Ever wondered which is the superior choice for metal protection: anodizing or electroplating? Each has its unique advantages in the realm of metal fabrication.
With extensive experience in metal fabrication, I offer a comprehensive perspective on these vital protective processes.
Anodizing and electroplating enhances the durability and aesthetic appeal of metals. Anodizing transforms the metal surface into a robust, corrosion-resistant oxide finish, while electroplating deposits a metal coating via chemical or electrochemical means.
This article will explore the advantages and challenges of anodizing and electroplating, providing insights to help you make an informed decision for your metal fabrication needs.
Keep reading to uncover the intricacies of these two metal protection strategies.
1. Overview of Surface Finishing
Surface finishing in metal fabrication is essential for improving the exterior qualities of metal, such as appearance, corrosion resistance, and surface hardness. This not only prolongs the durability of metal products but also ensures they fulfill specific functional and aesthetic standards. Key techniques in this field include anodizing and electroplating.
Regarding the global metal anodizing market, according to Coherent Market Insights, it was valued at approximately US$ 757.51 million in 2021. Demonstrating a Compound Annual Growth Rate (CAGR) of 5.92%, this market is projected to grow significantly during the forecast period from 2022 to 2030.
2. Understanding Anodizing
Anodizing is a specialized electrochemical process used to increase the thickness of the natural oxide layer on the surface of metal parts, primarily aluminum. This technique enhances the metal’s durability, corrosion resistance, and aesthetic appeal, making it a popular choice for various industrial and consumer applications. However, it’s limited to certain metals and can involve higher costs and potential color inconsistencies.

Benefits of Anodizing
- Enhanced Durability: Anodizing strengthens the natural oxide layer on aluminum, significantly increasing its resistance to wear and tear. This makes it ideal for high-use components.
- Corrosion Resistance: The anodized layer offers excellent protection against corrosion, essential for metal parts exposed to harsh environments or corrosive substances.
- Aesthetic Appeal: Anodizing allows for a range of colors and finishes, providing an attractive and customizable appearance that does not chip or peel easily.
Disadvantages of Anodizing
- Limited to Certain Metals: Anodizing is mainly effective on aluminum and cannot be universally applied to all metal types, limiting its applicability.
- Color Inconsistencies: While offering color options, anodizing can sometimes result in color variations, which may be a concern for specific applications or designs.
- Higher Costs: Compared to some other finishing processes, anodizing can be more expensive due to its specialized equipment and energy requirements, potentially impacting the overall project budget.
3. Exploring Electroplating
Electroplating is a process that involves the application of a thin layer of metal onto the surface of another metal through an electrochemical procedure. It’s known for its versatility and ability to enhance both the aesthetics and physical properties of metals. Electroplating is widely used for a variety of metals, offering improved wear resistance, corrosion resistance, and a range of aesthetic finishes like glossy, matte, or satin.
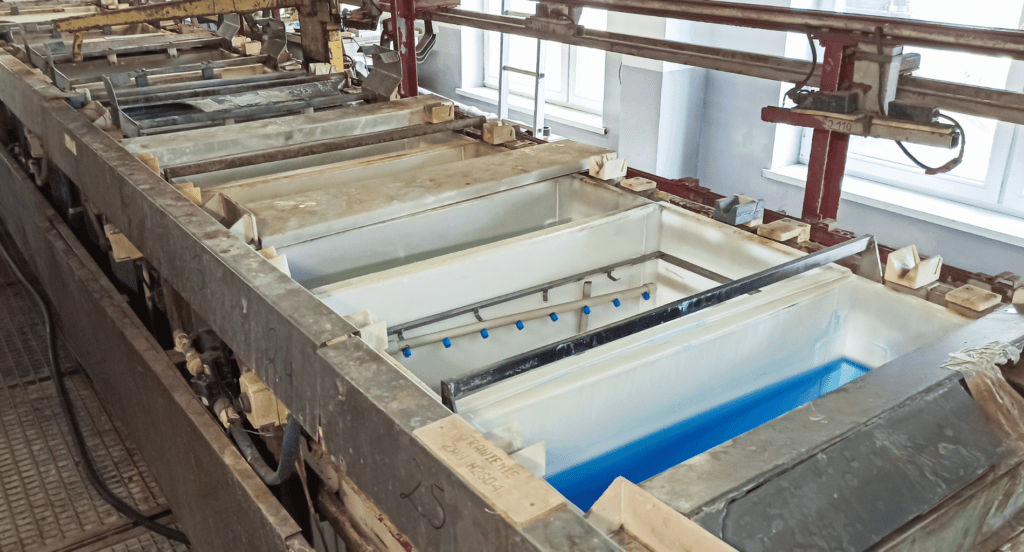
Benefits of Electroplating
- Versatile Material Compatibility: Electroplating can be applied to a wide range of metals, offering more versatility than anodizing in terms of applicable materials.
- Improved Aesthetics: This technique allows for a variety of finishes, including glossy, matte, or satin, enhancing the visual appeal of the metal product.
- Enhanced Physical Properties: Electroplating can increase the hardness, corrosion resistance, and wear resistance of the base metal, making it more durable and long-lasting.
Disadvantages of Electroplating
- Environmental Concerns: The process often involves toxic chemicals and can produce hazardous waste, posing environmental and health risks if not managed properly.
- Uneven Coating Issues: Achieving uniform thickness can be challenging in electroplating, leading to potential weak spots or inconsistencies in coating.
- Maintenance Requirements: Electroplated surfaces may require regular maintenance to retain their aesthetic and protective qualities, especially in harsh environments.
4. Comparative Analysis: Anodizing vs. Electroplating
After delving into the specifics of electroplating, it becomes imperative to contrast it with anodizing for a comprehensive understanding of their respective roles in metal fabrication. Here’s an in-depth look at some critical comparative aspects:
Metal Type Compatibility
- Anodizing: Excelling primarily with aluminum and its alloys, anodizing is somewhat restricted in its application to other metals. At Zemetal, this process enhances the natural oxide layer, offering significant benefits for aluminum but limiting its utility for diverse metal types.
- Electroplating: Showcases its versatility by being applicable to a vast range of metals, including common ones like steel, brass, and copper. This adaptability makes it a go-to choice for projects requiring coating on various metals, thereby catering to a broader spectrum of industrial needs.
Finish Durability and Aesthetic Diversity
- Anodizing: Known for producing a hard, durable finish, anodizing also allows for a range of customizable colors. However, it can sometimes struggle with achieving color uniformity across different batches, which might be a drawback for projects requiring consistent coloration.
- Electroplating: Offers an impressive variety of finishes, from glossy to matte, and a wide array of colors. This flexibility makes it particularly suitable for decorative purposes or when a specific aesthetic is a priority. However, the quality of the finish can depend on the electroplating process’s precision and the base metal’s quality.
Environmental and Health Considerations
- Anodizing: Stands out as a more environmentally friendly option, generating less hazardous waste and using fewer toxic chemicals. For instance, this aspect is increasingly important in industries seeking to minimize their environmental footprint and comply with strict environmental regulations.
- Electroplating: Involves hazardous materials and chemicals, raising significant environmental and health concerns. Proper handling, disposal, and safety measures are essential, which can add complexity and cost to the process, especially in regions with stringent environmental laws.
Precision in Coating Thickness and Uniformity
- Anodizing: Offers a reliable consistency in coating thickness and uniformity, a vital factor for components where precise dimensional tolerances are critical. This uniformity also contributes to the overall durability and quality of the finished product.
- Electroplating: Achieving uniform coating thickness can be a challenge, especially on complex shapes or uneven surfaces. For instance, inconsistent thickness can lead to weak spots or areas prone to quicker wear, impacting both the aesthetic and functional aspects of the coated metal. This requires careful process control and expertise to ensure uniform coverage and optimal performance.
5. 3 Tips for Choosing the Right Process for Your Needs
After a comparative analysis of anodizing and electroplating, the next crucial step is to discern which method aligns best with specific metal fabrication requirements. Here are the critical considerations to help you make an informed decision:
#1 Consideration of Metal Type and Properties
Anodizing is particularly effective for aluminum and its alloys, making it the preferred choice when these materials are in use. On the other hand, electroplating is more versatile and can be applied to a broader range of metals, including less reactive ones. It’s ideal when the properties of a specific metal need significant alteration or enhancement, such as improving hardness or electrical conductivity.
#2 Aesthetic Goals and Finish Requirements
Anodizing is well-suited for projects requiring a durable finish, like for aluminum products where aesthetic consistency and longevity are key. Conversely, electroplating offers a greater degree of aesthetic flexibility, with a wide range of colors and textures available. It’s the preferred method for projects where visual appeal is a concern, offering finishes ranging from shiny and glossy to matte and textured.
Anodizing and electroplating serve distinct purposes in providing finishes for various projects, as depicted in the table below.
Finish Method | Key Attributes |
Anodizing | Durable finish ideal for aluminum products, ensuring longevity and aesthetic consistency. |
Electroplating | Offers diverse aesthetic options with a wide array of colors and textures for enhanced visual appeal. |
Aesthetic Range | Limited color options but provides consistent finishes for projects prioritizing durability. |
Visual Flexibility | Extensive range of colors and textures, catering to projects emphasizing visual aesthetics. |
Material Suitability | Ideal for aluminum products needing longevity; may not suit all materials due to process specifics. |
#3 Long-term Durability and Maintenance
Anodizing typically offers enhanced durability with minimal maintenance needs, making it advantageous for outdoor or high-wear applications. Electroplating, while providing excellent corrosion resistance and aesthetic versatility, may necessitate more frequent maintenance. Zemetal understands that this aspect is crucial for projects where ongoing maintenance is a concern or where long-term durability is a paramount factor.
Conclusion
In the ultimate showdown, it’s clear that both methods offer distinct advantages depending on your specific metal fabrication requirements. Anodizing excels in enhancing corrosion resistance and wear properties. On the other hand, electroplating offers a wide range of finishes and coatings for various metals.
At Zemetal, we are ready to guide you in selecting the best process—be it anodizing or electroplating—for your project. Contact us today to explore how we can elevate your metal fabrication projects to new heights.
Dive Deeper Into Our Resources
For some insightful reads, we’ve curated a list of recommended articles just for you:
Still haven’t found what you’re looking for? Don’t hesitate to contact us. We’re available around the clock to assist you.