What does HDG steel mean in the vast world of metal fabrication? Simply put, it refers to ‘hot-dip galvanized’ steel, a process crucial for enhancing the steel’s durability and resistance.
With years of experience in metal fabrication, this insight into HDG steel is tailored for those who seek reliable and practical solutions in the industry.
HDG steel not only becomes resistant to corrosion but also enhances longevity and reliability. This process ensures that structures and products can withstand harsh environments and demanding applications.
In the following sections, we’ll dive into the technical aspects of HDG steel, its diverse applications, and the economic impact it brings to your business.
Keep reading and discover the comprehensive world of HDG steel.
1. Defining HDG Steel
HDG steel, short for Hot-Dip Galvanized steel, is a type of carbon steel that undergoes a galvanizing process where it’s immersed in molten zinc. This coating process enhances the steel’s resistance to corrosion, significantly extending its lifespan in harsh environments. HDG steel is renowned for its durability, making it an ideal choice for outdoor or industrial applications where exposure to elements is a constant challenge.
Its versatility and strength also make it suitable for a wide range of uses, from construction and automotive industries to smaller scale metal fabrications, offering a reliable solution for various business needs.
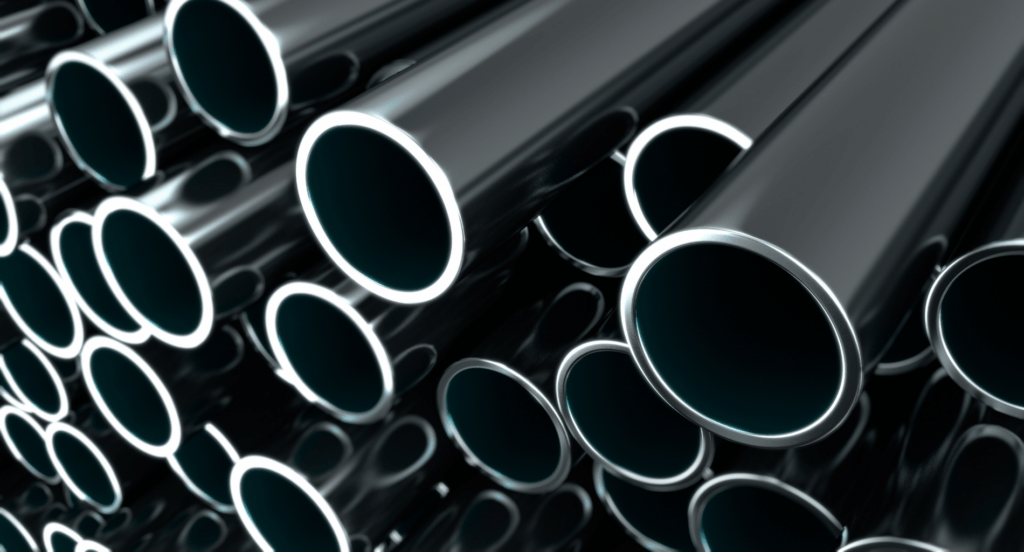
2. Benefits of Using HDG Steel
With a clear understanding of what HDG steel is, let’s explore its specific advantages for metal fabrication businesses. Here are four distinct benefits:
Superior Corrosion Resistance
HDG steel’s galvanization process creates a robust barrier against rust and corrosion. In metal fabrication, where materials are often exposed to corrosive environments, this property is invaluable. It ensures the longevity of metal components, especially in outdoor or marine applications, thereby reducing the frequency of replacements and maintenance costs.
Simplified Fabrication Process
The durability of HDG steel allows for a smoother fabrication process. Its resistance to damage during handling and transport means fewer defects and wastage. This property is particularly beneficial in large-scale production, where the consistency and integrity of materials are crucial for maintaining workflow efficiency and reducing operational downtimes.
Enhanced Aesthetic Appeal
HDG steel offers a sleek, uniform appearance that is desirable in visible structural elements or architectural features. This aesthetic quality is a significant advantage for fabricators working on projects where appearance is as important as functionality. The ability to provide both strength and visual appeal in one material is a considerable benefit for businesses looking to meet diverse client requirements.
Improved Safety in Fabrication
The strength and stability of HDG steel contribute to safer fabrication processes. For instance, its ability to withstand high stress and wear reduces the risk of accidents or structural failures during manufacturing and installation. Zemetal recognizes that this safety aspect is crucial for businesses aiming to maintain high safety standards and minimize liability risks.
3. Properties and Characteristics of HDG Steel
Following the exploration of HDG steel’s benefits for metal fabrication, it’s crucial to understand its properties and characteristics that make it so advantageous. Here are the key properties and characteristics:
Properties of HDG Steel
- Protection Against Corrosion: The zinc coating on HDG steel forms a protective barrier that shields the steel from moisture and pollutants, significantly reducing the risk of rust and corrosion.
- Self-Healing Feature: Minor damage to the coating can self-repair, as zinc’s galvanic action protects exposed steel by sacrificing itself, ensuring ongoing protection.
- Longevity: This durable coating extends the lifespan of steel products, making HDG steel a long-lasting solution in various environmental conditions.
Characteristics of HDG Steel
- High Tensile Strength: HDG steel exhibits superior strength, making it suitable for heavy-duty applications where structural integrity is paramount.
- Flexibility in Fabrication: Despite its strength, HDG steel retains enough ductility for shaping and forming, offering flexibility in fabrication processes.
- Resilience Under Stress: Its ability to withstand physical stresses without deforming makes it ideal for structural applications in construction and engineering.
4. The Manufacturing Process of HDG Steel
Exploring the properties and characteristics of HDG steel leads us to its manufacturing process. The transformation of steel into HDG steel involves several meticulous steps, crucial for achieving its renowned durability and performance. Here are the main stages:
Step#1 Surface Preparation
The first step in the HDG steel manufacturing process is surface preparation, which includes three crucial phases. It begins with degreasing, where the steel is thoroughly cleaned to remove any grease, dirt, and organic residues. The steel undergoes pickling, typically in an acid bath to eliminate rust and mill scale. The final step in this phase is is fluxing, where the steel is dipped in a zinc-ammonium chloride solution.
Step#2 Galvanizing
In the galvanizing phase, the prepared steel is submerged in a bath of molten zinc, usually at temperatures around 450°C (842°F). This process allows the zinc to bond with the steel, creating a robust, protective layer. During this stage, several layers of zinc-iron alloys form on the steel surface, which are harder than the steel itself, providing exceptional protection against wear and tear.
Step#3 Cooling and Finishing
After the hot-dip galvanizing, the steel is often quenched in water. This rapid cooling process is vital for enhancing the properties of the zinc coating and ensuring a smooth, uniform finish. At Zemetal, the steel then undergoes rigorous inspection and quality control to ensure the coating’s thickness and quality meet the required standards.
5. Applications of HDG Steel in Various Industries
Having explored the manufacturing process of HDG steel, we can now appreciate its widespread applications across various industries. Here are some of the primary industries and their uses of HDG steel:
Construction and Infrastructure
HDG steel’s extensive use in building frameworks provides a sturdy and enduring framework for diverse structures, crucial for ensuring their stability and safety over the long term. In light of projections by Global Construction Perspectives, which estimate an 85% growth in construction volume output, the importance of HDG steel in these applications is set to become even more significant.
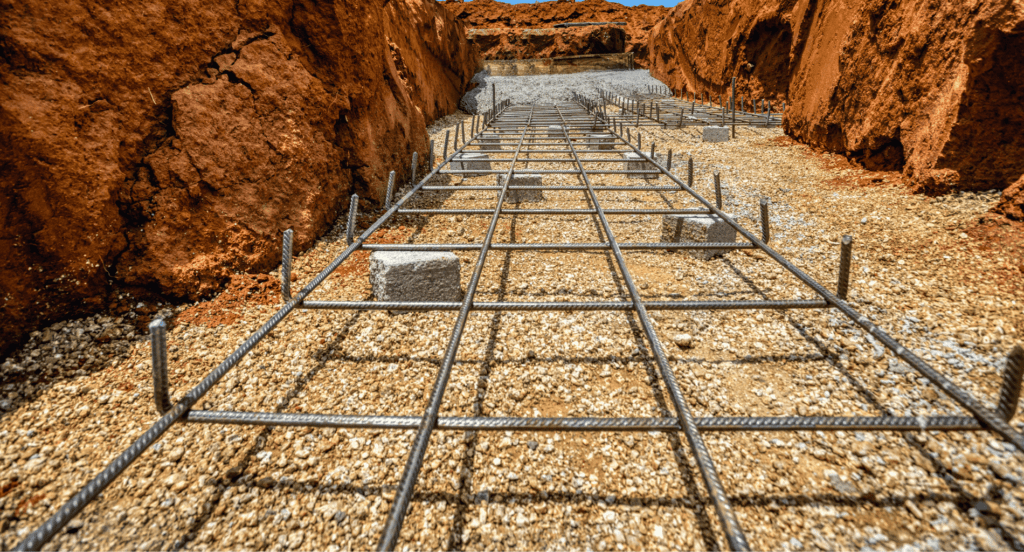
Automotive and Transportation
The automotive and transportation sector relies heavily on HDG steel for its ability to withstand harsh conditions and prolong the lifespan of components. Vehicle body parts made from HDG steel are better protected against rust, contributing to the longevity of vehicles. Additionally, it plays a crucial role in railway infrastructure, being utilized in railway tracks and supporting structures, where durability and safety are critical.
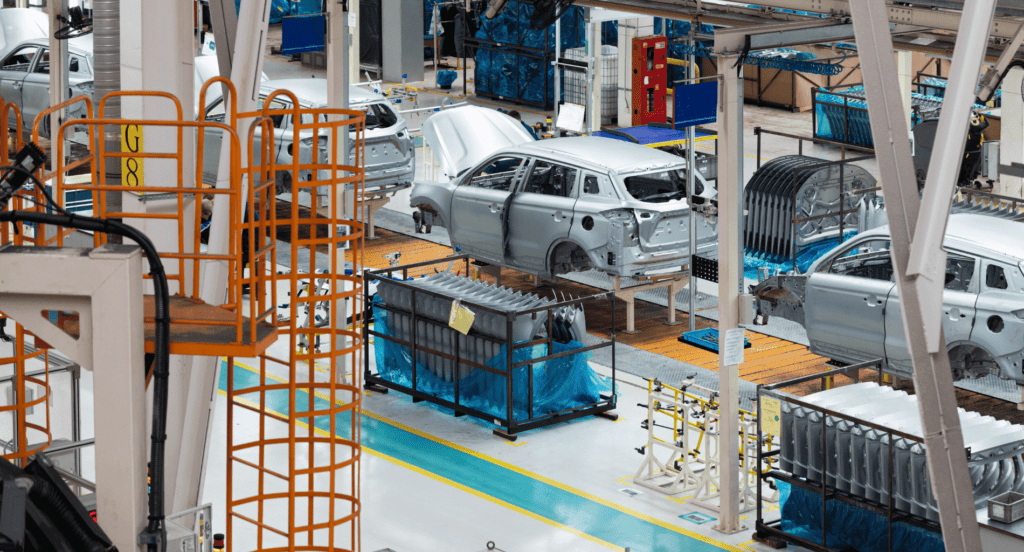
Industrial and Agricultural Equipment
In industrial and agricultural settings, the resilience and low maintenance of HDG steel are particularly advantageous. For instance, it is used in the manufacturing of machinery and heavy equipment, which require robust materials to withstand constant wear and tear. For storage and handling systems, such as grain silos and conveyor belts, HDG steel is ideal due to its protection against corrosion.
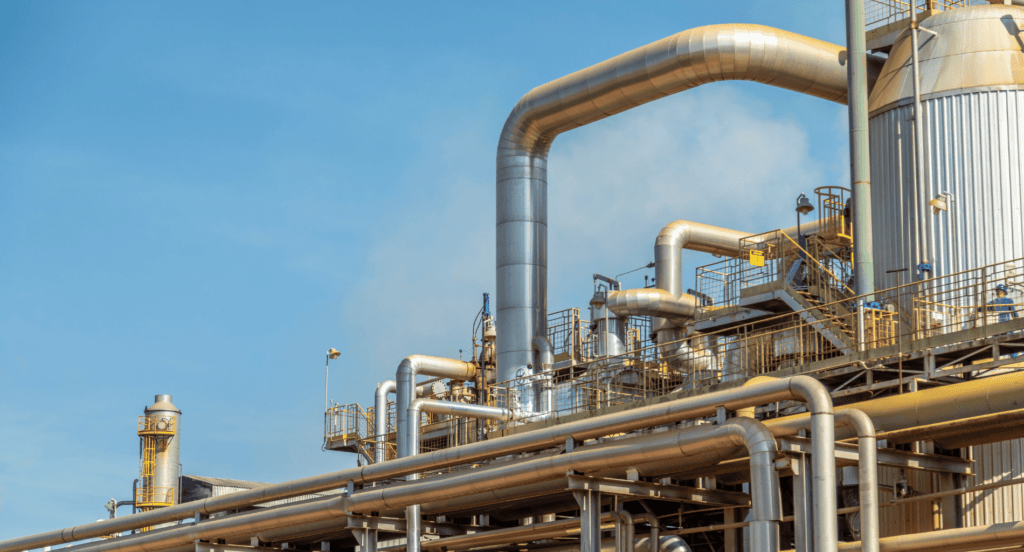
6. Challenges and Limitations of HDG Steel
While the applications of HDG steel in various industries are extensive, it is also important to acknowledge the challenges and limitations associated with its use. Here are the key challenges and limitations:
Challenges of HDG Steel
- Distortion During Galvanizing: The high temperatures used in the galvanizing process can cause dimensional changes or distortion in thinner steel components, posing challenges in precision applications.
- Higher Upfront Investment: Although cost-effective in the long term, the initial cost of HDG steel can be higher than other materials, which might be a barrier for small businesses or projects with tight budgets.
- Compatibility with Other Metals: When HDG steel is used in conjunction with different metals, galvanic corrosion can occur, especially in wet environments, necessitating careful planning in mixed-material projects.
Limitations of HDG Steel
- Aesthetic Changes: The shiny appearance of new HDG steel gradually dulls to a matte gray over time, which might not be desirable in applications where aesthetics are a priority.
- Complexity in Repairs: Damaged galvanized coatings can be challenging to repair, especially in the field, requiring specialized techniques and materials.
- Susceptibility to Certain Chemicals: HDG steel can be susceptible to corrosion from specific chemicals, such as strong acids or bases, limiting its use in certain chemical environments or industries.
7. Future Trends and Innovations in HDG Steel
Acknowledging the challenges and limitations of HDG steel is vital, but it’s equally important to look ahead at the future trends and innovations that are shaping its evolution. Here are some of the emerging trends and innovations in HDG steel:
Advanced Coating Technologies
In response to the need for improved performance and aesthetics, there is significant research and development in advanced coating technologies. These new coatings are designed to be more resilient, offering enhanced protection against corrosion and environmental factors. Moreover, they aim to maintain the aesthetic appeal of HDG steel over a longer period, addressing the issue of appearance changes over time.
The table below summarizes the key aspects of advanced coating technologies, particularly their application to hot-dip galvanized (HDG) steel:
Aspect | Description | Benefits |
Enhanced Durability and Resilience | Advanced coatings are designed to be more robust and withstand physical wear and tear. | Extends the lifespan of materials, reducing the need for frequent replacements or repairs. |
Improved Corrosion Resistance | These coatings provide a protective layer against rust and corrosion. | Preserves the structural integrity and functionality of metal surfaces, especially in harsh environments. |
Protection Against Environmental Factors | Formulated to resist environmental elements such as UV rays, moisture, and temperature changes. | Ensures long-term durability and performance of the coated materials in various climates. |
Aesthetic Appeal and Preservation | Focus on maintaining the original appearance of HDG steel over a longer period. | Addresses the issue of aesthetic degradation over time, keeping materials visually appealing. |
Research and Development | Ongoing innovation in material science to develop these advanced coatings. | Leads to the discovery of new, more effective, and environmentally friendly coating solutions. |
Eco-Friendly Production Processes
Sustainability is a growing concern in all industries, and the production of HDG steel is no exception. Future trends are likely to include more eco-friendly manufacturing processes that reduce environmental impact. This could involve innovations in reducing energy consumption during the galvanizing process or developing recycling methods that are more efficient.
Integration with Smart Technology
The integration of smart technologies in HDG steel production and application is an exciting frontier. This could involve embedding sensors in HDG steel structures for real-time monitoring of integrity and performance. Such innovations would allow for predictive maintenance, timely repairs, and overall safer and more efficient use of HDG steel in various applications.
Conclusion
HDG steel is a game-changer in the metal fabrication industry. Its robustness, and versatility make it an invaluable asset for businesses, wholesalers, and distributors. The knowledge of HDG steel’s meaning and applications empowers you to make informed decisions, ensuring the longevity and quality of your projects.
Zemetal, as a leader in metal fabrication services, understands the pivotal role of HDG steel in your business. Contact us today to learn more and start a partnership that drives success.
Dive Deeper Into Our Resources
Looking for more diverse service options? Browse through our handpicked selections:
For some insightful reads, we’ve curated a list of recommended articles just for you:
Still haven’t found what you’re looking for? Don’t hesitate to contact us. We’re available around the clock to assist you.