Ever wondered how powder coating and laser engraving stack up in the world of industrial finishing? These two techniques in metal fabrication offer distinct advantages and challenges in the industry.
With years of experience in industrial finishing, our insights offer a deep dive into these two popular methods. Trust us to guide you through the complex world of industrial finishes.
Powder coating provides a durable, aesthetic finish to metal surfaces, while laser engraving offers precision in creating complex designs and markings.
In this ultimate guide, we’ll explore the variations, applications, and technicalities of both powder coating and laser engraving. Discover which method suits your project’s needs best.
Read on to go through the details of these two powerful finishing techniques.
1. Understanding Powder Coating and Laser Engraving
Powder coating is a finishing process where a dry, powdered paint is electrostatically applied to a metal surface and then cured under heat to form a tough, skin-like layer. This method is renowned for its durability, environmental safety, and wide range of aesthetic options. Powder coatings can resist wear, corrosion, and fading, making them ideal for a variety of applications, from industrial machinery to consumer products.
Laser engraving, on the other hand, involves using a high-powered laser to etch or mark a surface. It’s a non-contact process, offering high precision and control. This technique is used for detailed work, such as creating complex designs, serial numbers, or logos on different materials, including metals, plastics, and glass. Laser engraving stands out for its accuracy, speed, and flexibility, allowing for customization even in small production.
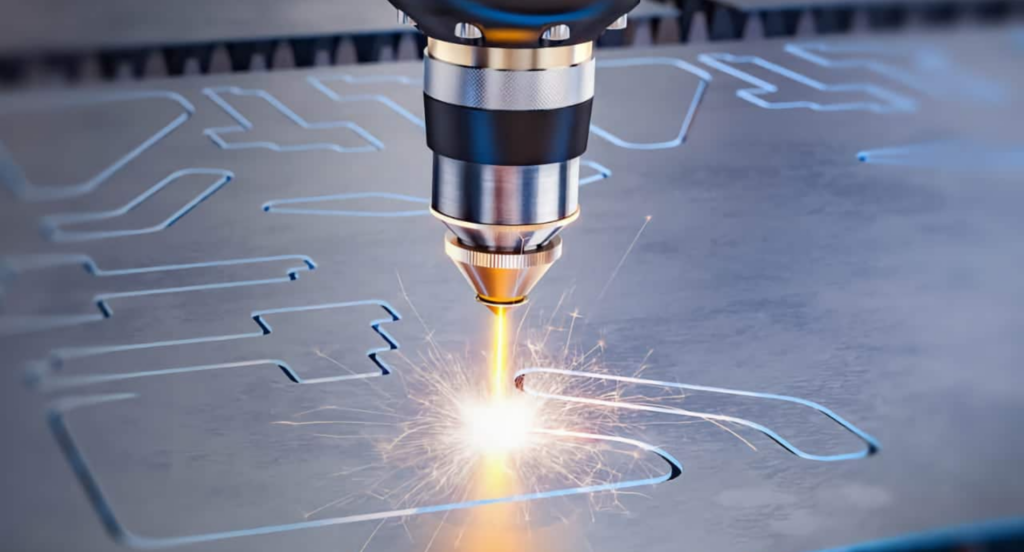
2. The Basics of Powder Coating
While we’ve touched on the essence of powder coating, going into its fundamentals reveals why it’s a preferred choice for many industries. This method creates an even, durable coating. After application, the coated object is cured in an oven, where the powder melts into a smooth, hard finish. This finish not only provides an appealing aesthetic but also offers robust protection against rust, scratches, and fading.
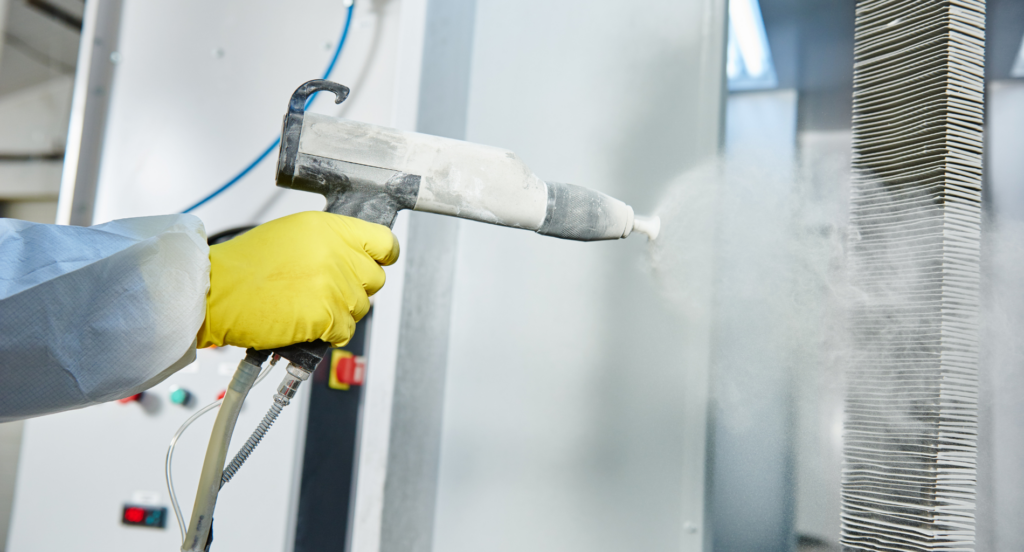
Components of Powder Coating
- Polymer Resin: The backbone of powder coating, polymer resin provides the necessary binding and forms the protective layer upon curing. It determines the texture, gloss, and durability of the finish.
- Pigments: These add color and aesthetic appeal to the coating. Pigments must be chosen carefully to ensure colorfastness and resistance to fading under various environmental conditions.
- Curing Agents: Essential for hardening the coating, curing agents react with the resin under heat, creating a tough, long-lasting surface.
- Specialty Additives: Some services incorporate advanced additives that enhance properties like UV resistance, gloss retention, and corrosion resistance, making their powder coatings ideal for challenging environments.
Pros:
- Durability: Forms a hard, abrasion-resistant layer, prolonging the life of the coated item.
- Eco-friendly: Contains no solvents, emitting unimportant volatile organic compounds, making it a greener choice.
- Uniform Finish: Ensures a smooth, consistent coating without drips or runs.
- Variety of Finishes: Offers a wide range of textures and colors for customization.
Cons:
- Limited Substrates: Mainly suitable for metal surfaces, restricting its application range.
- Color Matching Challenges: Precise color replication can be difficult, especially for specific shades.
- Curing Process: Requires a curing oven, adding to the energy cost and limiting the size of objects that can be coated.
- Thickness Limitations: This can result in a thicker layer than other finishes, which might not be desirable in some applications.
3. Delving into Laser Engraving
Transitioning from the tangible layers of powder coating, we now shift our focus to the precision-driven world of laser engraving. Laser engraving is an advanced process that uses a concentrated beam of light to etch or mark a material’s surface. This is a popular choice for industrial marking and decorations. The global laser engraving machines market size was valued at USD 1531.77 million in 2021, according to LinkedIn.
Components of Laser Engraving
- Laser Source: The heart of the engraving machine, the laser source generates the beam that etches the material. From my personal standpoint, its power and wavelength determine the types of materials it can engrave and the precision of the work.
- Controller System: This sophisticated software guides the laser’s path, speed, and frequency. From my previous experience, it’s responsible for the accuracy of designs and the consistency of the engraving depth.
- Cooling System: Essential for maintaining laser efficiency and longevity, the cooling system prevents overheating, ensuring consistent performance during prolonged operations.
- Customization Tools: Zemetal offers advanced customization options with its laser engraving services, including precise control over design details and adaptable settings for different material types, enhancing the engraving’s quality and detail.
Pros:
- High Precision: Allows for complex designs with extreme accuracy.
- Versatility: Suitable for various materials, including metals, plastics, and wood.
- Non-Contact Process: Reduces the risk of material damage and wear on the engraving tools.
- Speed: Efficient for both small and large-scale productions, saving time and costs.
Cons:
- Initial Cost: High upfront investment for quality laser engraving machinery.
- Material Limitations: Not all materials can be laser engraved, limiting their application scope.
- Power Consumption: High energy requirements for optimal operation.
- Training and Safety: Requires skilled operation and adherence to safety standards to avoid hazards like burns or harmful fumes.
4. Key Differences in Powder Coating and Laser Engraving
Having explored the individual characteristics of both powder coating and laser engraving, it’s essential to contrast them directly to understand their unique roles. Here are the key differences between these two techniques:
Aspect | Powder Coating | Laser Engraving |
Primary Function | Adds a protective and aesthetic layer to surfaces. | Etches designs, text, or markings onto surfaces. |
Material Compatibility | Primarily used on metal surfaces. | Can be used on metals, plastics, glass, and wood. |
Process | Electrostatic application of powder followed by heat curing. | Non-contact process using a laser beam to etch the surface. |
Finish | Creates a uniform, thick layer. | Does not add a layer; alters the surface itself. |
Durability | Offers high resistance to wear, corrosion, and fading. | Engraved designs are permanent but don’t protect the surface. |
Environmental Impact | Low VOC emissions, considered more eco-friendly. | Can produce fumes or debris, requiring proper ventilation. |
Customization | Limited to color and texture variations. | Allows for intricate and detailed designs. |
Setup and Operation | Requires a curing oven and spray equipment. | Needs laser engraving machinery and skilled operation. |
Application Speed | Relatively slower due to curing time. | Generally faster, depending on the complexity of the design. |
Cost Considerations | Lower operational costs, but can be material-intensive. | Higher initial equipment costs but lower material costs. |
5. 4 Tips for Making the Right Choice for Your Needs
Having explored the various aspects and considerations of powder coating and laser engraving, it’s clear that each method offers unique advantages for different scenarios. See the following essential tips below for making the right choice for your needs:
#1 Assessing Durability and Longevity Needs
When choosing between powder coating and laser engraving services, consider the durability and longevity required for your product. Powder coating is ideal for items exposed to harsh conditions. For example, outdoor furniture benefits greatly from powder coating due to its resistance to weather elements. In contrast, laser engraving is best for products where surface detail and precision are paramount.
#2 Production Scale and Efficiency
The scale and efficiency of your project can influence the choice between powder coating and laser engraving. Powder coating can be more time-consuming due to the curing process. Laser engraving, being faster, is more suited for both small and large-scale productions requiring quick completion. Zemetal offers efficient laser engraving services that can cater to high-volume demands without compromising on quality or detail.
#3 Budget and Cost Implications
Budget considerations are key in choosing between powder coating and laser engraving services. As an example, powder coating generally has lower operational costs but may require more material. In contrast, laser engraving involves higher initial equipment and setup costs. Analyze the long-term cost benefits of the specific requirements of your project to make a cost-effective decision.
#4 Compliance with Industry Standards
When choosing between powder coating and laser engraving services, it’s crucial to consider compliance with industry standards. Powder coating often aligns well with environmental and safety standards due to its low VOC emissions. Laser engraving, while producing some fumes, offers precision essential for industries that require detailed compliance markings like aerospace where traceability and compliance are non-negotiable.
Conclusion
To wrap up this journey, going through the complexities of powder coating and laser engraving becomes simpler with this guide, designed to lighten the path toward making the best choice for all specific needs. Empowered with this knowledge, you’re well-placed to optimize your project’s success.
For specialized assistance in powder coating and laser engraving, turn to Zemetal. Our team ensures all projects are handled with precision and care. To know how we can help your success, contact us today.
Dive Deeper Into Our Resources
For some insightful reads, we’ve curated a list of recommended articles just for you:
Still haven’t found what you’re looking for? Don’t hesitate to contact us. We’re available around the clock to assist you.