What is sandblasting? It’s a process where abrasive materials are blasted at high speed onto a surface to clean, smooth, or prepare it for further treatment.
As a Restoration Specialist, I often get asked about sandblasting and how it helps remove rust, old paint, and other surface contaminants effectively.
Don’t worry, the process is straightforward and highly effective for a wide range of surfaces.
In this guide, you will learn how sandblasting works, the materials commonly used, and why it’s a valuable technique for preparing metal surfaces.
So let’s begin!
1. Defining Sandblasting
Sandblasting plays a significant role in metal fabrication, employing high-speed particles to meticulously clean or texture metal surfaces. Its growth is underscored by a report from technavio, projecting the global sandblasting market to reach USD 2.99 billion from 2021 to 2026. This demand is fueled by the need for surface preparation in industries such as automotive, aerospace, construction, and manufacturing.
Additionally, infrastructure projects frequently require sandblasting for removing rust, corrosion, and old coatings, further driving the market.The precision and versatility of sandblasting enhance metal aesthetics and prep for treatments, proving essential for top-tier metalwork outcomes.
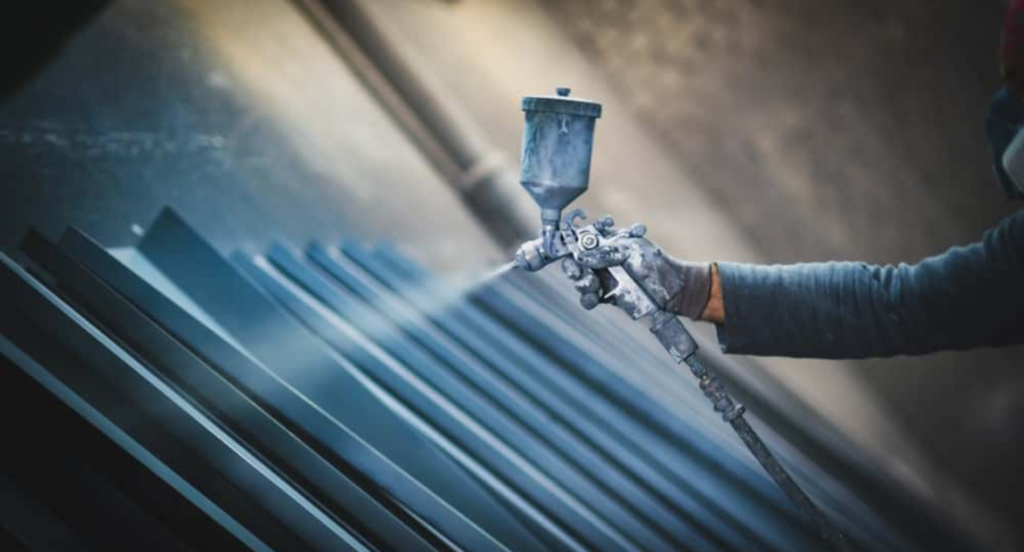
2. Benefits of Sandblasting
After discussing what sandblasting is and its pivotal role in metal fabrication, it’s important to delve into the numerous benefits it offers. Here are some key advantages:
Increased Efficiency and Productivity
The speed and effectiveness of sandblasting significantly boost productivity in metal fabrication processes. It allows for rapid cleaning and preparation of surfaces, reducing the time needed for manual labor. This efficiency is a game-changer in meeting tight project deadlines while maintaining high standards.
Extended Lifespan of Metals
Regular sandblasting can significantly extend the lifespan of metal products. By removing corrosive elements and preparing surfaces for protective coatings, sandblasting plays a vital role in preventing rust and decay. This preventative maintenance aspect of sandblasting is a key factor in ensuring the longevity and durability of metal products, contributing to cost-effectiveness in the long run.
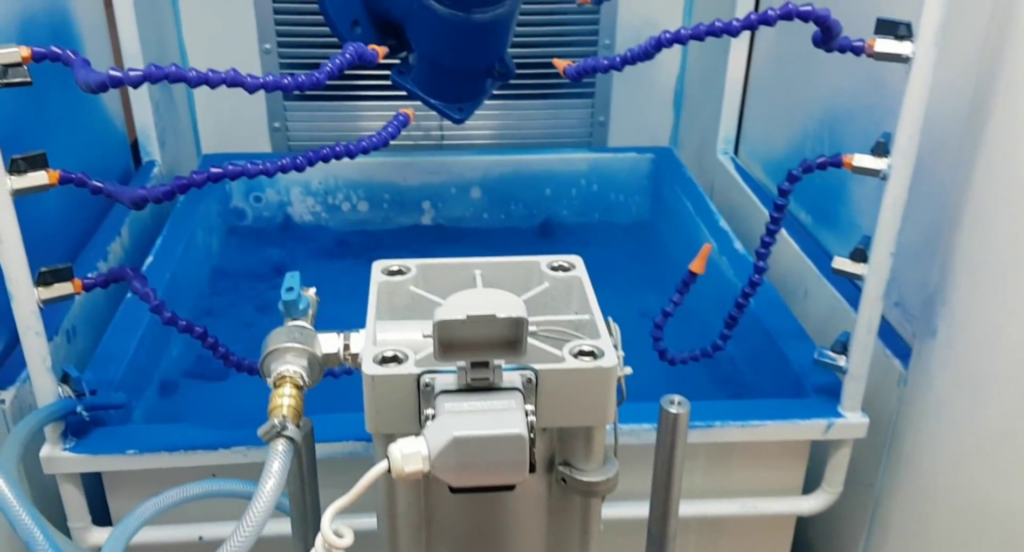
Precision and Uniformity
In the metal fabrication process, Zemetal harnesses sandblasting for its exceptional precision on metal surfaces. This technique ensures a consistent finish across extensive areas, crucial for maintaining uniform product quality. The reliability and uniformity provided by sandblasting are vital in industries that demand high precision, underlining its significance in achieving consistent and standardized results in metalwork.
3. Types of Sandblasting Techniques
Having explored the benefits of sandblasting, it’s equally important to understand the various techniques available. Each method offers unique advantages for different applications in metal fabrication. Let’s dive into some of these techniques:
- Dry Sandblasting: Traditional and widely used, dry sandblasting employs abrasive materials like sand to effectively strip rust, paint, and other surface debris. This method is particularly suited for robust, heavy-duty cleaning tasks.
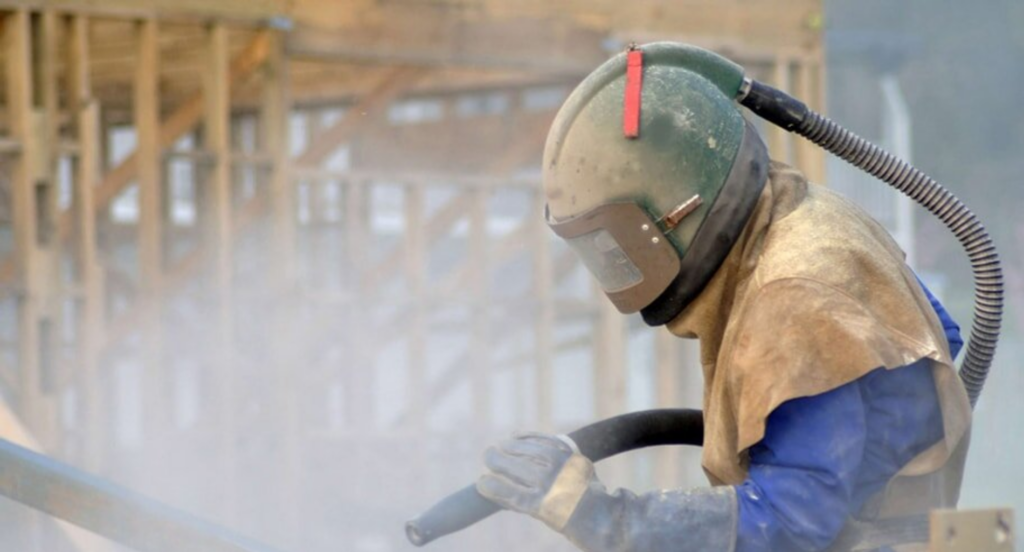
- Wet Sandblasting: In this approach, water is mixed with abrasive materials, significantly reducing dust emissions. Preferred for outdoor projects such as building or bridge maintenance, this technique lessens environmental impacts. It’s particularly useful in situations where dust suppression is essential.
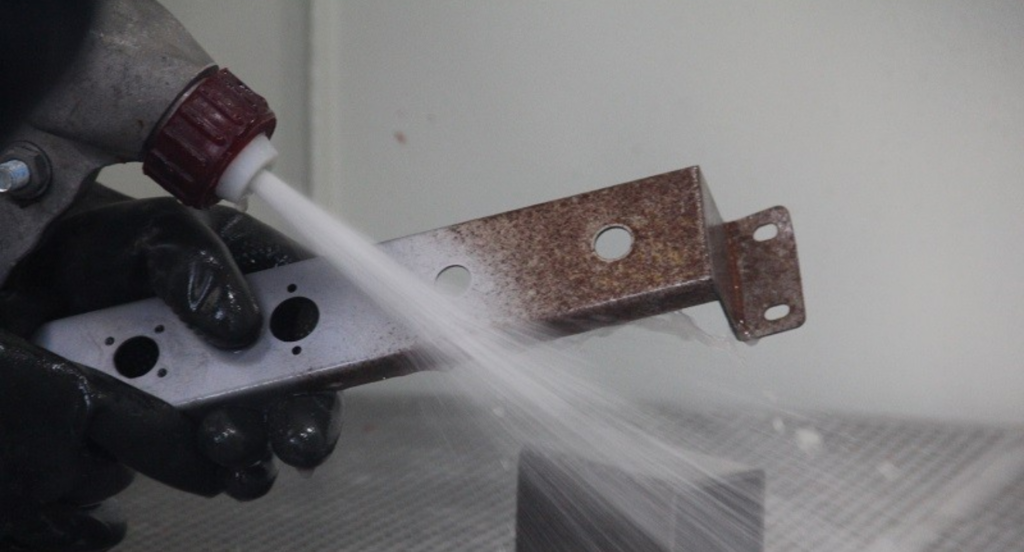
- Soda Blasting: Utilizing sodium bicarbonate, soda blasting offers a milder approach, perfect for delicate surfaces where minimal abrasiveness is required. This method proves invaluable for tasks like removing graffiti without harming the underlying structure.
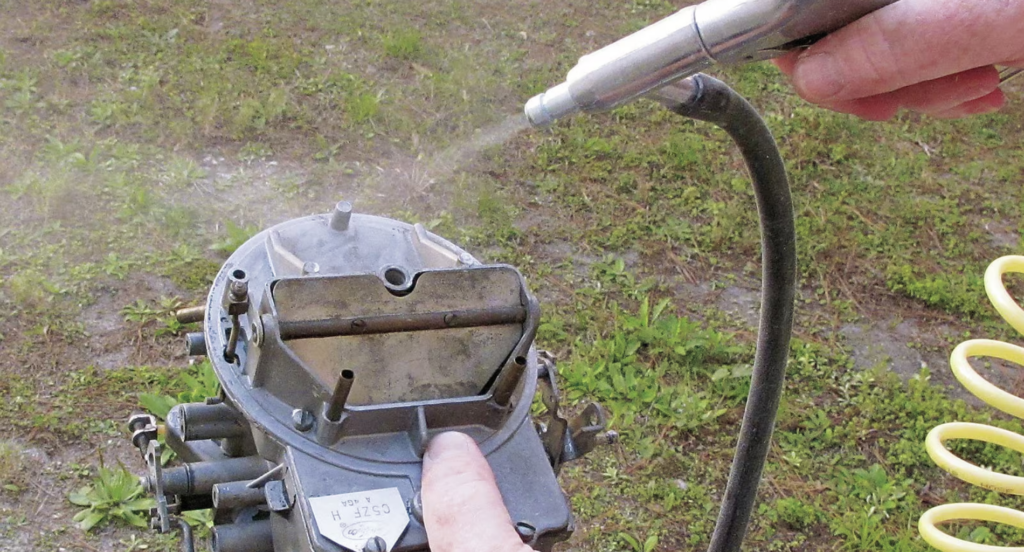
- Steel Grit Blasting: Employing steel grit as the blasting medium, this technique excels in aggressively clearing surfaces. Steel grit blasting is especially beneficial for prepping metal surfaces for welding, providing a clean base for optimal welding results.
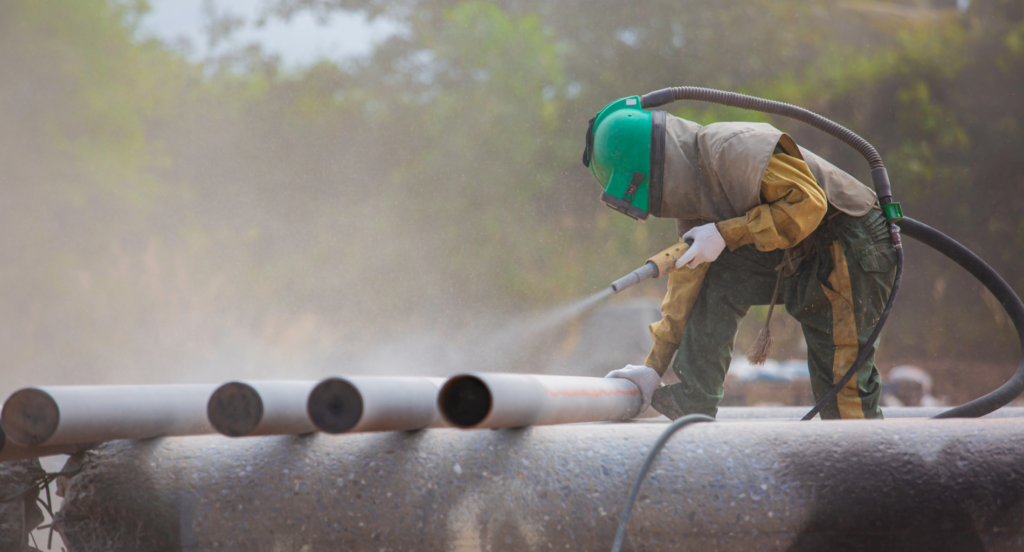
- Bead Blasting: Bead blasting uses fine glass beads and is great for achieving a smooth, clean finish on metal surfaces. This technique is frequently used in auto body work, ensuring a uniform surface ideal for subsequent painting or coating.
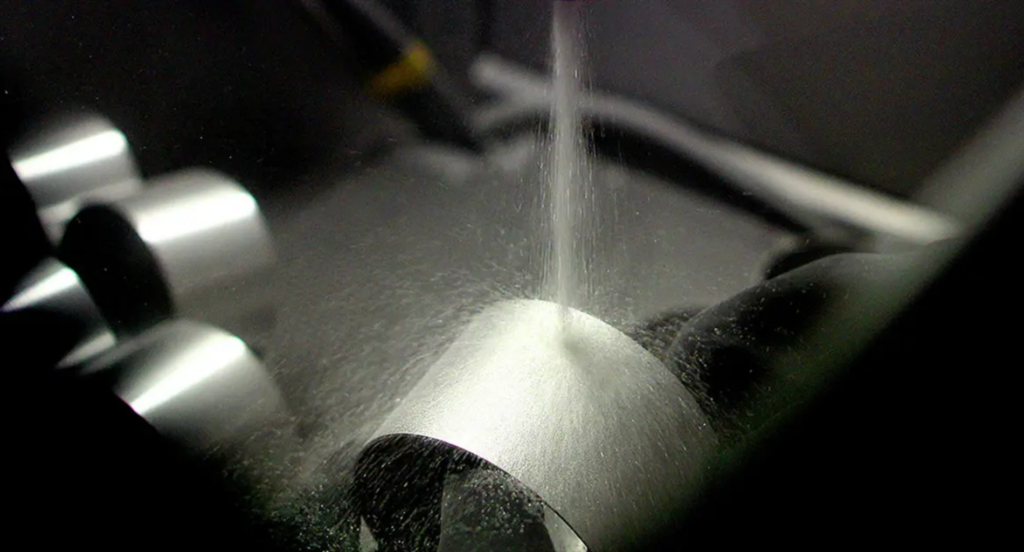
4. The Sandblasting Process
Following the overview of various sandblasting techniques, understanding the sandblasting process itself is crucial. This process, integral to metal fabrication, involves several key steps. Here’s a breakdown:
Step#1 Surface Preparation
The first step is to thoroughly clean the surface to be sandblasted. This involves removing any debris, oils, or existing coatings that might interfere with the sandblasting process. A clean surface ensures that the abrasive material can work effectively.
Step#2 Choosing the Right Abrasive
Selecting the appropriate abrasive material is vital for the desired outcome. Factors like the type of surface, the level of abrasion needed, and the intended finish guide this choice. Zemetal carefully selects abrasives to match each project’s specific requirements, ensuring optimal results.
Step#3 Setting Up the Equipment
Proper setup of the sandblasting equipment is essential. This includes preparing the blasting machine, air compressor, and nozzle. Ensuring the equipment is correctly configured guarantees efficiency and safety during the sandblasting process.
Step#4 Actual Sandblasting
The actual sandblasting involves projecting the abrasive material at high speed onto the surface. This step requires precision and control to achieve the desired level of abrasion without damaging the material. Having seen the transformation sandblasting can bring to the surface, the accuracy in this stage cannot be overstated.
Step#5 Cleaning and Finishing
After sandblasting, the surface undergoes thorough cleaning to remove any residual abrasive particles. The final step often involves inspections and any additional treatments, such as applying a protective coating to the newly sandblasted surface.
5. Applications of Sandblasting
With an understanding of the sandblasting process, we can now transition to its diverse applications across various industries. Sandblasting is a versatile technique, offering numerous benefits in different industrial settings. Here are some areas where sandblasting plays a critical role:
Aerospace Industry
In the aerospace industry, sandblasting plays a key role in maintaining and preparing aircraft components. It’s used for removing old paint, corrosion, and surface defects from aircraft parts, ensuring they meet the stringent safety and quality standards required in this field.
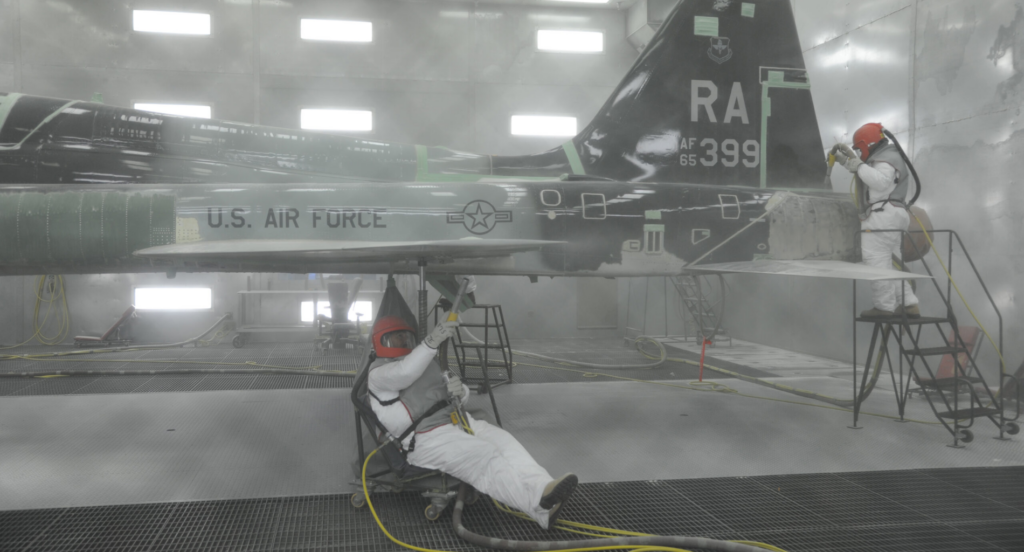
Marine Industry
The marine industry benefits greatly from sandblasting for maintaining and repairing ships and vessels. This technique effectively removes marine growth, rust, and old coatings from hulls and decks, ensuring these vessels maintain optimal performance and durability. It contributes significantly to the longevity and safety of marine crafts, an essential aspect in a sector that demands high resilience and reliability.
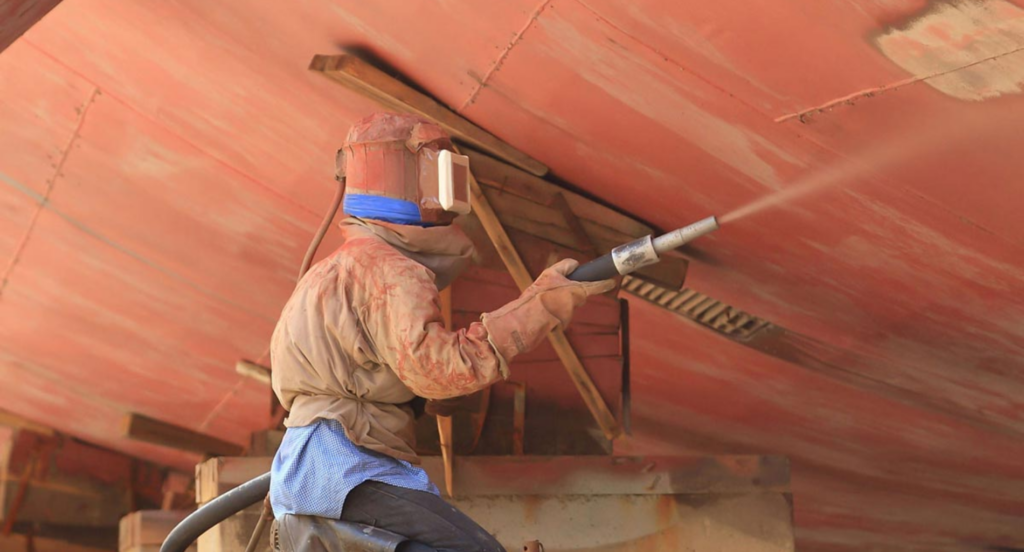
Oil and Gas Industry
In the oil and gas sector, sandblasting is a vital process for maintaining pipelines and preparing storage tanks. For example, it’s used to clean the inside of pipelines, removing corrosion and buildup that can hinder the flow of oil or gas. This is crucial not only for the efficient operation of these systems but also for preventing leaks and ensuring safety in this high-risk industry.
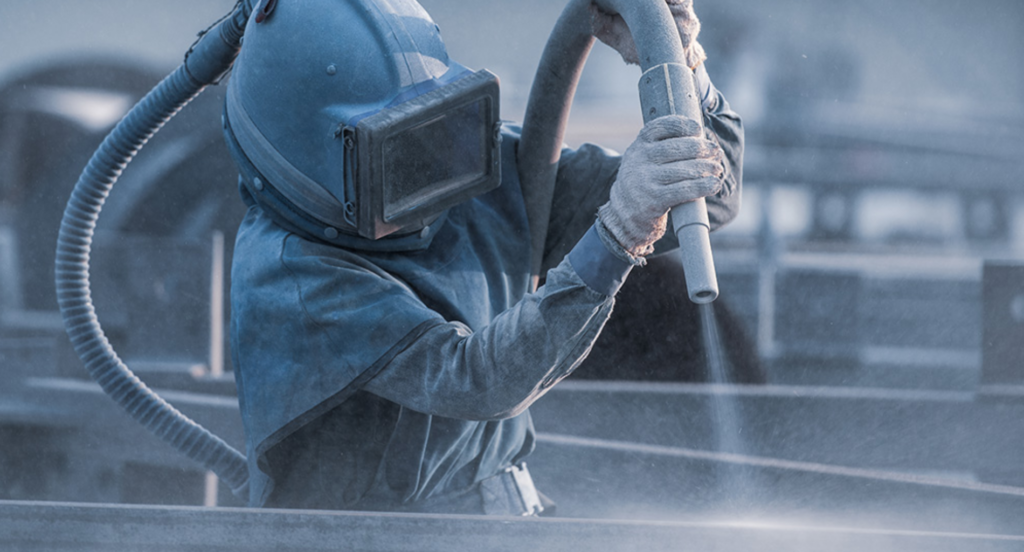
6. Safety Precautions in Sandblasting
While sandblasting is a versatile and effective technique used across industries, it’s equally critical to emphasize the safety precautions associated with its use. Ensuring the well-being of operators and the environment is paramount. Here are some essential safety measures to consider in sandblasting:
Protective Gear
Proper protective gear is non-negotiable in sandblasting operations. This includes heavy-duty gloves, goggles, face shields, and appropriate body covering. Respirators are particularly important to protect against inhaling fine abrasive particles. These safety equipment are essential for safeguarding operators from potential hazards associated with abrasive materials.
Ventilation and Dust Control
Effective ventilation systems are crucial in indoor sandblasting to prevent the accumulation of dust, which can be a health hazard. Additionally, using dust collection systems and wet sandblasting methods can significantly reduce airborne particles. This focus on dust control not only protects workers but also contributes to a cleaner and safer work environment.
Training and Procedures
Proper training in handling equipment and emergency procedures is vital. Operators should be well-versed in the machinery’s operation, the properties of different abrasives, and first-aid measures in case of accidents. Regular drills and updates on safety protocols ensure that the team is prepared for any contingencies, maintaining a high standard of safety in all operations.
This table details essential aspects of training and procedures for operators:
Aspect | Description | Importance in Operations |
Machinery Operation | Comprehensive training on machinery usage | Ensures efficient and safe operation |
Abrasives Knowledge | Understanding different abrasive properties | Vital for appropriate application |
Emergency First-Aid | Training in immediate accident response | Crucial for reducing injury impact |
Regular Safety Drills | Practicing and updating emergency procedures | Prepares team for potential emergencies |
Safety Protocol Updates | Keeping abreast with latest safety guidelines | Maintains ongoing operational safety |
7. 3 Tips for Effective Sandblasting
Building the emphasis on safety precautions for sandblasting, it’s equally important to focus on efficiency and effectiveness. Effective sandblasting requires a combination of skill, proper techniques, and the right tools. Here are some tips to ensure optimal results in your sandblasting projects:
#1 Choose the Right Abrasive
Selecting the appropriate abrasive material is critical for effective sandblasting. Factors like the type of surface, desired finish, and the level of aggressiveness needed should guide this choice. For example, using steel grit for removing heavy rust from structural steel ensures thorough and efficient cleaning.
#2 Maintain Proper Pressure and Distance
Optimal pressure and the right distance between the nozzle and the surface are key for effective sandblasting. Too much pressure or being too close can damage the surface, while too little pressure or being too far away will be ineffective. Adjusting these factors based on the material and the job ensures a balance between efficiency and surface protection.
#3 Regular Equipment Maintenance
Ensuring that sandblasting equipment is well-maintained and in good working order is essential. This includes regular checks of hoses, nozzles, and filters. Proper maintenance not only prolongs the life of the equipment but also guarantees consistent performance, reducing the risk of project delays or subpar results.
Conclusion
Sandblasting can be tricky if you’re dealing with stubborn surfaces or hard-to-remove materials. You need a process that’s both efficient and effective to get the job done right. At Zemetal, we’re here to help you achieve the perfect result with our top-notch sandblasting services.
In conclusion, this guide has broken down the basics of sandblasting and why it’s a powerful method for surface cleaning and preparation. If you’re ready to improve your project, reach out to us today. Zemetal excels in delivering the best sandblasting solutions for your needs.
Dive Deeper Into Our Resources
Looking for more diverse service options? Browse through our handpicked selections:
Still haven’t found what you’re looking for? Don’t hesitate to contact us. We’re available around the clock to assist you.