Has anyone ever marveled at the sheer adaptability of sheet metal, seamlessly shaping the backbone of countless industries? In the metal industry, sheet metal fabrication reigns in the highest rank.
As a seasoned expert in the field with a wealth of experience catering to wide industrial needs, I bring insights beyond the ordinary.
Sheet metal for fabrication is a symphony of strength and versatility. Its qualities enable the creation of components that withstand the test of time and open doors to complex designs.
In this ultimate guide, we delve into the core complexities of sheet metal fabrication. Its techniques set industry standards, the ideas of selecting the right materials, and exploring innovative applications.
To discover the secrets, read on!
1. Overview of Sheet Metal Fabrication
Sheet metal fabrication is the art and science of transforming flat sheets of metal into a wide array of useful components and structures. This intricate process hinges on the material’s inherent properties of strength and malleability. Utilized across a spectrum of industries, it finds applications in aerospace, automotive, construction, and beyond.
At its core, sheet metal fabrication involves precision cutting, shaping, and assembly. The process commences with the selection of the appropriate metal, considering factors such as thickness and material type. Next, skilled craftsmen employ cutting-edge technology like laser or plasma cutters to carve out precise shapes. These components are then carefully bent, folded, or welded, following complex designs.’
2. Types of Sheet Metals Used in Fabrication
After the foundation of sheet metal fabrication, understanding the types of sheet metals available is important. Now, let’s explore the wide spectrum of choices and discover their respective strengths and applications:
- Carbon Steel: Renowned for its strength and affordability, carbon steel is a go-to choice for a multitude of applications. It’s widely used in manufacturing durable components like machinery parts and structural elements.
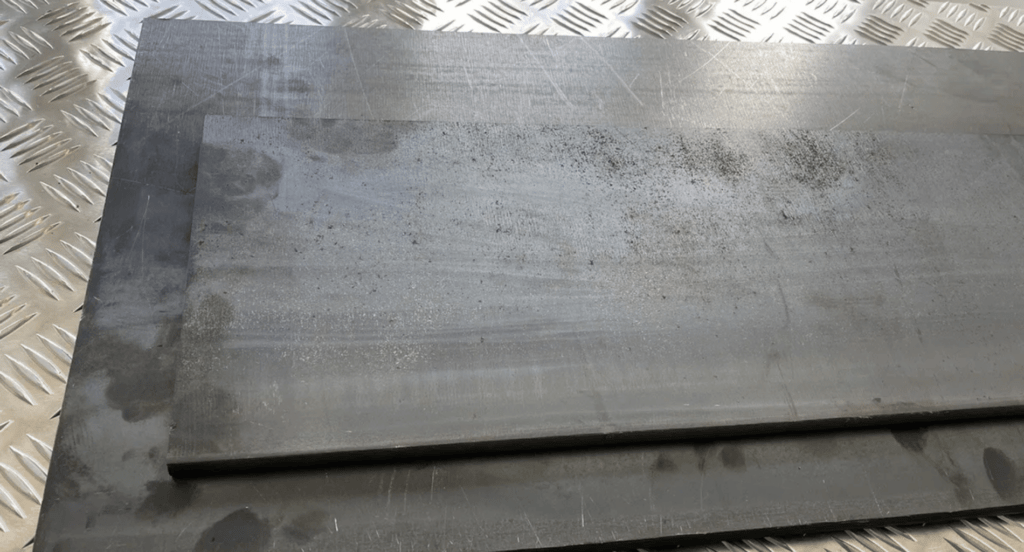
- Stainless Steel: Resistant to corrosion and staining, stainless steel is favored for its longevity. It finds a home in industries demanding hygiene and durability, such as food processing and medical equipment.
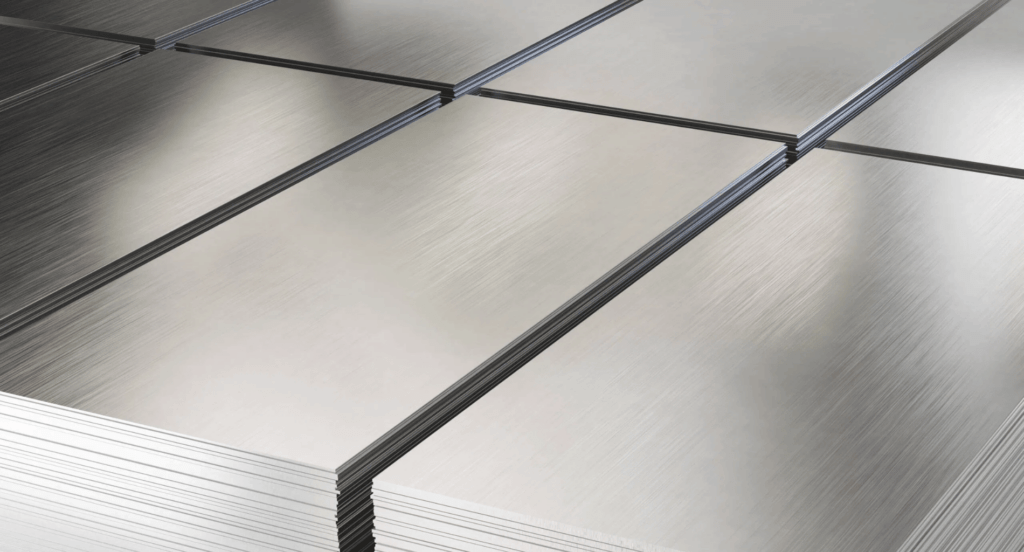
- Aluminum: Lightweight yet robust, aluminum is a preferred choice for aerospace and automotive applications. Its malleability enables complex designs, making it a versatile option.
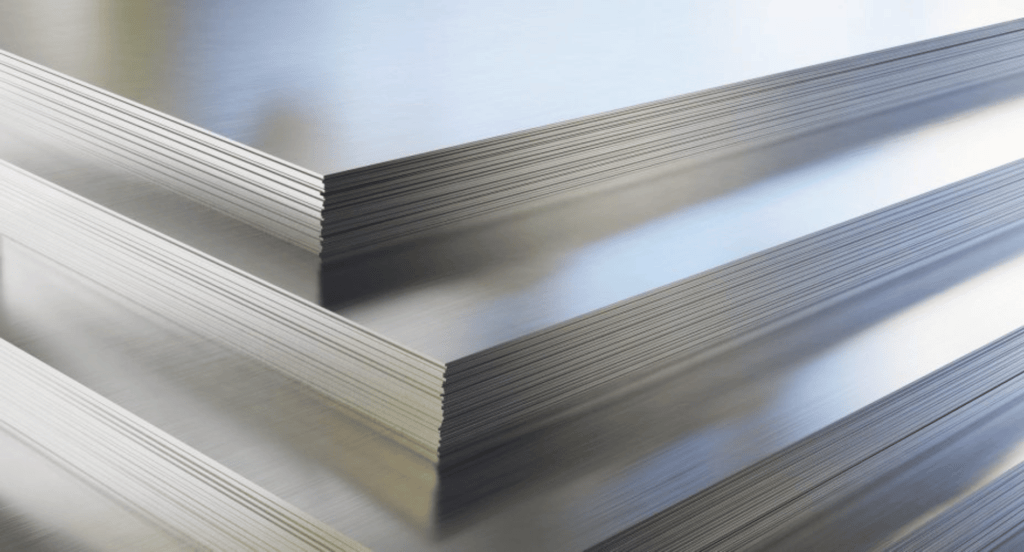
- Copper: Known for its excellent thermal and electrical conductivity, copper is indispensable in electrical wiring and heat exchangers, ensuring efficient energy transfer.
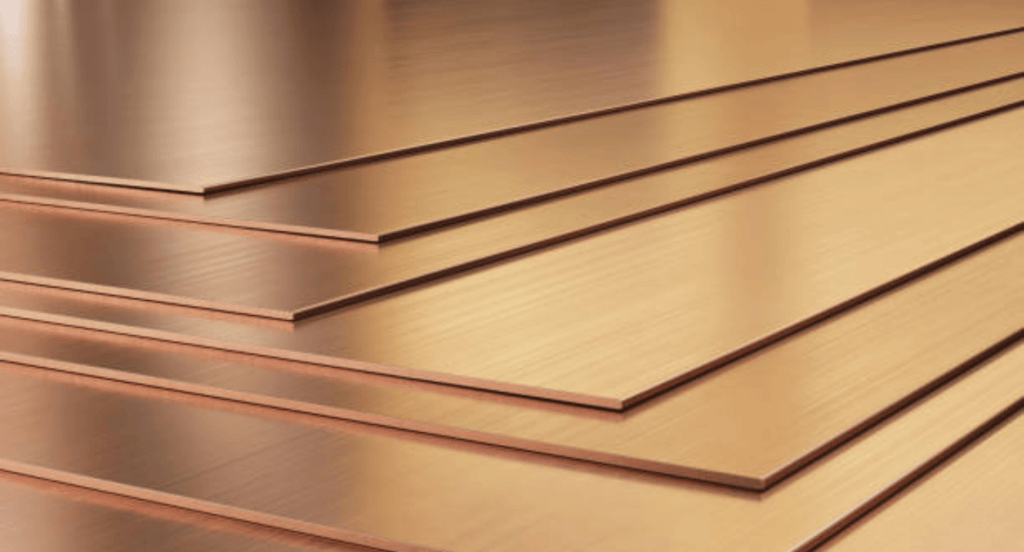
- Brass: Combining the properties of copper and zinc, brass boasts corrosion resistance and an attractive appearance. It’s ideal for decorative applications and marine hardware.
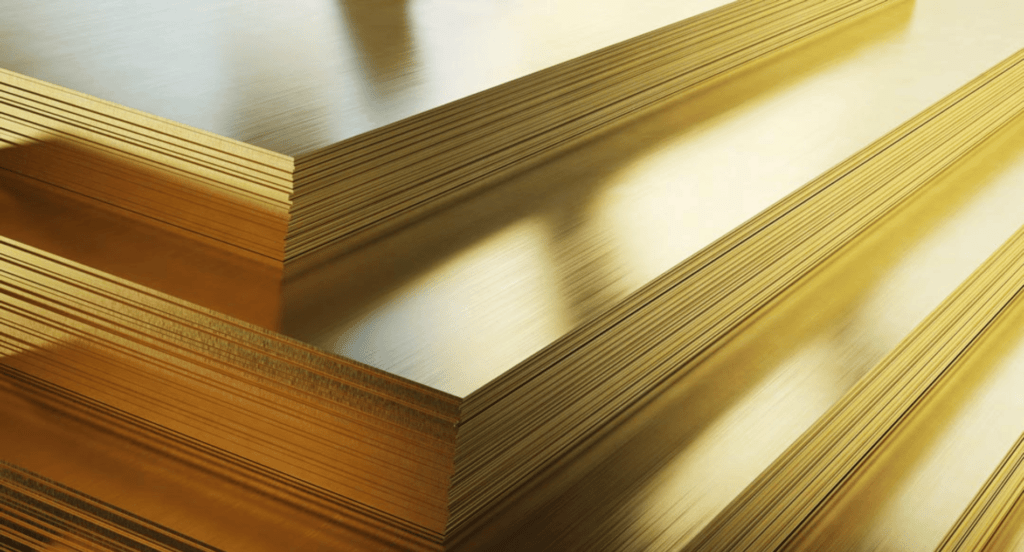
- Titanium: Known for its exceptional strength-to-weight ratio, titanium is utilized in aerospace, medical implants, and high-performance racing components due to its durability and corrosion resistance.
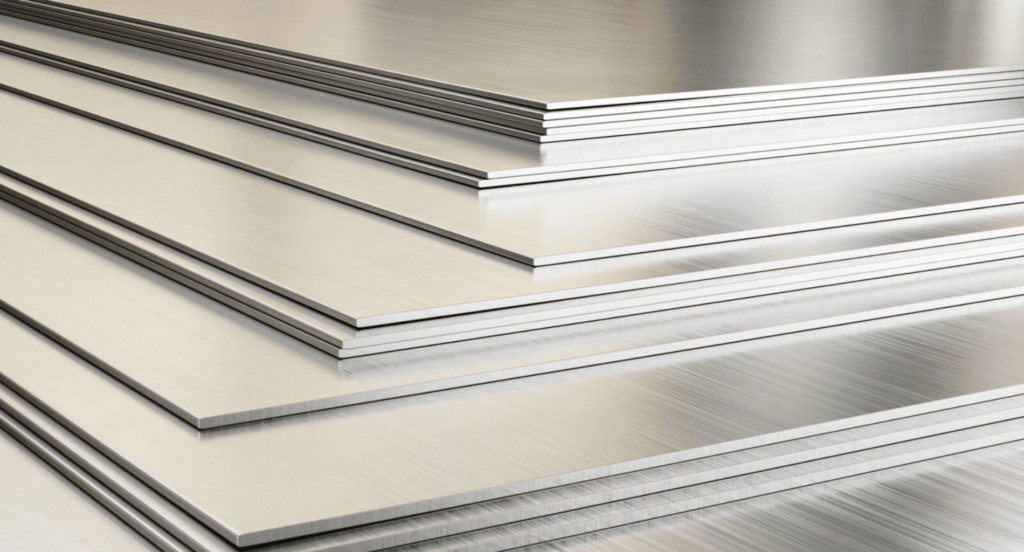
- Galvanized Steel: Enhanced with a protective zinc coating, galvanized steel resists rust and corrosion. It’s widely employed in outdoor structures and industrial equipment, enduring harsh environmental conditions.
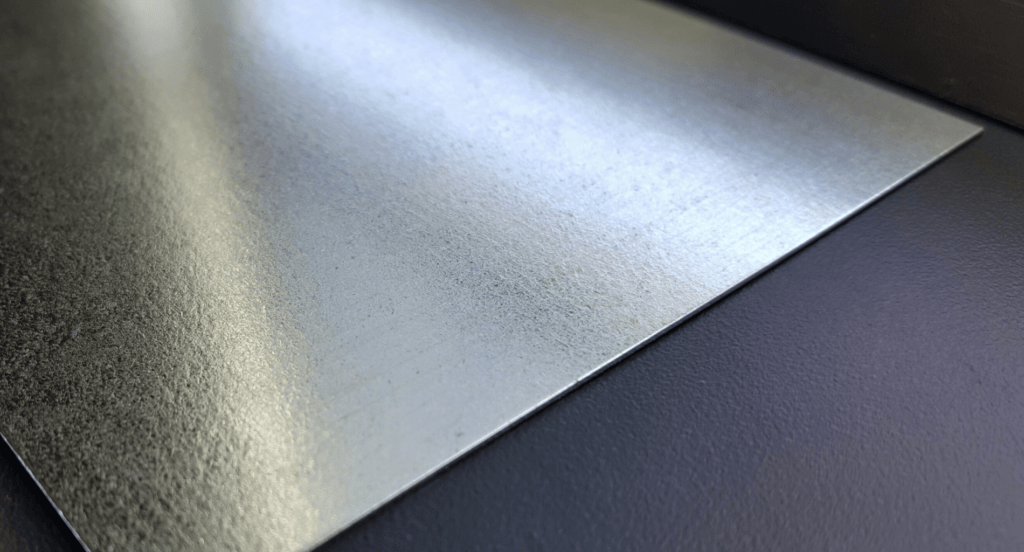
3. Sheet Metal Fabrication Techniques
Understanding the types of sheet metal available is crucial to making informed decisions in sheet metal fabrication. Now, let’s delve into the techniques that turn these materials into functional components:
Cutting and Shearing
The art of sheet metal fabrication often begins with precision cutting and shearing. Utilizing tools such as laser cutters, water jet cutters, or mechanical shears, sheets of metal are transformed into the desired shapes with perfect accuracy. For instance, laser cutting employs a high-energy laser beam to slice through metal, creating complex patterns and contours.
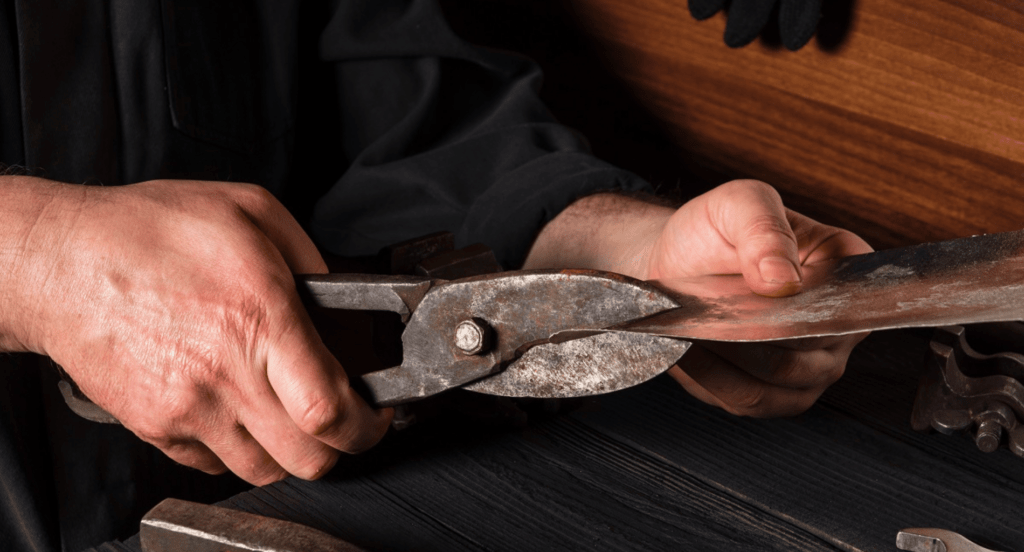
Bending and Forming
In the world of sheet metal fabrication, bending and forming techniques play an important role. Hydraulic press brakes and roll forming machines are used to bend and shape metal sheets with precision. This process is exemplified when crafting curved components for architectural designs, where sheets are carefully bent to create elegant, flowing forms.
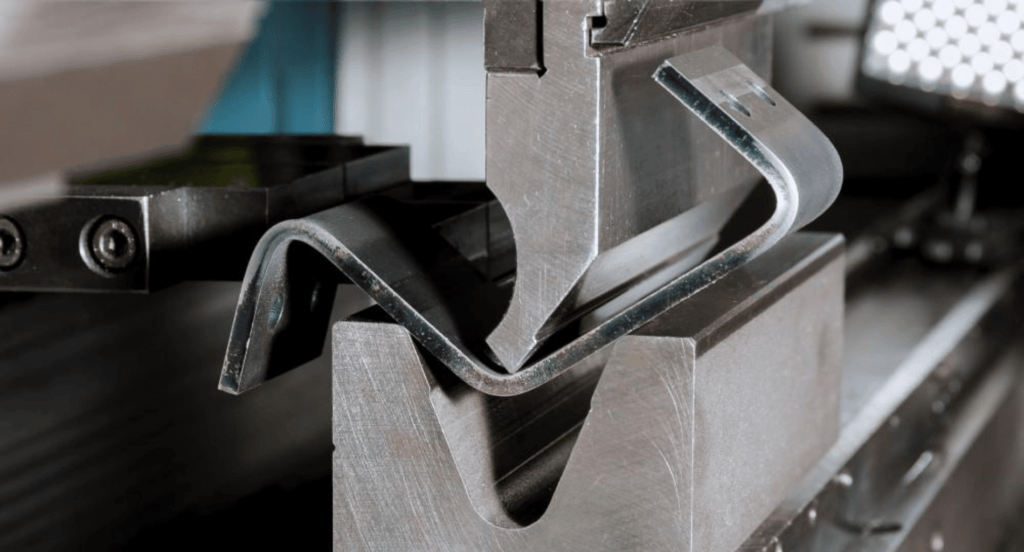
Welding and Joining
Welding and joining techniques fuse multiple metal pieces into cohesive structures. Various methods, such as MIG (Metal Inert Gas) and TIG (Tungsten Inert Gas) welding, offer distinct advantages depending on the material and application. For example, in MIG welding the most common Ar/CO2 mix is a 75/25 ratio, with 75% of it being argon and 25% of it being CO2 according to UNIMIG.
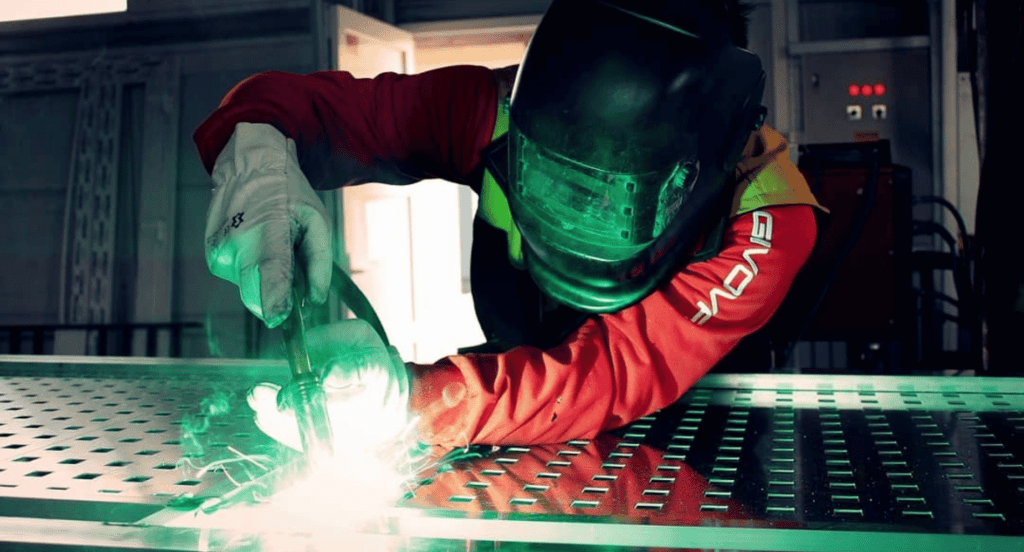
Assembly and Finishing
The final touches in sheet metal fabrication involve assembly and finishing. This includes fastening components together using techniques like riveting or using adhesives for specific applications. After assembly, finishes like powder coating or anodizing enhance both aesthetics and durability. For instance, powder coating provides a durable and visually appealing finish on sheet metal parts used in outdoor furniture.
4. Design Considerations in Sheet Metal Fabrication
Effective sheet metal fabrication techniques are essential, but it’s equally crucial to consider the design aspects. Let’s explore some considerations that play a role in achieving excellence in sheet metal fabrication:
Material Selection and Thickness
The choice of sheet metal material and its thickness is pivotal. Different materials exhibit distinct properties, influencing strength, corrosion resistance, and cost. The thickness of the sheet determines its structural integrity and suitability for specific applications. For example, in the automotive industry, selecting lightweight aluminum for body panels can enhance fuel efficiency without compromising safety.
Bend Radii and Tolerance
Precise bend radii and tolerances are critical design considerations. Understanding the limitations of sheet metal bending ensures that components can be formed accurately without defects. Designing with appropriate bend radii prevents cracking or weakening of the material during the bending process. This careful approach guarantees the reliability of the final product.
Assembly and Serviceability
Considering how components will be assembled and disassembled is essential, especially in industries where maintenance and repairs are routine. Designs that facilitate easy access to fasteners or components save time and reduce operational costs. Zemetal excels in providing design-for-assembly services, ensuring that complex sheet metal assemblies come together seamlessly.
Below is a table highlighting key aspects of Zemetal’s design-for-assembly services, focusing on the benefits of designing with maintenance and repair in mind.
Feature | Benefit | Application in Industry |
Modular Design | Simplifies assembly/disassembly | Aerospace, Automotive |
Accessible Fasteners | Reduces maintenance time | Manufacturing, Robotics |
Standardized Components | Lowers operational costs | Electronics, Machinery |
Intuitive Assembly | Minimizes assembly errors | Consumer Products, Healthcare |
Enhanced Durability | Extends product lifespan | Construction, Energy |
5. Applications of Sheet Metal in Different Industries
Design considerations are crucial, but equally important is recognizing the multitude of applications sheet metal serves in diverse industries. See the following sections to explore the breadth of its impact:
Aerospace and Aviation
Sheet metal plays an important role in the aerospace and aviation industry, where precision and reliability are paramount. From aircraft frames and engine components to interior fittings, sheet metal’s lightweight yet sturdy nature ensures safety and efficiency at high altitudes. For instance, aircraft engine nacelles are crafted from sheet metal to withstand extreme temperatures and turbulence.
Construction and Architecture
In the construction and architectural world, sheet metal finds its place in roofing, cladding, and decorative elements. Its ability to endure harsh weather conditions and provide design flexibility makes it a preferred choice. Architectural marvels often feature intricate sheet metal designs, such as ornate facades or functional roofing systems that blend aesthetics with durability.
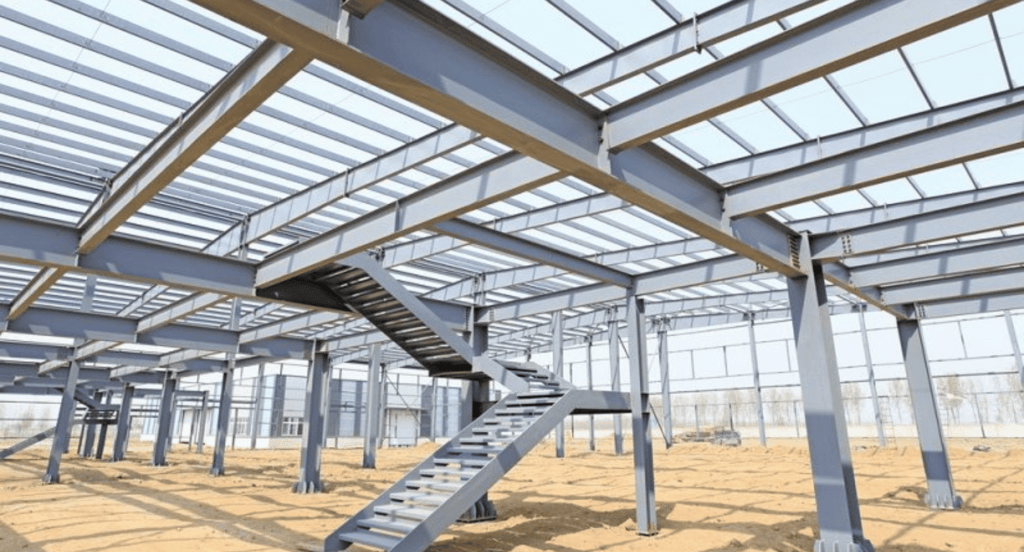
Automotive Engineering
The automotive industry relies heavily on sheet metal for vehicle bodies, chassis components, and various structural elements. The use of lightweight aluminum and high-strength steel ensures fuel efficiency without compromising safety. Sheet metal fabrication in this sector exemplifies precision engineering, where every component contributes to performance and safety.
Electronics and Technology
Sheet metal makes a big impact in the electronics and technology sector. It forms enclosures and chassis for countless electronic devices, ensuring electromagnetic shielding, structural integrity, and thermal management. Think of the sleek metal casing of your smartphone or the sturdy housing of a server rack – both made possible by sheet metal fabrication.
6. Quality Control in Sheet Metal Fabrication
Sheet metal applications span a multitude of industries. As we delve into quality control, we’ll see how maintaining high standards is essential for meeting the demands. Below are the key facets of quality control:
Material Inspection and Verification
Quality control begins with a strict inspection and verification of the sheet metal materials. This involves checking for material type, thickness, and dimensions to ensure they match the specifications of the project. Any discrepancies at this stage can lead to costly errors down the line. Zemetal offers material testing and verification of metals services, guaranteeing that the foundation of your project is solid.
Precision Machining and Tolerances
Maintaining precise machining and adherence to tolerances is a cornerstone of quality control. Advanced CNC (Computer Numerical Control) machinery ensures that cutting, bending, and forming processes meet the exact specifications required. Components with tight tolerances guarantee seamless assembly and optimal functionality.
Visual and Functional Inspection
Visual and functional inspections are the final checkpoints in quality control. Highly trained inspectors thoroughly examine the finished components for any defects, ensuring they meet the highest standards of aesthetics and functionality. This step ensures that the end product not only performs flawlessly but also meets visual expectations.
7. Common Challenges and Solutions in Sheet Metal Fabrication
Quality control forms the backbone of any sheet metal fabrication project, but challenges are inevitable. Listed are the challenges and solutions in sheet metal fabrication:
- Material Selection Dilemmas: Selecting the right material for a specific project can be challenging, as choosing the wrong material can lead to components lacking the required strength, durability, or corrosion resistance.
- Solutions: Thorough material analysis and expert consultation aid in selecting the most suitable materials based on project requirements.
- Complex Design Translations: Translating intricate designs into precise sheet metal components can be daunting, requiring a deep understanding of both design and fabrication processes.
- Solutions: Leveraging advanced CAD (Computer-Aided Design) software and employing skilled engineers help bridge the gap between complex designs and fabrication, ensuring the final product matches the intended specifications.
- Cost Management: Balancing high-quality materials and precision manufacturing with budget constraints poses a significant challenge in sheet metal fabrication.
- Solutions: Experienced sheet metal companies optimize manufacturing processes, minimize material wastage, and enhance operational efficiency to provide cost-effective solutions, ensuring projects remain within budget constraints.
8. 3 Tips for Choosing the Right Fabrication Partner
Knowing the common challenges and solutions in this area is crucial, but selecting the right fabrication partner is equally important. See the following tips to ensure you choose a partner that aligns with your objectives:
#1 Scalability and Capacity
Scalability and capacity are not just terms for the manufacturing floor but should also apply to the services offered by your fabrication partner. Consider whether your chosen partner can adapt and provide a range of services to meet the evolving needs of your business. An ideal partner offers a scalable service model that can handle projects of varying sizes.
#2 Customer Support and Collaboration
The level of customer support and collaboration offered by your fabrication partner should extend to their services. A partner who values open communication and collaboration in service delivery can better accommodate your project’s unique needs and changes. They should be responsive to all inquiries, provide regular updates on project progress, and actively involve the team in decision-making processes.
#3 Supply Chain Management
Efficient supply chain management is as critical in services as it is in manufacturing. Inquire about your partner’s ability to manage the service supply chain effectively. This includes ensuring a steady flow of materials, resources, and expertise needed to deliver services seamlessly. An experienced partner should have established relationships with reliable suppliers, subcontractors, and skilled professionals to avoid delays.
Conclusion
In summary, this comprehensive guide has unveiled the versatility and strength of sheet metal fabrication. Armed with this knowledge, businesses in need of sheet metal fabrication services can make informed decisions, ensuring the success of their projects.
To set on your sheet metal fabrication journey, discover the exceptional services and expertise offered by Zemetal. To explore how we can elevate your business, contact us today.
Dive Deeper Into Our Resources
Looking for more diverse service options? Browse through our handpicked selections:
For some insightful reads, we’ve curated a list of recommended articles just for you:
Still haven’t found what you’re looking for? Don’t hesitate to contact us. We’re available around the clock to assist you.