Has anyone wondered how anodizing aluminum can transform its appearance with vibrant colors? It’s a fascinating process that brings both aesthetic appeal and functional benefits to aluminum products.
As a seasoned expert in metal fabrication, I have extensive experience and insights into the process of anodizing aluminum for color finishes.
Anodizing aluminum color is more than just a surface-level enhancement. This process significantly enhances metal’s durability, making it highly favored in numerous industrial applications.
In this guide, we’ll navigate through the details of anodizing aluminum, highlighting how this technique can add a vibrant and durable finish to your products.
Read on to delve deeper into the world of anodizing aluminum color.
1. The Science Behind Color Anodizing
Anodizing aluminum for color involves a fascinating chemical process that integrates both art and science. It starts with the aluminum being submerged in an electrolytic solution, where an electric current is applied. This process creates a porous oxide layer on the metal’s surface. It’s always captivating to witness how, at this stage, dyes can be absorbed into these pores, embedding a range of colors into aluminum.
After coloring, a sealing process locks in the dye and enhances the surface’s resistance to wear and corrosion. This method not only adds visual appeal but also contributes significantly to the metal’s durability, making anodized aluminum a preferred choice in various applications.
2. Benefits of Anodized Colored Aluminum
Having discussed the science of color anodizing aluminum, it’s important to understand the tangible benefits this process brings to the table. Here are some key advantages that make anodized colored aluminum a preferred choice in various sectors:
Improved Corrosion Resistance
One of the standout features of anodized aluminum is its enhanced resistance to corrosion. By transforming the surface layer into a dense oxide, anodizing effectively seals the aluminum, shielding it from environmental factors such as moisture and salt air. This characteristic is particularly beneficial in my projects involving outdoor or marine environments, where corrosion resistance is paramount.
Enhanced Durability
Anodized colored aluminum boasts significantly increased durability. The process of anodizing creates a hardened layer that is integrated with the aluminum itself, rather than being a surface coating. This results in a remarkably resistant finish that stands up well to physical wear and tear. Especially in industrial settings, this robustness enhances component longevity and reliability, ultimately offering cost-effective solutions.
Aesthetic Appeal
The aesthetic flexibility offered by anodized colored aluminum is unparalleled. The anodizing process allows for a wide spectrum of colors, giving designers and manufacturers the freedom to create visually striking products. The color obtained from anodizing is also known for its uniformity and consistency, ensuring a high-quality appearance. This aspect is crucial for consumer products where visual appeal is a key selling point.
3. The Color Spectrum in Anodizing
Delving deeper into anodizing reveals a vibrant spectrum of color possibilities. Let’s take a closer look at the range and versatility that anodizing brings to aluminum surfaces:
- Metallic Silvers and Golds: Metallic finishes such as silver and gold are not just about the dye but also about metal polish before anodizing. These finishes are a favorite in my projects for their classic appeal, offering a luxurious look to everything from jewelry to electronic casings.
- Bright Reds and Oranges: Achieving bright and vibrant reds and oranges requires precise control over the anodizing process and specific dyes. These colors are often used to grab attention and convey energy, making them popular in consumer electronics, sports equipment, and safety-related items.
- Vibrant Blues: Achieving various shades of blue, from sky blue to navy, is possible through specific dye formulations and anodizing conditions. These shades are particularly favored for their calming yet vibrant appearance, commonly used in both industrial and artistic applications.
- Crisp Whites: While achieving a true white is more challenging in anodizing, off-white or silver tones are common. These are typically created through a controlled thin oxide layer, reflecting a clean and modern appearance, often used in architectural and consumer goods.
- Rich Blacks: Anodizing can produce deep, rich blacks that are both elegant and versatile. This color is achieved through a combination of specific dyes and longer immersion times, resulting in a finish that’s popular for its ability to provide a striking contrast and add sophistication to any design.
4. Techniques and Technologies in Anodizing
Anodizing aluminum is a field that’s continuously evolving with new techniques and technologies enhancing the process. Here’s an exploration of some of the most innovative methods being used today:
Precision Control Systems
Modern anodizing relies heavily on precision control systems to regulate factors like voltage, temperature, and time. These advanced systems ensure consistent quality across batches, allowing for precise customization of thickness and color. With these technologies, achieving the exact specifications required for high-end applications becomes more reliable, ensuring that every piece meets stringent quality standards.
This table outlines the critical elements of precision control systems in modern anodizing, highlighting their roles in ensuring consistent quality and adherence to specific requirements.
Control System Element | Function | Impact on Anodizing Process |
Voltage Regulation | Maintains consistent electrical flow | Ensures uniform anodizing thickness |
Temperature Control | Keeps the chemical bath at optimal conditions | Critical for color and finish consistency |
Timing Mechanisms | Precise control over the duration of anodizing | Allows for exact customizations |
Automated Monitoring | Tracks process parameters for quality assurance | Enhances reliability and repeatability |
Feedback Loops | Adjusts settings in real-time based on results | Guarantees adherence to stringent standards |
Eco-Friendly Anodizing
Sustainability is a growing concern in all industries, and anodizing is no exception. Eco-friendly anodizing techniques focus on minimizing waste and reducing harmful emissions. Zemetal are at the forefront of this movement, adopting greener practices without compromising the finish’s quality and durability. These methods benefit the environment and meet the rising demand for sustainable production.
Automated Dyeing Systems
The introduction of automated dyeing systems has transform the color anodizing process. These systems allow for more precise and uniform color application, significantly reducing human error and enhancing efficiency. Automation ensures each metal product has the precise shade and intensity needed, crucial for industries where aesthetics are key.
5. Practical Applications of Colored Anodized Aluminum
With the evolving landscape of anodizing techniques and technologies, colored anodized aluminum has found its way into numerous industries. Here’s how this versatile material is making an impact in specific sectors:
Architectural Industry
In the world of architectural sector, colored anodized aluminum is a advantage for its versatility and durability. It’s used extensively in facades, roofing, and interior elements, providing not just structural support but also aesthetic appeal. The material’s resistance to weathering makes it an ideal choice for external applications, ensuring that buildings not only stand out with their vibrant hues but also withstand the test of time.
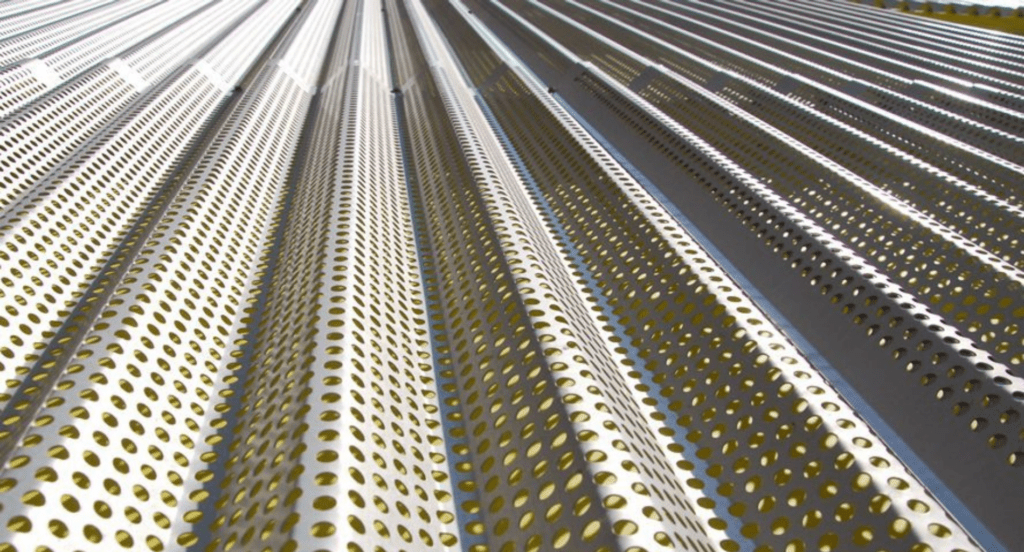
Consumer Electronics
In consumer electronics, the demand for sleek, durable, and lightweight materials is ever-present. Colored anodized aluminum meets these needs perfectly, providing a durable, scratch-resistant surface that feels premium to the touch. The use of this material in devices like smartphones, laptops, and tablets showcases its dual appeal — visually striking and robust, ensuring products meet daily demands with style and resilience.
Aerospace and Aviation Industry
In the aerospace and aviation industry, the strength-to-weight ratio of materials is critical. Colored anodized aluminum provides a lightweight yet durable solution for various components, including cabin interiors and exterior panels. The anodizing process adds color and enhances corrosion resistance, crucial for materials in extreme high-altitude conditions.
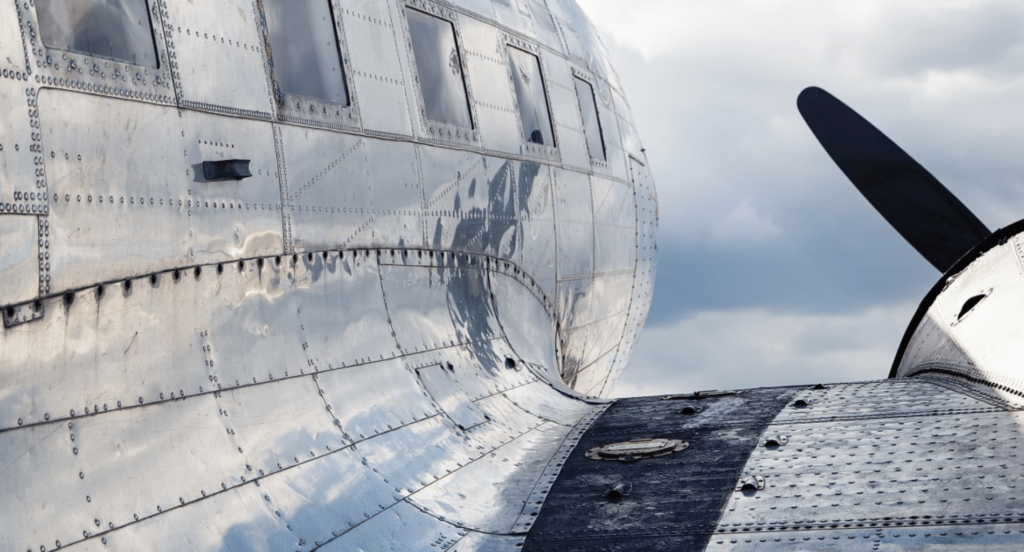
6. Maintenance and Care of Colored Anodized Aluminum
Ensuring the longevity and vibrancy of colored anodized aluminum requires understanding its maintenance needs. Let’s explore the best practices for preserving the quality and appearance of this material:
Routine Cleaning
Regular cleaning is crucial for maintaining the appearance and integrity of colored anodized aluminum. Simple solutions like mild soap and water are often enough to remove dirt and grime. It’s important to avoid abrasive materials and strong alkaline or acidic cleaners, as these can damage the anodized surface and fade the color. A soft cloth or sponge, along with gentle circular motions, is typically recommended for cleaning.
Scratch and Damage Prevention
Preventing scratches and other damage is key to maintaining the aesthetic of colored anodized aluminum. While the anodized layer is tough, it can still be vulenerable to scratching from rough contact. Zemetal recommends using protective coverings on anodized surfaces and avoiding abrasive tools to prevent scratches. Regular inspections for any signs of wear can also help in taking timely corrective actions.
Long-Term Preservation
For long-term preservation, it’s advisable to apply a thin layer of wax or special sealant designed for anodized surfaces. This layer acts as a barrier against contaminants and minor abrasions. Seeing the lasting shine and color on well-maintained anodized aluminum truly reflects the care put into its preservation. Storing anodized pieces in gentler environments helps preserve their longevity and vibrancy.
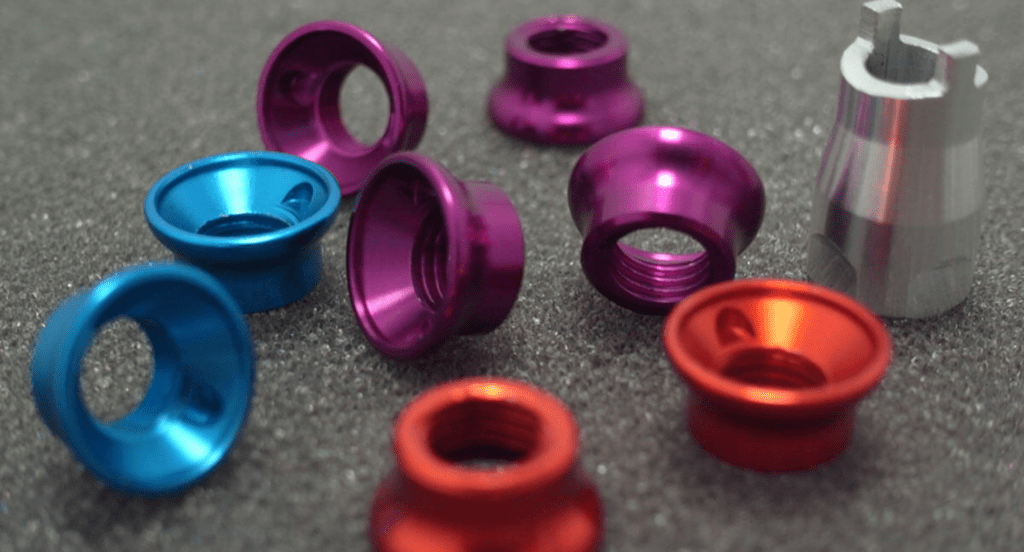
7. 3 Factors to Consider When Anodizing Colored Aluminum
While understanding maintenance and care is crucial for preserving anodized aluminum, it’s equally important to consider several factors before initiating the anodizing process. With the anodized aluminum market size projected to reach USD 3.68 Billion by 2030, as per verifiedmarketresearch. Here are some factors to consider:
#1 Material Purity
The purity of the aluminum alloy affects the final outcome of the anodizing process. Impurities can lead to uneven coloration and reduced durability. For example, alloys with a high copper or silicon content might not anodize as uniformly as purer grades. It’s essential to choose the right alloy for the desired finish and application, as this will significantly impact the quality and appearance of the anodized layer.
#2 Anodizing Environment
The conditions under which anodizing occurs are critical for achieving consistent and high-quality results. Factors like temperature, acidity of the solution, and electrical current must be carefully controlled. Even slight deviations can lead to significant differences in color and finish. Ensuring a consistent environment and careful monitoring is key for a uniform and durable anodic layer of aluminum.
#3 Desired Color and Finish
The intended color and finish are crucial considerations in the anodizing process. Different dyes and sealing methods can produce a wide range of hues and effects. For example, achieving a deep black might require a different approach than a bright blue. Understanding the specific requirements of the desired color, including its UV stability and resistance to fading, is vital for selecting the appropriate dyes and process parameters.
Conclusion
This guide has navigated the colorful and durable world of anodized aluminum, providing a comprehensive overview from scientific principles to maintenance best practices. Armed with this knowledge, you’re better equipped to enhance your projects with the beauty and resilience of anodized finishes.
Interested in harnessing the vibrant possibilities of anodized aluminum? Zemetal is here to support you with top-tier solutions. Contact us today to take the next step toward innovation.
Dive Deeper Into Our Resources
Looking for more diverse service options? Browse through our handpicked selections:
For some insightful reads, we’ve curated a list of recommended articles just for you:
Still haven’t found what you’re looking for? Don’t hesitate to contact us. We’re available around the clock to assist you.