Could CNC cutting be the key to elevating your offerings? This advanced technology brings a new level of precision and innovation to the world of metalworking.
Utilizing years of experience and in-depth knowledge in the field, we provide a reliable source, guiding you through the details and advantages of CNC cutting in today’s competitive manufacturing landscape.
CNC cutting serves as a clear symbol of innovation in manufacturing, transforming complex designs into reality with unmatched precision. Its role in elevating product quality and operational efficiency is vital in metal fabrication.
In this guide, we will explore the dynamic world of CNC cutting, uncovering its advanced capabilities, discuss how it improves manufacturing, and reveal strategies for maximizing its effectiveness and accuracy.
Read on to uncover the transformative power of CNC cutting!
1. Overview of CNC Cutting Technology
CNC (Computer Numerical Control) cutting represents a significant advancement in manufacturing technology. By automating the control of machine tools through a computer, it allows for accurate and consistent cuts on a variety of materials, primarily metals. This technology has transformed how items are produced, moving away from manual control to a more accurate, automated system.
The precision of CNC cutting machines originates from their ability to follow complex programming instructions. This guarantees each piece is cut with exact accuracy, reducing waste and increasing efficiency. This is widely used in various industries, from aerospace to automotive, due to its versatility and reliability. The impact of this technology on modern manufacturing is truly remarkable, shaping the future of production.
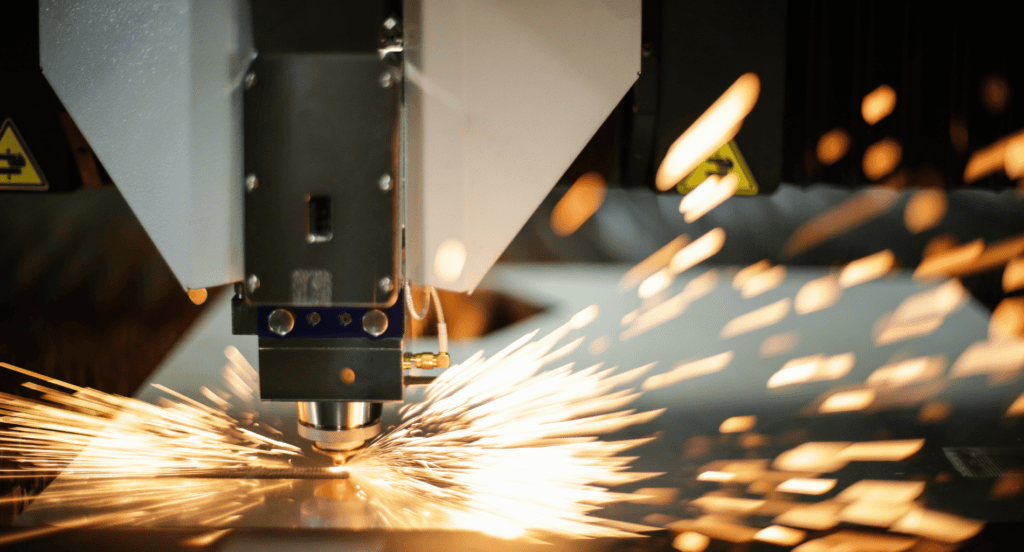
2. Benefits of CNC Cutting
After exploring the basics of CNC cutting technology, it’s crucial to assess its practical implications to grasp its role in modern manufacturing. Here are the vital benefits associated with it:
- Enhanced Precision and Consistency: CNC cutting offers unmatched precision, making it vital for complex and detailed projects. This technology ensures exact and repeatable cuts, maintaining high-quality standards, especially in industries where even slight variations matter.
- Increased Production Speed: CNC cutting accelerates production through automation, reducing the time needed for manufacturing, allowing for quicker turnaround times.This speed is a major asset in meeting tight deadlines and increasing overall productivity.
- Automation and Reduced Labor Costs: The automation in CNC cutting leads to significant reductions in labor costs by minimizing manual intervention, requiring fewer operators, and improving workplace safety.
3. Types of CNC Cutting Machines
Building on the benefits of CNC cutting, it’s essential to know the various machine types, each with unique capabilities catering to various needs. Here are the most commonly used CNC cutting machines:
Plasma Cutters
Plasma cutters are renowned for their ability to cut through thick metal sheets with remarkable speed and precision. They work by directing ionized gas at high temperatures to melt the metal, making them ideal for heavy-duty tasks. Their efficiency is particularly advantageous in large-scale industrial applications.
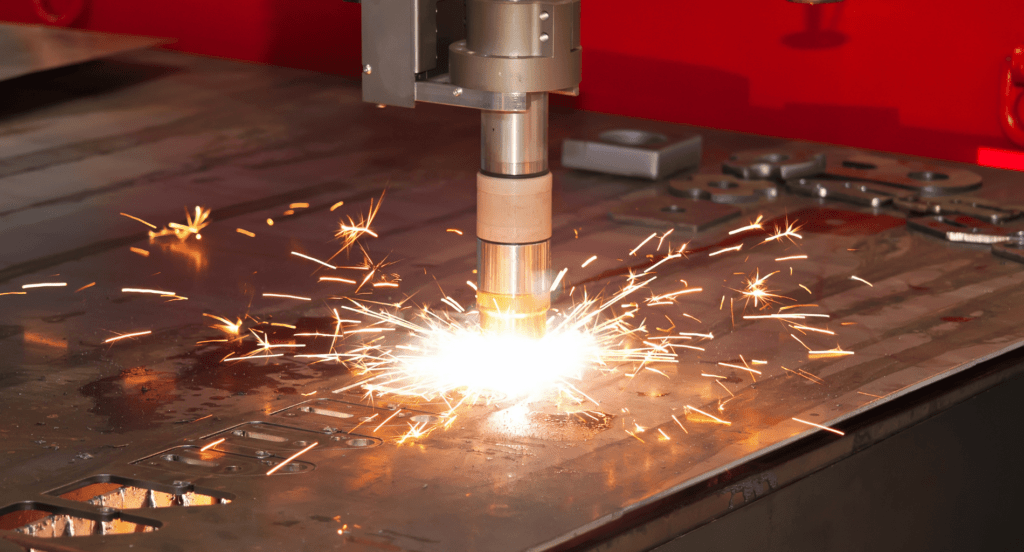
Laser Cutters
Laser cutters utilize concentrated light beams to achieve high-precision cuts, offering unmatched accuracy in metal fabrication. These machines excel in complex designs and fine detailing, making them favored in industries requiring meticulous work like electronics and jewelry. As per Fortune Business Insights, laser cutting is set to grow at a 9.6% CAGR from 2023 to 2030, driven by demand for precision cutting.
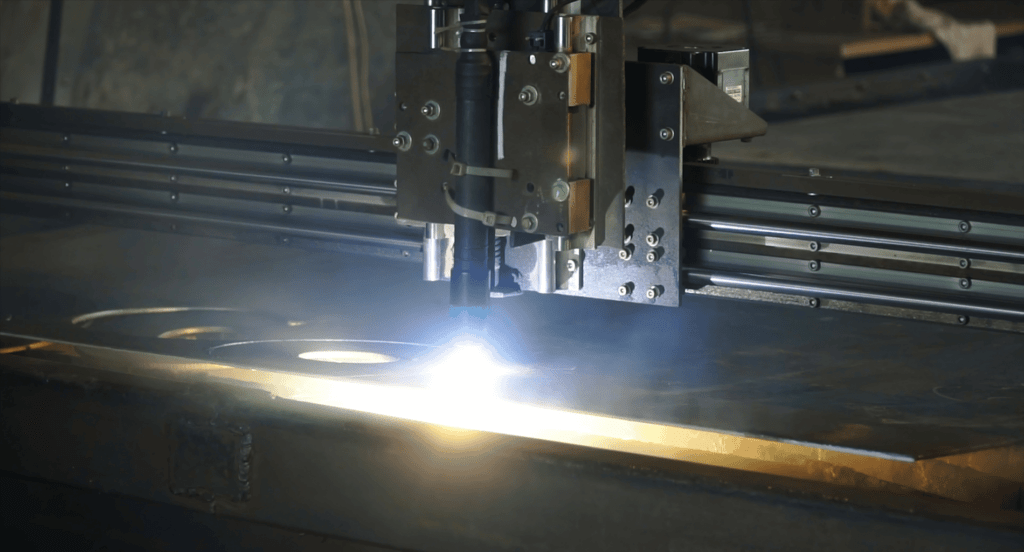
Waterjet Cutters
Waterjet cutters employ high-pressure water streams, often mixed with abrasive materials, to cut through metal. This method is notable for producing no heat, thereby ideal for complex shapes and heat-sensitive materials, preventing distortion or warping. At Zemetal, we utilize the power of advanced waterjet cutters to ensure the highest precision in our metal fabrication processes.
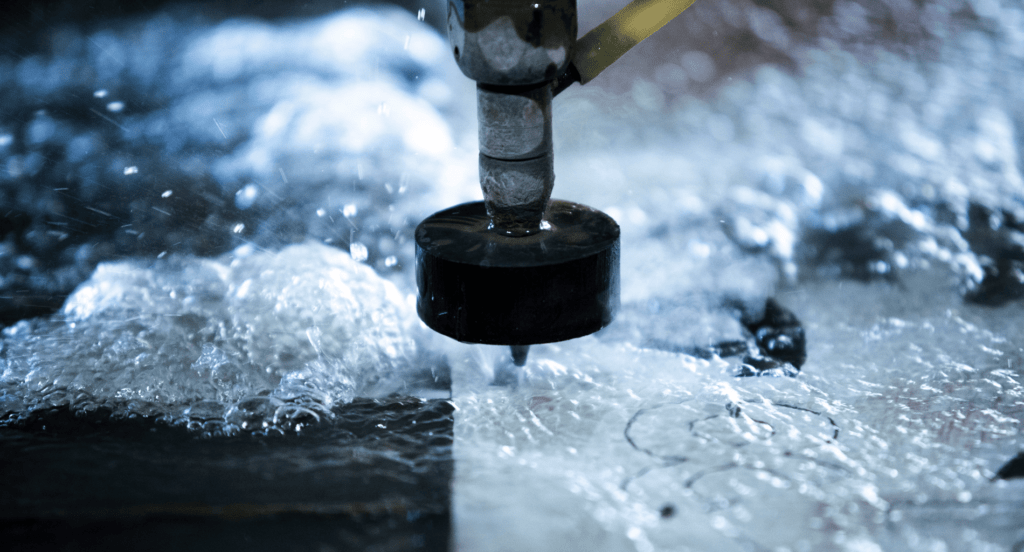
Milling Machines
Milling machines are highly versatile, capable of performing various cuts by removing material from a workpiece with rotary cutting tools. They are crucial for creating complex shapes, especially in custom manufacturing and prototype development. They are widely used in automotive and aerospace industries for their ability to produce precision parts.
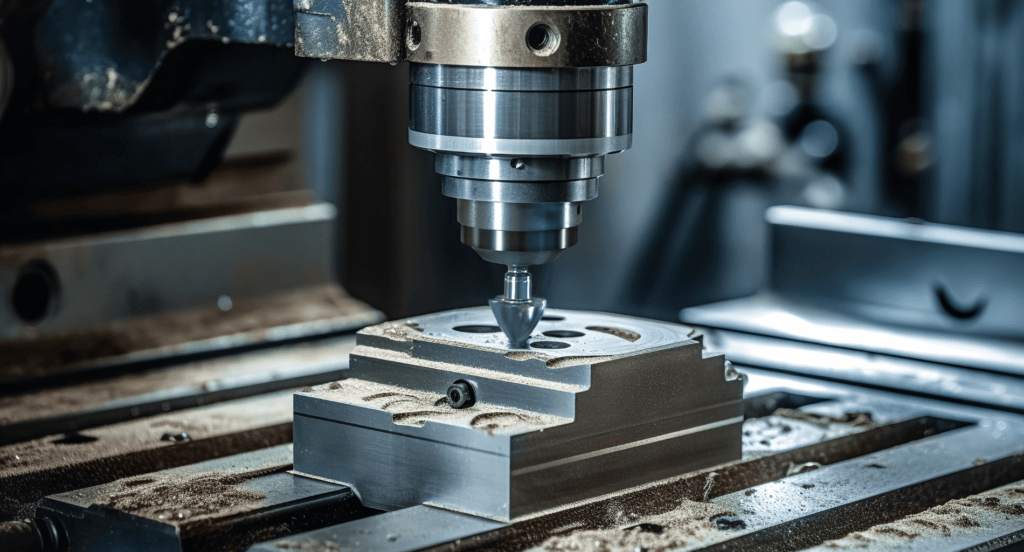
4. Advanced CNC Cutting Techniques
Transitioning from the types of CNC cutting machines, it’s vital to explore advanced techniques that complement and enhance the capabilities of these machines. Here are the techniques pushing CNC cutting boundaries:
3D Modeling and Simulation
3D modeling and simulation in CNC cutting are crucial for visualizing and testing designs before actual production. This technique allows for the identification and correction of potential errors, saving time and resources. It ensures that the final product meets the exact specifications with minimal waste.
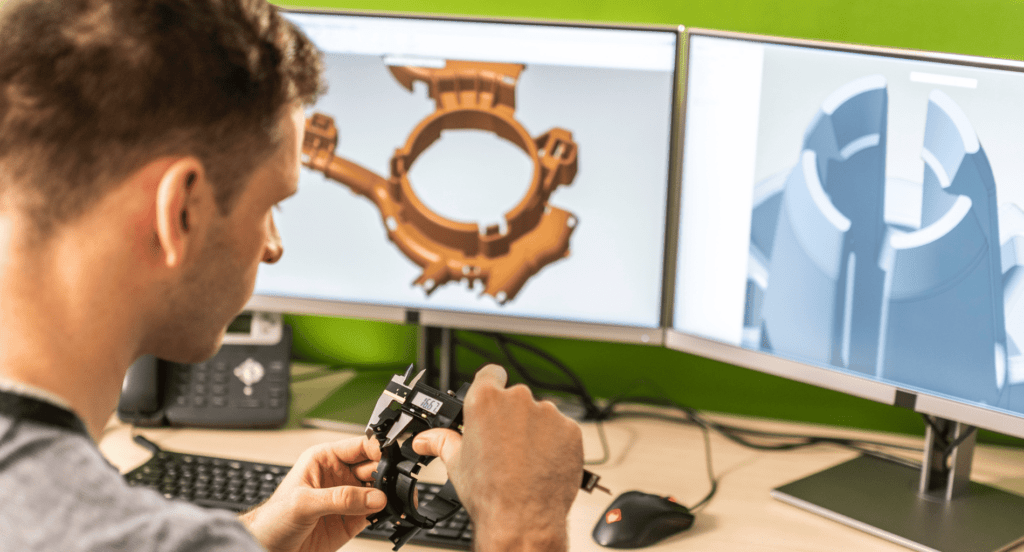
Multi-axis Machining
Multi-axis machining involves the movement of a cutting tool or workpiece along multiple axes simultaneously, enabling complex geometries and shapes. This technique allows for the creation of detailed designs with high precision, which would be impossible with traditional machining methods. It’s particularly beneficial for aerospace and automotive industries, where complex components are required.
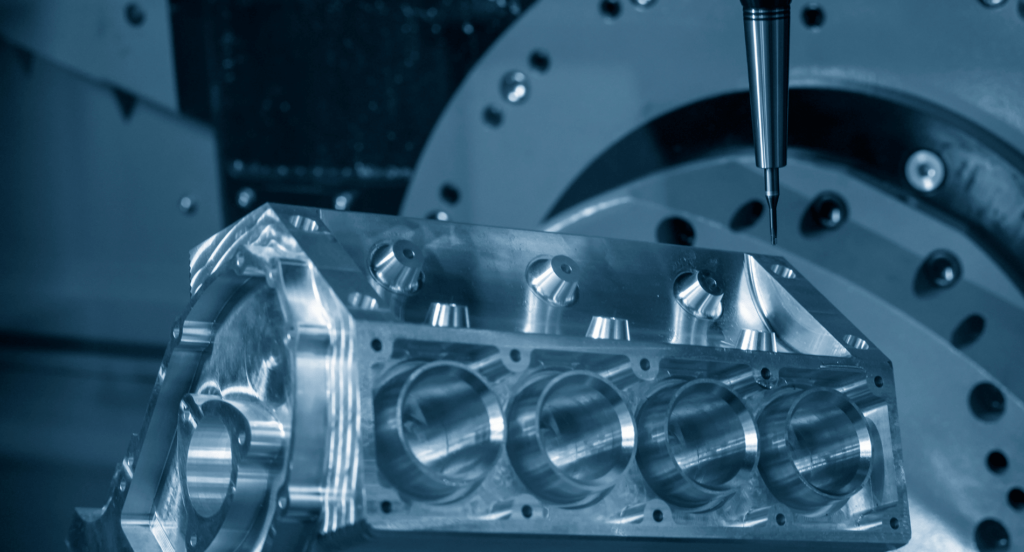
Automation and Robotics Integration
Integrating automation and robotics into CNC cutting simplifies the manufacturing process, enhancing both speed and consistency. Robots can handle repetitive tasks with precision, reducing human error and increasing overall efficiency. This integration is key in high-volume production environments where consistency and speed are critical.
High-Speed Machining
High-speed machining in CNC cutting refers to using high spindle speeds and faster feed rates to increase productivity. This technique reduces the time taken for machining operations, improves the quality of the surface finish, and makes tools last longer. It’s particularly effective in industries where time efficiency is as crucial as precision.
5. The CNC Cutting Process
With the advanced techniques already explored, it’s time to focus on the CNC cutting process, each step critical to ensuring the precision and quality of the final product. Here is the step-by-step process:
Step#1 Design and CAD Modeling
Initially, a detailed design using CAD (Computer-Aided Design) software is created. The exact shapes, dimensions, and features that the finished piece will have is drawn. The CAD model serves as a detailed guide for the CNC machine, outlining every aspect of the design necessary for accurate cutting.
Step#2 Converting CAD to CNC Program
Once the CAD design is complete, it is converted into a CNC program, typically in G-code format. This code provides specific instructions for the CNC machine, detailing the paths and movements required for cutting. The program acts as a bridge between the design and the physical cutting process.
Step#3 Machine Setup and Tool Selection
Before cutting, the CNC machine is prepared and calibrated based on the task. Appropriate cutting or shaping tools such as drill bits or end mills are selected and the machine settings like speed and feed rate are adjusted according to the specific requirements of the project. This preparation is essential for precise execution of the cutting process.
Step#4 Material Placement and Securing
The selected metal is accurately positioned on the CNC machine’s cutting surface. It is securely fastened using clamps or other holding mechanisms to hold it firmly in place during cutting process. This precise placement and securing are crucial to prevent any movement or shifting of the material, which could lead to inaccuracies in the cut.
Step#5 Executing the Cutting Process
The CNC machine starts the cutting operation, following the pre-programmed paths and instructions. It cuts, drills, or engraves the metal, adhering closely to the specified design. During this phase, the machine shapes the metal into the desired form through controlled removal of material, transforming the raw material into the desired form.
Step#6 Monitoring and Adjustments
Throughout the cutting process, the machine’s operation is closely monitored. If any differences or errors are detected, immediate adjustments are made to the machine’s settings or program. This involves recalibrating the machine, optimizing the cutting speed, or modifying the tool paths to ensure the final metal product aligns precisely with the original design.
Step#7 Post-Processing and Finishing
Once cutting is complete, the metal piece undergoes post-processing. Initially, the piece undergoes deburring to remove any sharp or rough edges resulting from the cutting process. Then, it is cleaned to eliminate any residues or debris, ensuring a clean surface. Finally, surface treatments or finishes are applied to enhance the metal’s appearance and resistance to environmental factors.
Step#8 Quality Control and Inspection
The final step involves a thorough inspection of the finished piece. Precision measuring tools and techniques are utilized to check the dimensions, alignments, and tolerances against the design specifications. Surface imperfections, such as rough edges or irregularities are also examined, to ensure the metal piece meets the predefined quality criteria.
6. CNC Cutting in Various Industries
Shifting from the process, CNC cutting has proven its worth across diverse sectors, each utilizing its capabilities to enhance efficiency, precision, and innovation. Here are key industries where this technology is crucial:
Maritime Industry
The maritime industry benefits greatly from CNC cutting, particularly in the fabrication of structural components like hull plates and engine parts for ships and submarines. This technology enables the creation of large, complex components for vessel integrity and performance, ensuring safety and durability in harsh marine environments. It’s impressive how CNC cutting has become a trusted tool in maritime engineering.
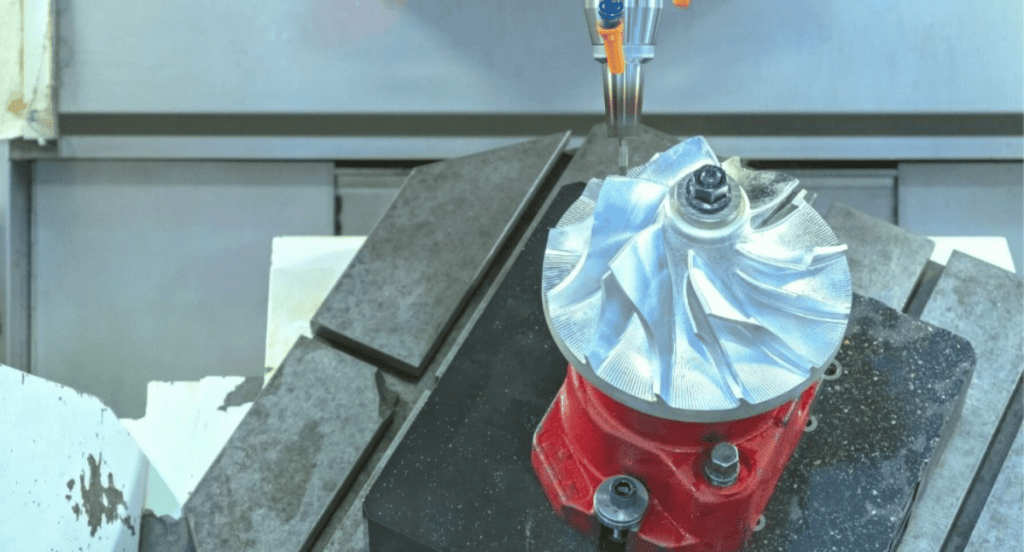
Aerospace Industry
In the aerospace industry, CNC cutting is essential for creating complex, lightweight components that meet strict safety and quality standards. For example, it allows for the precise fabrication of parts used in aircraft engines, fuselages, and other critical components, where even the slightest variation can lead to significant consequences.
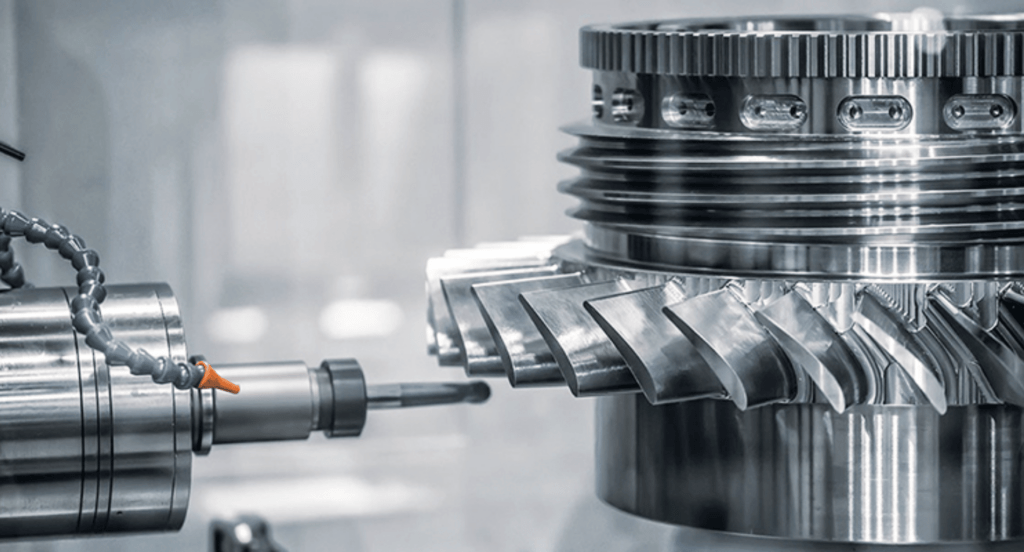
Automotive Industry
CNC cutting has transformed the automotive industry by enabling the production of detailed and durable parts with high precision. This technology is essential for manufacturing engine components, custom fittings, and complex designs that require a high degree of accuracy and repeatability. Zemetal’s CNC solutions stand out for its reliability and advanced capabilities, catering to the complex needs of automotive manufacturing.
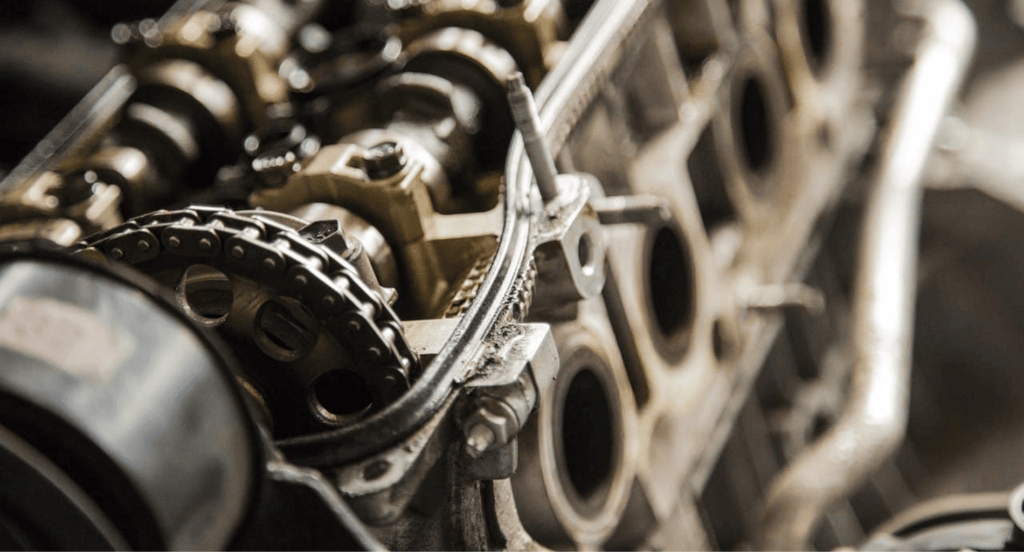
7. Challenges and Solutions in CNC Cutting
Navigating the complexities of CNC cutting is crucial for optimizing its benefits across various industries. Here are some key challenges together with their solutions to CNC cutting:
Dealing with Material Variability
The variability of materials can be challenging in CNC cutting, as different metals have unique properties affecting the cutting process. To address this, it’s crucial to tailor the cutting parameters and tool choices for each material type. Regular testing and calibration ensure the machine settings are optimized for each specific metal, leading to consistent quality.
This table outlines five different metals used in CNC cutting, highlighting their unique properties and the tailored cutting parameters required for optimal processing.
Metal Type | Unique Properties | Tailored Cutting Parameters |
Aluminum | Lightweight, soft | High-speed cutting, specific carbide tools |
Stainless Steel | Hard, corrosion-resistant | Slower speeds, high-pressure coolant |
Brass | Malleable, low melting point | Moderate speeds, sharp tools to prevent sticking |
Titanium | Strong, heat-resistant | Slow speeds, high-feed rates, cooling techniques |
Copper | High thermal conductivity | Moderate speeds, sharp tools, frequent recalibration |
Ensuring Precision in Complex Designs
Maintaining precision in detailed designs is challenging due to the complexities involved in translating designs into precise cuts. The solution lies in utilizing advanced software and precision engineering tools. This approach, combined with skilled operation and regular machine calibration, ensures high accuracy in even the most complex designs.
Adapting to New Materials and Techniques
Keeping up with new materials and techniques presents a challenge due to the ever-evolving nature of CNC technology. The solution is to promote a culture of continuous learning and adaptation within the workforce. Regular training and experimentation with new materials and methods help businesses stay at the forefront of CNC cutting technology.
8. 4 Tips When Considering CNC Cutting Services
After addressing the challenges and solutions, it’s crucial to focus on practical tips when considering CNC cutting services for businesses to choose the suitable service. Here are some essential tips to take note of:
#1 Assessing Quality and Precision Standards
Quality and precision are essential in CNC cutting services. Ensure that the provider you choose consistently delivers high-precision cuts and adheres to strict quality control measures. This commitment to excellence is vital for producing parts that meet exact specifications.
#2 Evaluating Machine Technology and Capabilities
The technology and capabilities of a CNC service provider are critical to the success of the project. Ensure that provider use advanced, well-maintained machines that can handle the project’s specific requirements, whether it involves complex shapes or large-scale production. The more technologically advanced the equipment, the better the precision and efficiency you can expect.
#3 Understanding Cost-Efficiency and Turnaround Time
Cost efficiency and turnaround time are crucial factors in choosing a CNC cutting service. Look for a provider that offers competitive pricing without compromising on quality, and one that can deliver within the required timelines. This balance is key, especially for projects with strict budgets and tight deadlines.
#4 Checking Compliance with Industry Standards
Ensure that the CNC cutting service adheres to industry standards and regulations. Compliance is not only about maintaining quality but also about ensuring that the products meet safety and legal requirements. This is crucial in industries where precision and adherence to standards are critical. For example, a provider serving the aerospace sector must follow AS9100 standards to ensure precision and reliability, meeting critical requirements.
Conclusion
CNC cutting stands as a testament to the sophistication and efficiency achievable in modern manufacturing. This guide has shed light on the complexities of CNC cutting, providing valuable insights for businesses seeking efficiency and quality in operations, enhancing your market standing and productivity.
If you are looking to enhance the quality of your metal product, Zemetal’s advanced CNC solutions are designed to meet your needs. Contact us today to explore how we can assist in transforming your operational success.
Dive Deeper Into Our Resources
Looking for more diverse service options? Browse through our handpicked selections:
For some insightful reads, we’ve curated a list of recommended articles just for you:
Still haven’t found what you’re looking for? Don’t hesitate to contact us. We’re available around the clock to assist you.