How do businesses achieve unmatched precision and efficiency in shaping stainless steel sheets? In the world of metal fabrication, laser cutting stands out as technology, transforming how to make stainless steel.
With years of experience in the field, I bring a deep understanding of laser cutting technology and its applications.
Laser cutting of stainless steel sheets sets a new standard in the metal fabrication industry by combining precision, speed, and versatility.
In this ultimate guide, you’ll discover the workings of laser cutting, its advantages, technical considerations, and how it transforms stainless steel sheet fabrication.
Read on to unlock the full potential of laser cutting.
1. Understanding Stainless Steel (SS) Sheets
Stainless steel sheets are a cornerstone in the metal fabrication industry, prized for their durability and resistance to corrosion. Formed from an alloy primarily composed of iron, chromium, and nickel, these sheets offer a balance of strength and aesthetic appeal. The inclusion of chromium, typically at least 10.5%, is crucial as it forms a passive layer of chromium oxide on the surface, protecting the material from rust, etc.
This unique characteristic makes stainless steel sheets an ideal choice for a wide range of applications, from architectural designs to automotive parts. Each stainless steel sheet possesses its grade and finish, determined by the specific alloy composition and the treatment applied to its surface. These variations cater to different requirements in terms of strength, malleability, and appearance.
For example, Grade 304 stainless steel has excellent corrosion resistance and is widely used in kitchen appliances. As per VMR, it was valued at USD 117.65 Billion in 2023. While Grade 316, with its higher resistance to chlorides, is more suitable for marine or chemical environments. Understanding these differences is important for businesses to select the appropriate grade for their specific application needs.
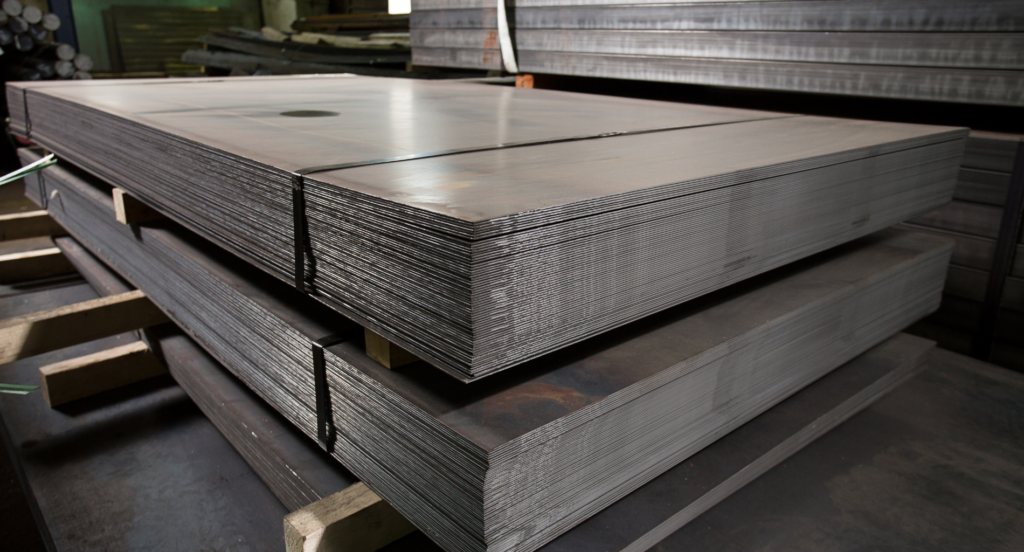
2. Benefits of Laser Cutting for SS Sheets
Transitioning from the fundamental understanding of stainless steel sheets, it’s essential to explore how laser cutting technology enhances their fabrication. Here are the key benefits of employing laser cutting for stainless steel sheets:
- Precision and Accuracy: Laser cutting allows for incredibly precise cuts, with a high level of accuracy that is difficult to match with other cutting methods. This precision is crucial for intricate designs and tight tolerances required in many industrial applications.
- Speed and Efficiency: Compared to traditional cutting methods, laser cutting is significantly faster, enabling quicker turnaround times for projects. This efficiency is essential in meeting tight deadlines and increasing productivity.
- Versatility in Design: Laser cutting provides the flexibility to create complex shapes and designs without the need for additional tooling. This versatility opens up a world of design possibilities for businesses.
- Minimal Material Waste: The precision of laser cutting results in minimal material waste, making it a more sustainable and cost-effective solution. Efficient use of materials is not only eco-friendly but also reduces overall project costs.
- Superior Edge Quality: Laser cutting leaves a high-quality finish on the edges of stainless steel sheets, reducing the need for additional finishing processes. This results in a cleaner, more polished final product.
- Reduced Labor Costs: Automated laser cutting reduces the need for manual labor, thereby decreasing labor costs. Zemetal’s advanced laser cutting services exemplify this benefit, providing efficient and cost-effective solutions for businesses.
3. Advanced Techniques and Innovations
Building on the benefits of laser cutting for stainless steel sheets, it’s crucial to delve into the advanced techniques and innovations that are shaping the industry. Here are the key areas of innovation:
Fiber Laser Technology
The adoption of fiber laser technology has transformed the cutting of stainless steel sheets. This advanced technology, with its solid-state laser source, offers superior beam quality compared to traditional carbon dioxide lasers. It’s particularly effective for cutting reflective metals like stainless steel, enabling faster processing speeds for thin to medium-thick SS sheets.
Automation in SS Sheet Fabrication
Automation plays an important role in the laser cutting of SS sheets. The integration of automated loading and unloading systems, along with robotics, has streamlined the production process. This technological leap minimizes human error and maximizes output, enhancing the overall efficiency of laser cutting SS sheets. Software advancements have also improved material utilization with optimized nesting algorithms.
Customization and Adaptive Cutting
Laser cutting SS sheets now embraces a higher level of customization thanks to adaptive cutting technologies. These include dynamic focus systems that adjust the cutting parameters for different thicknesses and contours of SS sheets. This flexibility is crucial for bespoke projects that demand intricate detailing and precision. Laser cutting is being increasingly integrated with other fabrication processes to produce complex SS sheet products.
This table summarizes the key features and benefits of adaptive cutting technologies in laser cutting SS (stainless steel) sheets, emphasizing the enhanced customization and precision they offer for intricate and complex projects.
Feature | Description | Benefit for Customization |
Dynamic Focus Systems | Adjusts laser for varying thicknesses and contours | Enables precise cuts on diverse shapes |
Customized Cutting Parameters | Tailored settings for specific project requirements | Achieves intricate detailing with accuracy |
Integration with Fabrication Processes | Combines with other techniques for complex structures | Facilitates production of sophisticated designs |
High Precision and Accuracy | Ensures exact cuts and minimal material wastage | Essential for detailed and bespoke projects |
Versatility in Design | Adapts to a wide range of designs and specifications | Supports creative and unique SS sheet products |
4. Applications of Laser-Cut SS Sheets in Various Industries
The advancements in laser cutting SS sheet technology not only redefine the fabrication process but also expand its applications across various industries. Below are the key industries benefiting from it:
Automotive Industry
In the automotive sector, the use of laser-cut SS sheets is pivotal. The technology’s precision is critical in producing parts with tight tolerances and complex shapes, essential for vehicle performance and safety. Components like exhaust systems, engine parts, and decorative trims are often crafted from laser-cut stainless steel, ensuring durability and corrosion resistance.
Architecture and Construction
Laser-cut SS sheets are also extensively used in architecture and construction. Their application ranges from structural elements to intricate decorative panels. Stainless steel’s aesthetic appeal and resistance to environmental factors make it a popular choice for façades, balustrades, and artwork installations. Zemetal services provide tailored solutions that align with the architectural vision.
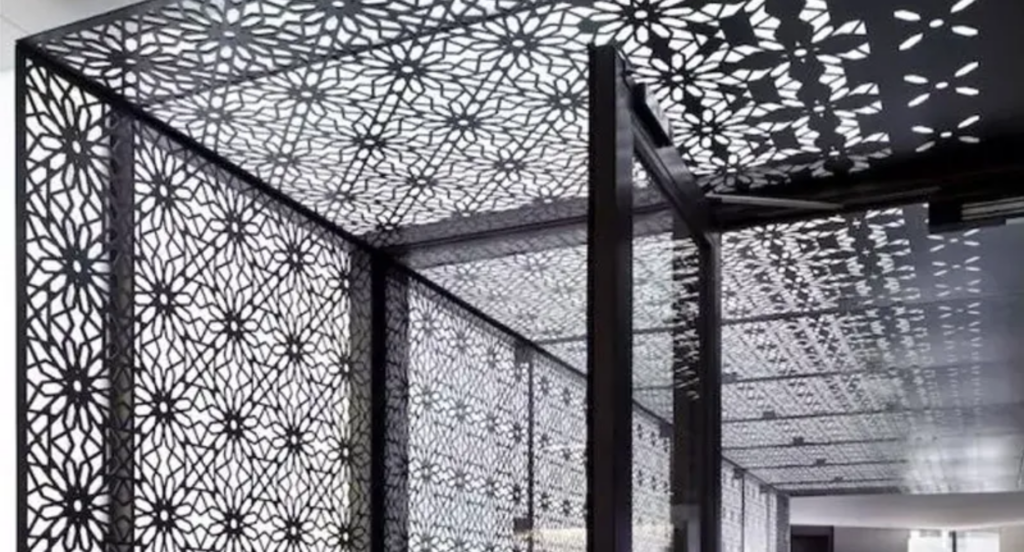
Medical Equipment Manufacturing
The medical industry greatly benefits from the precision of laser-cut SS sheets. Stainless steel’s hygienic properties and resistance to sterilization processes make it ideal for medical devices and surgical tools. Laser cutting enables the production of intricate components with high precision, essential in medical applications where even a fraction of a millimeter can make a significant difference.
5. Safety and Environmental Aspects of Laser Cutting
As we delve into the practical applications of laser-cut SS sheets across industries, it’s equally important to consider the safety and environmental aspects of this technology. Here are some keys to keep in mind:
Worker Safety in Laser Cutting Operations
Worker safety is paramount in any industrial operation, and laser cutting is no exception. The process involves high-powered lasers that can pose significant risks if proper safety measures are not in place. Personal protective equipment (PPE) like safety goggles and fire-resistant clothing is essential to protect operators from laser radiation and potential burns.
Environmental Impact and Waste Management
Laser cutting, while efficient, does have environmental implications primarily related to energy consumption and waste generation. However, advancements in laser technology have led to more energy-efficient machines, reducing the carbon footprint of operations. Waste management is another critical aspect. The process can produce metal scraps and fumes, which need to be properly handled and disposed of.
Compliance with Regulations and Standards
Adhering to industry regulations and standards is essential for any business involved in laser cutting SS sheets. This includes compliance with local and international safety standards, environmental regulations, and occupational health guidelines. Regular audits and inspections ensure that operations remain compliant and up-to-date with the latest regulations.
6. Challenges and Solutions in Laser Cutting SS Sheets
Acknowledging the safety and environmental aspects of laser cutting SS sheets sets the stage to address the challenges faced in this field. Listed are the most common challenges and their corresponding solutions:
Material Reflectivity and Heat Management
Challenge: Stainless steel’s reflective nature can pose a challenge for laser cutting, as the laser beam might reflect off the surface, leading to inefficiencies and potential damage to the equipment. Additionally, managing the heat generated during the cutting process is crucial to prevent warping or deformation of the SS sheet.
Solution: Using fiber lasers, which are more effective in cutting reflective materials like stainless steel, is a key solution. These lasers have a wavelength that is better absorbed by the metal, reducing reflectivity issues. Implementing proper heat management techniques, such as controlling the laser’s power output and using assist gases like nitrogen, can help dissipate heat more effectively and prevent material warping.
Maintaining Precision
Challenge: Achieving consistent precision across different thicknesses of SS sheets can be challenging. Thicker sheets require more laser power and slower cutting speeds, which can affect the cut quality and dimensional accuracy.
Solution: Advanced laser cutting machines equipped with adaptive optics and real-time feedback systems can automatically adjust the focus and power of the laser beam based on the thickness of the material. In my experience, investing in such adaptive technology has been a game-changer, allowing for consistent precision across a range of material thicknesses without sacrificing speed or quality.
Cost-Effectiveness and Efficiency
Challenge: Balancing the cost-effectiveness and efficiency of laser cutting operations, especially for large-scale or complex projects, can be a significant challenge. The initial investment in laser cutting equipment is high, and operational costs, including power consumption and maintenance, need to be managed effectively.
Solution: To address this, optimizing the cutting process through advanced software for nesting and path planning is essential. Efficient nesting reduces material waste, and optimized cutting paths shorten processing time, thus saving on operational costs. Regular maintenance and staying updated with technological advancements also ensure the longevity and efficiency of the equipment.
7. 3 Tips for Choosing the Right Laser Cutting Service for Your Business
After discussing the essential aspects of epoxy powder coating, it’s crucial to move towards another key industrial process: choosing the right laser cutting service for your business. See the following tips:
#1 Prioritize Material Capabilities
Different laser cutting services might specialize in various materials. It’s essential to choose a service that excels in cutting the specific materials you need for your projects. For example, some may specialize in metals like steel and aluminum, while others might have expertise in plastics or composites. Ensuring the service provider has the right expertise and equipment for your material requirements will lead to better quality.
#2 Assess Quality Control Measures
Quality control is non-negotiable when it comes to laser cutting services. Inquire about the provider’s quality assurance processes and certifications. Ensure they adhere to industry standards and have measures in place to consistently deliver high-quality cuts. This includes regular maintenance of their machinery and thorough inspection of finished products.
#3 Feedback and After-Sales Support
Finally, consider the service provider’s reputation. Check client feedback, testimonials, and case studies. This will give you an insight into their reliability and customer service. After-sales support is also crucial, especially if you require additional modifications or encounter any issues with the delivered product. A service that stands by its work and offers robust support is a valuable partner in any business venture.
Conclusion
Wrapping up, this comprehensive guide to laser cutting stainless steel sheets offers valuable insights into the technology, its applications, and best practices. It serves as an important resource for businesses looking to optimize their operations and harness the full potential of laser cutting in their projects.
For specialized, high-quality laser cutting services, consider Zemetal as your go-to partner. Our expertise and cutting-edge technology are tailored to meet your specific needs. To know more, feel free to contact us today.
Dive Deeper Into Our Resources
Looking for more diverse service options? Browse through our handpicked selections:
Still haven’t found what you’re looking for? Don’t hesitate to contact us. We’re available around the clock to assist you.