Is your operation maximizing the potential of laser cutting and bending technologies? These techniques are crucial in transforming the precision and efficiency of metal fabrication.
Our expertise in the field ensures you receive reliable, up-to-date information, empowering you with the knowledge needed to utilize laser cutting and bending to the fullest capabilities.
Laser cutting and bending are at the forefront of creating precise and complex designs. These techniques offer unmatched accuracy and flexibility, essential in modern manufacturing.
In this guide, we’ll explore the critical aspects of laser cutting and bending, providing insights on how they can significantly enhance the metal fabrication process.
Read on to uncover these transformative techniques.
1. Overview of Laser Cutting and Bending Processes
Laser cutting and bending are essential technologies in modern metal fabrication, known for their precision and efficiency. In laser cutting, focused laser beams are used to cut through various metals, creating detailed and complex shapes with high accuracy. This technique is favored for its ability to produce detailed designs and maintain material integrity.
Bending, on the other hand, involves the manipulation of metal sheets into specific shapes and angles. This process utilizes specialized machinery to achieve precise bends, ensuring consistency and uniformity in production. Together, laser cutting and bending provide a comprehensive solution for creating complex metal components with exact specifications.

2. Advantages of Laser Cutting and Bending
Building on the understanding of the processes, it’s crucial to dive into the key benefits that laser cutting and bending bring that transform production efficiencies and design possibilities. Here are their key advantages:
- Enhanced Fabrication Flexibility: Laser cutting combined with bending provides unmatched flexibility in metal fabrication, allowing for complex shapes and precise cutouts. This combination creates complex three-dimensional structures, ideal for aesthetically pleasing and strong designs in the industry.
- Streamlined Production Workflow: Integrating laser cutting and bending in one production line optimizes manufacturing, reducing machine use and handling steps. This boosts workflow efficiency and reduces turnaround times by minimizing transition between production stages.
- Improved Structural Integrity: Laser cutting paired with bending enhances structural integrity. Precise laser cuts ensures clean edges, enhancing bending predictability for stronger, reliable metal components. This is vital in industries like construction and automotive manufacturing where durability matters.
- Cost-Effective Production: Laser cutting and bending can save costs compared to traditional methods by reducing material waste, eliminating extra joining steps and labor expenses, making it attractive to businesses looking to optimize budgets.
3. Materials Suitable for Laser Cutting and Bending
Following the notable advantages of laser cutting and bending, it’s essential to understand the materials that best complement these processes. Here are some of the most compatible materials:
Stainless Steel
Stainless steel is a standout choice for laser cutting and bending due to its strength and corrosion resistance. These qualities make it an ideal candidate for creating durable and precise parts in laser cutting and bending processes, particularly in high-stress environments like construction and automotive industries. Its versatility in fabrication makes it a go-to material for a variety of applications.

Aluminum
Aluminum’s combination of lightness and strength plays exceptionally well with the precision of laser cutting and the flexibility of bending processes. This material is easily shaped and maintains its structural integrity, making it a popular choice in industries that value weight efficiency, such as aerospace and consumer electronics. Its adaptability in laser cutting and bending processes is a key factor in its widespread use.
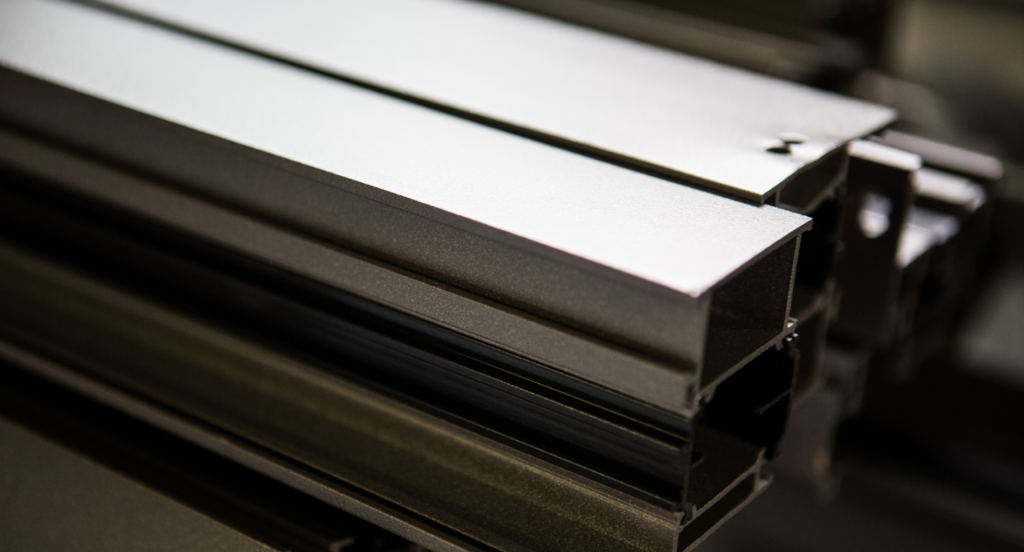
Brass and Copper
Brass and copper are highly malleable, making them excellent for detailed laser cutting and complex bending. These materials are known for their thermal and electrical conductivity, making them ideal for electrical components and decorative applications. Their unique color and finish options also add aesthetic value to the final product.
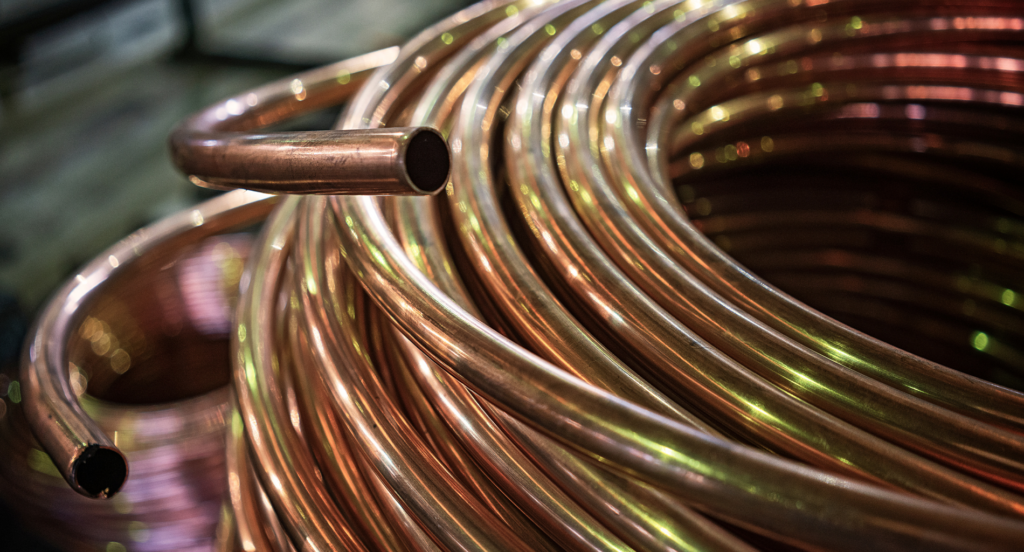
High-Strength Alloys
High-strength alloys are tailored to endure the challenges of laser cutting and bending, making them essential in sectors that demand resilience, such as defense and heavy machinery. These materials maintain their structural integrity under high stress and are capable of being precisely shaped and bent, meeting the strict requirements of critical applications where failure is not an option.
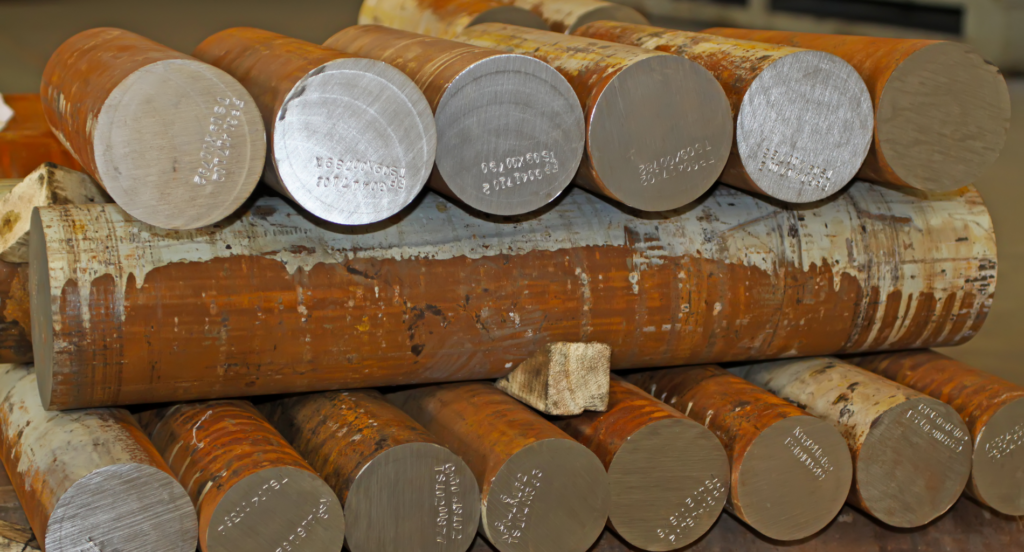
Specialty Metals
Specialty metals like titanium are particularly suitable for laser cutting and bending due to their extraordinary strength-to-weight ratio and corrosion resistance. Ideal for precision-driven sectors such as aerospace and medical device manufacturing, where accuracy and durability are crucial. Their compatibility with laser cutting and bending techniques enables the creation of high-performance, complex components.
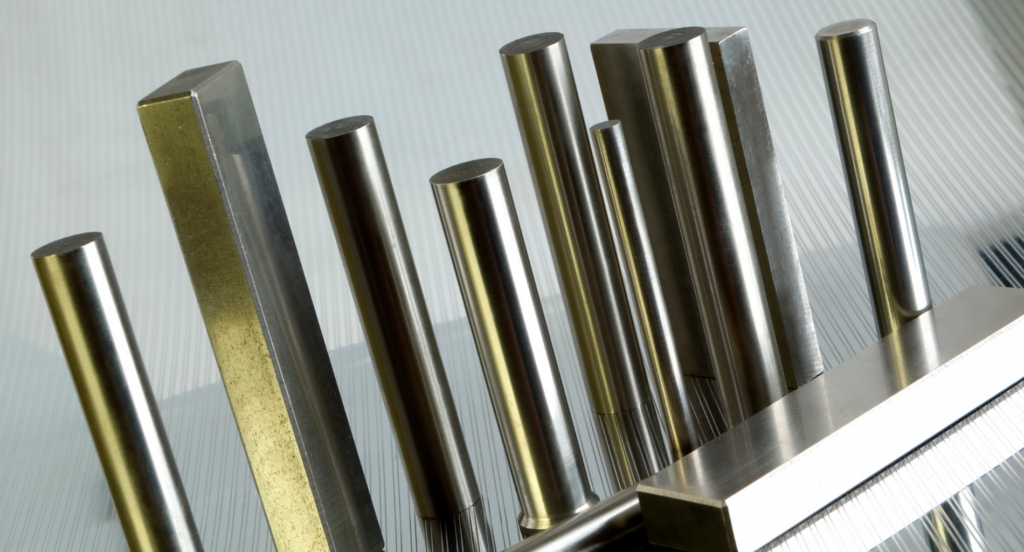
4. Applications of Laser Cutting and Bending in Industry
After determining suitable materials for laser cutting and bending, exploring their practical applications reveals their vital role in various industries. Here are key sectors where these technologies have significant impact:
Automotive Manufacturing
In automotive manufacturing, laser cutting and bending are used to create critical vehicle components like chassis, body parts, and complex engine components. These techniques ensure high precision and consistency, which are vital for maintaining the safety and performance standards of vehicles. They are also instrumental in producing lightweight and aerodynamic designs that enhance fuel efficiency.
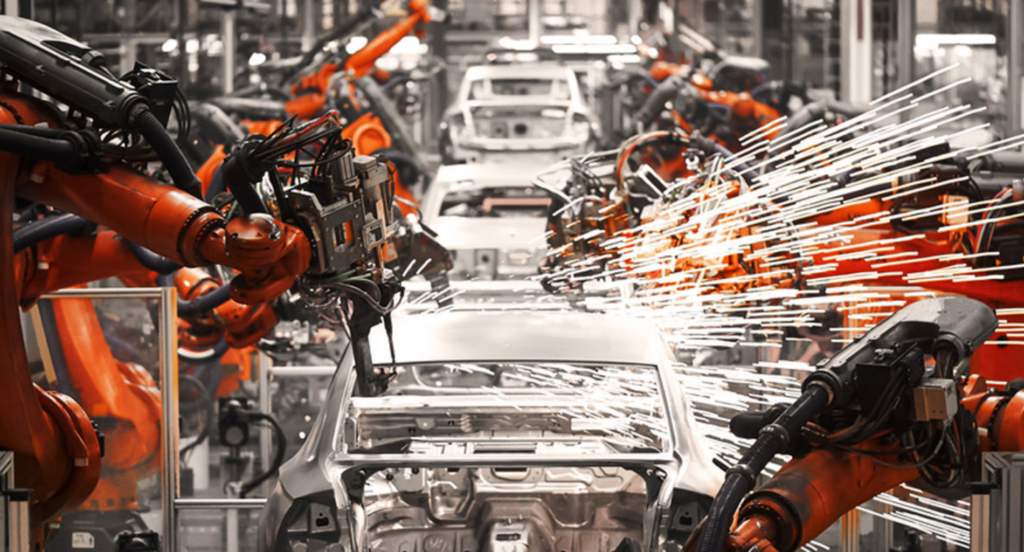
Aerospace Industry
Within the aerospace industry, laser cutting and bending are employed for creating components of aircraft and spacecraft, such as airframe structures, engine parts, and interior cabin panels. This application is crucial for ensuring the structural integrity and weight optimization of aircraft, directly impacting performance and safety. The precision of these methods is key to meeting the strict compliance and quality standards of this sector.
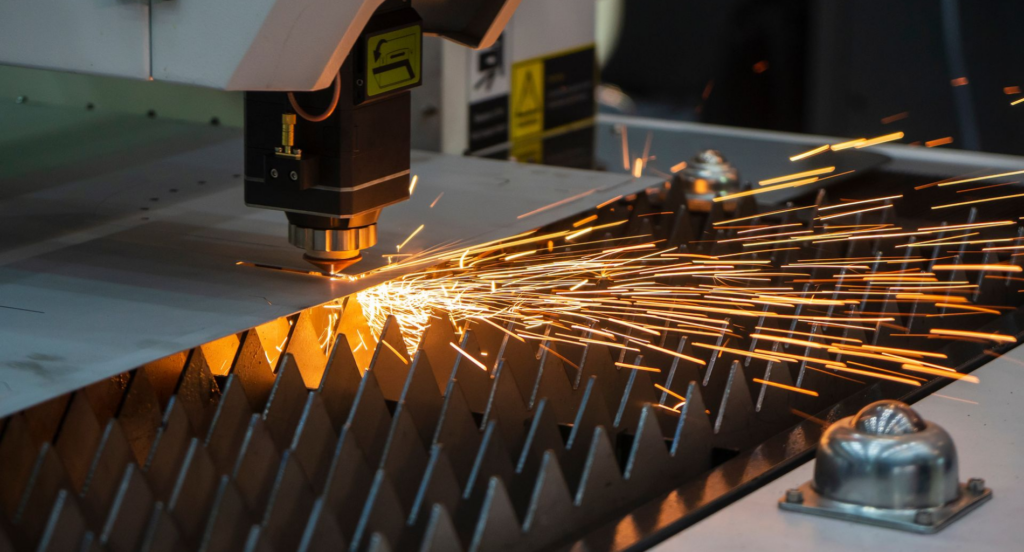
Architectural Metalwork
The architectural industry benefits greatly from the versatility of laser cutting and bending. These techniques allow for the creation of unique, custom-designed metal elements that are both structurally sound and aesthetically pleasing. For example, they are used in the creation of decorative elements, structural supports, and custom-fit panels for buildings, offering architects more creative freedom.
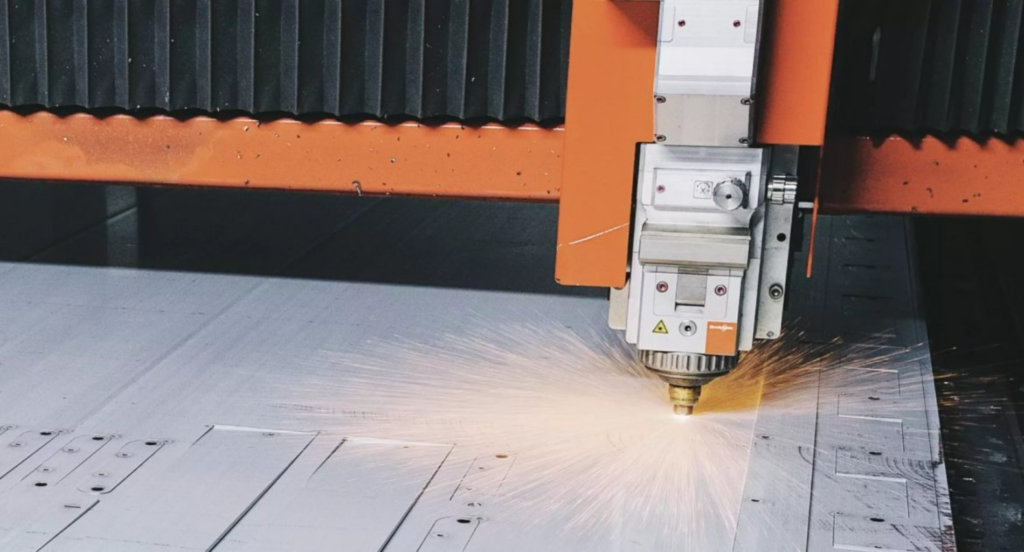
Medical Equipment Manufacturing
Precision is crucial in medical equipment manufacturing, and laser cutting and bending deliver just that. They are employed to produce surgical instruments, implants, and medical devices. The accuracy of these methods ensures that equipment meets the strict standards required in healthcare. They also enable the creation of customized medical tools tailored to specific surgical needs.
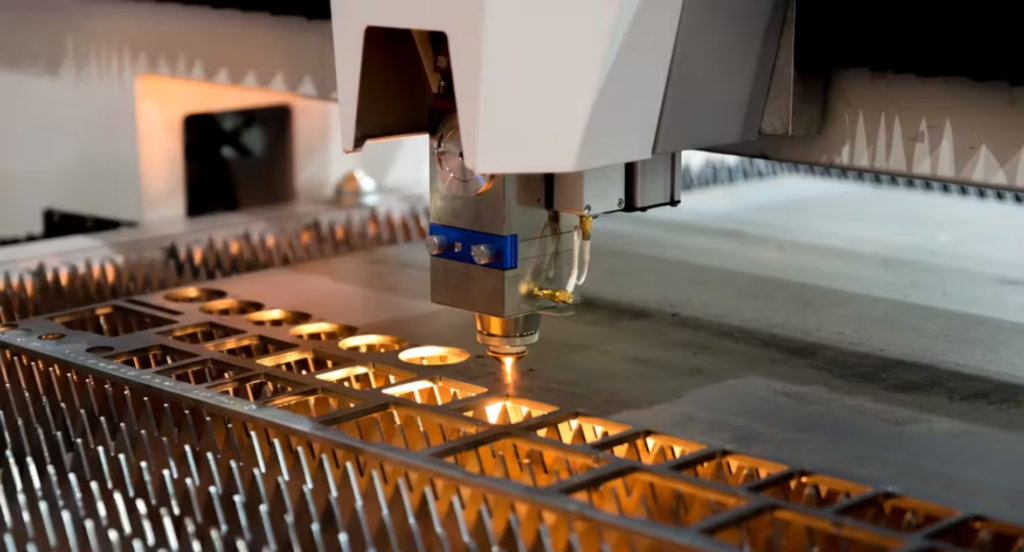
5. Safety Protocols in Laser Cutting and Bending
Laser cutting and bending processes in different industries require strict safety measures to ensure the well-being of operators and the smooth operation of machinery. Here are the vital safety protocols in detail:
Personal Protective Equipment (PPE)
In laser cutting and bending operations, wearing PPE is vital for operator safety and confidence in handling machinery. This includes safety goggles, gloves, and fire-resistant clothing to protect against laser radiation, sparks, and debris. Grand View Research reports that the global PPE market is expected to grow at a 6.7% CAGR from 2023 to 2030, driven by increasing workplace safety awareness.
Machine Maintenance and Calibration
Regular maintenance and precise calibration of laser cutting and bending machines are crucial for safety and performance. Ensuring that machines are in top condition minimizes the risk of malfunctions, which can lead to accidents. Scheduled checks and maintenance also prolong the life of the equipment, ensuring consistent quality in metal fabrication.
Ventilation and Air Quality Control
Proper ventilation systems are essential in facilities where laser cutting and bending are performed. These systems prevent the accumulation of harmful fumes and particles, maintaining a safe working environment. Regular monitoring of air quality is also necessary to protect workers from potential health hazards. Zemetal places a high emphasis on safety, ensuring facilities follow the best air quality management practices.
Emergency Response Plans
Having well-structured emergency response plans in place is crucial for handling unforeseen incidents during laser cutting and bending operations. For example, these plans should include procedures for immediate machine shutdown, medical aid, and evacuation. Regular drills and clear communication channels ensure that all staff are prepared to respond effectively in case of an emergency.
6. Challenges and Solutions in Laser Cutting and Bending
Transitioning from safety protocols, it’s important to recognize the obstacles and strategic solutions to these processes to enhance efficiency and effectiveness. Here are some of the challenges together with its solution:
Technological Upgrades
Keeping pace with rapid technological advancements is a significant challenge in the laser cutting and bending industry. The solution lies in regularly upgrading equipment and embracing the latest software to improve precision and efficiency. This approach not only enhances production capabilities but also ensures competitiveness in a fast-evolving market.
Managing Thermal Effects
The thermal effects of laser cutting, such as warping or material deformation, present a unique challenge. Implementing controlled cooling systems and using materials with higher thermal resistance can effectively reduce these effects. Additionally, optimizing the laser parameters, like power and cutting speed, can reduce the thermal impact on materials.
Environmental Considerations
The environmental impact of these processes, particularly in terms of energy consumption and waste production, poses a significant challenge. Adopting eco-friendly practices, such as using renewable energy sources and recycling waste materials, offers a practical solution. Such sustainable practices reduce the environmental footprint and cater to the growing market demand for environmentally responsible solutions.
Skilled Workforce Development
A major challenge in this field is the shortage of skilled professionals well-versed in the latest laser cutting and bending technologies. Addressing this requires a commitment to training and developing a skilled workforce, through comprehensive educational programs and on-the-job training. By nurturing talent and expertise, companies can ensure high operational standards and promote innovation in their processes.
This table focuses on the strategies and benefits of developing a skilled workforce in the field of laser cutting and bending technologies, addressing the current skills shortage.
Strategy | Description | Impact on Industry |
Comprehensive Educational Programs | Courses and workshops on latest technologies | Enhances knowledge base of professionals |
On-the-Job Training | Practical, hands-on experience in real-world scenarios | Improves technical skills and adaptability |
Talent Nurturing | Identifying and developing potential within employees | Fosters innovation and expertise growth |
Industry-Academia Collaboration | Partnerships with educational institutions | Creates a pipeline of skilled entrants |
Continuous Learning and Development | Ongoing training to keep up with evolving technologies | Ensures workforce stays competent and updated |
7. Future Trends in Laser Cutting and Bending Technology
After addressing the challenges of laser cutting and bending, exploring emerging trends in these processes that pave the way for future innovations is vital. Here are the key trends that will reshape these techniques:
Advanced Optical Technology
The advancement in optical technologies is a key trend in laser cutting and bending. Enhanced precision in laser optics allows for more detailed cuts and bends, pushing the boundaries of what can be achieved in metal fabrication. This improvement in precision not only increases the quality of the end product but also expands the potential for more complex and detailed designs.
Increased Use of Fiber Lasers
Fiber lasers are becoming increasingly popular in laser cutting and bending operations. They offer greater efficiency, higher cutting speeds, and lower maintenance costs compared to traditional lasers. This shift towards fiber lasers highlights the industry’s focus on enhancing productivity and operational cost-effectiveness.
Integration of 3D Printing Technologies
The integration of 3D printing with laser cutting and bending is a trend gaining momentum. This combination allows for the creation of more complex and customized metal components, offering unmatched flexibility in design and prototyping. It opens up new possibilities in terms of both design innovation and rapid production.
Expansion of Robotics and Automated Systems
Robotics and automated systems are playing an increasingly significant role in laser cutting and bending processes. The use of robots for handling and positioning materials enhances precision and consistency, while automation simplifies the production process, improving efficiency and reducing labor costs. Zemetal, at the forefront of these advancements, integrates these technologies to provide high-quality and efficient services.
Conclusion
Navigating through laser cutting and bending opens up a landscape of precision and innovation, crucial for the advancement of various industrial processes. This guide has provided essential insights, aiding businesses in optimizing operational techniques for enhanced productivity and design flexibility.
For those seeking advanced solutions in laser cutting and bending, Zemetal is your go-to resource. Contact us to explore how our expertise can elevate your fabrication projects.
Dive Deeper Into Our Resources
For some insightful reads, we’ve curated a list of recommended articles just for you:
Still haven’t found what you’re looking for? Don’t hesitate to contact us. We’re available around the clock to assist you.