Have you ever wondered how metal surfaces can transform the quality and appeal of your products? Metal surfaces offer a unique combination of durability and aesthetics that are essential in today’s market.
With years of experience in metal fabrication, I bring a depth of knowledge and insight that can help you understand the potential of these materials.
Metal surfaces are more than just a practical choice; they are a canvas of possibilities. From the sleek and modern to the rugged and industrial, the right metal surface can define the character of a product.
In this blog, we’ll delve into the world of metal surfaces, exploring their types, benefits, and applications. You’ll gain insights into how to choose the right metal surface for your specific needs.
So, keep reading.
1. Overview of Metal Surfaces
Metal surfaces are fundamental in manufacturing and design, offering both visual appeal and practical durability. Stainless steel, noted for its corrosion resistance, and aluminum, favored for its lightness and adaptability, are among the variety of metals used. Copper and brass are also popular, valued for their unique colors and antimicrobial properties, making them suitable for both decorative and health-oriented uses.
The enhancement of these surfaces through various treatments and finishes is crucial. Different techniques not only augment the metal’s resistance to corrosion but also provide diverse visual finishes. Incorporating recent industry data, it’s noted that the global metal surface treatment service market is projected to expand at a Compound Annual Growth Rate (CAGR) from 2023 to 2029, according to Industry Research.
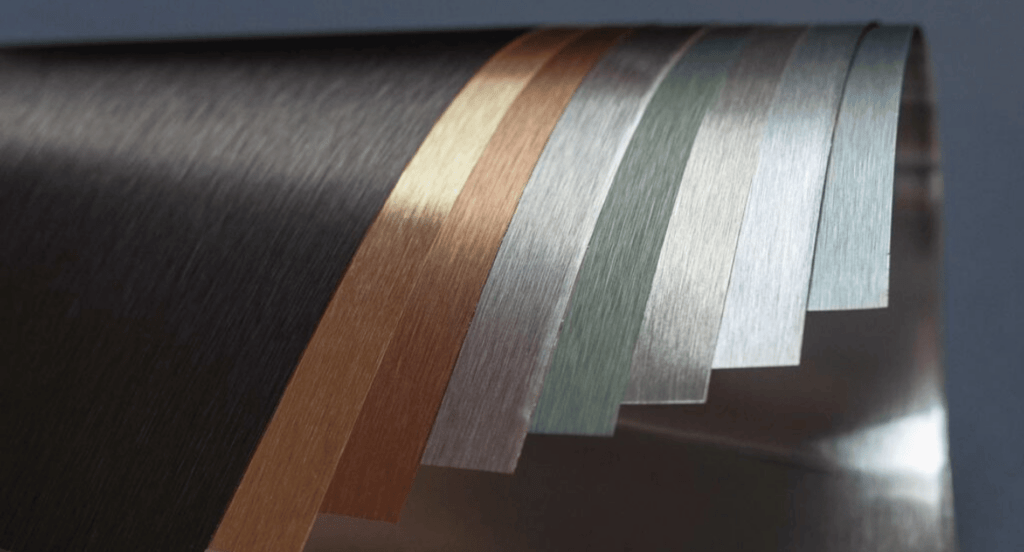
2. Types of Metal Surfaces
As we’ve seen in the overview, metal surfaces play a pivotal role in various industries, offering unique properties that cater to specific needs. Here are some common types of metal surfaces:
- Stainless Steel: Known for its corrosion resistance, it’s widely used in kitchenware, medical instruments, and architecture.
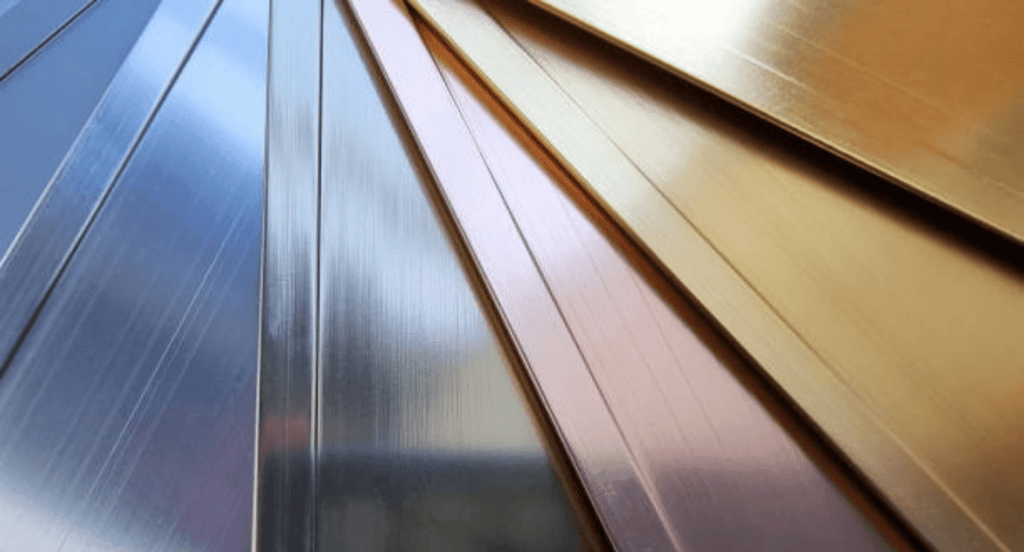
- Aluminum: Lightweight yet strong, it’s popular in automotive and aerospace industries for its durability and malleability.
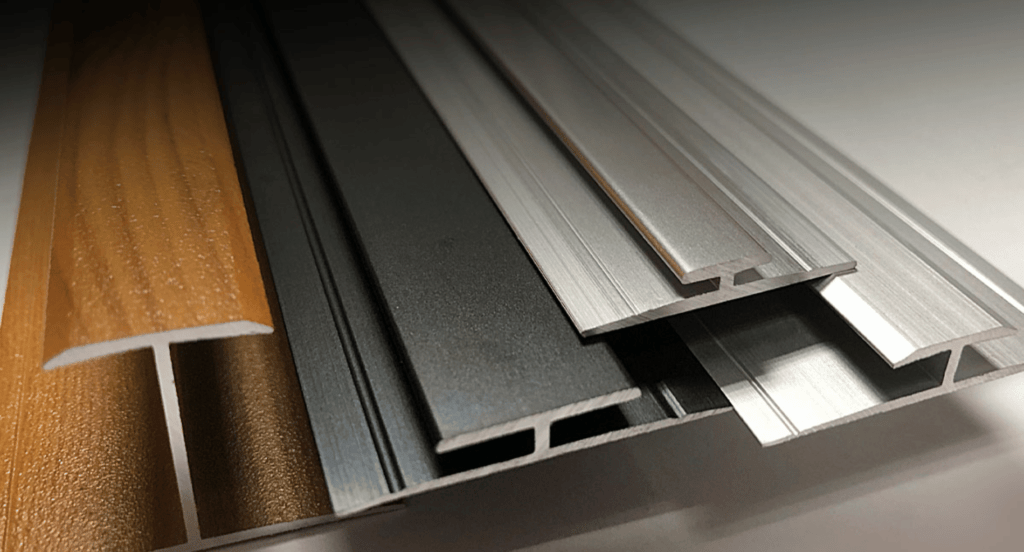
- Copper: Valued for its conductivity and antimicrobial properties, ideal for electrical components and healthcare settings.

- Galvanized Steel: Steel coated with a layer of zinc to prevent rusting, used in outdoor structures and automotive bodies.
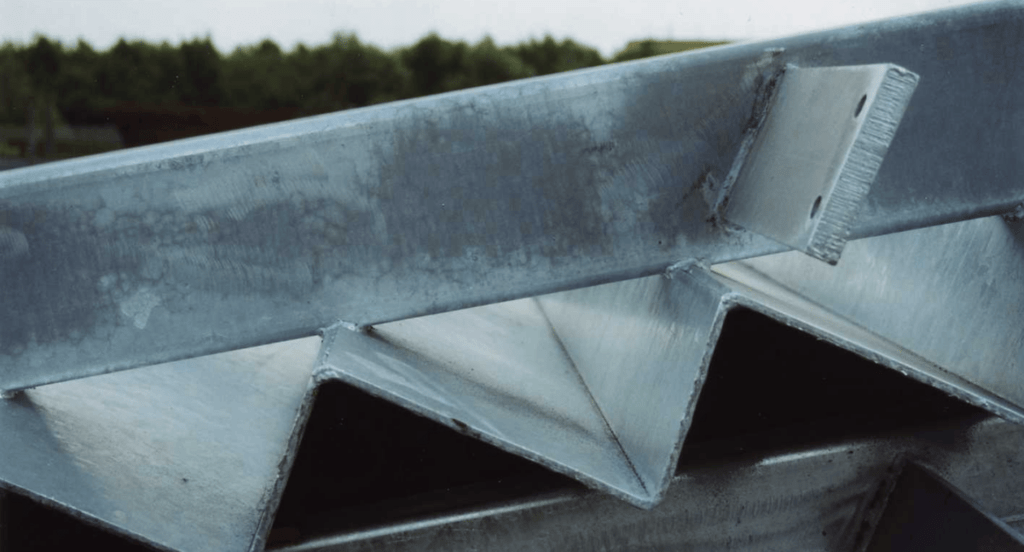
- Titanium: Known for its high strength-to-weight ratio and corrosion resistance, it’s used in aerospace, medical devices, and sports equipment.
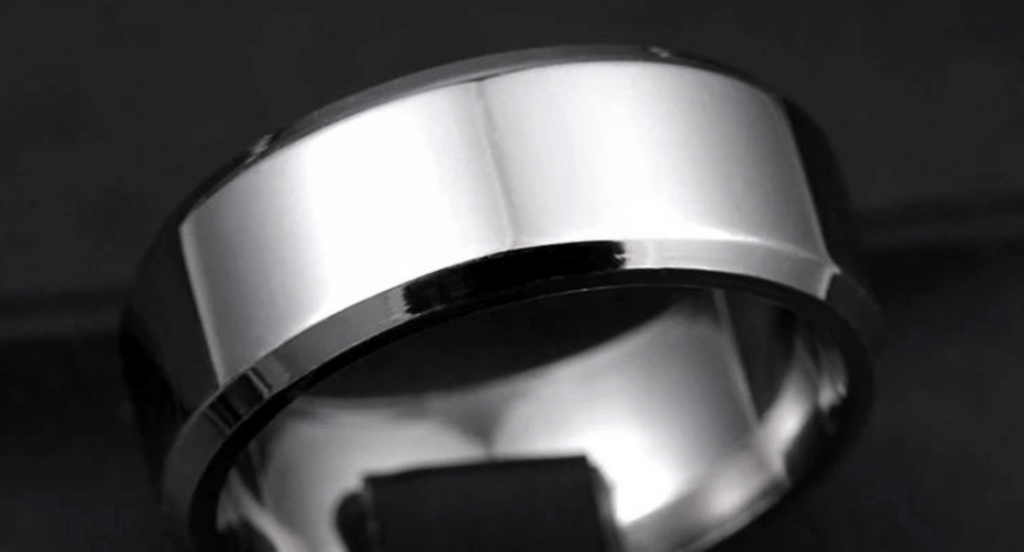
- Nickel: Offers a smooth, polished finish and is used for its protective and decorative properties in coatings and alloys.
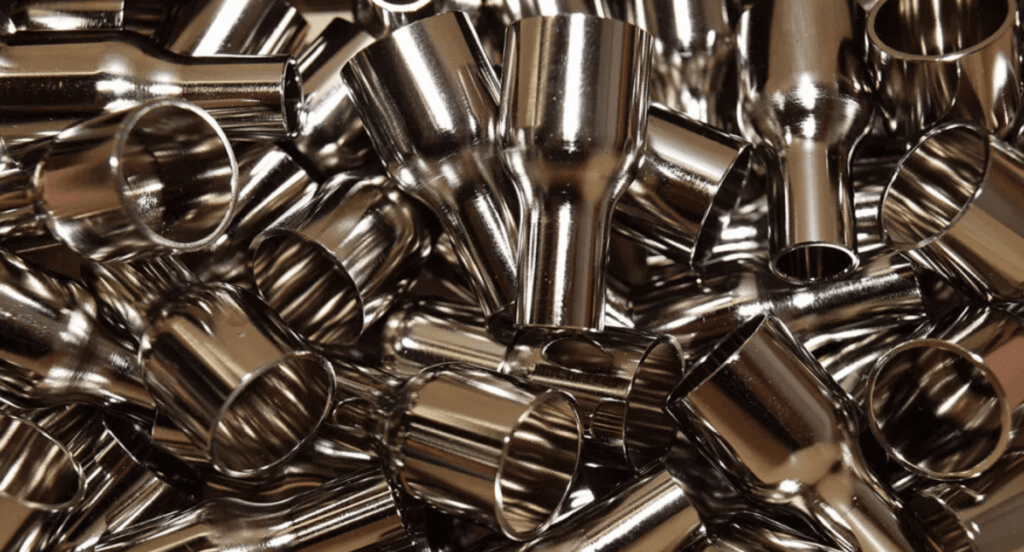
3. Properties of Metal Surfaces
In the context of the types of metal surfaces we’ve discussed, their properties are equally vital for making informed decisions in their application. Understanding these characteristics is key to leveraging their full potential in various industries. Here are some essential properties of metal surfaces:
Durability and Strength
Metals like stainless steel and titanium stand out for their exceptional durability and strength. They are highly resistant to wear and tear, making them ideal for heavy-duty applications. This robustness is crucial in sectors where longevity and reliability are paramount. The load-bearing capacity of metals like steel and titanium is also a significant factor, especially in structural applications where tensile strength is critical.
Aesthetic and Design Flexibility
The aesthetic appeal of metals cannot be overstated. Metals such as brass and copper offer distinct colors and sheens, providing a unique visual appeal that enhances the design of products. Furthermore, the ability to customize metal surfaces through various treatments like anodizing and electroplating broadens the scope for designers and manufacturers.
Corrosion Resistance
Corrosion resistance is a crucial property, especially for metals used in outdoor or harsh environments. Stainless steel and galvanized steel, for example, are highly resistant to rust and corrosion, which prolongs their lifespan and reduces maintenance needs. This property is especially beneficial in industries like marine, construction, and automotive, where exposure to corrosive elements is frequent.
Here’s a concise overview of corrosion resistance in metals, highlighting their significance in combating environmental challenges across various industries.
Metal Type | Industries Benefiting | Key Benefits |
Stainless Steel | Marine, Construction | High resistance to rust, minimal maintenance |
Galvanized Steel | Automotive, Construction | Protective zinc coating, durable |
Aluminum | Marine, Aerospace | Lightweight, naturally resistant to corrosion |
Copper | Electrical, Marine | Antimicrobial properties, corrosion-resistant |
Titanium | Aerospace, Marine | Exceptional strength, highly resistant |
Conductivity and Reactivity
The conductivity of metals is a significant aspect, especially in electrical and thermal applications. At Zemetal, metals like copper are known for their excellent electrical and thermal conductivity, making them indispensable in electrical components and heat exchangers. On the other hand, the chemical reactivity of metals like aluminum is a critical factor in certain applications.
4. Different Surface Treatment Techniques
The properties of metal surfaces, as previously outlined, can be significantly enhanced and modified through various surface treatment techniques. Here are some of the most commonly used surface treatment techniques:
Anodizing
Anodizing is a process primarily used for aluminum surfaces. It involves an electrochemical procedure that thickens the natural oxide layer on the surface of metal parts. This treatment enhances the metal’s durability, corrosion resistance, and wear resistance. Additionally, anodizing allows for the introduction of colored dyes, giving the metal a decorative and visually appealing finish.
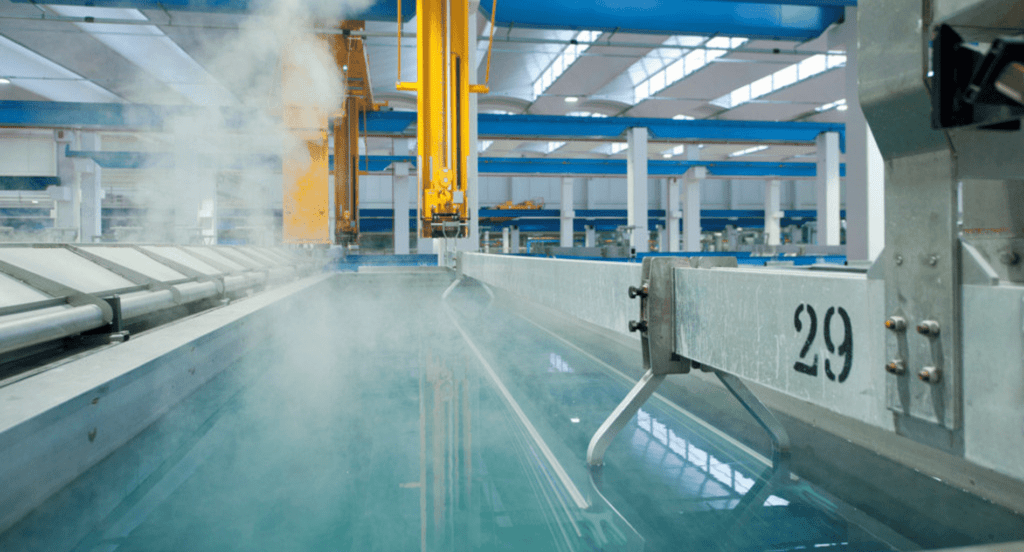
Powder Coating
Powder coating is a popular surface treatment used to create a hard, durable finish on metals. It involves applying a dry powder, typically a polymer or epoxy, which is then cured under heat to form a skin-like layer. This coating is more resistant to chipping, scratching, and fading compared to traditional paint. It’s widely used for a variety of applications due to its durability and versatile finish options.
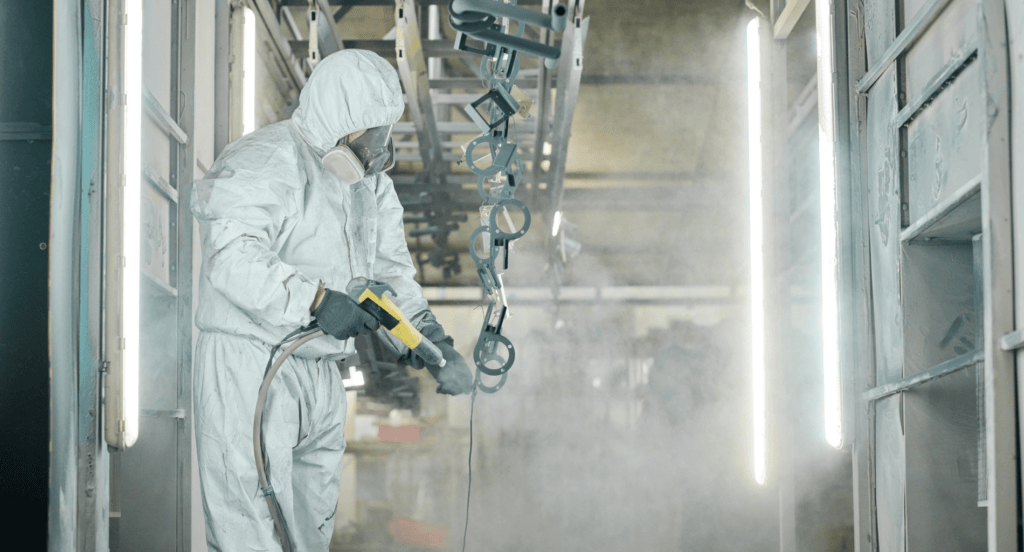
Electroplating
Electroplating involves depositing a thin layer of one metal onto the surface of another by using an electric current. This process enhances various properties of the base metal, including corrosion resistance, abrasion resistance, and aesthetic appeal. Common metals used for electroplating include nickel, chromium, and gold. This technique is widely used in the automotive, jewelry, and electronics industries.
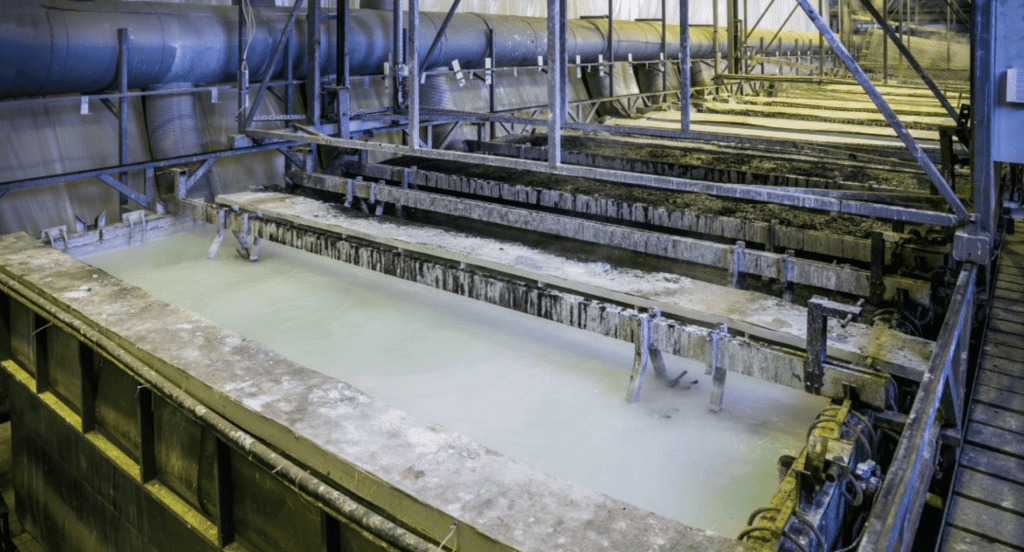
Heat Treatment
Heat treatment is a controlled process of heating and cooling metals to alter their physical and mechanical properties without changing their shapes. This treatment can increase the strength, hardness, and toughness of the metal. At Zemetal, it is a crucial step in many manufacturing processes, especially for metals that need to withstand high stress or extreme conditions, like steel used in construction and tool-making.
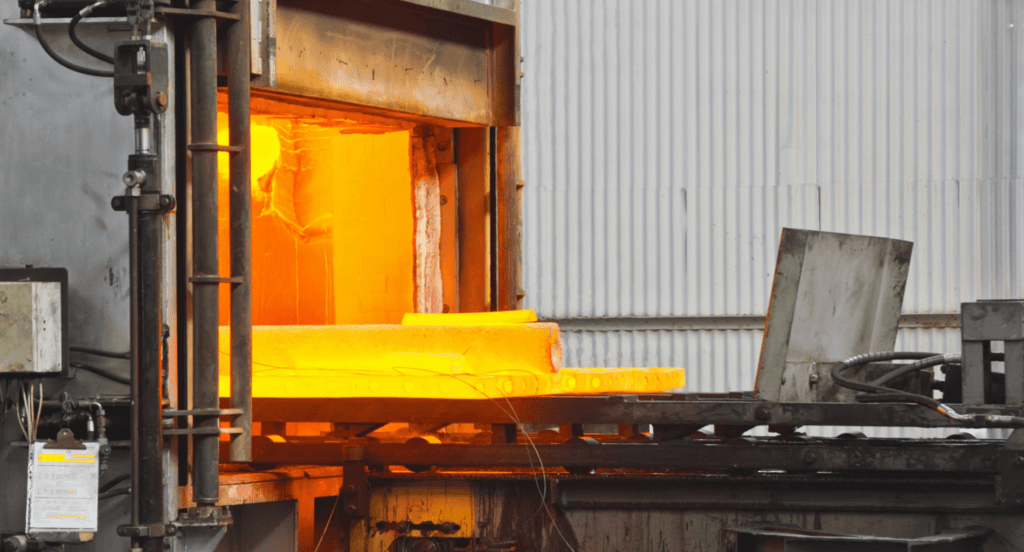
5. Applications of Metal Surfaces
The various surface treatment techniques we’ve discussed greatly expand the applications of metal surfaces in different sectors. Here are some of the key applications of treated metal surfaces:
Automotive Industry
In the automotive industry, metal surfaces play a critical role. Surface treatments like electroplating and powder coating are applied to improve wear resistance and aesthetics, with electroplated chrome being a popular choice for decorative elements and powder coating used for durable, color-fast finishes on body parts.
Construction and Architecture
The construction and architecture sectors heavily rely on metal surfaces for both structural integrity and aesthetic purposes. Steel, known for its strength and durability, is a staple in building frameworks, reinforcements, and roofing. In architecture, metals like copper and bronze are used for their unique colors and textures, enhancing the visual appeal of buildings and monuments.
Consumer Electronics and Appliances
Metal surfaces are essential in consumer electronics and appliances. Aluminum, with excellent heat dissipation properties, is a popular choice for electronic devices. Surface treatments like anodizing provide scratch-resistant and visually appealing finishes for electronic casings, while electroplating is employed to enhance the electrical conductivity of various components.
6. Common Challenges with Metal Surfaces
While metal surfaces have diverse applications, as discussed earlier, they also come with their own set of challenges. Here are some of the common challenges associated with metal surfaces:
Corrosion
Corrosion is one of the primary challenges faced by metal surfaces, especially in environments exposed to moisture, chemicals, or saline conditions. Metals like iron and steel are particularly susceptible to rusting, which can weaken their structural integrity. Preventive measures, such as galvanization, powder coating, and the use of corrosion-resistant alloys like stainless steel, are essential to mitigate this issue.
Wear and Tear
Regular use and exposure to abrasive conditions can lead to wear and tear of metal surfaces. This is a significant concern in industries like automotive and manufacturing, where metal parts are subject to constant friction and stress. Implementing surface treatments such as hardening, anodizing, or the application of wear-resistant coatings can enhance the durability of these metal surfaces.
Aesthetic Degradation
Over time, metal surfaces can suffer from aesthetic degradation, such as fading, staining, or losing their sheen. This issue is particularly important in consumer-facing applications, like appliances and architectural elements, where appearance is crucial. Regular maintenance, along with the choice of appropriate surface treatments and finishes, can help preserve the visual appeal of metal surfaces.
7. 4 Factors Affecting Surface Quality
As we have explored the various applications and challenges of metal surfaces, it’s evident that maintaining high surface quality is essential for their performance and longevity. Here are some critical factors affecting the surface quality of metals:
#1 Material Composition
The inherent composition of the metal significantly affects its surface quality. Different alloys and grades have varying properties, like hardness, grain structure, and impurity levels, which can influence the surface’s susceptibility to issues like corrosion, tarnishing, and wear. For instance, higher grades of stainless steel offer better corrosion resistance, while certain aluminum alloys may be more prone to surface irregularities.
#2 Manufacturing Processes
The processes used in manufacturing metal products, such as rolling, casting, or forging, can impact surface quality. These processes can introduce surface defects like cracks, pits, or scratches, which might compromise the final product’s appearance and performance. Ensuring precision and control during these processes is vital to minimize such defects.
#3 Surface Treatment Methods
The type and quality of surface treatments applied to metal surfaces are crucial factors. Techniques like anodizing, plating, and coating not only enhance the metal’s appearance but also protect it from environmental factors. However, improper application of these treatments can lead to issues like uneven coating, discoloration, or reduced protection against corrosion.
#4 Environmental Exposure
The environment in which a metal product is used plays a significant role in its surface quality. Exposure to harsh conditions like extreme temperatures, moisture, chemicals, and UV radiation can degrade the surface over time. Metals used in outdoor or industrial settings need to be appropriately treated and maintained to withstand these conditions and retain their surface quality.
Conclusion
As we’ve explored, metal surfaces are not just functional components; they are integral elements that can elevate the value and appeal of your products. Understanding metal surfaces is key to making informed decisions that can set your business apart in the competitive world of metal fabrication.
For those looking to enhance their products with high-quality metal surfaces, Zemetal offers expert metal fabrication services. Contact us today to discover how we can help you achieve your business goals.
Dive Deeper Into Our Resources
Looking for more diverse service options? Browse through our handpicked selections:
Still haven’t found what you’re looking for? Don’t hesitate to contact us. We’re available around the clock to assist you.