Has anyone wondered what screen printing really is in the metal fabrication world? It’s a term that’s often thrown around, but its full of significance.
With years of experience in the metal fabrication industry, I bring a wealth of knowledge that clarifies complex concepts, making them accessible and relevant to your business needs.
Understanding the true meaning of screen printing unlocks a realm of possibilities, transforming methods of product design and creation across the business landscape.
In this guide, we’ll dive deep into the technicalities, processes, and benefits of screen printing in metal fabrication.
Read on to learn how screen printing can elevate your business.
1. Brief Overview of Screen Printing
Screen printing in metal fabrication, where ink is pressed through a stenciled mesh screen to produce detailed designs, is renowned for its precision and adaptability across different metals. This process not only enhances the functionality but also the aesthetic appeal of metal products.
The growing significance of this method is highlighted by data from futuremarketinsights, which predicts the global screen printing mesh market will reach a remarkable US$ 1,134.2 million by 2033, indicating a robust and expanding industry reliance on screen printing techniques.Screen printing’s adaptability makes it a popular choice for diverse metal fabrication needs, combining precision with artistic flair.
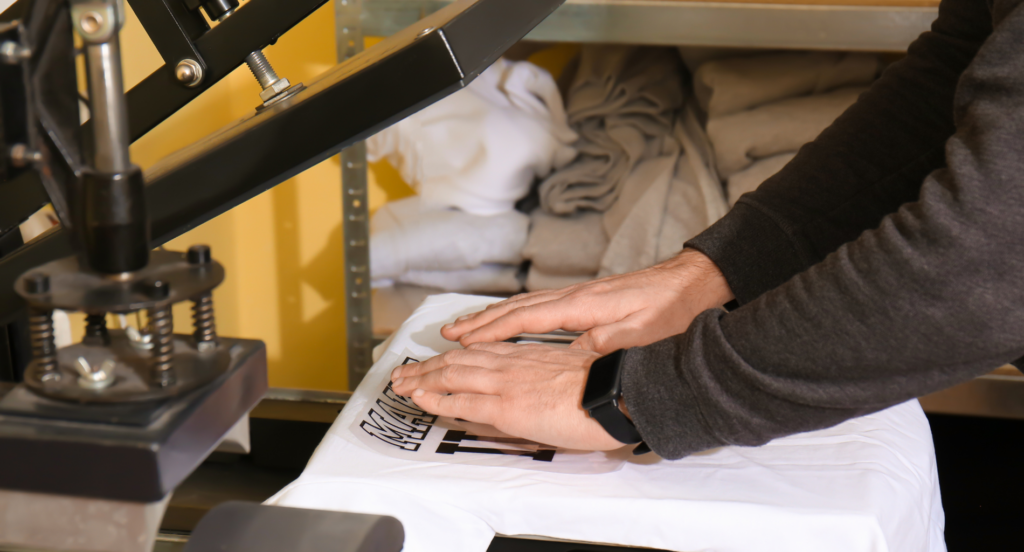
2. Benefits of Screen Printing in Metal Fabrication
Following the brief overview of screen printing, it’s clear this technique offers significant advantages in metal fabrication. Let’s explore some key benefits that make it a preferred method for businesses:
High-Quality and Durable Prints
Screen printing stands out for its ability to produce high-quality, durable prints. The ink layer is thicker compared to other printing methods, resulting in vibrant and long-lasting designs. This quality is especially beneficial in applications where metal products are exposed to harsh environments. For example, outdoor signs and machinery panels retain their clarity and vibrant colors for extended periods due to screen printing.
In this table, we delve into three key features of screen printing that contribute to its capacity for producing high-quality and durable prints, particularly beneficial for metal products used in challenging environments.
Feature of Screen Printing | Benefit for Print Quality | Application Example |
Thicker Ink Layer | Enhanced vibrancy and color depth | Outdoor signage exposed to sunlight |
Superior Ink Adhesion | Improved resistance to wear and tear | Machinery panels in industrial settings |
Versatility in Ink Types | Suitability for various environments | Marine equipment resistant to corrosion |
Enhanced Aesthetic Appeal
Screen printing greatly enhances the aesthetic appeal of metal products. It allows for vibrant, full-color designs that can transform a simple metal surface into a visually striking piece. This benefit is particularly valuable in consumer-facing products, where visual impact is crucial.
Versatility in Design and Application
The versatility of screen printing in metal fabrication is unmatched. It can accommodate a wide range of designs, from simple logos to complex patterns, all with high precision. This adaptability makes it ideal for a variety of projects, enhancing both the aesthetics and functionality of metal products. The ability to apply unique, intricate designs to metal surfaces is a testament to the technique’s artistic and technical capabilities.
3. Materials and Tools in Screen Printing
With the benefits of screen printing in metal fabrication established, understanding the essential materials and tools involved is key. Let’s delve into what’s needed to achieve those high-quality, durable prints:
- Screen and Frame: The core of screen printing is the screen itself, typically made of finely woven fabric stretched over a frame. The material of the screen varies based on the intricacy of the design and the type of ink used.
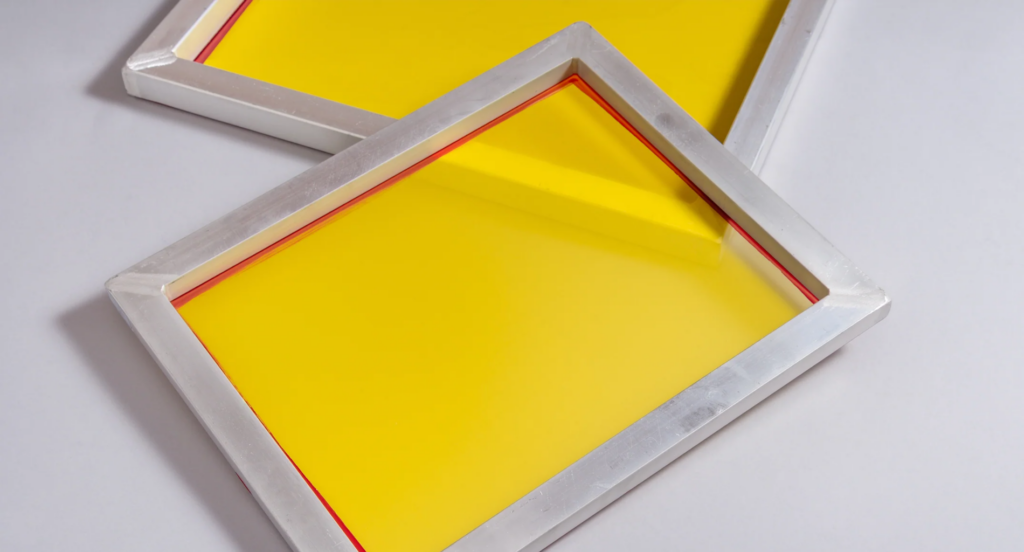
- Photo Emulsion and Sensitizer: Used for creating the stencil, the photo emulsion reacts with light, and the sensitizer initiates this reaction. These are applied to the screen to develop the detailed designs that are characteristic of screen printing.
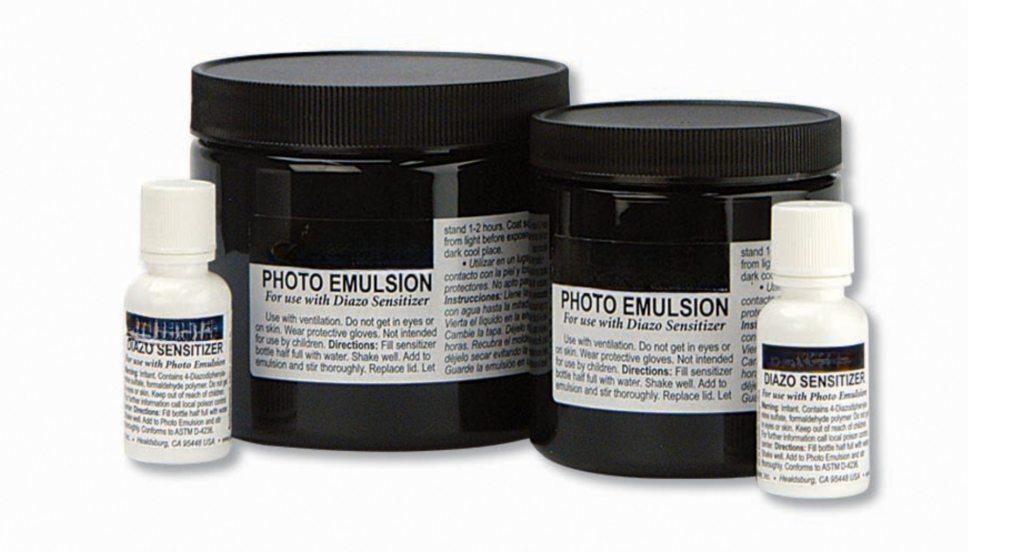
- Inks: Special inks in screen printing are essential for securing adherence to metal surfaces and ensuring durability. A variety of inks are available, specifically formulated for metal fabrication, to guarantee that prints remain both vibrant and enduring over time.
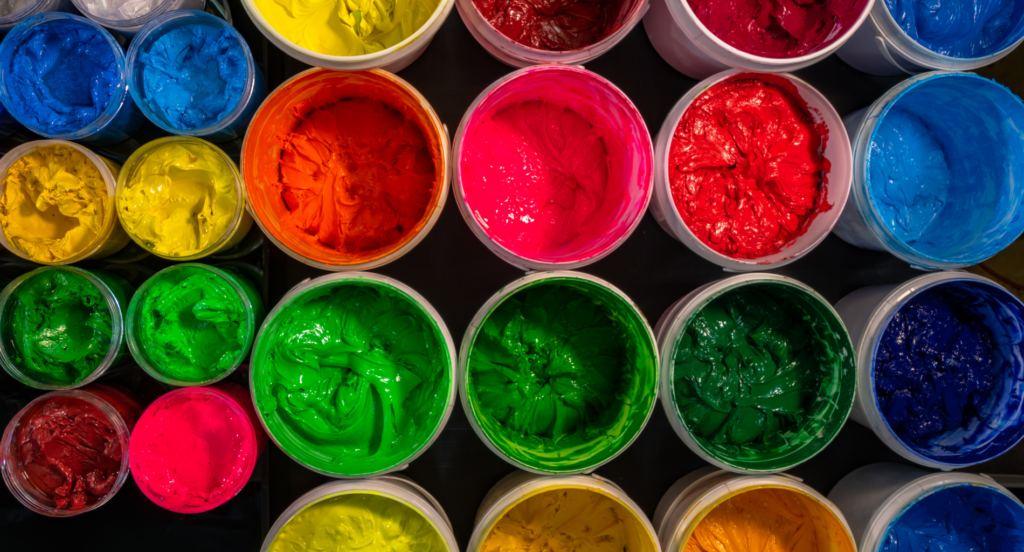
- Squeegee: Essential for evenly spreading the ink over the screen, a squeegee ensures that the ink is pressed through the mesh onto the metal surface. The squeegee’s precision in ink application is crucial for achieving sharp, clean prints.
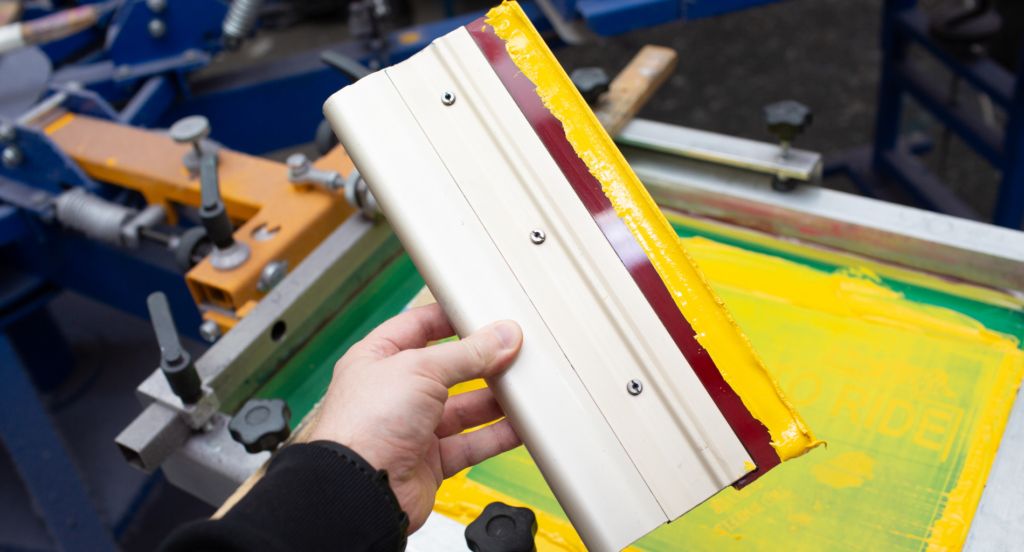
- Exposure Unit: This equipment is used to harden the photo emulsion, helping to create the stencil on the screen. The exposure unit is vital for accurate and detailed design transfer, especially for complex or fine patterns.
4. The Screen Printing Process
After exploring the essential materials and tools in screen printing, the next step is understanding the actual process. Below are the key stages involved in screen printing on metal surfaces:
Step#1 Screen and Frame Preparation
The process begins with stretching a fine mesh over a frame, creating the screen. This mesh is then coated with a light-sensitive emulsion. In screen printing, the quality of the screen setup directly impacts the precision of the print, making this initial step fundamental.
Step#2 Applying Ink
Once the screen is prepared, ink is applied to the top. Using a squeegee, the ink is evenly spread across the screen, with pressure ensuring it passes through the mesh onto the metal substrate. Consistent ink application is key to achieving uniform color and design.
Step#3 The Printing Process
After inking, the screen is placed on the metal surface, and the ink is pressed through the stencil onto the substrate. This step requires precision to ensure the design is accurately transferred. For example, in creating custom metal signage, this precision is critical for readability and visual appeal.
Step#4 Curing the Ink
Following printing, the ink on the metal needs to be cured, often through a heat process. This solidifies the ink, making the design durable and resistant to environmental factors. The curing step is a delicate balance; too much heat can damage the metal, while too little may leave the ink vulnerable.
Step#5 Cleaning and Reclaiming the Screen
Finally, the screen is cleaned, removing all ink residues, and the emulsion is stripped for reuse. This maintenance is essential for the longevity of the screen and consistency in future prints. Proper cleaning ensures the screen is ready for the next project without compromise in quality.
5. Technological Advancements in Screen Printing
Having outlined the screen printing process, it’s fascinating to see how technology has enhanced this method over time. Let’s take a look at some of the major technological advancements in screen printing:
Digital Screen Making
One significant advancement is digital screen making. This technology replaces traditional manual methods with digital processes, improving accuracy and reducing preparation time. Screens can now be prepared with precision and consistency, ensuring that even the most intricate designs are flawlessly replicated. This shift to digital has revolutionized the screen printing workflow, making it more efficient and reliable.

Advanced Inks and Coatings
The development of advanced inks and coatings has been evolving. These new formulations offer better adhesion to metal surfaces, enhanced color brightness, and increased durability. They also allow printing on a wider range of metal types and finishes. This innovation in ink technology has opened up new possibilities for metal fabrication, broadening the scope of projects and applications.
Automated Screen Printing Machines
The introduction of automated screen printing machines has greatly increased production speed and consistency. Zemetal utilizes these machines to offer clients faster turnaround times while maintaining high-quality prints. This automation significantly benefits the metal fabrication industry by enabling large-scale, consistent production, reducing labor costs, and minimizing human error, thereby enhancing efficiency.
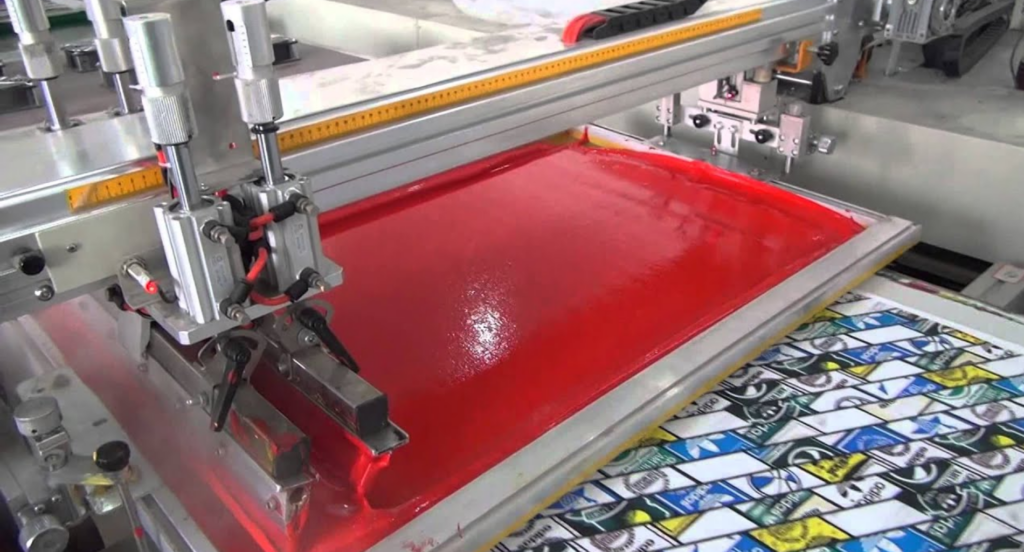
6. Screen Printing vs. Other Printing Techniques
Building upon the technological advancements in screen printing, it becomes important to understand how it compares to other printing methods. Let’s delve into how how screen printing stands apart in various aspects:
Screen Printing vs. Laser Engraving
Screen printing excels in producing colorful prints for larger runs with its scalability and cost-effectiveness, involving ink pushed through a mesh screen onto metal surfaces. Laser engraving, in contrast, uses laser beams to etch designs directly onto metal surfaces. This method is ideal for precise, permanent markings and detailed graphics, excelling in precision and permanence but without color, unlike screen printing.
Screen Printing vs. Pad Printing
Screen printing is versatile in handling a wide range of designs on various surfaces, including metals. It’s particularly efficient for uniform and large-scale production runs, offering durable prints. Pad printing transfers ink from a plate to the product using a silicone pad. While excellent for three-dimensional objects and uneven surfaces, pad printing is more suited for smaller designs, unlike screen printing’s expansive, vibrant creations.
7. 3 Practical Tips for Effective Screen Printing
Moving from the comparison of screen printing with other techniques, it becomes essential to focus on maximizing its potential. Here are some practical tips to ensure the most effective screen printing outcomes:
#1 Selecting the Right Mesh Count
Choosing the appropriate mesh count is crucial for screen printing. A higher mesh count is best for detailed designs, as it allows for finer ink deposition. Conversely, a lower mesh count is suitable for bolder, less detailed graphics. This selection impacts the clarity and quality of the final print, making it a vital step in the screen printing process.
#2 Proper Ink Preparation and Handling
Maintaining the right consistency of inks is vital in screen printing. Properly mixed inks at the correct viscosity are key to achieving high-quality prints. Zemetal specializes in providing these, such as solvent-based inks, tailored for specific metal substrates to optimize adhesion and longevity. They emphasize the importance of regular stirring to ensure consistent ink quality, enhancing the printing process’s overall effectiveness.
#3 Accurate Exposure Times
The exposure time during the stencil-making process is critical. Too little exposure can result in underdeveloped screens, while too much exposure can lead to difficulty in washing out the design. Finding the right balance ensures a crisp, clean transfer of the design onto the metal surface. This precision in exposure time is a subtle art, yet it makes a world of difference in the quality of the print.
Conclusion
Screen printing is a crucial and transformative technique in metal fabrication, enhancing both aesthetic and functional aspects. This comprehensive overview provides valuable insights for businesses looking to optimize their fabrication processes.
For those looking to delve deeper into screen printing or seeking expert services, Zemetal is your ideal partner. To discover more about our offerings and how we can support your business, feel free to contact us.
Dive Deeper Into Our Resources
Looking for more diverse service options? Browse through our handpicked selections:
Still haven’t found what you’re looking for? Don’t hesitate to contact us. We’re available around the clock to assist you.