Have you considered the transformative impact of anodized aluminum in your production processes? Anodized aluminum stands out as a superior material choice, offering unmatched durability and aesthetic appeal in various industrial applications.
With our extensive knowledge and experience in the field, we provide insights that are crucial for businesses seeking to utilize anodized aluminum’s unique properties.
Anodized aluminum showcases cutting-edge material innovation, combining exceptional strength with versatile aesthetics. Its rising recognition in various sectors highlights its ability to adapt and excel under diverse demands.
In this guide, we will cover the essential aspects of anodized aluminum, from its basic definition to the advanced applications in various industries, providing a thorough understanding of its benefits and uses.
Read on for insightful revelations.
1. Defining Anodized Aluminum
Anodized aluminum is a uniquely enhanced form of aluminum, achieved through an electrochemical process, which improves its natural oxide layer. This process results in a durable, corrosion-resistant finish that is essential to the aluminum itself, differentiating it from surface-level coatings like paint. The anodized layer is much harder than the base aluminum, lending superior resilience to the material.
This treatment not only boosts the metal’s durability but also its aesthetic versatility. The anodized surface can be colored through various dyeing methods, offering a wide range of decorative options and electrical insulation, ideal for non-conductive applications. As per Verified Market Research, anodized aluminum market will grow at 5.02% CAGR from 2022 to 2030, driven by demand for attractive, durable products.
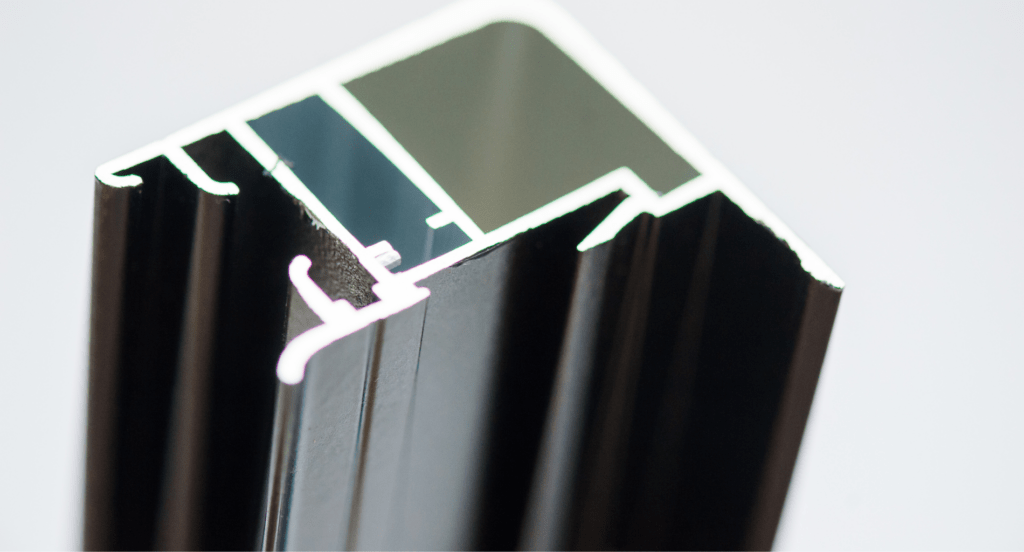
2. Advantages of Anodized Aluminum
After defining anodized aluminum, understanding its advantages is key to appreciating its widespread use in various applications. Here are the key benefits that make it a superior choice in many scenarios:
- Durability: Anodized aluminum is renowned for its remarkable durability. The electrochemical process used in anodizing hardens the surface, significantly increasing its resistance to wear and tear. This makes it an ideal choice for applications where a long-lasting material is essential.
- Corrosion Resistance: The enhanced corrosion resistance of anodized aluminum is one of its most valued qualities. The anodized layer acts as a strong barrier against rust and environmental degradation, ensuring longevity even in harsh conditions. This property is particularly beneficial for outdoor or marine applications.
- Electrical Insulation: Anodized aluminum provides excellent electrical insulation due to its non-conductive oxide layer. This characteristic is crucial in electrical and electronic applications, where preventing electrical conduction is necessary for safety and functionality.
- Ease of Maintenance: The ease of maintenance associated with anodized aluminum is a practical benefit. Its surface doesn’t require extensive care, retaining its appearance and physical properties with minimal cleaning, which is an attractive feature for both industrial and consumer applications.
3. Types of Anodized Aluminum
Transitioning from the advantages of anodized aluminum, the shift focuses on its type, each tailored for specific applications and aesthetic preferences. Here are the distinct types of anodized aluminum:
Type I – Chromic Acid Anodizing
Type I anodizing employs chromic acid to produce a slightly enhanced oxide layer while preserving the metal’s original texture. It’s ideal for applications needing minimal surface changes while providing excellent corrosion resistance, commonly used in aerospace and defense industries due to its non-conductive and damage-resistant properties.
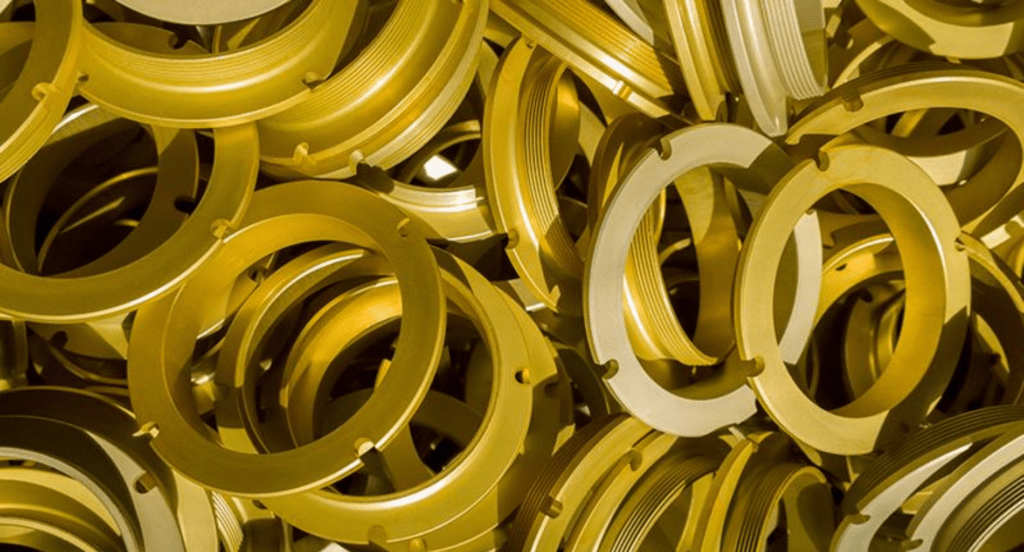
Type II – Sulfuric Acid Anodizing
Type II, involving sulfuric acid, creates a thicker oxide layer, making it suitable for a variety of color finishes. This type is favored for its balance of aesthetic versatility and enhanced durability, widely used in architectural, automotive, and consumer product industries. For instance, it’s commonly applied in the facade panels of modern buildings, offering both visual appeal and longevity.
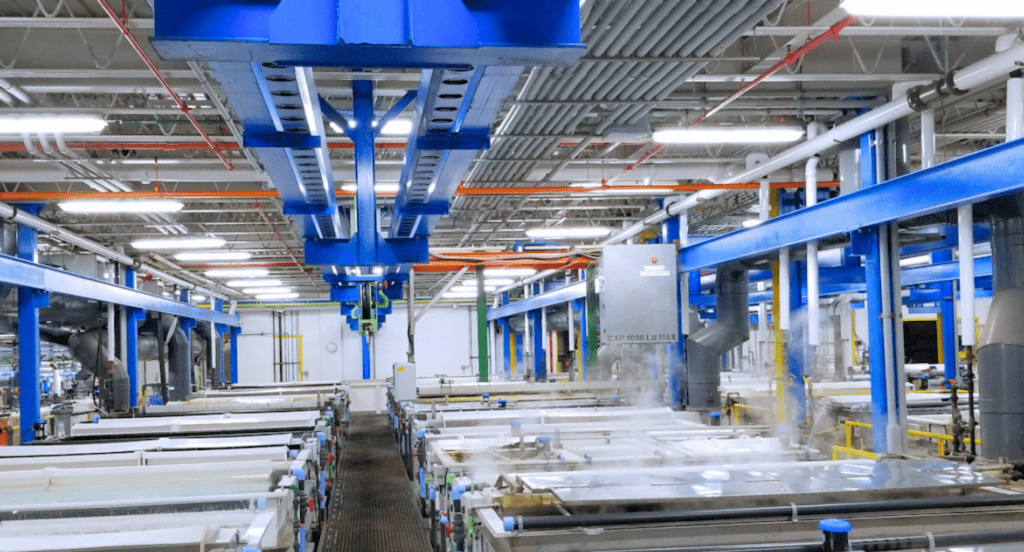
Type III – Hardcoat Anodizing
Type III, also known as hardcoat anodizing, forms a very thick and hard layer, significantly increasing wear and abrasion resistance. This type is particularly suited for industrial and engineering applications where extreme durability and resistance to harsh conditions are critical.
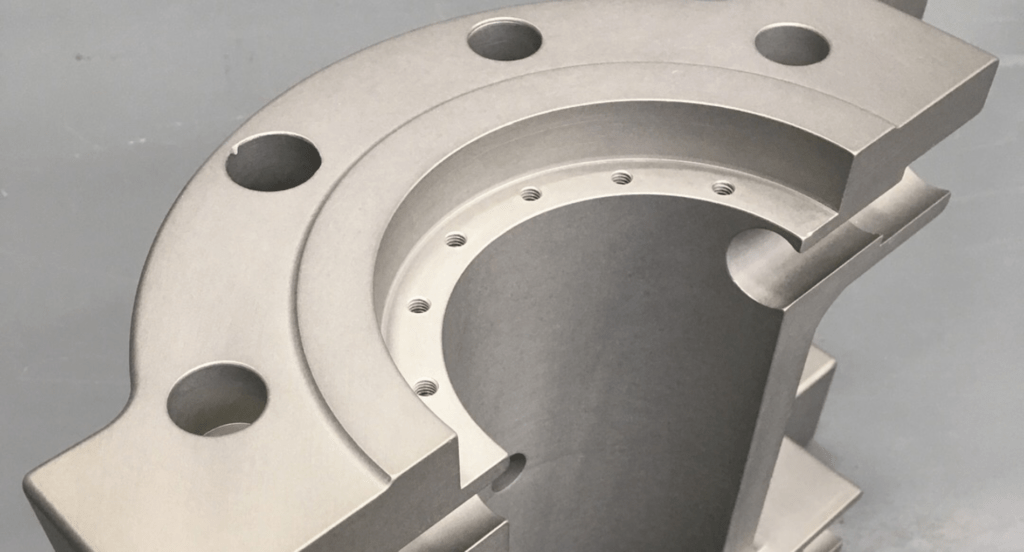
4. Physical Properties of Anodized Aluminum
Building on the types of anodized aluminum, it’s essential to understand its physical properties that define the material’s functionality and scope of application. Here are its key attributes:
Surface Hardness
The process of anodizing aluminum significantly enhances its surface hardness, a key factor in its widespread use. This treatment effectively transforms the outer layer of aluminum into a strong, scratch-resistant surface. This attribute is particularly beneficial in environments where resistance to abrasion and mechanical wear is crucial.
Thermal Conductivity
Despite the insulating properties of the oxide layer, anodized aluminum maintains excellent thermal conductivity. This characteristic ensures that it remains effective in applications where heat transfer is essential, such as in heat exchangers and cooling systems, without compromising the material’s protective qualities.
Non-Toxicity
Anodized aluminum is notable for its non-toxic nature, making it safe for a wide range of applications, including those in contact with food or used in medical devices. The anodization process does not involve the addition of any toxic materials, ensuring aluminum remains safe for both the environment and end-users.
Weight-to-Strength Ratio
The weight-to-strength ratio of anodized aluminum is a key advantage. While the anodization process adds significant strength and durability to the material, it does so without increasing its weight. This makes anodized aluminum an excellent choice for applications where light weight and high strength are priorities, such as in aerospace and automotive industries.
5. The Anodization Process
To enhance the remarkable physical properties of anodized aluminum, it’s crucial to explore the steps of the anodization process, each vital to achieving the material’s renowned characteristics. Here are the steps:
Step#1 Preparation of Aluminum
Begin by thoroughly cleaning the aluminum surface to eliminate any impurities, such as debris, oils, or contaminants. This cleaning typically involves a chemical bath to cleanse and etch aluminum. After cleaning, thoroughly rinse and dry the aluminum to ready it for anodization.
Step#2 Anodizing Bath
The cleaned aluminum is then placed in an electrolytic solution, commonly containing sulfuric acid. An electrical current is passed through the solution, initiating an electrochemical reaction that forms an oxide layer on the aluminum surface. This oxide layer grows directly from aluminum, covering the entire surface evenly.
Step#3 Coloring (if applicable)
For adding color, the open oxide layer is subjected to a dyeing process. The aluminum is dipped in a colored bath, allowing the dye to seep into the tiny openings in the oxide layer. Alternatively, electrolytic coloring involves using metal salts to add color to the pores of the oxide layer.
Step#4 Sealing the Anodized Aluminum
In the final step, the anodized aluminum is sealed to close the pores in the oxide layer. This is done by placing the aluminum in hot purified water or steam, which causes the pores of the oxide layer to expand and then close. The sealing process solidifies the oxide layer, completing the anodization process. This guarantees the longevity and effectiveness of the anodizing treatment, sealing the deal for this remarkable material.
6. Anodized vs. Non-Anodized Aluminum
Moving from the physical properties of anodized aluminum, it’s time to explore how it compares to non-anodized aluminum to better grasp their distinct characteristics and applications. Here are their key differences:
Durability
- Anodized: Anodized aluminum is significantly durable due to its hard oxide layer, making it resistant to wear and tear. This increased strength means it can withstand harsher conditions and longer usage periods. The anodization prevents aluminum from chipping or peeling, adding to its longevity.
- Non-Anodized: Non-anodized aluminum, while naturally durable, lacks the hardened surface provided by anodization. It is more prone to scratches, dents, and corrosion over time. This makes it less ideal for high-wear applications or environments with harsh weather conditions.
Suitability for Customization
- Anodized: Anodized aluminum offers versatile customization with a wide color range and texture options. It’s perfect for design-focused projects, with long-lasting customizations, making it valuable for creative and architectural applications.
- Non-Anodized: Non-anodized aluminum is limited in terms of customization options. Its natural metallic appearance, though initially attractive, does not offer the same creative flexibility. It is more suited for applications where the functional qualities of aluminum are prioritized over aesthetic customization.
Cost Implications
- Anodized: Anodizing aluminum may raise initial cost, but it pays off with extended lifespan and less maintenance. This long-term durability and reduced replacement requirement make it a cost-effective option.
- Non-Anodized: Non-anodized aluminum is cheaper initially compared to its anodized counterpart. However, it may lead to higher long-term costs due to wear and environmental damage. It suits budget-conscious applications with lower demands.
Environmental Impact
- Anodized: Anodized aluminum is environmentally friendly due to its durability and recyclability. Its longer lifespan means less frequent replacement and reduced waste. The anodization process itself is also evolving to become more eco-conscious, reducing its environmental footprint.
- Non-Anodized: Non-anodized aluminum, though recyclable, has a shorter lifespan, increasing material turnover and environmental impact. Without a protective anodized layer, it may require energy-intensive maintenance or restoration, resulting in a higher overall environmental impact.
7. Maintenance and Care for Anodized Aluminum
Following the comparison of anodized versus non-anodized aluminum, it’s crucial to understand the maintenance and care required to preserve the superior qualities of anodized aluminum. Here are essential tips:
Cleaning and Care
Preserving the integrity of anodized aluminum calls for gentle cleaning methods. For example, a solution of lukewarm water and a mild, pH-neutral detergent, applied with a soft, non-abrasive cloth, is ideal for maintaining its surface. This method ensures that the anodized layer remains undamaged, preserving the flawless appearance of aluminum.
This table summarizes effective cleaning and care methods for maintaining the integrity of anodized aluminum, emphasizing gentle techniques to preserve its appearance.
Method | Description | Benefit |
Lukewarm Water and Mild Detergent | Safe for regular cleaning without damaging the surface | Preserves anodized layer and appearance |
Soft, Non-Abrasive Cloth | Prevents scratches and maintains finish | Ideal for maintaining surface integrity |
Regular Rinsing | Removes surface debris and prevents buildup | Ensures long-term cleanliness and luster |
Avoid Harsh Chemicals | Prevents corrosion and surface damage | Essential for preserving anodized quality |
Dry Thoroughly After Cleaning | Prevents water spots and retains sheen | Enhances the overall aesthetic appeal |
Repair and Restoration
If anodized aluminum gets damaged, it can often be re-anodized to restore its protective layer. This process involves cleaning the surface and reapplying the anodic coating, effectively rejuvenating the material’s appearance and durability. It’s a cost-effective way to extend the lifespan of the material without needing a complete replacement.
Avoiding Harsh Impacts
To safeguard anodized aluminum from damage, it’s important to avoid harsh impacts and abrasive cleaners during both use and cleaning. Protective measures, such as the use of soft pads or bumpers in high-contact areas, can help preserve the anodized surface from scratches and dents. Zemetal also offers specialized care advice for maintaining anodized aluminum, ensuring its longevity and aesthetic appeal.
Minimizing UV Impact
Though anodized aluminum is resistant to UV rays, excessive and prolonged exposure to sunlight can lead to slight changes in its appearance. Using protective coverings or UV-resistant coatings can help maintain the color and finish of anodized aluminum in outdoor or sun-exposed settings.
8. Future Trends and Innovations in Anodizing Technology
Following the maintenance and care of anodized aluminum, we now turn to the future, where technological advancements are set to transform anodizing methods. Here are some essential developments:
Nanotechnology in Anodizing
Nanotechnology is poised to transform anodizing processes. By manipulating materials at the molecular level, researchers are working to enhance the strength and durability of anodized surfaces. This innovation could lead to the development of ultra-thin, yet incredibly resilient anodized layers, opening up new applications in high-precision industries.
Automated Anodizing Systems
Automation in anodizing is expected to increase efficiency and consistency in the anodizing process. Advanced automated systems, equipped with precise control mechanisms enhance uniform finishes, simplifying production and reducing errors for higher-quality anodized products. At Zemetal, we recognize the potential of these advancements and continuously integrate them into our processes to provide superior results.
Environmentally Sustainable Anodizing Methods
Sustainability continues to be a driving force in anodizing technology development. Researchers are working on anodizing methods that use renewable energy sources and environmentally friendly chemicals. Such sustainable practices not only reduce the ecological footprint of anodizing but also cater to the growing market demand for green manufacturing processes.
Conclusion
Anodized aluminum, with its exceptional durability and versatile design options, plays a vital role in advancing the quality and longevity of products in various industries. This guide offers valuable insights, empowering businesses to make informed decisions about utilizing this versatile material in your operations.
If you are looking for advanced solutions in anodized aluminum, Zemetal provides expert assistance and customized options. Reach out to us for guidance that can transform your projects.
Dive Deeper Into Our Resources
Looking for more diverse service options? Browse through our handpicked selections:
For some insightful reads, we’ve curated a list of recommended articles just for you:
Still haven’t found what you’re looking for? Don’t hesitate to contact us. We’re available around the clock to assist you.