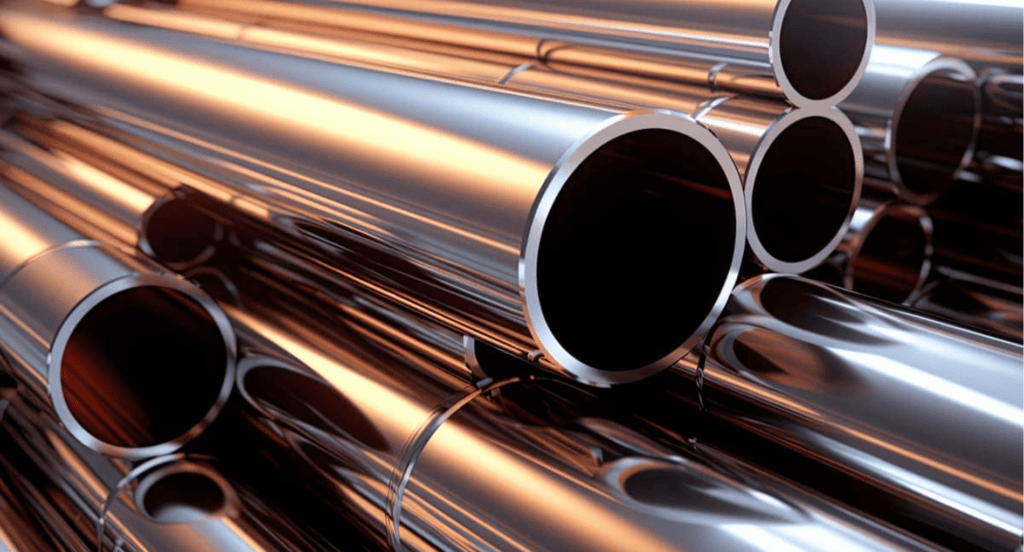
- Galvanized Steel: Already coated steel can undergo cold dip galvanizing for additional protection. This is common in re-coating or repairing damaged galvanized surfaces.
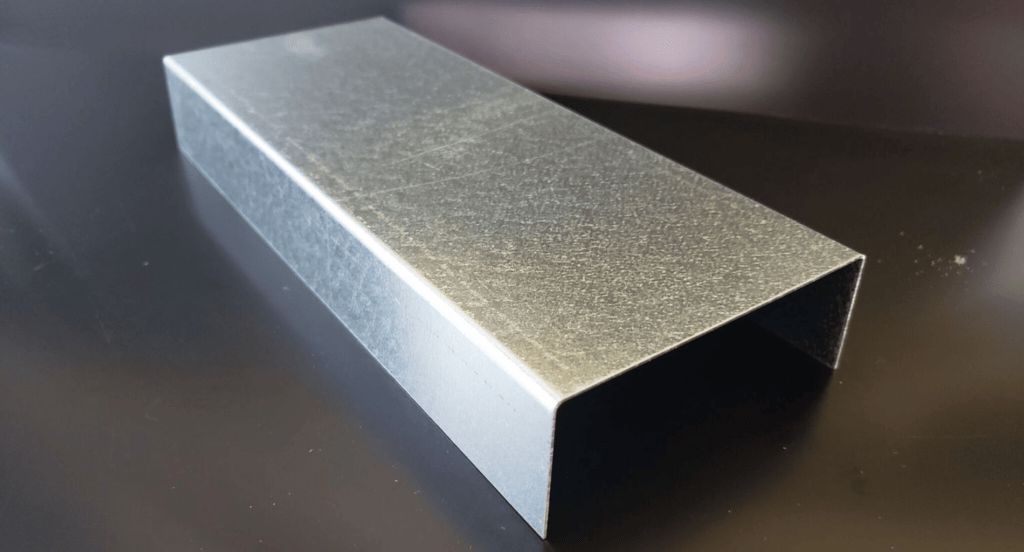
- Stainless Steel: Stainless steel can also be galvanized, although it’s less common. For example, like outdoor kitchen appliances, adding a zinc coating can further augment its corrosion resistance.
4. Step-by-Step Guide to the Cold Dip Process
The Cold Dip Galvanizing process is meticulous and methodical. Here’s a step-by-step guide to understanding how this essential treatment is applied to materials:
Step#1 Surface Preparation
The first step is thorough cleaning to remove any impurities. Materials undergo degreasing, pickling, and fluxing to ensure that the zinc will adhere properly. A clean, prepared surface is crucial for a successful galvanizing outcome, preventing imperfections and ensuring longevity.
Step#2 Preheating
Before dipping, materials are preheated to a specific temperature to prevent thermal shock. This careful temperature control ensures that the zinc coats evenly and bonds effectively with the material, providing a uniform and durable layer.
Step#3 Dipping in Molten Zinc
Next, the core of the process involves immersing the material into molten zinc with precision to ensure optimal thickness and coverage. This step is crucial as the material forms a tightly bonded alloy layer with zinc, significantly enhancing its resistance to corrosion.
Step#4 Cooling
After dipping, the materials are slowly cooled in a controlled environment to solidify the zinc coating. This stage is vital as it determines the final quality and appearance of the coating. A gradual cooling process prevents cracking and ensures a smooth, sleek finish.
Step#5 Inspection and Finishing
The final step is a thorough inspection to ensure the coating’s quality and thickness meet strict standards. Any excess zinc is removed, and the material is polished to a smooth finish. With this meticulous approach, each piece is guaranteed to have robust, long-lasting protection.
5. Industrial Applications of Cold Dip Galvanizing
Following the detailed Step-by-Step Guide to the Cold Dip Process, it’s evident how this method is integral to various industries. Let’s delve into the specific applications where cold dip galvanizing is making a significant impact:
Construction and Infrastructure
In the construction and infrastructure industry, Zemetal’s expertise in cold dip galvanizing protects steel frameworks, beams, and reinforcements against the elements. This process is crucial for structures exposed to harsh weather, such as bridges, highways, and buildings. By providing a robust, corrosion-resistant coating, galvanizing enhances the longevity and safety of key structures, vital to urban development and architecture.
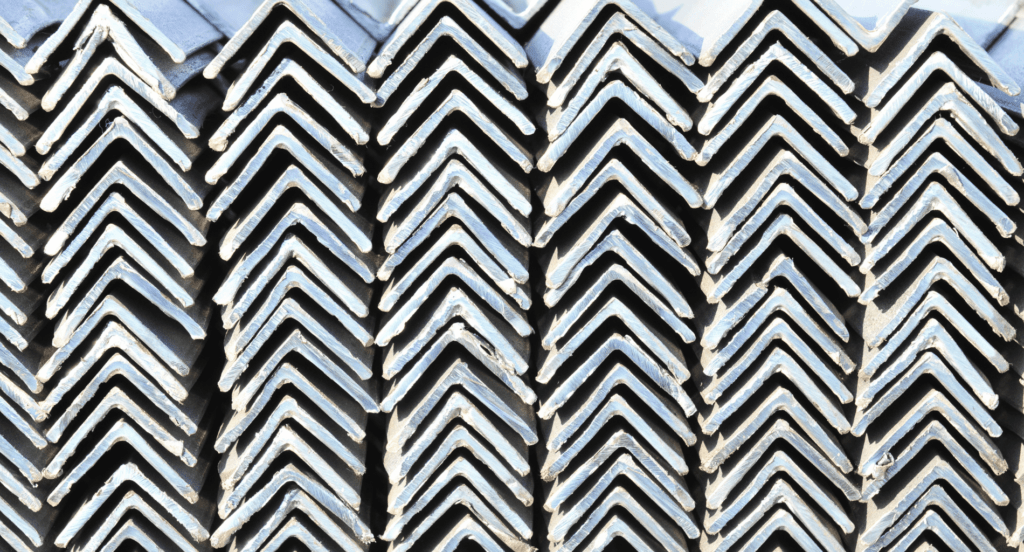
Automotive and Transportation
The automotive and transportation sector relies heavily on cold dip galvanizing for vehicle bodies, parts, and safety barriers. This treatment is vital for components exposed to road salts and environmental stressors, offering a shield that prolongs their life and maintains their structural integrity. This age-old technique remarkably ensures that today’s vehicles and infrastructure remain durable and reliable in our fast-paced world.
Energy and Utilities
In the energy and utilities industry, cold dip galvanizing is essential for protecting structures like transmission towers, wind turbines, and solar panel frames. Exposure to the elements can lead to rapid deterioration, but with galvanizing, critical components can withstand harsh conditions, ensuring stable energy supply. This not only aids in efficient power distribution but also supports the growing demand for renewable energy sources.
6. Comparing Hot-Dip vs. Cold Dip Galvanizing
Distinguishing between Hot-Dip and Cold Dip Galvanizing is essential for selecting the right coating method. Here’s a table form of comparative look at their differences across three critical aspects:
Aspect | Hot-Dip Galvanizing | Cold Dip Galvanizing |
Coating Thickness | Typically thicker, offering robust protection. | Generally thinner, suitable for precision applications. |
Temperature | Involves immersion in molten zinc at high temperatures. | Uses a cooler zinc solution, ideal for delicate items. |
Durability | Provides long-lasting protection, ideal for harsh environments. | Effective for moderate conditions; may require more frequent upkeep. |
Flexibility | Best for larger, more resilient items. | Better suited for smaller, intricate objects. |
Cost | Higher initial cost but less maintenance over time. | Lower upfront cost but may need more regular maintenance. |
Hot-Dip Galvanizing provides a thicker, more durable coating suitable for harsh environments, while cold dip galvanizing offers a finer, more precise application for delicate items. The decision between them depends on balancing factors like cost, durability, and environmental conditions. Selecting the appropriate method is crucial for optimizing the protection and longevity of your metal assets.
7. Maintenance and Care of Cold Dip Galvanized Products
After exploring the differences between Hot-Dip and Cold Dip Galvanizing, it’s vital to understand how to maintain and care for the latter to ensure longevity. Let’s take a look at the essential maintenance steps for cold dip galvanized products:
Regular Inspections
Regular inspections are essential for preserving the integrity of cold dip galvanized coatings. It’s important to monitor signs of wear or damage, particularly in areas subjected to harsh conditions. A consistent routine of checking helps in early identification of any problems, maintaining the continuous and optimal protection of the galvanized layer.
Cleaning Procedures
Keeping cold dip galvanized products clean enhances their lifespan and appearance. Use mild, non-abrasive cleaning agents and soft brushes to remove dirt and grime. It’s always rewarding to see how a little care can significantly extend the life of these coatings, preserving their protective qualities and aesthetic appeal.
Repair and Touch-Up
Even with excellent care, some areas may require touch-ups over time. Use zinc-rich paint or similar products recommended by professionals for minor repairs. For larger areas, consult with a provider like Zemetal to determine the best course of action, ensuring that the protective layer remains intact and effective.
8. 3 Factors When Considering Cold Dip Galvanizing Services
Selecting the right cold dip galvanizing service requires careful consideration of several factors to ensure quality results. Here are some key aspects to keep in mind:
#1 Provider’s Expertise and Reputation
The experience and reputation of the service provider are paramount. A company with a solid track record in cold dip galvanizing ensures reliability and quality. Look for providers who have extensive knowledge and a history of successful projects, as this reflects their capability to handle various challenges and material types.
#2 Quality of Materials and Equipment
The quality of materials and equipment used in the galvanizing process directly impacts the outcome. Ensure the service provider uses high-grade zinc and maintains their equipment to the highest standards. This includes regular updates and checks on their galvanizing baths and temperature control systems.Quality inputs and tools are essential for a superior finish.
#3 Customization and Flexibility
Different projects have unique requirements. A service provider who offers customization options, like varying zinc thicknesses or specialized treatments for different materials, adds significant value. Example, a provider that can tailor the process for detailed architectural elements shows their adaptability and commitment to meeting specific client needs. This flexibility is crucial for achieving desired results in diverse applications.
Conclusion
Through this guide, you’ve gained a deeper understanding of cold dip galvanizing, its importance, and how it can significantly benefit your operations. With this knowledge, you’re better positioned to make decisions that will enhance the longevity and quality of your metal products.
If you’re looking to implement top-notch galvanizing solutions, consider Zemetal your go-to resource. For more information or to get started, contact us today. Your next project’s success begins here.
Dive Deeper Into Our Resources
Looking for more diverse service options? Browse through our handpicked selections:
For some insightful reads, we’ve curated a list of recommended articles just for you:
Still haven’t found what you’re looking for? Don’t hesitate to contact us. We’re available around the clock to assist you.