Ever considered how prototype sheet metal fabrication can change the way your products are developed? It’s a vital process, turning designs into physical prototypes to assess design efficacy and practicality.
With extensive industry experience and specialized knowledge, we provide critical and actionable insights equipping businesses with the tools and understanding to elevate product quality.
Prototype sheet metal fabrication is not just a process; it’s a transformative journey for any design, adding practicality and market readiness. It acts as the link between an idea and the end consumer, shaping the future of product development.
In this guide, we will dive into the complex world of prototype sheet metal fabrication, uncovering its methodologies, significance, and impact on the modern manufacturing sector.
Read on to unlock the secrets of effective prototyping.
1. Basics of Prototype Sheet Metal Fabrication
Prototype sheet metal fabrication is the initial phase in manufacturing, involving the creation of a sample or ‘prototype’ to evaluate a design’s feasibility and functionality. This is critical for identifying potential issues before mass production, saving time and resources. It involves various techniques like cutting, bending, and assembling, which are adapted based on the complexity and requirements of the prototype.
Understanding the materials and their properties is key in this stage. Different metals like aluminum, steel, and copper, each with distinct characteristics, are selected based on the prototype’s intended function and the environment it will operate in. This selection impacts the fabrication process, influencing the methods and tools used.
2. Design Considerations in Prototyping
Building on the basics of prototype sheet metal fabrication, it’s vital to dive into the design considerations that shape the prototype’s effectiveness and usability. Here are the key considerations:
Modular Design
In prototyping, adopting a modular design approach can be highly beneficial. This involves creating the prototype in separate, easily replaceable modules or sections, allowing for easier modification and testing of individual components. Modular designs facilitate flexibility and rapid changes, which are crucial in the prototyping phase.
Simplicity and Minimalism
Emphasizing simplicity and minimalism in prototype design can lead to more efficient and cost-effective fabrication processes. This approach involves reducing the prototype to its essential features, eliminating unnecessary complexities that could interrupt manufacturing or increase costs. A minimalist design often results in a more straightforward and user-friendly final product.
Functional Aesthetics
Balancing functionality with aesthetics is essential in prototype design, especially for consumer-facing products. This involves creating a prototype that is not only operationally efficient but also visually appealing. Functional aesthetics can play a significant role in the marketability and user acceptance of the final product.
Sustainable Design
Incorporating sustainability and eco-friendliness into prototype design is becoming increasingly important. This includes using recyclable materials, designing for energy efficiency, and minimizing waste during the fabrication process. Sustainable design practices not only benefit the environment but also connect with eco-conscious consumers and can enhance the brand image.
3. The Prototype Fabrication Process
Following the careful considerations in design, the next critical phase is the prototype fabrication process, bringing a design from concept to reality. Here are the steps involved:
Step#1 Design and CAD Modeling
The process begins with creating a detailed digital model using Computer-Aided Design (CAD) software. This step converts the initial concept into a precise 3D model, capturing every aspect of the proposed design. The CAD model acts as the foundational blueprint for all following fabrication steps.
Step#2 Material Preparation and Processing
The selected material is then prepared, involving cutting it to size and shaping it according to the design requirements. Techniques like bending, stamping, or other forming methods are employed to meet specific design specifications. Surface treatments or coatings may also be applied to enhance the material’s properties or appearance.
Step#3 Component Fabrication
Individual components of the prototype are fabricated using techniques such as laser cutting, punching, or precision machining. Each part is meticulously crafted to match the exact dimensions and specifications outlined in the CAD model. The precision in this step is crucial for the overall fit and function of the assembled prototype.
Step#4 Assembly and Integration
Once all components are fabricated, they are assembled to construct the complete prototype. This involves joining the parts using techniques appropriate to the design and materials, such as welding, soldering, or using mechanical fasteners, depending on the materials and design. The focus during assembly is on aligning each component accurately, ensuring the prototype’s structural integrity.
Step#5 Testing and Evaluation
Once assembled, the prototype undergoes various tests to assess its performance, durability, and functionality. For example, these tests can include stress analysis, operational simulations, and quality inspections. The objective is to verify that the prototype adheres to the design criteria and performs as expected in its intended environment.
Step#6 Feedback and Iteration
Based on the testing results, feedback is collected, leading to potential modifications to the prototype. This ongoing process involves revising the design, changing fabrication techniques, or adjusting materials, as necessary. The prototype is re-evaluated after each change to ensure it meets the desired standards and functions optimally.
4. Prototyping for Different Industries
Moving beyond its process, prototyping is essential in various industries, each utilizing it in unique ways to address their specific needs.Here’s how prototyping is used across different sectors:
Automotive Industry
In the automotive sector, prototyping is primarily used for developing body panels, engine components, and structural frames. These prototypes are crucial for testing aerodynamics, safety features, and overall vehicle performance before mass production. The process allows for rapid revisions and improvement, ensuring that the final products meet strict automotive standards.
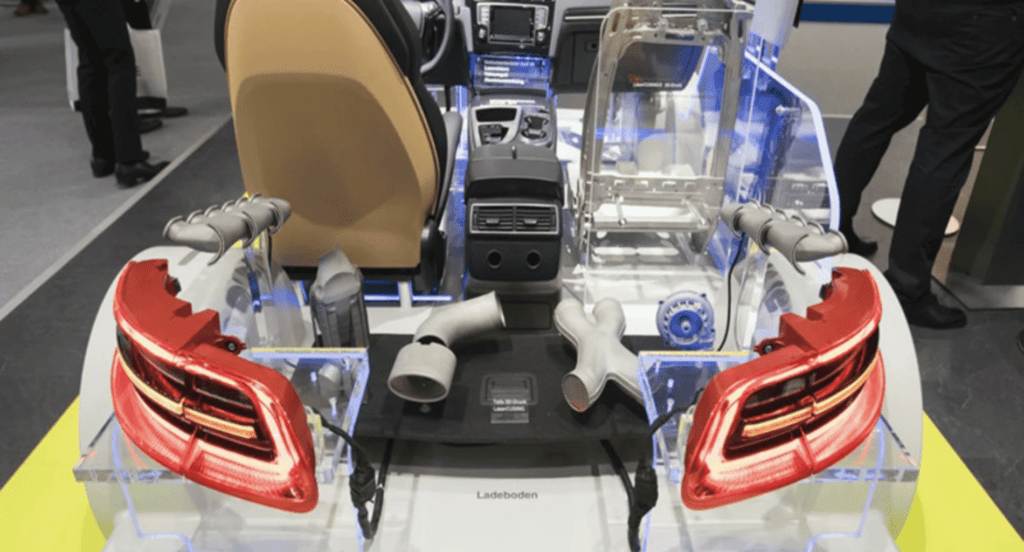
Aerospace Industry
Prototyping significantly affects aircraft and spacecraft reliability and performance, aligning with the projected 7.80% CAGR in the industry from 2023 to 2032 as per Precedence Research. It is utilized in components like airframe structures, engine parts, and interior cabin elements. These prototypes undergo rigorous testing for stress tolerance and environmental resilience to ensure safety in extreme conditions.
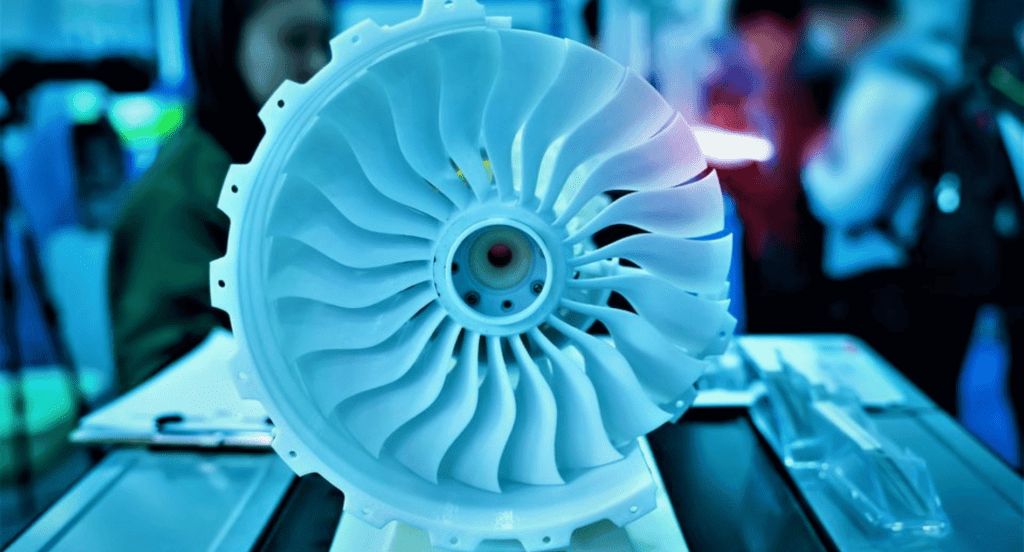
Consumer Electronics
In consumer electronics, prototyping is used to design and test components like metal casings, heat sinks, and structural supports. These prototypes help in assessing the durability of a product, how it handles heat, and its user-friendly design. This is critical for improving design elements that influence the product’s market appeal and functional efficiency.
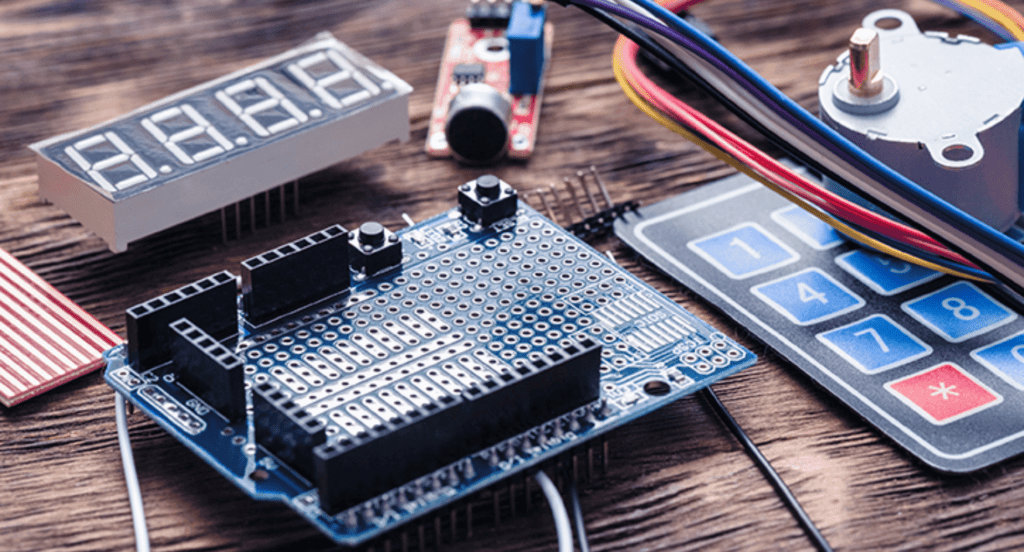
Medical Devices
Medical device prototyping involves creating surgical tools, implants, and diagnostic equipment components. These are tested for functionality, patient safety, and compliance with medical standards,to ensure that the devices perform reliably under various medical conditions and procedures. Zemetal excels in precision medical prototyping services, ensuring top-quality results.
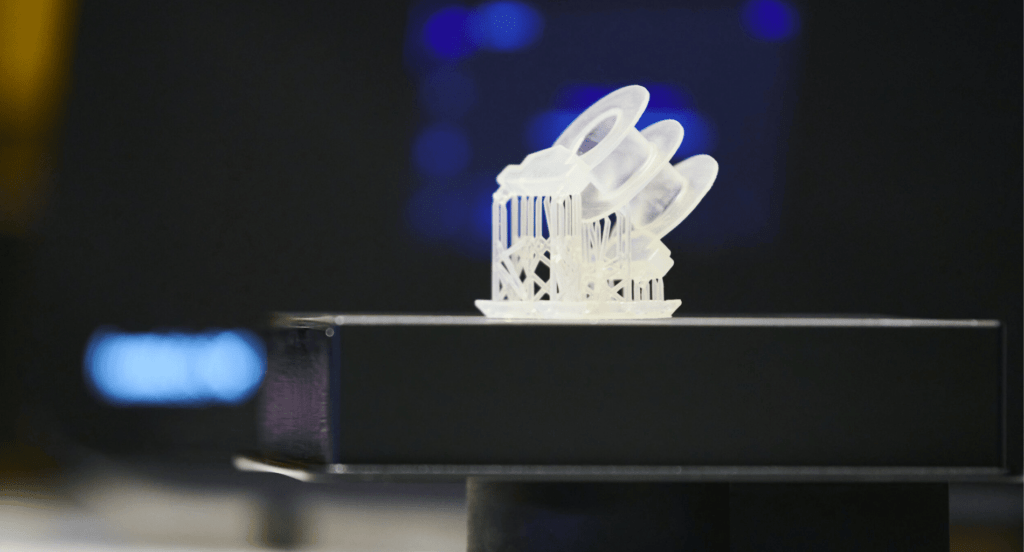
5. Quality Control and Testing in Prototyping
To ensure that the prototypes designed for various industries meet the highest standards of performance and reliability, meticulous quality control must be employed. Here are some of the key aspects:
Dimensional Accuracy Testing
This testing focuses on verifying that the prototype’s dimensions precisely match the design specifications. This involves using tools like calipers and coordinate measuring machines (CMM) to measure and ensure that each part of the prototype adheres to the set tolerances. Accurate dimensions are critical for the prototype’s functionality, especially when it must fit into an existing system or assembly.
Functional Testing
Functional testing involves putting the prototype through scenarios that mimic its intended use to evaluate its performance and reliability. This testing phase is designed to identify any operational issues or shortcomings, ensuring the prototype meets both the design intent and user requirements. It is vital in ensuring the prototype’s practical feasibility.
Surface Finish and Aesthetics Inspection
The prototype is thoroughly inspected to ensure it matches the design specifications. This involves examining the prototype for uniformity in color, texture, and overall surface treatment, using both visual inspection and tactile assessments. Meticulous attention is given to identify imperfections like scratches or dents, impacting product’s appearance and customer perception.
Compatibility Testing with Other Components
Testing for compatibility with other components or systems is essential, especially for prototypes meant to be part of larger assemblies. This includes assessing fit, alignment, and interaction with other parts, guaranteeing smooth integration in the intended operational environment. This testing is key to avoiding costly modifications in later stages of product development.
6. Challenges and Solutions in Prototype Fabrication
Moving beyond quality control, understanding the challenges and solutions in prototype fabrication is crucial for straightforward transition from concept to production. Here are some of the issues:
Adapting to Rapid Design Changes
Rapid changes in design specifications can be a significant issue in prototype fabrication, requiring quick adaptation and flexibility. The solution lies in implementing adaptable manufacturing processes and utilizing versatile fabrication equipment that can quickly adjust to new designs. This approach ensures that prototypes remain relevant and accurate despite frequent design updates.
The table below highlights the impact of rapid changes in design specifications on prototype fabrication and the solutions to mitigate these challenges through adaptable manufacturing processes.
Challenge | Solution |
Frequent design updates | Implementing adaptable manufacturing processes |
High costs due to constant redesign | Utilizing versatile fabrication equipment |
Delays in prototype development | Streamlining communication between design and production teams |
Compromised prototype accuracy | Integrating real-time design feedback mechanisms |
Increased waste and resource consumption | Adopting flexible and scalable production techniques |
Ensuring Prototype-to-Product Consistency
Maintaining consistency between the prototype and final product is a common challenge, as prototypes sometimes differ significantly from mass-produced items. To address this, it’s essential to use scalable processes and materials from the prototyping stage itself. This strategy ensures that the prototype accurately represents the final product, reducing differences in later stages.
Managing Intellectual Property Risks
Protecting intellectual property during the prototype fabrication process can be difficult, especially when external partners are involved. Implementing strict confidentiality agreements and secure data management practices are key solutions. These measures safeguard sensitive design information, ensuring that intellectual property remains protected.
Integrating Multi-Material Components
Integrating multiple materials into a single prototype can be complex, often leading to issues in assembly and functionality. The solution involves thorough material compatibility analysis and employing advanced assembly techniques like precision welding and adhesive bonding. This integrated approach ensures smooth incorporation of various materials into the prototype.
7. 4 Factors to Consider in Prototyping Sheet Metal
Bridging from challenges and solutions, considering factors in prototyping sheet metal is crucial to ensure the success and feasibility of the final product. Here are some critical considerations to remember:
#1 Technological Integration
Incorporating the latest technology in prototyping is crucial for precision, efficiency, and innovation. For example, advanced technologies like 3D printing and AI-driven design tools can significantly reduce time and cost while enhancing the prototype’s accuracy. Staying updated of technological advancements ensures that the prototyping process remains cutting-edge and competitive.
#2 Scalability
Scalability in prototyping is crucial to efficiently transform a successful prototype into large-scale production. It’s important to assess if the prototype’s design and manufacturing can scale up without acquiring significant costs or compromising quality for a smooth transition to market. Zemetal ensures scalability from prototypes to full-scale production, maintaining quality and efficiency.
#3 Material Innovation and Experimentation
Exploring new materials and experimenting with their combinations can lead to breakthroughs in prototype design and functionality. Innovating with materials can result in prototypes with enhanced properties like increased strength, reduced weight, or improved thermal resistance. This exploration is crucial for pushing the boundaries of what is possible in sheet metal fabrication.
#4 Cost-Benefit Analysis and Budget Management
Conducting a thorough cost-benefit analysis and effectively managing the budget are critical in prototype sheet metal fabrication. Balancing the prototype’s quality and features with the available resources ensures that the project remains financially feasible without compromising on vital aspects. Proper budget management is key to maintaining a sustainable development process from prototyping to production.
Conclusion
Prototype sheet metal fabrication is a vital process in transforming innovative designs into reality, showcasing the capabilities of modern manufacturing. This guide aims to simplify this complex process, providing clarity and insight into its role in product development for your business’s strategic growth.
For those seeking expert guidance and superior execution of prototype sheet metal fabrication, Zemetal is your go-to partner. Reach out to us to discover how our tailored solutions can transform your next project.
Dive Deeper Into Our Resources
Looking for more diverse service options? Browse through our handpicked selections:
Still haven’t found what you’re looking for? Don’t hesitate to contact us. We’re available around the clock to assist you.