Ever wondered why bending sheet steel is a vital skill in metal fabrication? It’s a process that transforms a flat piece of steel into a work of functional art.
With years of expertise in metal fabrication, I offer insights that can streamline your processes and enhance product quality.
Bending sheet steel is an art form that requires precision, understanding, and the right approach. This skill is crucial in various applications, from constructing robust building frameworks to crafting intricate metalwork.
In the following sections, you’ll learn about the most effective techniques, essential tips, and indispensable tools for bending sheet steel.
Stay tuned to master the art of bending sheet steel.
1. Overview of Bending Sheet Steel
The versatility of sheet steel is essential for a range of applications, from industrial machinery to architectural structures. Highlighting its significance, Data Bridge predicts the sheet metal market will grow by 4.70% from 2021 to 2028. This growth underscores the importance of precision and understanding the material’s properties in the bending process.
Bending sheet steel is an art as much as a science, focusing on retaining the metal’s strength while achieving the desired form. Each technique demands a unique approach to ensure a flawless finish, meeting both aesthetic and functional requirements of any project.
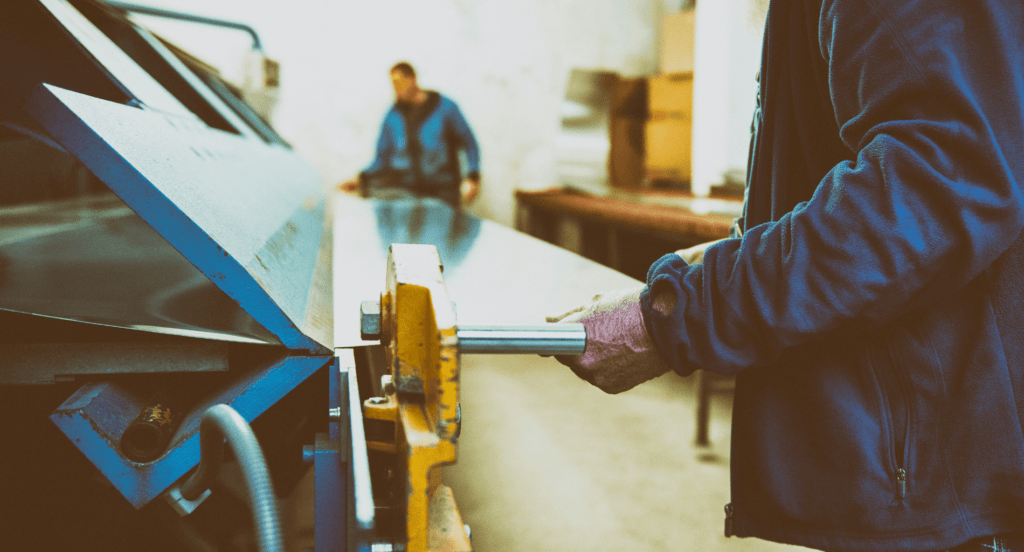
2. Essential Tools for Bending Sheet Steel
After discussing the overview of bending sheet steel, having the right tools is also crucial in achieving precision, enabling the transformation of sheet steel into desired shapes without compromising its strength. Here are some essential tools for bending sheet steel:
- Press Brake: This machine is fundamental for precise bending, especially for creating sharp and accurate angles in thicker steel sheets. It uses a set of dies to press the metal into the desired shape.
- Roll Bender: Ideal for creating smooth, circular bends, the roll bender is used when working with long sheets of steel and for forming curves and tubes.
- Folding Machine: For simpler bends, especially in thinner metal sheets, a folding machine offers a more straightforward approach, allowing for quick and accurate bends.
- Sheet Metal Hand Brake: A versatile tool for smaller or more delicate projects, hand brakes are perfect for on-site adjustments and small-scale fabrications.
- Angle Finder and Protractor: These tools are essential for measuring and setting precise angles during the bending process, ensuring accuracy in every bend.
3. Techniques and Methods in Steel Bending
After exploring the essential tools for bending sheet steel, it’s crucial to understand the various techniques and methods that utilize these tools effectively. Each method offers unique benefits and is suited for specific types of projects. Here are some key techniques and methods:
Air Bending
In this technique, the sheet metal is not fully pressed into the die, but rather, it’s bent by being pressed down into a V-shaped cavity partially. This method allows for the creation of various bend angles with the same set of tools, making it highly versatile. However, since the metal doesn’t fully conform to the die, precision control is vital to ensure the desired bend angle is achieved.

Bottoming and Coining
Bottoming involves forcibly pressing the sheet metal into the die until it conforms to its shape, resulting in a precise and sharp bend. This method is more accurate than air bending but requires more force. Coining takes this a step further by applying even more pressure, essentially imprinting the die’s shape onto the metal. This results in extremely precise bends, making it perfect for projects requiring uniformity and precision.
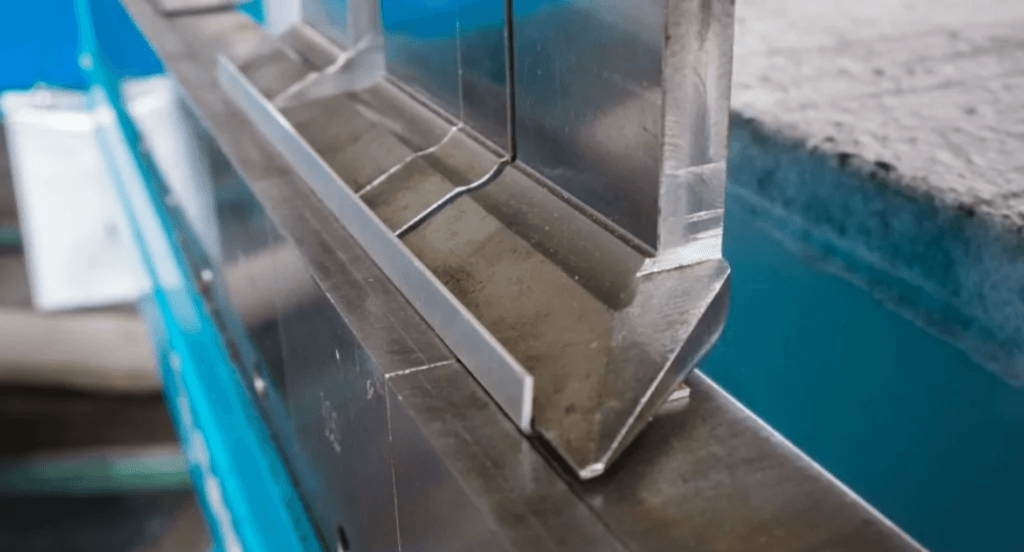
Rotary Bending
Rotary bending is particularly suited for applications where surface integrity is paramount. Unlike traditional bending methods, there’s no direct contact between the tool and the metal’s surface. At Zemetal, this method uses a rotating motion to bend the metal, avoiding scratches or marring, making it ideal for pre-painted materials or delicate surfaces.
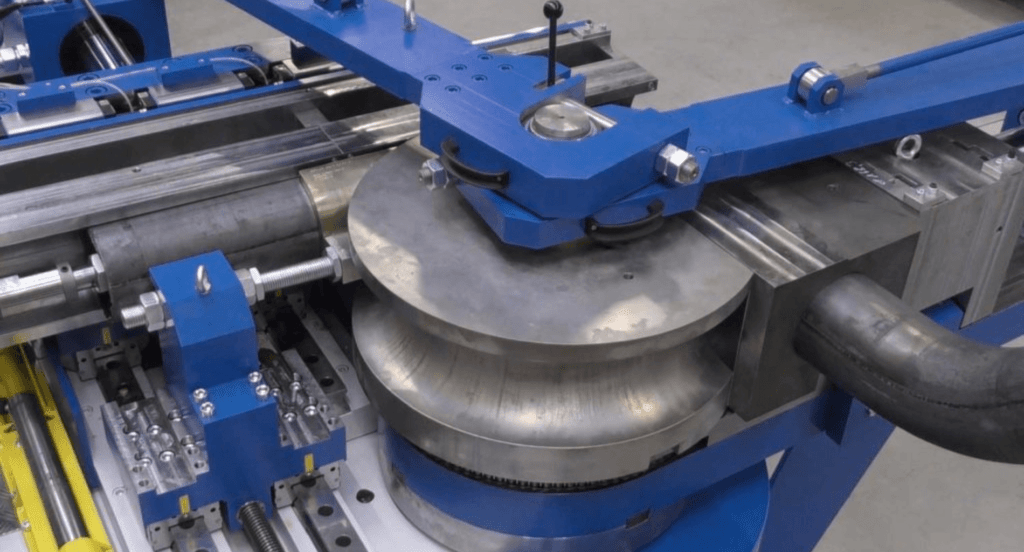
Three-Point Bending
Three-point bending provides enhanced control over the bending process, especially useful for thicker or more resilient sheet metals. This method uses a punch and two dies, applying force at three points along the metal sheet. This technique is excellent for complex projects where precision and control over the metal’s deformation are critical for the success of the final product.
4. Step-by-Step Guide to Bending Sheet Steel
Building on the various techniques and methods of steel bending, it’s now crucial to understand how these are practically applied. Here are detailed steps to guide you through the bending process:
Step#1 Material Selection and Preparation
Before any bending process begins, selecting the appropriate type of sheet steel for your project is vital. For instance, consider the thickness, grade, and overall size of the metal sheet. Once selected, prepare the steel by cleaning its surface to remove any contaminants and marking the bend lines accurately. This preparation ensures a clean and precise bend.
Step#2 Choosing the Right Bending Technique
Based on your project requirements, choose the bending technique that best suits your needs. If you’re working with thin sheets or require multiple bend angles, air bending might be suitable. For more precise bends, consider bottoming or coining. Rotary bending is ideal for preserving surface finish, while three-point bending is best for thicker materials.
Step#3 Setting Up the Bending Machine
After selecting the technique, set up your bending tool or machine accordingly. This involves installing the appropriate dies in the case of a press brake, or adjusting the rollers for a roll bender. Ensure all settings, such as bend angle and pressure, are adjusted according to the material thickness and desired bend radius.
Step#4 Executing the Bend
With everything set, it’s time to execute the bend. Place the sheet steel into the machine, aligning it with the marks you’ve made. Apply force gradually to avoid any sudden movements that could distort the metal. Throughout this process, maintain consistent pressure and speed to achieve a smooth and even bend. After bending, inspect the angle and finish to ensure it meets the project requirements.
5. Creative Applications of Bending Sheet Steel
Having explored the step-by-step process of bending sheet steel, it’s exciting to consider the creative applications this skill enables. Here are some creative ways in which bending sheet steel can be utilized:
Architectural Features
Sheet steel, with its versatility and durability, is ideal for creating stunning architectural features. This can range from intricate facade elements to functional yet stylish staircases and balustrades. The precision of bending techniques allows for the creation of unique shapes and curves, adding a modern and elegant touch to buildings and structures.
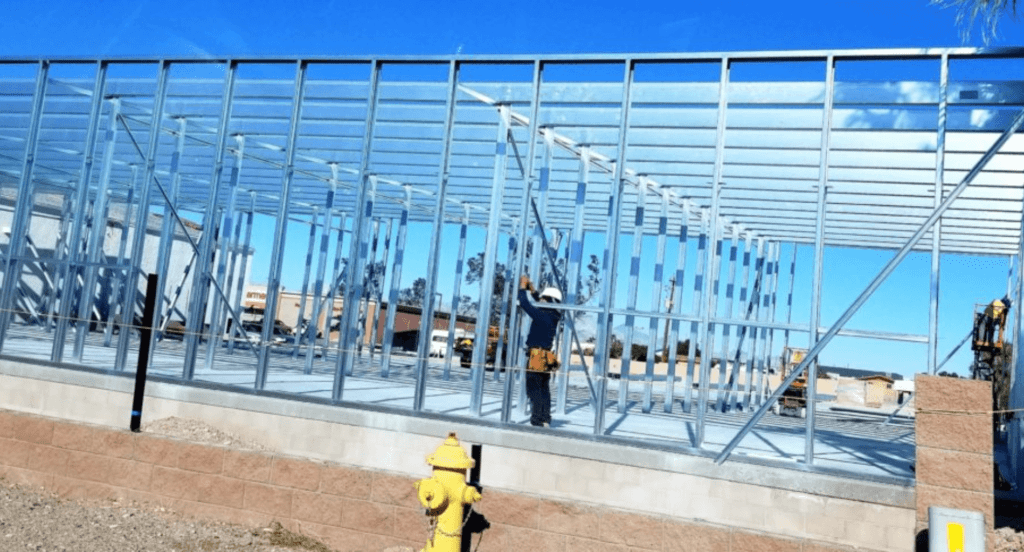
Custom Furniture and Decor
Bending sheet steel isn’t limited to large-scale industrial applications; it also has a place in crafting bespoke furniture and home decor items. For instance, from sleek, contemporary chairs to custom light fixtures, the possibilities are endless. The strength of steel paired with the elegance of well-executed bends can produce pieces that are both beautiful and durable, making them perfect for both indoor and outdoor settings.
Artistic Sculptures
The industry of artistic sculpture greatly benefits from the techniques of bending sheet steel. Artists can transform flat sheets into stunning three-dimensional sculptures, pushing the boundaries of metal art. The ability to create curves and angles in steel provides a unique medium for artists to explore, resulting in outdoor installations, wall art, and abstract pieces that showcase the malleability and beauty of metal.
6. Avoiding Common Pitfalls in Steel Bending
While the creative applications of bending sheet steel are vast, it’s equally important to be aware of the common pitfalls that can occur during the bending process. Here are key areas to focus on to prevent common issues in steel bending:
Over-Bending and Springback
One of the most common issues in steel bending is dealing with springback. To counter this, it’s essential to understand the specific properties of the steel you’re working with, such as its tensile strength and elasticity. Adjusting the bending angle slightly beyond the required angle can help mitigate springback, ensuring the final shape aligns with project specifications.
Incorrect Material Thickness
Selecting the right thickness of sheet steel for your project is critical. If the material is too thick, it may not bend properly or could damage the bending tools. Conversely, material that’s too thin might not hold the bend or could warp. It’s crucial to match the material thickness with the appropriate bending method and the capacity of your bending equipment.
Inadequate Preparation of the Steel
Before bending, the steel must be properly prepared. This includes cleaning the surface to remove any dirt or grease, which could affect the quality of the bend. Accurately marking out bend lines is also crucial for precision. Errors in marking can lead to bends being made at incorrect angles or positions, affecting the functionality and aesthetic of the final product.
The table below outlines the essential steps in preparing steel for bending, emphasizing the importance of each step for achieving optimal results.
Step | Description | Importance |
Surface Cleaning | Removing dirt, grease, and other contaminants from the steel surface. | Ensures clean contact points for uniform bends. |
Marking Bend Lines | Accurately outlining where bends should occur on the steel. | Critical for precision in bend angles and positions. |
Tool and Die Mismatch
Press brake tools like die and punch should be specifically suited to the type and thickness of the steel being bent. Using mismatched tools can not only cause damage to the steel, resulting in cracks or undesired deformations, but also wear down the tools themselves. Regularly reviewing and selecting the correct tooling for each project is vital for achieving the desired outcome.
7. Safety and Best Practices in Sheet Steel Bending
Beyond avoiding common pitfalls, prioritizing safety and best practices is paramount in the process of bending sheet steel. Here are key practices to incorporate:
Personal Protective Equipment (PPE)
Using appropriate personal protective equipment is non-negotiable. This includes wearing gloves to protect against sharp edges, safety glasses to guard against metal shavings or sparks, and ear protection in environments with high noise levels. Ensuring that all personnel are equipped with the right PPE minimizes the risk of injuries.
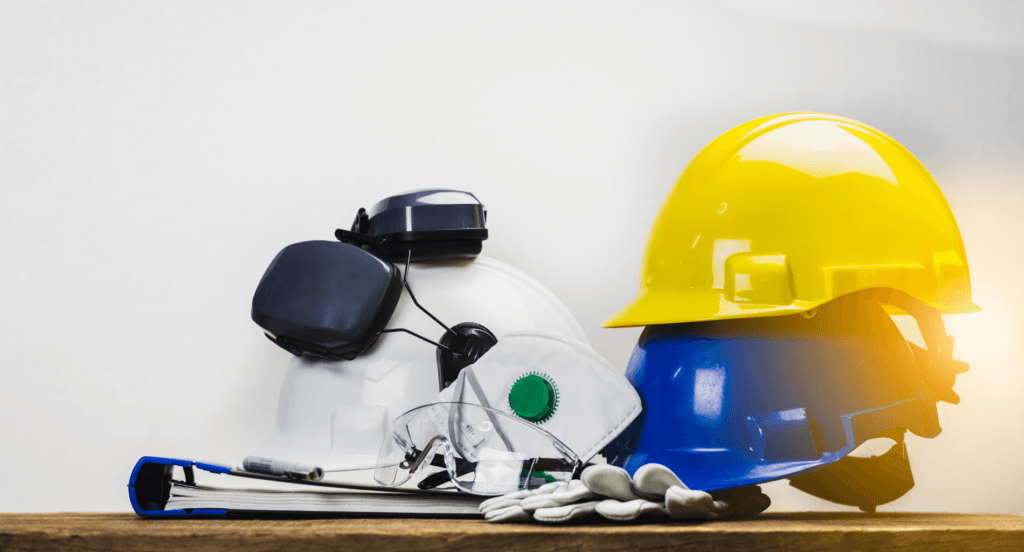
Regular Equipment Maintenance
Maintaining bending tools and machinery in top condition is crucial for both safety and efficiency. At Zemetal, regular checks for signs of wear, proper alignment, and calibration of machines help prevent equipment failure and accidents. This maintenance also ensures that the machines are producing accurate and consistent bends, which is critical for quality control.
Proper Training and Technique
Ensuring that all personnel involved in the bending process are adequately trained is essential. They should be well-versed in the correct operating procedures for bending equipment, understand the different techniques of bending, and be aware of the safety risks involved. This includes training on emergency procedures and the correct handling of materials.
Workplace Safety Measures
Creating a safe working environment is key. This involves keeping the workspace clean and organized to prevent tripping hazards or accidents. Safety guards and features on the machines should be regularly checked to ensure they are functioning correctly. Implementing a safety-first culture, where workers are encouraged to prioritize safety and report potential hazards, contributes significantly to preventing accidents.
Conclusion
Mastering the art of bending sheet steel is essential for any metal fabrication business. This guide has provided you with the foundational knowledge, practical tips, and insights into the tools needed to excel in this skill. Remember, every bend you make is a step towards perfection and efficiency in your work.
Looking to elevate your metal fabrication projects with expertise? Zemetal, a leader in metal fabrication services, is here to assist. Contact us today to transform your metal fabrication endeavors into success stories.
Dive Deeper Into Our Resources
Looking for more diverse service options? Browse through our handpicked selections:
For some insightful reads, we’ve curated a list of recommended articles just for you:
Still haven’t found what you’re looking for? Don’t hesitate to contact us. We’re available around the clock to assist you.