Is your business utilizing the full potential of anodizing magnesium for your products? Discover how this key process can transform magnesium into a superior material for various applications.
With years of expertise in the metal fabrication field, our knowledge is here to guide you through the details and benefits of anodizing magnesium to provide insights that can elevate your business’s approach.
Anodizing magnesium is not just a process; it’s a crucial innovation in material science. Its ability to significantly boost durability and aesthetic value is reshaping industry standards.
In this guide, we’ll navigate through the details of anodizing magnesium, uncovering its transformative impact on materials, cutting-edge applications, and emerging trends in the industry.
Read on for key insights into anodizing magnesium.
1. Overview of Anodizing and Its Importance
Anodizing represents a vital process in the metal fabrication industry, enhancing the metal’s surface through an electrochemical method. This process not only increases the durability of metals like magnesium but also significantly improves their appearance and resistance to wear. The anodized layer serves as a strong, protective coat, safeguarding the metal against corrosion and environmental damage.
In the world of manufacturing and product design, anodizing stands as a crucial step for ensuring longevity and reliability of metal components. It’s especially important in contexts where both aesthetic qualities and functional durability are essential. This process also offers an eco-friendly solution, as it is a safe and sustainable way to treat metals, aligning with modern environmental standards.
2. Benefits of Anodizing Magnesium
Following the detailed overview of anodizing and its importance, it’s clear that anodizing magnesium brings a range of benefits, enhancing both its performance and appearance. Here are some of its key benefits:
- Thermal Conductivity Management: Anodizing magnesium creates a layer that acts as a thermal barrier, reducing heat transfer, keeping them safer and more effective. This makes it ideal for components used in high-temperature environments, ensuring stability and longevity.
- Enhanced Adhesion for Coatings: The anodized surface of magnesium provides better adhesion for paints and coatings. This allows coatings to last longer and protect the metal more effectively, reducing maintenance needs.
- Increased Surface Hardness: Anodizing increases the surface hardness of magnesium, making it more resistant to scratches and wear. This hardness is essential for parts that face regular physical stress, ensuring they last longer.
- Lightweight Nature Preservation: Anodizing improves the properties of magnesium without adding significant weight. This is crucial for applications like aerospace and automotive, where weight is as important as strength.
3. Applications of Anodized Magnesium
The diverse benefits of anodizing magnesium have led to its widespread application across various industries. Here are the crucial industries where anodized magnesium is making a significant impact:
Consumer Electronics
In consumer electronics, anodized magnesium finds its place in the chassis of laptops, smartphones, and tablets. It adds style and durability to these devices while managing heat, crucial for their longevity and performance. Zemetal’s expertise in anodizing techniques significantly contributes to this sector, ensuring the highest quality and performance.
Medical Equipment
The medical industry utilizes anodized magnesium in surgical instruments and portable medical devices. Its biocompatibility makes it safe for patient contact, while its durability withstands the meticulous sterilization processes typical in medical environments.This application ensures both the safety and longevity of critical medical equipment.
Aerospace and Aviation
Anodized magnesium is a game-changer in aerospace and aviation, particularly for components like fuselage panels and engine parts. Its lightweight nature contributes to the overall weight reduction of aircraft, enhancing fuel efficiency. Moreover, its strength ensures the durability of these critical components in challenging flight conditions.
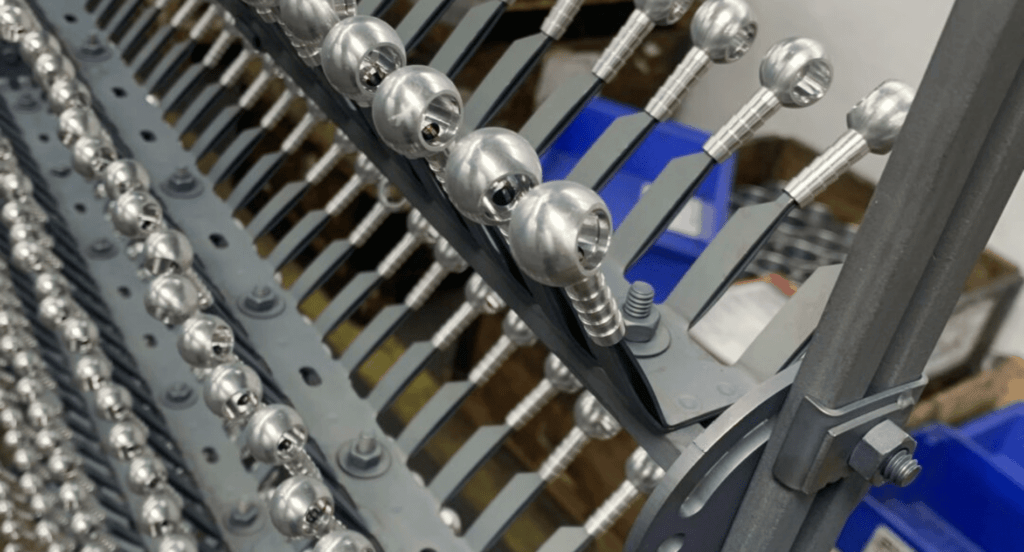
Automotive Industry
With the automotive industry greatly benefiting from anodized magnesium, a significant growth in the market is projected at a 2.79% CAGR, according to LinkedIn. Anodized magnesium is commonly employed in engine blocks, transmissions, and wheel rims, reducing vehicle weight, resulting in enhanced fuel efficiency and handling. Its durability ensures longevity even in the harsh environments of automotive operation.
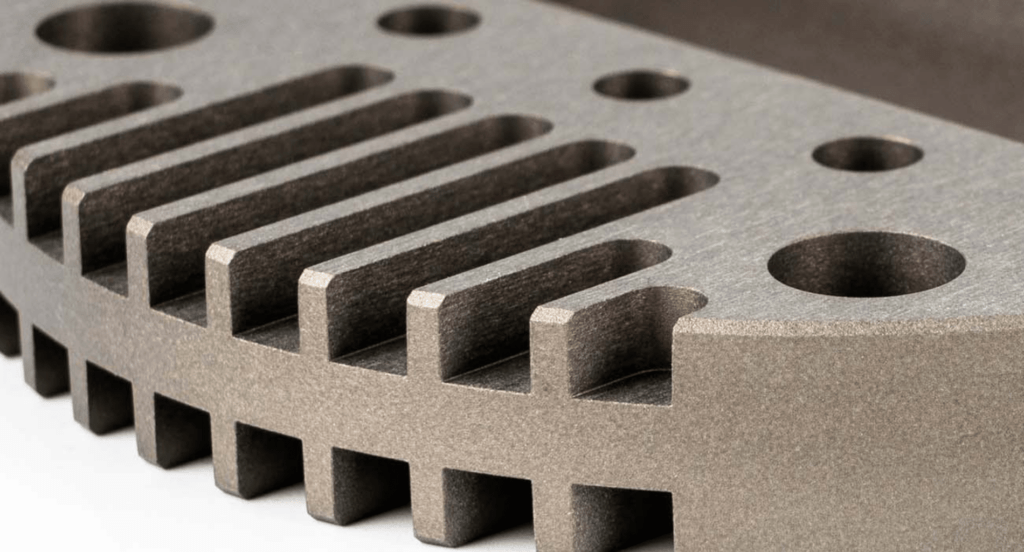
4. Comparing Magnesium Anodizing to Other Metals
After exploring the varied applications of anodized magnesium, the shift focus on its comparison with other metals to further appreciate its unique qualities. Here are some key comparisons:
Anodized Magnesium vs Aluminum
Magnesium, when anodized, offers a higher strength-to-weight ratio compared to aluminum, making it ideal for applications where weight is a critical factor. Although aluminum anodizing is more common and cost-effective, magnesium excels in situations demanding lightweight and strong components. Therefore, for industries like aerospace and automotive, anodized magnesium is often the superior choice.
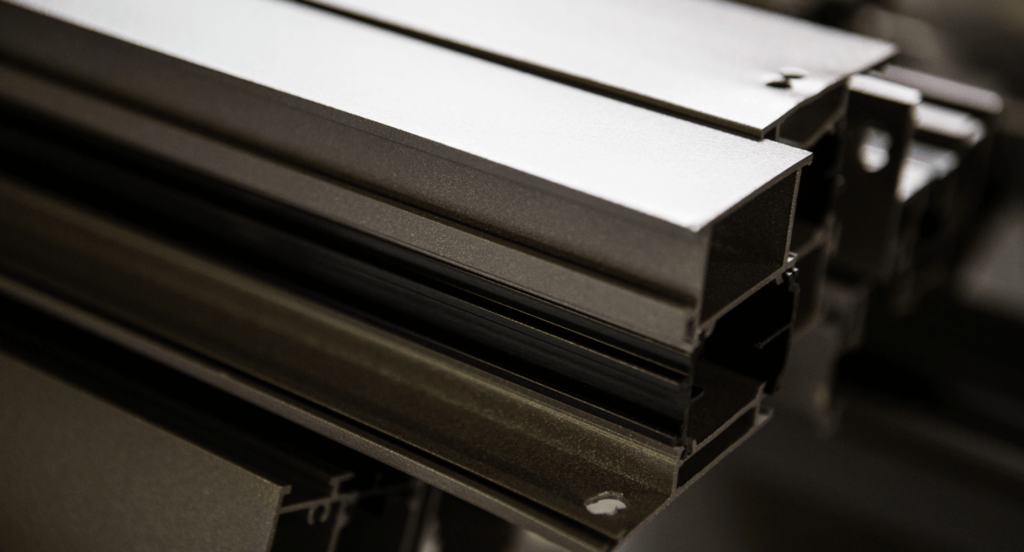
Anodized Magnesium vs Steel
Steel is heavier and less adaptable to corrosion resistance than anodized magnesium. The anodizing process significantly enhances magnesium’s resistance to environmental factors, making it superior to steel in situations where cutting weight and preventing corrosion are vital. This makes magnesium an attractive alternative in industries seeking lighter, more durable materials.
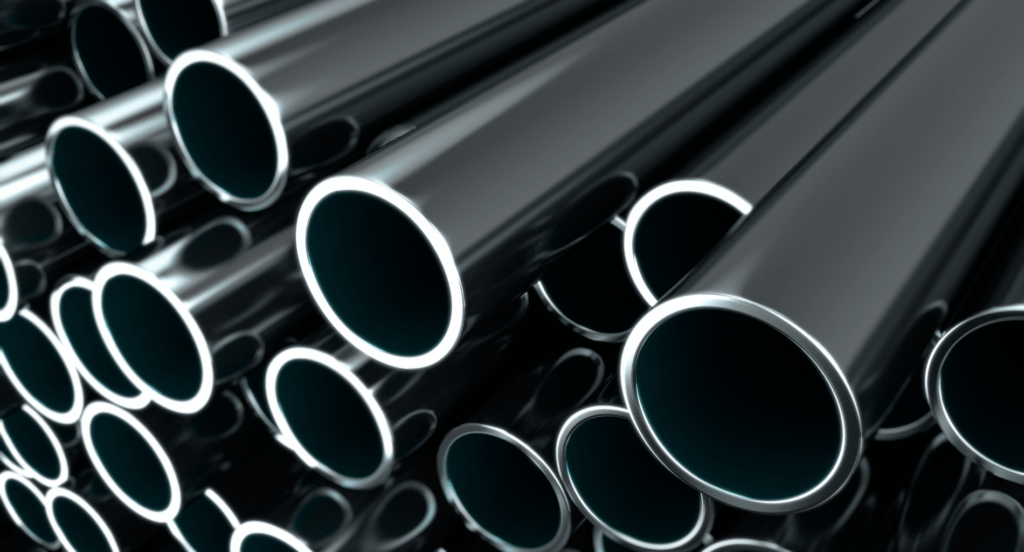
Anodized Magnesium vs Titanium
Titanium is comparable to magnesium in terms of strength and weight, but it is significantly more expensive. Anodizing magnesium can help reduce costs and improve performance, providing a more economical alternative for many applications. This positions anodized magnesium as a cost-effective substitute for titanium in sectors like medical devices and consumer electronics.
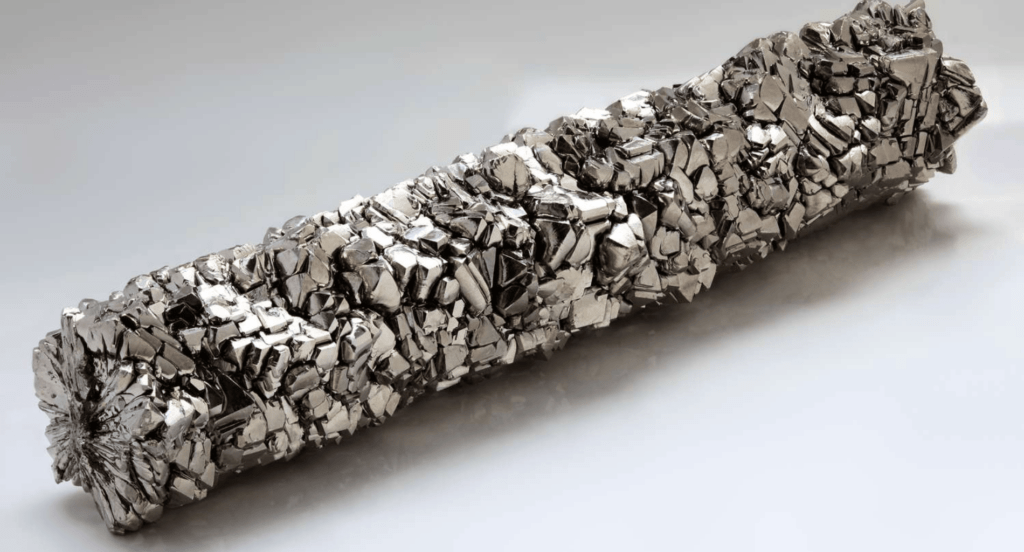
Anodized Magnesium vs Copper
Copper, which is not usually anodized, relies on its natural ability to fight off rust and its attractive aging color for protection. Anodized magnesium, however, provides superior durability and maintains its appearance over time. This makes anodized magnesium a more fitting choice in sectors where maintaining both the integrity and appearance of components is vital.
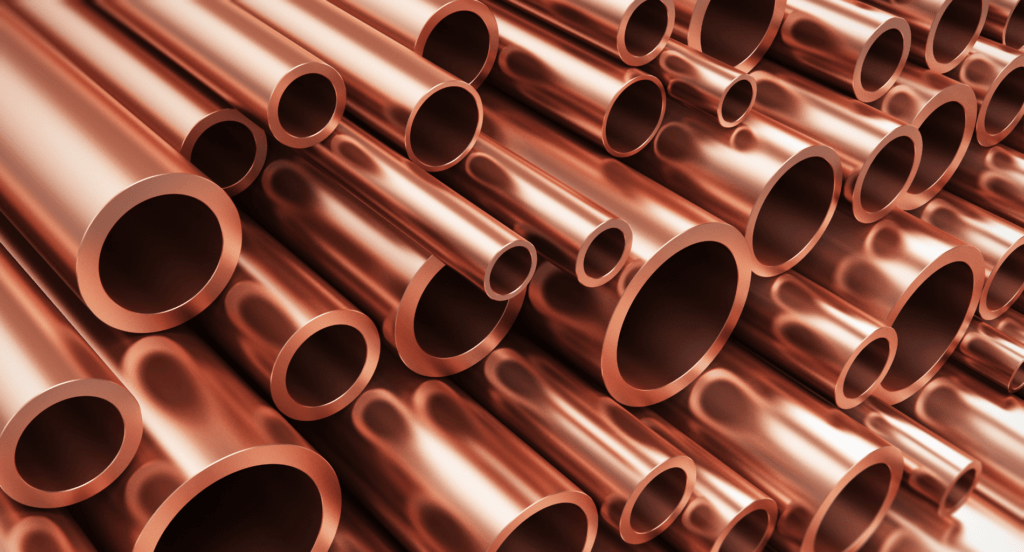
5. Maintenance and Care of Anodized Magnesium
Considering the advantages of anodized magnesium over other metals, maintaining its integrity and appearance is crucial to preserve its benefits over time. Here are essential tips for its maintenance:
Cleaning and Handling
Regular cleaning of anodized magnesium is essential to maintain its appearance and protective qualities. Use gentle, non-abrasive cleaners and soft cloths to avoid scratching the surface. For example, wiping down with a diluted vinegar solution can effectively maintain the anodized surface. This gentle approach helps retain the finish and protective layer, ensuring the longevity and effectiveness of the anodized layer.
Inspection and Maintenance
Periodic inspection of anodized magnesium components is key to detecting any early signs of wear or corrosion damage. Regular checks help catch problems early, preventing minor issues from escalating into major problems. This consistent maintenance approach guarantees that anodized magnesium components stay in great condition and maintain their aesthetic qualities.
Repair and Restoration
If anodized magnesium surfaces become damaged, professional repair and restoration are recommended. Experts in metal treatment can often restore the anodized layer, rejuvenating the appearance and protective qualities of the magnesium part. This process can significantly extend the lifespan of the component, making it a cost-effective solution.
Long-term Care
For long-term care, it’s important to store anodized magnesium components in suitable environments. Avoid exposing them to harsh chemicals or extreme temperatures, as these can degrade the anodized layer. Proper storage and handling will preserve the structural integrity and appearance of anodized magnesium parts for years to come.
6. Challenges and Solutions in Magnesium Anodizing
Following maintenance and care, it’s important to address the challenges of magnesium anodizing to ensure long-term durability and quality. Here are the key issues faced and how they are effectively resolved:
Managing Porosity
In magnesium anodizing, managing the porosity of the created oxide layer presents a significant challenge, as excessive porosity can weaken the layer’s protective qualities. To counter this, advanced sealing processes are employed, which enhance the oxide layer’s density and uniformity. This solution effectively minimizes porosity, ensuring a more durable and protective anodized finish.
Color Consistency
Maintaining color consistency during anodizing can be difficult due to varying material properties and processing conditions. This is addressed by implementing strict control protocols and utilizing consistent processing techniques. These measures ensure that each batch of anodized magnesium maintains a uniform color, crucial for both aesthetic and quality standards.
This table details the approaches and their significance in achieving color consistency in anodizing processes, particularly for magnesium, where uniform color is vital for quality and aesthetics.
Approach | Description | Importance in Color Consistency |
Strict Control Protocols | Standardizing procedures to minimize variations | Ensures uniformity across batches |
Consistent Processing Techniques | Using uniform methods in material handling and anodizing | Reduces discrepancies in color output |
Quality Material Selection | Choosing magnesium with similar properties | Aids in achieving consistent results |
Regular Equipment Maintenance | Ensuring machinery operates at optimal conditions | Prevents process-induced color changes |
Monitoring Environmental Conditions | Keeping consistent temperature and humidity levels | Reduces impact of external factors |
Environmental Considerations
The environmental impact of magnesium anodizing, particularly concerning chemical use and waste management, poses a significant challenge. The industry is shifting towards environmentally friendly methods, such as using less toxic chemicals and implementing recycling systems. These sustainable practices not only reduce environmental impact but also align with regulatory standards.
Technical Expertise
The technical complexity of magnesium anodizing requires specialized knowledge and skills. In response, companies invest in ongoing training and development programs for their staff, ensuring they are up-to-date in the latest anodizing techniques. This investment in expertise not only enhances the quality of the anodizing process but also ensures adherence to industry standards and innovations.
7. Future Trends and Innovations in Magnesium Anodizing
After addressing the challenges of magnesium anodizing, the shift focuses on the exciting advancements shaping the future of this field. Here are some innovative directions:
Nanotechnology Integration
The integration of nanotechnology in magnesium anodizing is a significant development. This approach involves manipulating materials at the molecular level to enhance the anodized layer’s properties, such as increasing wear resistance and improving thermal insulation. Nanotech-enabled anodizing is set to open up new applications in high-precision fields like microelectronics and nanodevices.
Smart Anodizing Processes
Smart anodizing, driven by IoT and AI, is gaining popularity. These technologies enable real-time monitoring and adjustments during the anodizing process, improving outcomes and reducing waste, benefiting industries requiring precision and consistency. At Zemetal, we are actively integrating these advanced technologies into our anodizing services to enhance precision and efficiency in our client projects.
Biocompatible Coatings
The development of biocompatible coatings in magnesium anodizing is a significant leap forward, especially for medical applications. This innovation involves creating anodized layers that are compatible with human tissues, making magnesium an ideal choice for medical implants and devices. This advancement not only extends the material’s applications but also showcases the importance of material safety in sensitive applications.
Advanced Coloration Techniques
Coloration techniques for magnesium anodizing are evolving with new dyes and application methods, creating a wider range of vibrant, durable colors and patterns. For example, advancements in electrochemical coloring allow for more precise control over color shades and intensity, leading to more consistent and visually appealing finishes. This innovation improves anodized product appearance and customization.
Conclusion
Exploring anodizing magnesium reveals its vital role in enhancing the resilience and aesthetic appeal of metal products. This guide has served as a valuable resource, equipping you with key insights and knowledge to effectively utilize this process in your operations and further enhance your approach to metal treatment.
If you are looking to elevate your metal products through innovative anodizing techniques, Zemetal is here to assist. Reach out to us for specialized support and to discuss how we can enhance your offerings.
Dive Deeper Into Our Resources
Looking for more diverse service options? Browse through our handpicked selections:
For some insightful reads, we’ve curated a list of recommended articles just for you:
Still haven’t found what you’re looking for? Don’t hesitate to contact us. We’re available around the clock to assist you.