Is your metal fabrication process missing a critical edge? The answer might just lie in the transformative power of abrasive sand blasting.
With years of expertise in the metal fabrication industry, I bring insights that can significantly enhance your business operations.
Abrasive sand blasting isn’t just a procedure; it’s a game-changer in metal surface preparation. This method swiftly removes impurities, ensuring a pristine surface ready for further processing.
In this article, you’ll learn about the numerous advantages of abrasive sand blasting and how to effectively incorporate it into your metal fabrication process.
Read on to unlock the full potential of abrasive sand blasting.
1. Understanding Abrasive Sand Blasting
Abrasive sand blasting is a highly effective method for surface preparation in metal fabrication. This technique involves propelling abrasive materials, such as sand, against a surface under high pressure. It effectively removes rust, scale, and other contaminants, leaving a uniformly textured surface. This uniformity is crucial for ensuring consistent coating adhesion in subsequent processes like painting or galvanizing.
According to acumen, the abrasive blasting market is expected to expand significantly, with an anticipated growth of USD 14.9 billion from 2023 to 2032. This trend highlights the increasing importance of abrasive sandblasting in achieving meticulous and high-quality surface preparation, which is crucial in the ever-competitive metal fabrication industry.
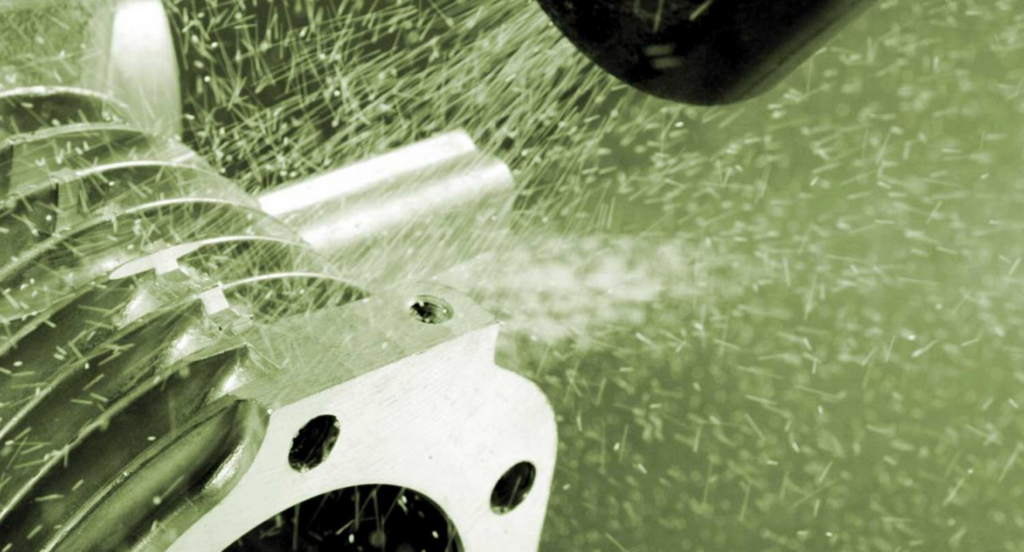
2. Benefits of Abrasive Sand Blasting
Following the exploration of what abrasive sand blasting entails, it’s important to highlight its numerous benefits. These advantages are key to recognizing why this technique is so essential in the metal fabrication sector. Let’s delve into the significant benefits this technique offers:
Consistent and High-Quality Results
Abrasive sand blasting ensures a consistent and high-quality finish. By thoroughly removing surface imperfections and preparing the metal, it sets the stage for subsequent treatments to adhere better and last longer. This process guarantees a level of finish that manual cleaning methods can not match, ensuring every project meets the highest standards of quality.
This table outlines the benefits of abrasive sand blasting for achieving consistent and high-quality results in metal finishing, highlighting its superiority over manual cleaning methods.
Benefit | Description | Impact on Metal Finishing Quality |
Surface Imperfection Removal | Effectively eliminates rust, scale, and other contaminants | Prepares a clean, uniform surface |
Enhanced Treatment Adherence | Creates an ideal surface for coatings and treatments to bond | Improves longevity of treatments |
Consistency Across Projects | Provides uniform results for all types of metal surfaces | Ensures standardized quality |
Time Efficiency | Quicker and more thorough than manual cleaning | Increases overall productivity |
Superior Finish Quality | Achieves a level of finish manual methods can’t replicate | Elevates aesthetic and functional standards |
Cost-Effective and Time-Saving
Incorporating abrasive sand blasting in operations like those brand at Zemetal demonstrates its cost-effectiveness. It reduces labor hours significantly compared to manual surface preparation methods. This efficiency translates into lower operational costs and faster project completion times, making it an economically viable option for businesses looking to optimize their production processes.
Versatility in Application
The versatility of abrasive sand blasting is impressive. It is effective on various materials, from metals to plastics, making it adaptable for different industrial needs. This flexibility allows for its application across a wide range of projects, from intricate component preparation to large-scale industrial maintenance, proving its indispensability in diverse fabrication and restoration tasks.
3. Types of Abrasive Materials and Their Applications
Exploring the world of abrasive sand blasting further, it’s crucial to understand the variety of abrasive materials available and their specific applications. Each type offers unique benefits suited to different tasks. Here are some of the key types and their typical applications:
- Aluminum Oxide: Known for its hardness and durability, aluminum oxide is ideal for aggressive cleaning and surface etching. It’s often used on metals, fiberglass, and wood, making it a versatile choice for various industrial applications.
- Glass Beads:Glass beads provide a softer, less aggressive finish. They are commonly used for polishing and smoothing surfaces without causing significant material removal. An example is their use in automotive parts to create a clean, bright finish without altering the metal’s integrity.
- Silicon Carbide: This is the hardest abrasive available, often used for fast cutting of hard materials like stone, glass, and ceramics. Its sharpness makes it a preferred choice for jobs requiring precision and speed.
- Steel Grit and Shot: Steel grit is used for aggressive surface cleaning, while steel shot provides a smoother, polished finish. Both are particularly effective on metal surfaces, with steel grit being excellent for removing heavy paint and rust, and steel shot for creating a smooth, polished surface on metal parts.
4. Advanced Techniques in Abrasive Sand Blasting
As the field of abrasive sand blasting continues to evolve, new and advanced techniques are emerging. These innovative methods enhance efficiency and effectiveness in metal fabrication. Let’s take a look into some of these cutting-edge techniques:
Automated Blasting Systems
Automated blasting systems represent a leap forward in abrasive sand blasting technology. Brands like Zemetal specialize in utilizing these systems, which employ advanced robotics and programmable logic controllers to automate the blasting process. This automation ensures consistent quality, reduces labor costs, and significantly increases throughput, making them a valuable asset in the metal fabrication industry.
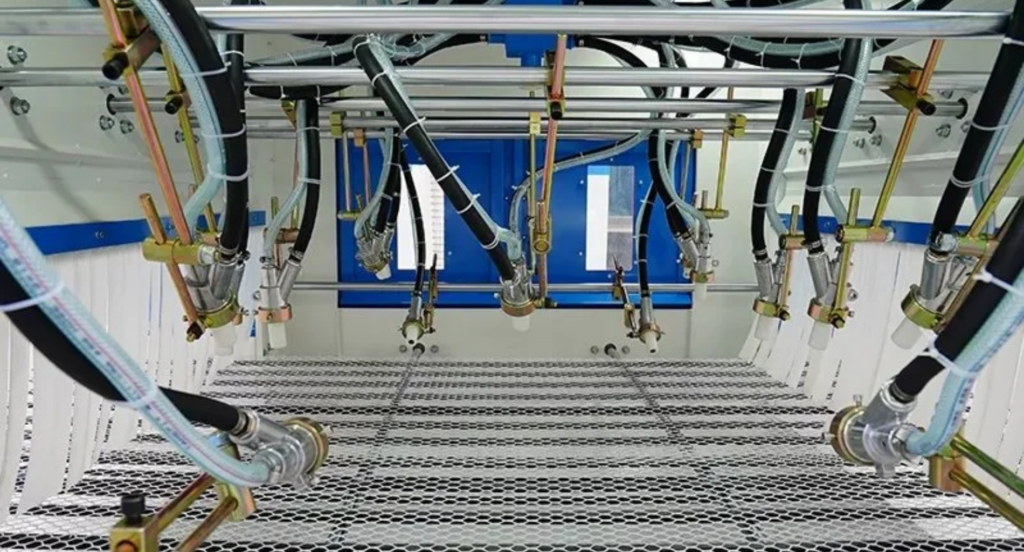
Wet Abrasive Blasting
Wet abrasive blasting is an advanced technique that mixes water with abrasive materials. This method reduces dust generation, making it environmentally friendly and safer for operators. The addition of water also enhances the impact of the abrasive material, allowing for a smoother finish. This technique is particularly useful in applications where dust suppression and surface cleanliness are of utmost importance.
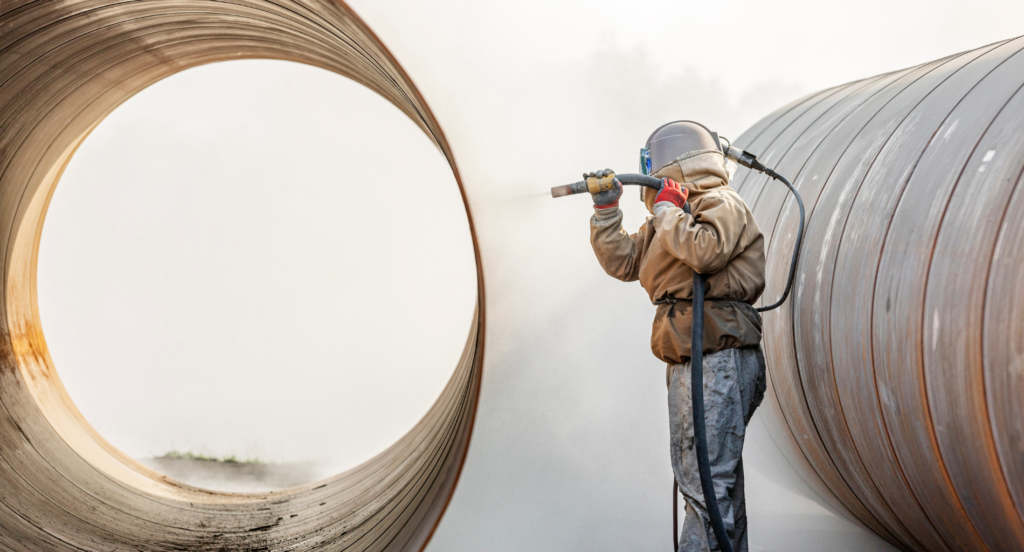
Micro-Abrasive Blasting
Micro-abrasive blasting uses fine abrasives and precise delivery systems for detailed work on small or delicate parts. This technique is perfect for applications requiring high precision, such as in the aerospace and medical device industries. It allows for the targeted removal of surface materials without damaging the underlying structure, showcasing the precision and control achievable with advanced abrasive blasting methods.
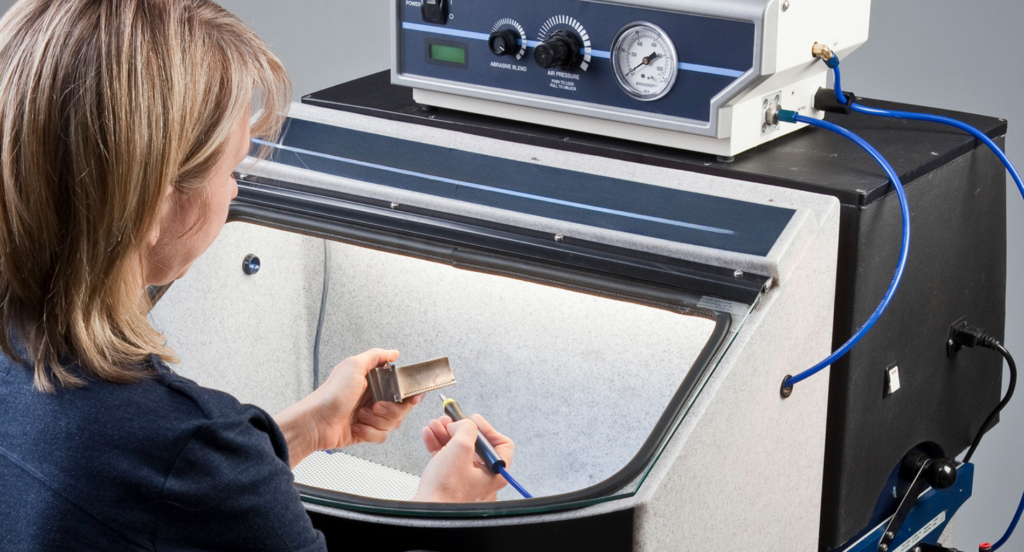
5. Practical Applications in Different Industries
Building on the advanced techniques of abrasive sand blasting, it’s fascinating to see how these methods are applied across various industries. Each sector leverages this technology to meet unique surface preparation and finishing needs. Here are some specific industries where abrasive sand blasting plays a crucial role:
Automotive Industry
In the automotive industry, abrasive sand blasting is essential for removing rust, paint, and other coatings from vehicle bodies and parts. This process prepares surfaces for repainting or coating, ensuring a high-quality finish that is critical for both aesthetic appeal and vehicle protection. The precision and efficiency of abrasive blasting make it ideal for both manufacturing new vehicles and restoring classic cars.
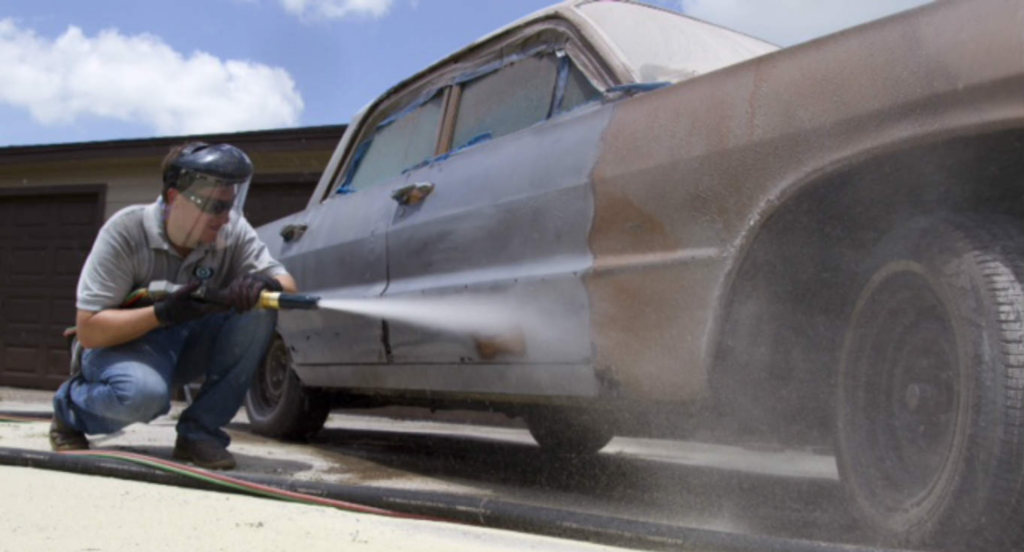
Aerospace Industry
The aerospace industry relies on abrasive sand blasting for the precise preparation of aircraft components. This process is used to remove old paint, prepare surfaces for new coatings, and clean components without damaging their integrity. The precision of abrasive sand blasting is particularly crucial in this industry, where even minor surface imperfections can have significant consequences.
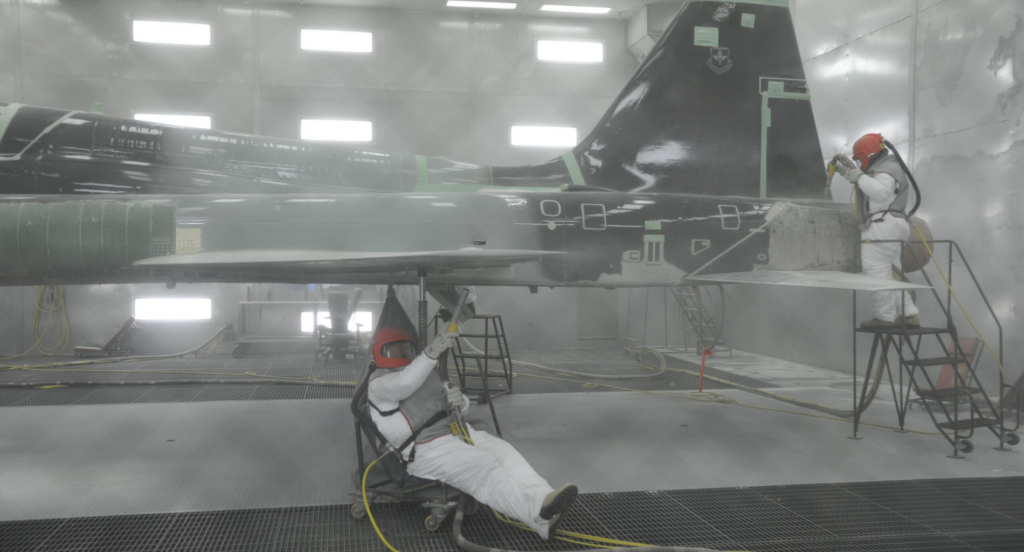
Restoration and Construction Industry
In restoration and construction, abrasive sand blasting is used for cleaning buildings, bridges, and other structures. It effectively removes dirt, graffiti, and old paint, restoring surfaces to their original condition. This method is also employed in the maintenance of historical buildings, where preserving the underlying material is as important as the cleaning process itself.
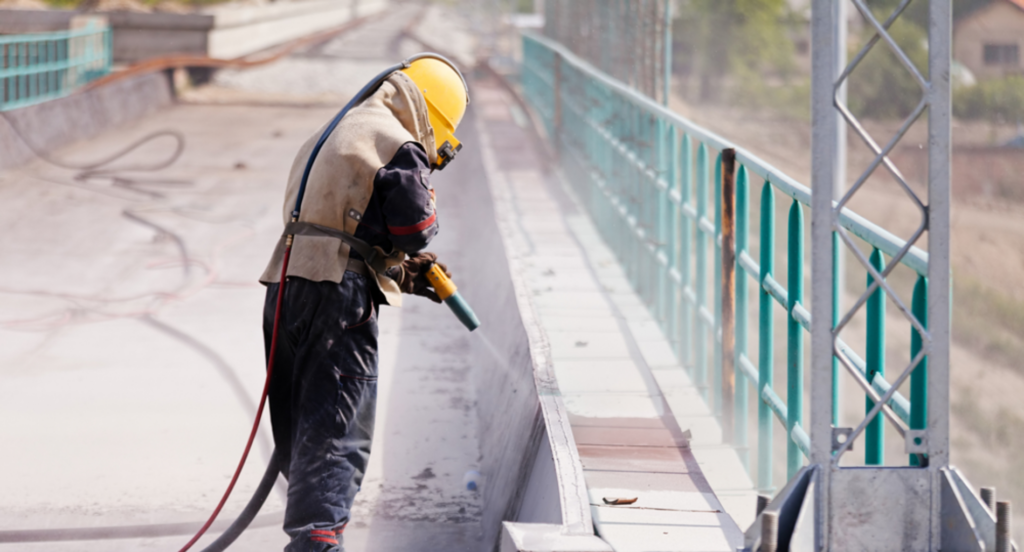
6. Challenges and Solutions in Abrasive Sand Blasting
Abrasive sand blasting, while highly effective, comes with its own set of challenges. Understanding these challenges and implementing effective solutions is crucial for maintaining efficiency and safety. Let’s explore some of the common issues and their resolutions:
Equipment Maintenance and Reliability
The equipment used in abrasive sand blasting can face wear and tear due to the abrasive nature of the materials used. Regular maintenance is often overlooked, leading to breakdowns and inefficiencies in the process. To address this, implementing a strict maintenance schedule is key. Regular checks and timely replacement of worn parts can significantly extend equipment life and ensure consistent performance.
Abrasive Material Disposal and Recycling
Disposing of used abrasive materials poses environmental concerns. The waste can be hazardous, and improper disposal can lead to pollution. Recycling used abrasive materials is an effective solution. Technologies for cleaning and reusing abrasives lessen environmental impact and cut down on costs for new materials. Additionally, using eco-friendly abrasives that are less harmful to the environment can be a beneficial practice.
7. 3 Tips for Choosing the Right Sandblasting Service
Selecting the appropriate sandblasting service is crucial for achieving desired outcomes in any project. It’s about finding a balance between expertise, equipment quality, and service scope. Here are the key factors to consider when making this important decision:
#1 Assessing Expertise and Experience
It’s essential to evaluate the expertise and experience of the sandblasting service. Look for a provider with a proven track record in handling projects. A company that has successfully managed complex and diverse projects demonstrates their capability to adapt and deliver quality results. Checking their portfolio and asking for client testimonials can offer valuable insights into their level of expertise.
#2 Equipment Quality and Capabilities
The quality and capabilities of the equipment used by the sandblasting service are paramount. High-quality, modern equipment ensures efficiency and better results. For example, a service using the latest automated blasting systems can offer more precise and uniform sandblasting, which is particularly important for large-scale projects. Ensure the service has the right tools to meet the specific needs of the project.
#3 Service Scope and Customization
When choosing a sandblasting service, it’s crucial to consider the range of services they offer and their ability to customize solutions. A reputable service should provide various blasting techniques, like wet, dry, and micro-abrasive blasting, to cater to different materials and desired finishes. Such as, a provider offering micro-abrasive blasting is ideal for delicate tasks, such as restoring vintage car parts, where precision is key.
Conclusion
This comprehensive guide has navigated the vital role of abrasive sand blasting in modern fabrication, detailing its techniques, applications, and benefits. It serves as a valuable resource for businesses seeking to optimize their metal fabrication processes.
If you’re looking for expert sandblasting services, Zemetal is your ideal partner. Contact us to explore how we can enhance your fabrication needs.
Dive Deeper Into Our Resources
Looking for more diverse service options? Browse through our handpicked selections:
Still haven’t found what you’re looking for? Don’t hesitate to contact us. We’re available around the clock to assist you.