What if it was revealed that anodised brass could transform metal fabrication businesses? Anodised brass, known for its durability, aesthetics, and corrosion resistance, benefits various industries in metal fabrication.
As an experienced expert in metal fabrication, I’ve personally observed the substantial improvements in efficiency and precision that these technologies can bring about.
Anodised brass is a remarkable material known for its durability, aesthetics, and versatility. Businesses across various industries rely on anodised brass for its corrosion resistance and attractive finish.
This article explores brass anodizing, its applications, advantages, and how it can enhance metal fabrication projects for both beginners and experts.
Read on to understand brass anodizing’s impact in metal fabrication.
1. Basics of Anodisation
Anodisation is vital because it enhances metal in two key ways: by strengthening the surface for demanding tasks and preventing rust that can weaken and diminish its usefulness. The importance of anodisation is underscored by the anticipated growth in the Global Anodizing market, which, according to LinkedIn, is expected to rise significantly during the forecast period between 2022 and 2030.
The growth in anodisation reflects its recognized benefits, such as the enduring resilience and appearance of anodised brass. Why is anodisation important? Firstly, it fortifies the metal surface, making it robust for challenging tasks. Secondly, it provides strong defense against rust, preventing the reduction of metal’s utility. Through anodisation, metals not only retain their strength but also their aesthetic appeal over time.
2. Benefits of Anodised Brass
Having explored the fundamentals of anodization, it’s time to dive into the remarkable advantages of anodized brass. Here are the following:
Enhanced Durability
Anodised brass becomes extremely durable after the anodisation process, similar to giving brass a protective suit of armor. This heightened durability ensures the metal’s resilience against challenging conditions and extensive usage while maintaining its visual appeal over time. Opting for anodised brass represents a prudent investment in enduring quality.
Anodized brass gains remarkable durability through the anodization process, akin to a protective armor, ensuring resilience and long-lasting visual appeal. This table details key aspects of anodized brass:
Aspect | Description |
Enhanced Durability | Anodization significantly increases brass’s resistance to wear, tear, and corrosion. |
Maintained Aesthetics | The process preserves brass’s visual appeal, preventing discoloration and dullness. |
Resistance to Conditions | Anodized brass withstands harsh environmental conditions like moisture and UV exposure. |
Longevity | The treatment extends the lifespan of brass, making it a long-term investment. |
Cost-Effectiveness | Despite initial costs, the long-term durability makes anodized brass a cost-effective choice. |
Corrosion Resistance
One of the standout advantages is corrosion resistance. After anodisation, brass becomes highly resistant to rust and corrosion. It’s similar to giving the metal a strong shield, protecting it from the toughest elements. I’ve seen this resilience in action, and it’s truly impressive how the quality ensures that the metal products remain in impeccable condition, even when subjected to demanding environments.
Low Maintenance
Maintaining anodised brass is straightforward, as it does not necessitate ongoing polishing or cleaning. Its resistance to tarnishing and discoloration ensures it retains its aesthetic appeal with minimal upkeep. This feature is similar to having self-maintaining metal, making it perfect for situations where low maintenance is very important.
Eco-Friendly Choice
Selecting anodised brass also aligns with environmentally conscious practices. Anodisation uses fewer harmful chemicals than some other metal treatments, making it an eco-friendly choice while enjoying top-quality metal. Environmentally friendly products typically rely on renewable natural resources, making them a cost-effective alternative to artificially produced items.
3. Properties of Anodised Brass
After thoroughly exploring the benefits of anodised brass, we can now delve into the key properties of anodised brass, shedding light on the unique characteristics that make it a favored choice in the world of metal fabrication:
Surface Hardness
Anodised brass acquires impressive surface hardness through the anodisation process, akin to equipping brass with enhanced armor. This heightened hardness boosts its ability to withstand wear and tear, guaranteeing longevity in challenging applications. Additionally, this increased hardness also aids in maintaining the metal’s pristine appearance over time.
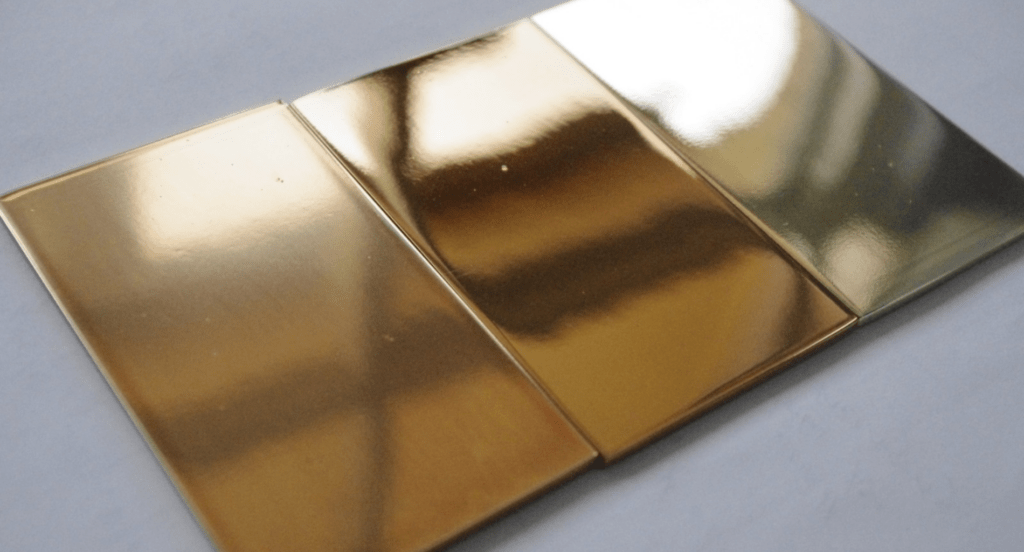
Electrical Insulation
One noteworthy property is its electrical insulation capacity. After anodisation, brass becomes an effective insulator, similar to rubber insulating wires. This feature is especially valuable when wanting to prevent electrical conductivity, making it useful in different applications. For instance, in electrical panels, anodized brass components can insulate and separate conductive elements, ensuring safety and functionality.
Thermal Resistance
Anodised brass, like a reliable heat-resistant shield, maintains its structural integrity even in high temperatures. This quality is particularly valuable in heat-sensitive applications. This feature, from my experience, makes it an ideal choice for applications where dealing with heat is a common concern. Its thermal resistance enhances the lifespan of components exposed to fluctuating temperatures.
Dimensional Stability
Dimensional stability stands out as a significant attribute, with anodised brass preserving its form and dimensions despite shifts in environmental conditions. It’s comparable to having metal that remains unaffected by warping or expansion when circumstances change, guaranteeing accuracy in projects. This stability is crucial for precision parts where exact measurements are essential.
Decorative Finishes
Anodised brass offers a wide range of decorative finishes, akin to selecting a car color. It allows the choice of various colors and styles to match the project’s aesthetics, similar to a design palette for metal. This flexibility in customization not only enhances the visual appeal but also adds a unique character to each project. Personally, I find this aspect thrilling, as it allows each project to have its unique flair and personality.
4. The Anodising Process for Brass
After looking at what makes anodised brass special, here are the steps in the anodising process for brass, showing how brass becomes strong and tough:
Step#1 Surface Preparation
In the initial stage of the anodising process, meticulous attention is given to preparing the brass surface. This includes a thorough cleaning process to eliminate any grease or dirt. The significance of this step cannot be overstated, as it plays a pivotal role in ensuring that the resulting anodised finish maintains a consistent, smooth, and even appearance.
Step#2 Anodising Bath
Following that, the brass undergoes immersion in a specially crafted anodising bath. This bath can be likened to a mysterious potion that initiates the transformation process. Inside this bath, an electric current flows through and into the brass, resulting in the formation of a protective oxide layer on the surface of the metal. This chemical reaction boosts brass’s strength and durability, ensuring it can handle diverse challenges.
Step#3 Coloring Options
After the anodisation process, brass becomes capable of taking on a unique color selection. With an extensive range of color options available, it’s possible to customize the brass to blend seamlessly with the project’s visual theme. This process is like giving metal a unique makeover, infusing a personal touch into the final product, and enhancing its aesthetic appeal.
Step#4 Sealing
To secure the advantages, anodised brass goes through a sealing process. This step is crucial because it’s like locking in the benefits, ensuring the protective layer remains intact, and preserving the vibrant color. I’ve seen how this final touch is similar to adding the last brushstroke to the metal masterpiece, giving it that personal flair and making it ready for use and display.
Step#5 Quality Inspection
Before anodised brass is deemed ready for its intended purpose, it undergoes a meticulous and comprehensive quality inspection process. This crucial step ensures the final product meets high performance and appearance standards. Zemetal’s meticulous attention to detail in this phase is crucial for anodised brass to exceed expectations and offer top-notch quality and reliability.
5. Applications of Anodised Brass
After exploring the intricacies of the anodising process for brass, let’s now proceed into the diverse applications of anodised brass. In the following subsections, we’ll highlight its various applications:
Architectural Features
Anodised brass is a favored material in architectural applications, lending a touch of both elegance and durability. Whether in the form of door handles or decorative fixtures, it elevates the aesthetics of buildings while proving its resilience over time. It’s a choice I’ve frequently encountered in architectural designs, appreciated for its enduring beauty and functionality.
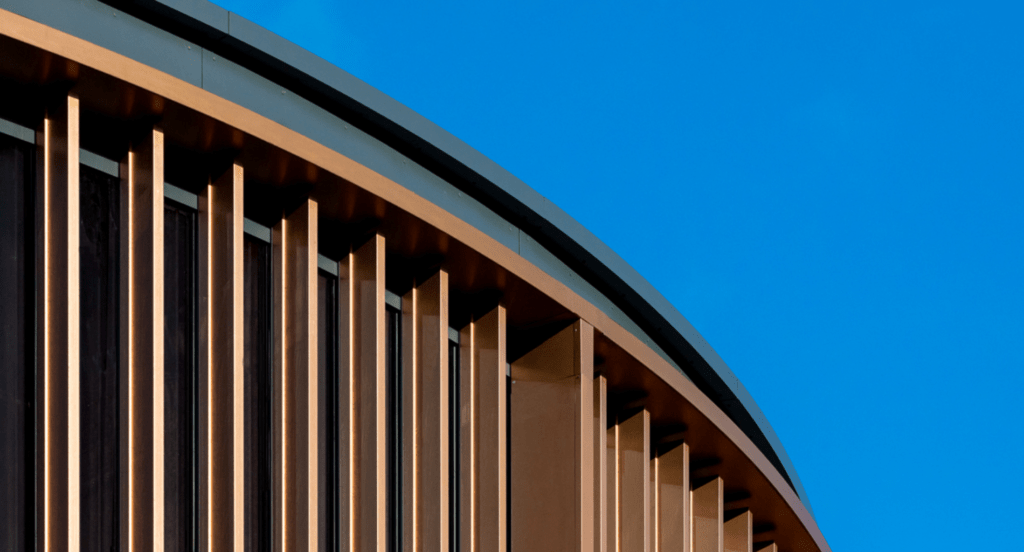
Jewelry and Accessories
Anodised brass is a fantastic choice for crafting jewelry and accessories. It adds a unique style while making these items strong and durable. Whether it’s rings, necklaces, or other lovely pieces created with anodised brass, they can withstand the test of time and retain their attractive appearance. This makes it a popular option for those who want both beauty and longevity in their accessories.
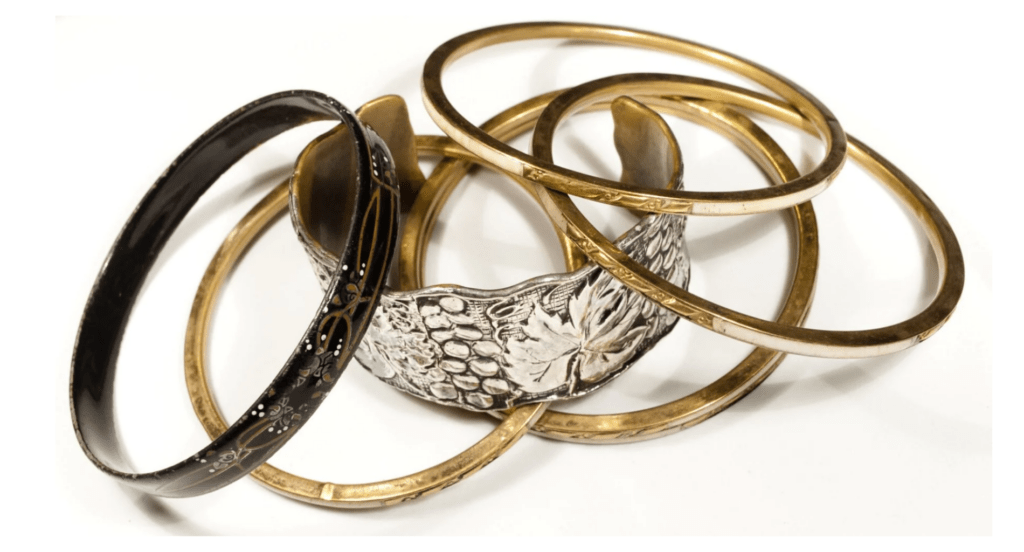
Industrial Components
Anodised brass components shine in industrial settings because they have two important qualities: they don’t easily corrode, and they stay the same size even when conditions change. These properties are a big plus when they’re using them in machines, equipment, and tools because they ensure these items perform reliably, even in challenging environments where rust or changes in size could be a problem.
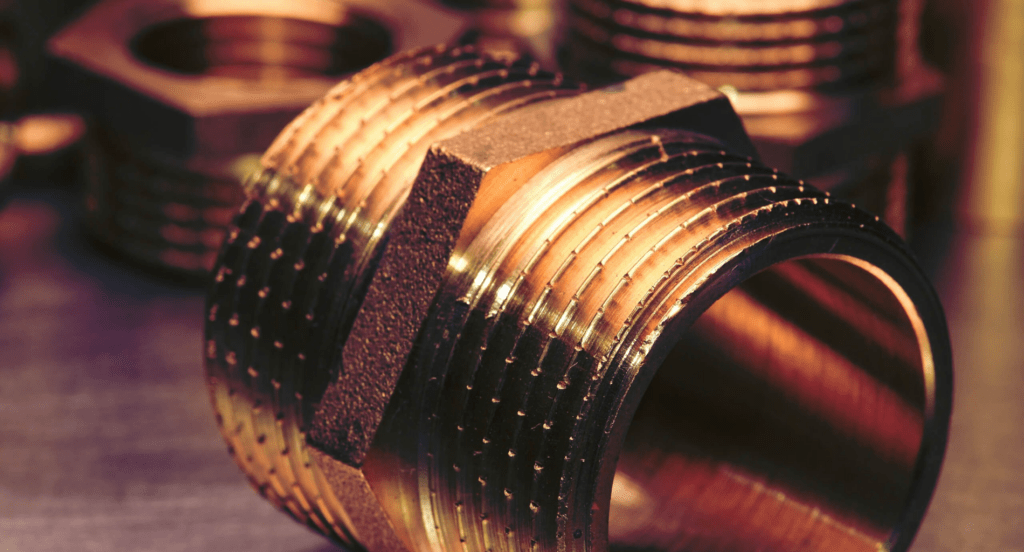
Marine and Nautical Applications
In maritime industries, anodised brass holds significant value due to its exceptional resistance to the corrosive nature of saltwater. Whether it’s applied to boat fittings or crucial navigational equipment, anodised brass ensures that these vital components maintain their structural integrity over time. This makes it a wise choice for maritime ventures, where saltwater and tough marine conditions are always a challenge.
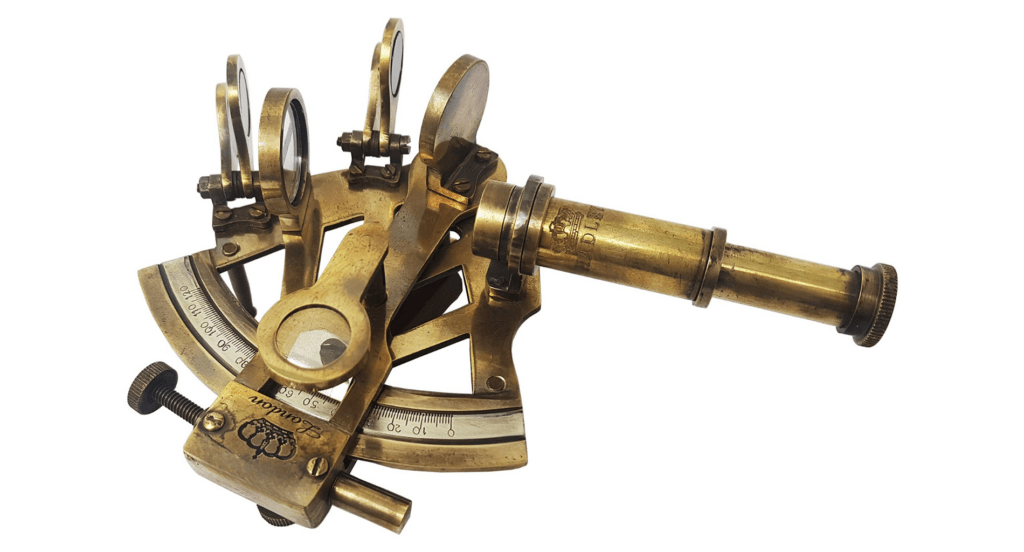
6. Challenges and Solutions in Anodising Brass
After exploring the various applications, let’s now uncover the challenges and their solutions in the process. Below are the main challenges and solutions to anodising brass, as addressed by industry experts:
Surface Preparation Challenges
Anodising brass begins with surface preparation, which can be challenging if the brass is heavily soiled or corroded. The solution lies in thorough cleaning and pre-treatment processes to ensure a pristine surface, ready for anodisation. This step is crucial in my experience, as it sets the foundation for a successful anodising process.
Color Consistency
Maintaining consistent color during the anodising process can be a challenge, especially when dealing with large batches of brass. Solutions involve precise control of processing parameters, such as temperature and voltage, to ensure uniform coloration. This meticulous control plays a vital role in achieving the desired results, particularly in projects where color consistency matters.
Corrosion Control
While anodized brass is renowned for its corrosion resistance, keeping it protected in harsh environments can be challenging. For example, in coastal areas with high salt exposure, the application of a protective clear sealer becomes a valuable strategy. This additional layer of defense significantly extends the life of anodized brass components, ensuring they remain corrosion-free.
Cost-Efficiency
Balancing quality and cost-effectiveness is a significant challenge in anodising brass. However, industry professionals have discovered that selecting efficient anodising techniques and closely managing process variables can help strike that delicate balance between maintaining high quality and staying within budget. This balance is crucial, particularly in cost-conscious projects, while still meeting performance expectations.
7. Maintenance Tips and Care for Anodized Brass
After covering the challenges and solutions in anodizing brass, let’s now explore proper maintenance and care for anodized brass components. Below is practical advice on maintaining the luster and durability of anodized brass to ensure it remains in excellent condition:
Regular Cleaning
Preserving the look of anodized brass involves regular cleaning as a fundamental measure. Achieve this by utilizing a gentle detergent along with a soft cloth or sponge to efficiently eliminate built-up dirt and grime. This straightforward cleaning, backed by experience, preserves the shine and finish of anodized brass components. Incorporating it in regular maintenance guarantees prolonged aesthetic upkeep.
Avoid Abrasive Materials
When cleaning anodized brass, it’s crucial to steer clear of abrasive materials like steel wool or abrasive cleaning pads. I’ve seen how these tools can potentially create surface scratches, putting the anodized layer at risk of damage. Instead, choose soft materials for cleaning to maintain the brass’s integrity. This precautionary step helps prevent unsightly scratches, preserving the overall quality and appearance of the anodized brass.
Protective Coatings
Considering the application of a protective clear coat to anodized brass components is worthwhile, especially in settings exposed to outdoor conditions or high levels of traffic. The clear coat adds an extra layer of defense, preserving brass appearance and durability in challenging conditions. Zemetal prioritizes the quality and durability of their anodized brass components, ensuring they meet the highest industry standards.
Routine Inspection
Regularly inspect anodized brass components for signs of wear, scratches, or damage. Address any issues promptly to prevent further deterioration. This proactive approach ensures that the anodized brass remains in top-notch condition. Additionally, routine maintenance can significantly extend the lifespan and aesthetics of the material.
8. 3 Factors to Consider When Choosing Anodized Brass
Following the discussion on maintenance tips and care for anodized brass, the focus now shifts to the crucial factors in selecting anodized brass for projects. Here are the key considerations to ensure the right type of anodized brass is chosen:
#1 Purpose and Application
Start by clearly defining the intended purpose and usage of the anodized brass component. Take into account whether it will be utilized indoors or outdoors, in environments prone to corrosion, or areas with heavy foot traffic. This initial assessment, drawn from my practical experience, serves as a crucial step in narrowing down the most appropriate type of anodized brass for the specific requirements.
#2 Alloy Composition
The composition of the brass alloy is a crucial factor in determining its performance. Various alloys offer different levels of corrosion resistance, strength, and color choices.Selecting an alloy that matches the project’s requirements and meets the desired specifications is crucial. The right alloy can enhance the anodising process, ensuring a more consistent and durable finish.
#3 Supplier Reputation
Research the reputation of the supplier or manufacturer providing the anodized brass. Check for reviews, testimonials, and their track record in delivering quality products. Investigating their certifications and compliance with industry regulations can also provide valuable insights. A reliable supplier plays a crucial role in project success, ensuring the provision of materials that meet industry standards.
Conclusion
This comprehensive guide has shed light on the fascinating world of anodized brass, offering valuable insights to metal fabrication businesses, wholesalers, distributors, and small business owners. We’ve covered anodization, benefits, properties, and applications, empowering your project decisions.
At Zemetal, our expert team is dedicated to providing top-notch anodized brass solutions that meet your specific needs. Contact us today to explore how we can assist you in achieving exceptional results.
Dive Deeper Into Our Resources
Looking for more diverse service options? Browse through our handpicked selections:
For some insightful reads, we’ve curated a list of recommended articles just for you:
Still haven’t found what you’re looking for? Don’t hesitate to contact us. We’re available around the clock to assist you.