What sets anodized niobium apart in the industry of metal fabrication? This material distinguishes itself through its remarkable properties, offering unique benefits in various applications.
As a metal fabrication expert, understanding anodized niobium’s potential can revolutionize your approach to metal fabrication, offering innovative solutions for your business needs.
Anodized niobium’s remarkable resistance to corrosion, ability to take on vibrant colors, and hypoallergenic nature, can elevate the quality and aesthetic of your projects.
In this article, we’ll explore the unique properties of anodized niobium and how it can benefit your business.
Keep reading to uncover the secrets of anodized niobium.
1. Understanding Anodized Niobium
Anodized niobium undergoes a process called anodization, which enhances its natural properties through electrolytic passivation. This process thickens the metal’s oxide layer, increasing its resistance to corrosion and wear, and enables the absorption of dyes for vibrant and durable colorations. Ideal for industries prioritizing durability and aesthetics, anodized niobium is particularly valued for its hypoallergenic nature.
This makes it a popular choice in sectors like jewelry and medical device manufacturing, where material sensitivity is critical. The metal anodizing market, which includes processes like this, is expected to grow significantly. According to Verified Market Research, the market size is projected to reach USD 4.6 Billion by 2030, growing at a CAGR of 4.1% from 2023 to 2030.
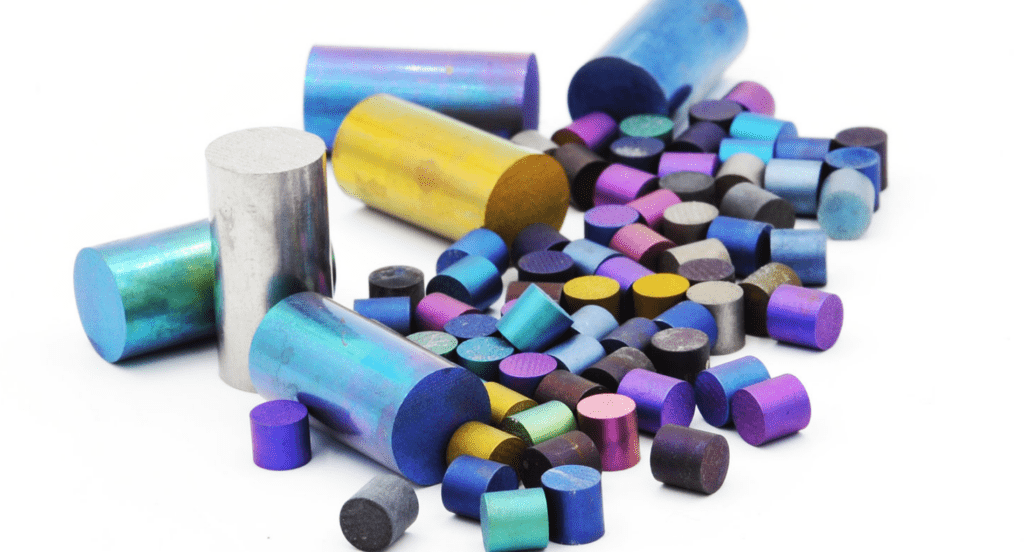
2. Advantages of Anodized Niobium for Metal Fabrication
After understanding the properties of anodized niobium, it’s important to focus on its specific advantages for metal fabrication. Here are key benefits tailored to this field:
- Enhanced Corrosion Resistance: Anodized niobium excels in its resistance to corrosion, making it ideal for use in harsh environmental conditions. This characteristic ensures longevity and integrity of fabricated parts, especially important in sectors like aerospace and marine engineering, where materials are exposed to corrosive elements.
- Improved Wear Resistance: The anodization process significantly increases the wear resistance of niobium, an essential factor in metal fabrication. This enhanced durability means components made from anodized niobium can withstand high stress and usage, reducing the need for frequent replacements and maintenance.
- Ease of Machining: Despite its strength, anodized niobium remains relatively easy to machine, a critical advantage in fabrication. This property allows for precise shaping and detailing, essential for creating complex components and intricate designs, thus expanding the creative and functional scope for fabricators.
- Thermal Stability: Anodized niobium offers excellent thermal stability, maintaining its properties across a wide temperature range. This makes it highly suitable for applications in extreme thermal environments, such as engine parts and heat exchangers in industrial settings, where consistent performance is crucial.
3. Unique Characteristics of Anodized Niobium
Having explored the advantages of anodized niobium in metal fabrication, it’s also essential to delve into its unique characteristics. Here are the distinct features that set anodized niobium apart in the field:
Exceptional Coloration Capabilities
According to Jewellery Business, anodized niobium is renowned for its ability to take on rich, vibrant colors through anodization. This unique characteristic is due to the formation of an oxide layer that can refract light, creating a spectrum of colors without the need for dyes. This feature is particularly valuable for applications where both the strength of metal and aesthetic appeal are required.
Non-Magnetic Nature
An often-overlooked characteristic of anodized niobium is its non-magnetic nature. This makes it an ideal material for applications where magnetic interference must be avoided, such as in sensitive electronic equipment and medical devices. This property enhances the scope of its use in various technologically advanced sectors.
Bio-Compatibility
Niobium’s bio-compatibility, further enhanced by the anodization process, is a critical factor in its application in medical devices and implants. This characteristic ensures that anodized niobium can be safely used in the human body without adverse reactions, making it invaluable in the medical field for both surgical tools and implants.
4. Anodizing Process of Niobium
Following our examination of the unique characteristics of anodized niobium, it’s vital to understand the step-by-step process of anodizing niobium. Here are the critical stages that transform niobium into its anodized form:
Step#1 Cleaning and Preparation
The first step in the anodizing process is thoroughly cleaning the niobium. This involves removing any contaminants, oils, or residues that might interfere with the anodization. Proper cleaning ensures a uniform and consistent oxide layer, which is crucial for achieving the desired properties and appearance.
Step#2 Electrolytic Bath
Once cleaned, the niobium is submerged in an electrolytic bath, typically composed of acids like sulfuric or phosphoric acid. This bath serves as a medium for the anodization process, where an electrical current is applied. The specific composition and parameters of the bath can vary based on the desired outcome of the anodization.
Step#3 Application of Electrical Current
The core of the anodizing process is the application of an electrical current through the niobium while it’s in the electrolytic bath. At Zemetal, this current causes an oxide layer to form on the surface of the metal. The thickness and characteristics of this layer can be controlled by adjusting the current’s voltage and duration.
Step#4 Coloring and Sealing
After the oxide layer is formed, the niobium can be colored if desired. The unique property of anodized niobium to refract light allows for a range of colors without external dyes. Following the coloring, the niobium is sealed to enhance the durability of the oxide layer and to lock in the color, completing the anodizing process.
5. Industrial Applications of Anodized Niobium
Having detailed the anodizing process of niobium, it’s essential to explore how this material is utilized in various industrial sectors. Here are some of the key applications of anodized niobium in the industry:
Aerospace and Aviation
In the aerospace and aviation industries, anodized niobium is prized for its strength-to-weight ratio and corrosion resistance. For instance, its use in components like engine parts, fasteners, and structural elements helps improve the longevity and performance of aircraft, making it a valuable material in these high-demand environments.
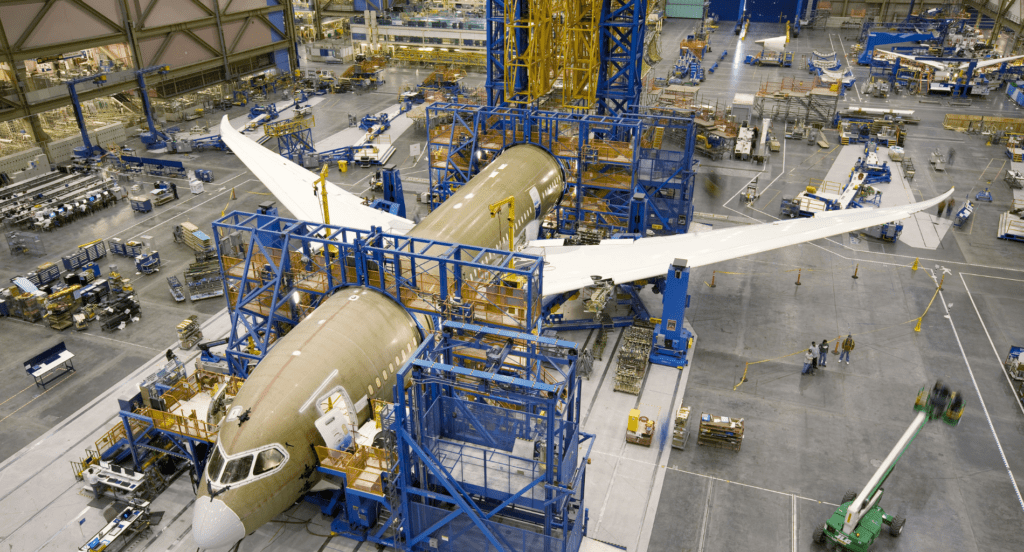
Medical Devices
Anodized niobium’s bio-compatibility makes it an excellent choice for medical devices and implants. Its use ranges from surgical instruments to implants, such as pacemakers and orthopedic devices. The material’s non-reactive nature ensures safety and durability, crucial in medical applications.
Consumer Electronics
In the consumer electronics industry, anodized niobium offers both functional and aesthetic benefits. Its non-magnetic properties are essential for electronic components, while its ability to be colored enhances the visual appeal of consumer products like smartphones, laptops, and wearable devices. This dual advantage makes anodized niobium a highly sought-after material in this rapidly evolving sector.
6. Economic Aspects of Anodized Niobium
Following our exploration of the industrial applications of anodized niobium, it’s important to consider its economic aspects. Here are the key economic factors associated with the use of anodized niobium in various industries:
Cost-Effectiveness
Anodized niobium, while initially more expensive than some traditional materials, offers long-term cost-effectiveness due to its durability and low maintenance requirements. Its longevity reduces the need for frequent replacements and repairs, providing significant savings over time, especially in industries where material longevity is critical.
Market Demand
The unique properties of anodized niobium have led to a growing market demand, particularly in high-tech and specialized sectors like aerospace, medical devices, and consumer electronics. This increasing demand influences the market value and production costs of anodized niobium, making it a significant material in the global economy.
This table illustrates the growing market demand for anodized niobium, highlighting its applications in various industries and the consequent impact on market value and production costs.
Sector | Application | Impact on Market Demand |
Aerospace | Used for lightweight, corrosion-resistant components | Drives demand due to performance requirements |
Medical Devices | Ideal for biocompatible implants and instruments | Increases value due to specialized use |
Consumer Electronics | Utilized in high-performance electronics | Boosts demand for advanced materials |
Market Value | Growing preference increases material value | Influences global economic significance |
Production Costs | High-tech processing elevates costs | Affects pricing and accessibility in markets |
Investment in Innovation
Investing in anodized niobium technology represents a commitment to innovation. Companies that utilize this material are often seen as leaders in adopting advanced materials, which can lead to increased business opportunities and partnerships, especially in sectors that value cutting-edge technological advancements.
7. 4 Maintenance Tips for Anodized Niobium Products
After considering the economic aspects of anodized niobium, maintaining its integrity and appearance over time is equally important. Here are essential maintenance tips for ensuring the longevity of anodized niobium products:
#1 Regular Cleaning
Regular cleaning is vital to maintain the appearance and integrity of anodized niobium. Use mild soap and water to gently clean the surface, avoiding abrasive materials that can scratch or damage the anodized layer.
#2 Avoiding Harsh Chemicals
It’s crucial to avoid harsh chemicals when cleaning anodized niobium. Strong acids or alkalis can damage the anodized layer, compromising its protective qualities. Stick to neutral pH cleaners to ensure the anodization remains intact and effective.
#3 Proper Storage
Proper storage is key to preserving anodized niobium products, especially in environments prone to moisture or extreme temperatures. Store these items in a dry, cool place to prevent any deterioration of the anodized layer, which can be affected by environmental conditions.
#4 Routine Inspections
Regular inspections can help identify any issues with the anodized layer, such as scratches or wear, early on. Promptly addressing these problems can prevent further damage and maintain the material’s protective and aesthetic qualities.
8. Factors to Consider When Considering Anodized Niobium
Reflecting on the maintenance aspects of anodized niobium, when considering this material for your projects, it’s important to weigh several key factors. Here are essential considerations:
Suitability for Intended Use
When considering anodized niobium, assess its suitability for your intended use. For instance, this includes evaluating its corrosion resistance, strength, and hypoallergenic properties against the demands of your specific application. Ensuring compatibility with your project’s requirements is crucial for optimal performance and longevity.
Coloration and Aesthetic Impact
One of the unique features of anodized niobium is its ability to be colored through anodization. Consider how the range of color options and the potential for custom hues align with your project’s aesthetic needs. This factor is especially important for applications where visual appeal is a priority.
Environmental and Temperature Considerations
Anodized niobium’s performance can vary depending on environmental and temperature conditions. Consider factors like exposure to harsh chemicals, extreme temperatures, and environmental stressors. Zemetal recognizes that understanding these aspects will help in determining if anodized niobium is the right choice for your project’s environment.
Long-term Durability and Maintenance
Finally, weigh the long-term durability and maintenance requirements of anodized niobium. While it is known for its durability and low maintenance needs, understanding the specific upkeep and potential wear and tear over time will help in making an informed decision about its use in your projects.
Conclusion
As we’ve explored, anodized niobium presents a wealth of opportunities for businesses in the metal fabrication sector. Embracing anodized niobium can set your business apart, offering products that are not only functional but also aesthetically pleasing and long-lasting.
For those ready to take their metal fabrication projects to the next level, Zemetal offers comprehensive metal fabrication services tailored to your specific needs. Contact us today and see how we can help.
Dive Deeper Into Our Resources
Looking for more diverse service options? Browse through our handpicked selections:
For some insightful reads, we’ve curated a list of recommended articles just for you:
Still haven’t found what you’re looking for? Don’t hesitate to contact us. We’re available around the clock to assist you.