What is sheet metal stamping? It’s a manufacturing process that uses dies and presses to form, cut, or shape metal sheets into specific parts or designs with high precision.
As a Metal Fabricator, I often get asked about how sheet metal stamping can help produce consistent and durable components for various applications.
Don’t worry, the process is straightforward and can be applied to a wide range of materials.
In this guide, you will learn how sheet metal stamping works, the types of stamping techniques, and its applications in different industries. By understanding this process, you’ll see how it can improve efficiency and quality in your projects.
Let’s jump right in!
1. The Basics of Sheet Metal Stamping
Sheet metal stamping is a manufacturing process used to convert flat metal sheets into specific shapes. It involves placing the metal sheet between a die and a press tool, where the press shapes the metal into the desired form. This technique is highly efficient for producing large quantities of uniform metal parts. It’s fascinating to see how a simple sheet transforms into something so complex and functional.
The demand for sheet metal stamping is continuously growing. According to Grand View Research, the global metal stamping market size was estimated at USD 236.83 billion in 2023. It is projected to grow at a compound annual growth rate (CAGR) of 4.2% from 2024 to 2030. This growth indicates a robust future for businesses involved in metal stamping.
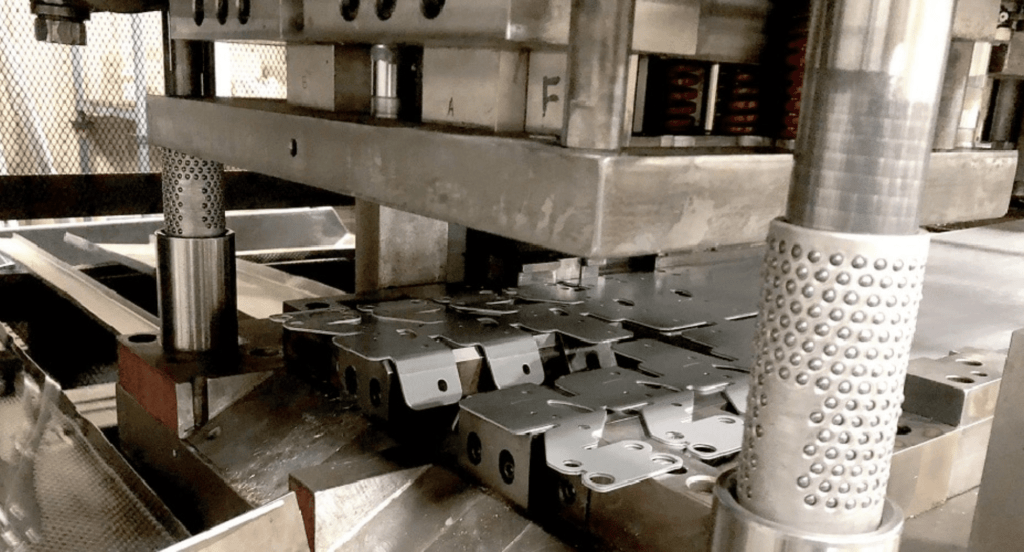
2. Types of Sheet Metal Stamping Operations
After understanding the basics of sheet metal stamping, it becomes clear that stamping operations can vary widely to suit different needs. Different stamping operations shape metal uniquely. Below are essential types to note:
Progressive Die Stamping
This method involves multiple stamping stations, each performing a different operation on the metal as it moves through the press. It’s like an assembly line for metal shaping. Progressive die stamping is ideal for high-volume production, ensuring consistency and efficiency in each piece. This process also minimizes material waste, making it a cost-effective choice for large orders.
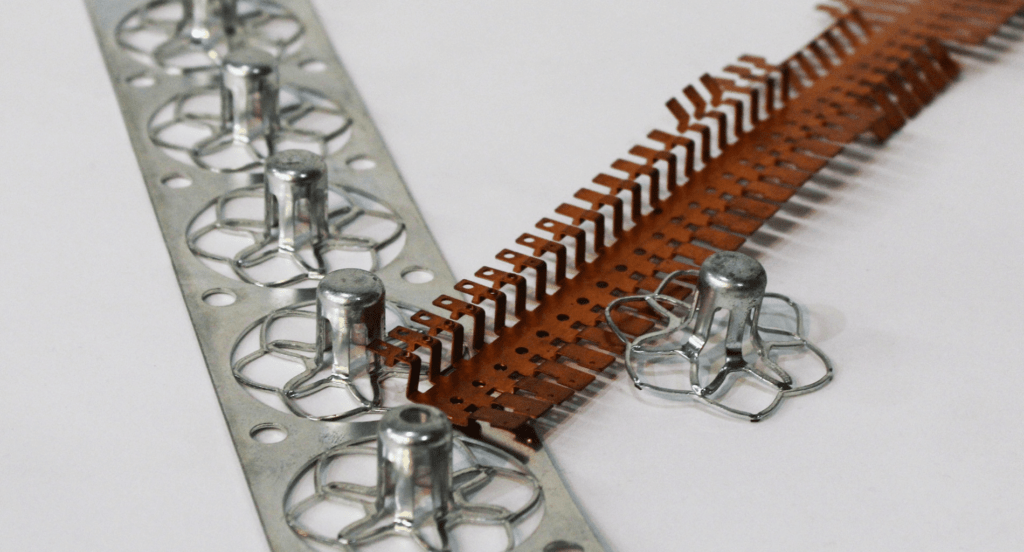
Deep Draw Stamping
Used for creating deep recesses in metal parts, this method stretches the metal into a desired shape, ideal for components like pots and sinks. Deep draw stamping is notable for its ability to produce seamless parts with high depth-to-diameter ratios. The remarkable transformation of a flat sheet into a deep, functional shape always amazes me.
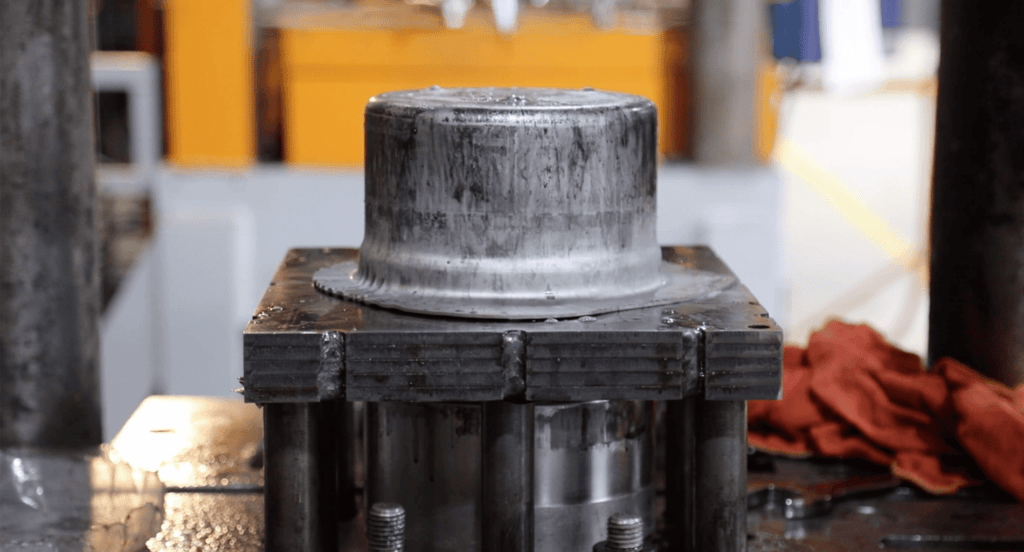
Four-Slide Stamping
A versatile process, four-slide stamping allows for complex bends and twists in metal parts. The precision and complexity achievable here are quite impressive. This method can produce smaller, intricate parts with multiple bends, perfect for custom or specialized hardware. Its adaptability makes it a go-to choice for detailed, complex designs.
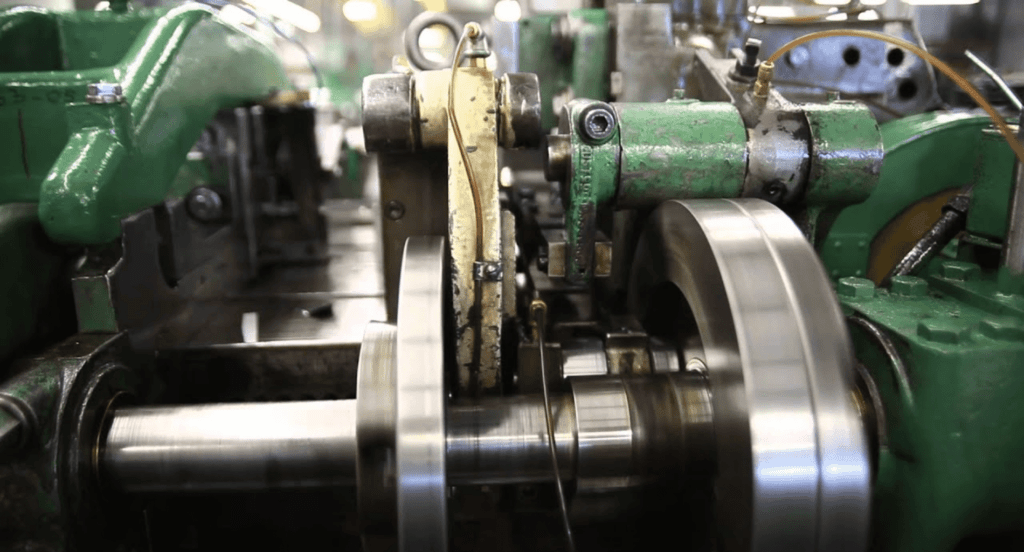
Compound Die Stamping
In this operation, a single stroke of the press produces a complete part. It’s a fast and cost-effective method for simple shapes. Compound die stamping is especially useful for parts that require high precision and repeatability, like electrical components. Zemetal’s expertise in compound die stamping ensures top-notch quality every time.
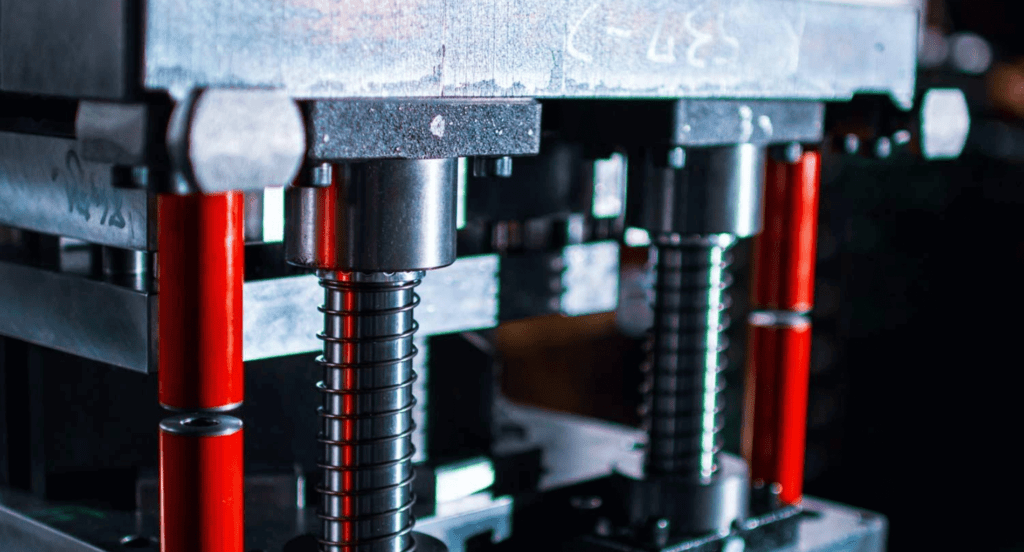
Transfer Die Stamping
Here, individual parts are transferred from one stamping station to another. This method is suited for larger parts that require multiple operations. Transfer die stamping excels in manufacturing complex parts with various shapes and sizes, often used in automotive manufacturing. It allows for more complex designs while maintaining high production rates.
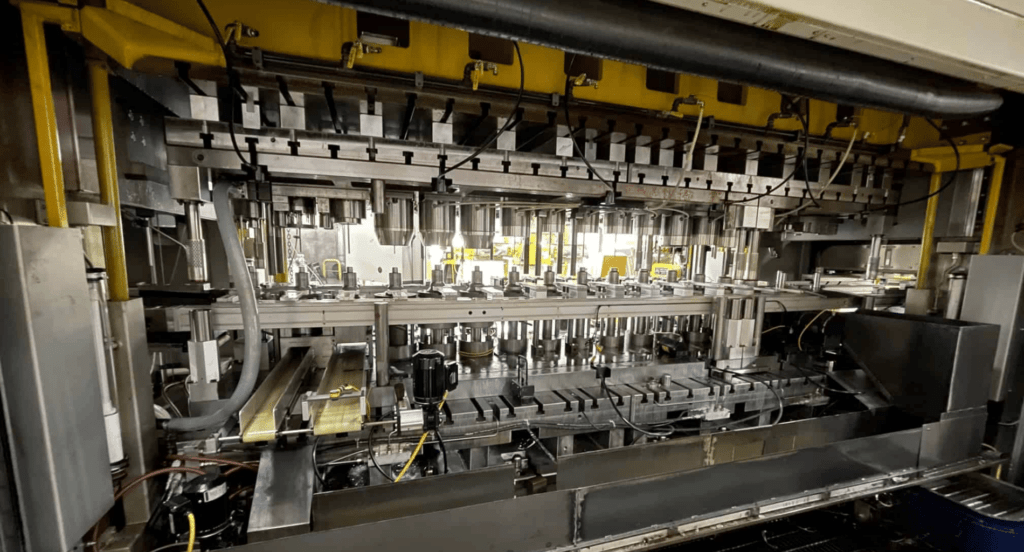
3. Key Equipment and Tools in Stamping
After exploring the types of stamping operations, it’s crucial to understand the equipment and tools that make these processes possible. Below are key equipment and tools essential in this industry:
Stamping Press
The heart of the operation, stamping presses apply the necessary force to shape the metal. These powerful machines are the backbone of every stamping project. They come in various types and sizes, tailored to different stamping needs, from single-stroke to progressive operations. Their versatility and power make them indispensable in our industry.
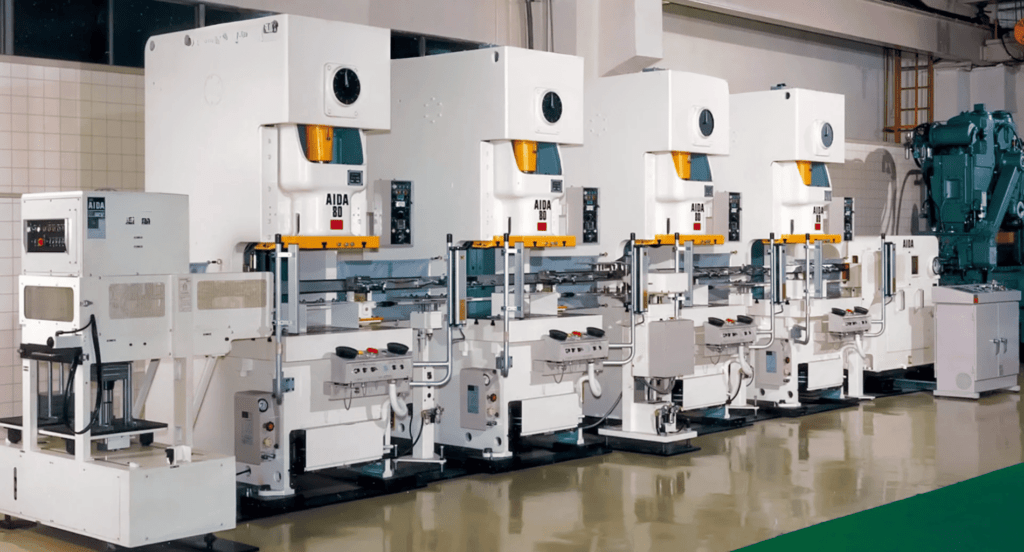
Dies
Custom-designed for each project, dies determine the shape and features of the stamped part. They are the molds that guide the metal into its new form. Precision in die design is critical, as it directly affects the quality and accuracy of the final product. The artistry and engineering in die design never cease to amaze me. Watching a piece perfectly take shape in the die is always satisfying.
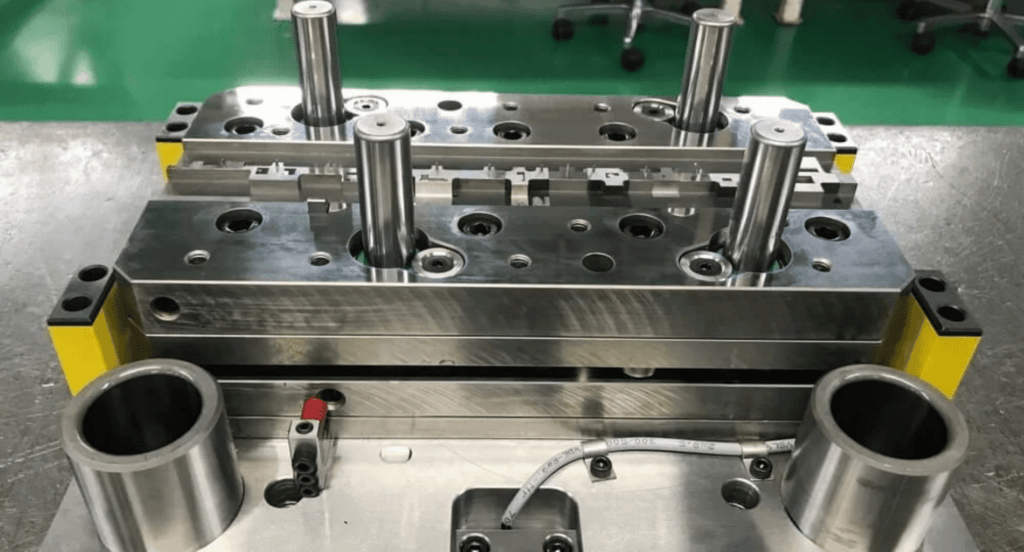
Feeders
These devices control the movement of metal sheets through the press, ensuring accurate positioning for each stamping action. Feeders can be mechanical or servo-driven, offering varying degrees of control and speed. They play a key role in maintaining efficiency and reducing material waste. Additionally, their integration with automated systems further enhances productivity and precision in the stamping process.
Coil Lines
Essential for handling rolled metal materials, coil lines unroll, straighten, and feed the metal into the press. They are crucial for maintaining a continuous production flow, especially in high-volume stamping operations. Coil lines ensure that metal is prepared correctly for stamping, free from defects and irregularities. They set the stage for a flawless stamping process.
Transfer Mechanisms
Used primarily in transfer die stamping, these systems move parts from one station to another within the press, crucial for complex operations. They provide the flexibility to handle parts with multiple stages of processing. Transfer mechanisms are designed for precision and coordination, ensuring each piece moves seamlessly through the press. Their orchestration of the stamping process is like a well-conducted symphony.
4. Advanced Techniques in Sheet Metal Stamping
After delving into the key equipment and tools, it’s important to explore the advanced techniques enhance precision and efficiency in sheet metal stamping that could blend technology with innovation. Below are key techniques transforming sheet metal stamping:
Microstamping
This technique is used for creating extremely small and detailed parts, often for electronics and medical devices. It’s amazing how technology enables us to stamp at such a tiny scale. Microstamping is crucial for applications where space is limited and precision is most important. The ability to produce such minute parts has opened up new possibilities in miniaturization.
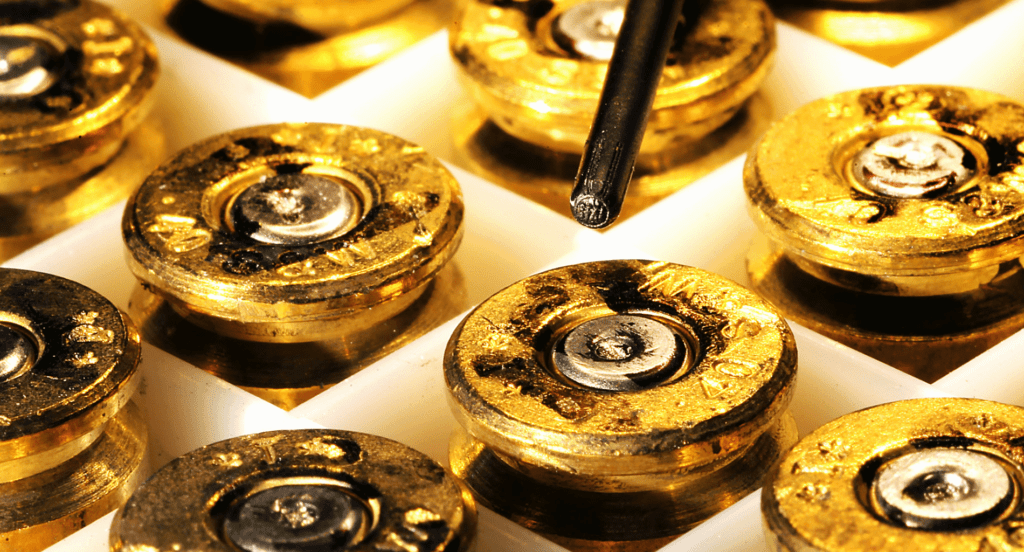
Laser Cutting Stamping
Combining traditional stamping with laser cutting allows for more intricate designs and tighter tolerances. This hybrid approach enhances the detailing capabilities of stamping, allowing for complex cuts that were previously impossible. It’s particularly useful for complex patterns and precise geometries, often required in decorative or high-precision components.
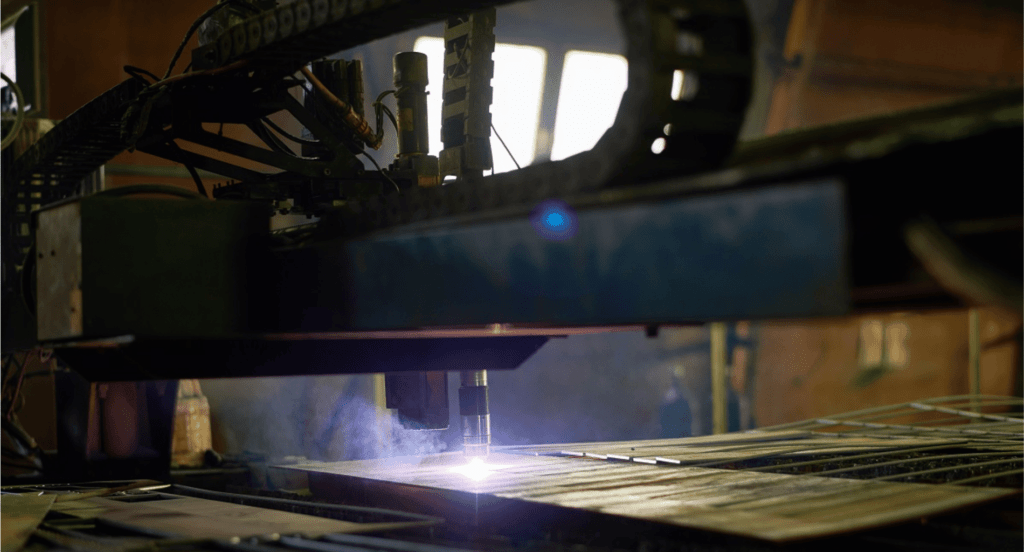
3D Stamping
This innovative approach enables the creation of three-dimensional shapes, offering more design flexibility compared to traditional flat stamping. 3D stamping can produce more complex geometries, increasing the potential applications for stamped parts. This method is a game-changer for industries looking to innovate in product design and functionality.
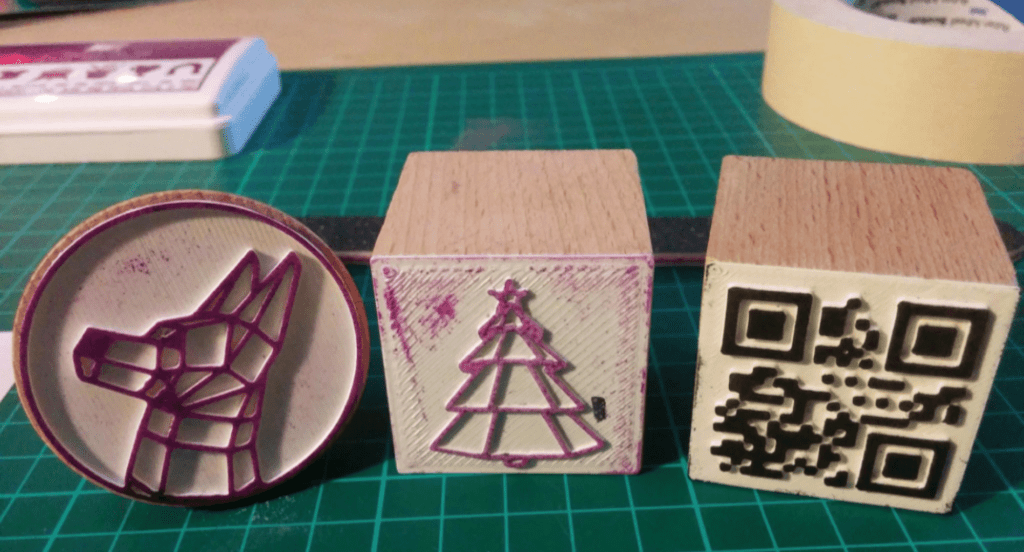
Automated Stamping
Using robotics and automation in stamping processes increases consistency, speed, and reduces labor costs. Automated systems also enhance safety, by reducing the need for manual handling in dangerous operations. The seamless integration of technology in stamping is a remarkable leap forward for the industry. This evolution in stamping is key for mass production, where uniformity and efficiency are critical.
Hydroforming
A specialized technique where high-pressure hydraulic fluid is used to shape metal, ideal for complex, lightweight parts, hydroforming allows for the creation of stronger, more rigid parts with fewer seams. For example, it’s used in manufacturing car chassis or aircraft fuselage panels, where its precision and strength are invaluable. It’s crucial for automotive and aerospace parts needing high strength-to-weight ratios.

5. Step-by-Step Guide to the Stamping Process
After exploring the advanced techniques, it’s essential to understand the fundamental steps involved in the stamping process. This guide outlines each stage from design to final product in the stamping process, crucial for those in metal fabrication:
Step#1 Design and Engineering
The process begins with creating a detailed design of the part, taking into consideration the metal’s properties and the intended use of the product. A solid design sets the foundation for success. This step involves collaboration between engineers and designers to ensure feasibility and efficiency in production. The design also dictates the type of stamping process to be used.
Step#2 Creating the Die
Based on the design, a die is custom-made. This die will shape the metal into the desired form. The die-making process requires precision engineering and skilled craftsmanship. It’s crucial that the die matches the design specifications exactly to ensure the final product meets all requirements. The die’s durability is also key, as it must withstand repeated use without degrading in quality.
Step#3 Material Selection and Preparation
Choosing the right metal and preparing it for stamping is crucial. This includes cutting the metal to size and ensuring its quality. The material’s thickness, strength, and flexibility must be appropriate for the intended product. Preparing the material may also involve cleaning and priming it for the stamping process. The correct preparation ensures the final product’s integrity and quality.
Step#4 Stamping
The prepared metal is then placed in the stamping press, where the die shapes it into the final part. This step involves applying the right amount of force and precision to ensure the metal conforms to the die’s shape. The stamping process can be repeated multiple times if the part requires several different shapes or features. Regular monitoring ensures each piece meets the required dimensions and tolerances.
Step#5 Finishing and Inspection
After stamping, the parts are finished, which may include deburring, painting, or plating, and then inspected for quality. The finishing process enhances the appearance and durability of the part. Seeing the final product emerge in perfect condition is always a moment of pride. Each piece undergoes careful inspection to ensure it meets all quality standards and specifications.
6. Applications of Sheet Metal Stamping
After the Step-by-Step Guide, it’s interesting to see how sheet metal stamping is applied in various industries. Sheet metal stamping is used across diverse applications, showcasing its versatility and significance. Below are some key applications:
Automotive Industry
Stamping is essential in manufacturing car bodies, engines, and various automotive parts. The cars we drive owe much to this technique. In the automotive industry, stamping ensures the production of high-strength, lightweight parts that contribute to vehicle safety and efficiency. This process also allows for the mass production of consistent, uniform parts, which is vital in the automotive sector.
Electronics
From small components like connectors to larger parts like computer framework, stamping is integral in electronics manufacturing. The precision of metal stamping enables the creation of complex, miniature parts necessary for modern electronic devices. It also allows for the rapid production of large quantities, keeping up with the fast-paced demand of the electronics market.
Aerospace
This sector relies on stamping for lightweight, durable components critical to aircraft performance. Aerospace stamping demands the highest standards of precision and quality, as these components often play a role in critical flight systems. The use of advanced metals and alloys in this field showcases the adaptability of stamping techniques to various materials.
Construction
Metal stamping produces parts used in building structures, from roofing materials to structural supports. It provides the construction industry with durable, cost-effective components essential for both residential and commercial buildings. Its role in creating robust and reliable infrastructure is truly foundational. It’s remarkable how stamping shapes the very buildings we live and work in.
7. Challenges and Solutions in Metal Stamping
After exploring the applications of sheet metal stamping, it’s important to understand the challenges faced in this field and how they can be overcome. Below are the key challenges and solutions in metal stamping:
Material Wrinklin
During stamping, materials often wrinkle due to uneven pressure. This is a challenge because it affects the quality of the final product. To solve this, using precision-engineered dies and optimizing the pressure distribution throughout the stamping process can significantly reduce wrinkling.
The table below outlines strategies to minimize material wrinkling during stamping:
Strategy | Description |
Precision-Engineered Dies | Utilize dies engineered with high precision to ensure uniform contact and pressure on the material. |
Pressure Distribution Optimization | Adjust the stamping press to apply pressure evenly across the material surface. |
Material Preparation | Pre-treat materials to enhance their formability and reduce susceptibility to wrinkling. |
Advanced Monitoring Systems | Implement real-time monitoring to adjust pressure distribution dynamically during the stamping process. |
Tooling Design Modification | Modify tooling designs to support material flow and reduce stress concentrations that lead to wrinkling. |
Tool Wear
Frequent use of stamping tools leads to wear and tear, impacting their efficiency and the quality of stamped parts. The challenge lies in maintaining consistent quality over time. Regular maintenance and using wear-resistant materials for tools can prolong their life and ensure consistent quality. Incorporating advanced coatings on tools can also significantly reduce wear.
Springback Effect
When metal is stamped, it tends to return slightly to its original shape, known as the springback effect. This makes achieving precise dimensions challenging. To address this, adjusting the design of the stamping tools to account for this natural tendency of the metal can result in more accurate final products. Employing computer simulations can help predict and compensate for the springback effect during the design phase.
High Production Costs
Metal stamping can be expensive due to the cost of materials and energy used. The challenge is to reduce these costs without compromising quality. Implementing efficient production techniques and using cost-effective materials where possible can help in reducing overall expenses. For instance, using recycled metals instead of new materials can significantly lower material costs while maintaining product quality.
8. 4 Tips When Considering Sheet Metal Stamping Services
After discussing the challenges and solutions in metal stamping, it’s essential to consider some practical tips when looking into sheet metal stamping services. Below are the useful tips when considering sheet metal stamping services:
#1 Research the Provider’s Reputation
Before choosing a stamping service, research their market reputation and track record. Ensure they have a history of delivering quality products and meeting deadlines. Look for customer reviews and case studies to get a real sense of their capabilities. Additionally, check if they have any industry certifications or awards, which can be a good indicator of their commitment to quality.
#2 Evaluate Material Quality
Check the quality of materials used by the stamping service. High-quality materials lead to better end products and reduce issues like wear and tear. Ask for specifics about the material grades and their sources. It’s also helpful to understand how they handle material testing and quality assurance processes. Zemetal offers detailed documentation on their material sourcing and testing protocols.
#3 Consider the Technology Used
Assess the technology and machinery used by the service provider. Advanced technology often results in higher precision and efficiency in the stamping process. Inquire about their latest machinery upgrades and how often they update their equipment. Also, find out if they utilize any innovative processes or software that sets them apart from competitors.
#4 Review Cost and Value
While cost is a significant factor, also consider the value you’re getting. Cheaper services might compromise on quality, so balance cost with the quality of services offered. Look into the details of what’s included in their pricing, like after-sales support and warranty. Affordable doesn’t always mean it’s the best choice, but it’s important to ensure you’re not paying extra for services you don’t need.
Conclusion
If you’ve been struggling with achieving high precision or efficiency in metal production, sheet metal stamping offers a reliable solution. It’s a process that saves time, reduces waste, and delivers consistent results. At Zemetal, we specialize in helping businesses streamline their production with expert sheet metal stamping services.
In conclusion, this guide has explained what sheet metal stamping is and how it can benefit your projects by improving production quality and speed. With this knowledge, you’re better equipped to leverage this technique for your needs. Contact us today to learn more about how Zemetal can support you with professional sheet metal stamping solutions.
Dive Deeper Into Our Resources
Looking for more diverse service options? Browse through our handpicked selections:
Still haven’t found what you’re looking for? Don’t hesitate to contact us. We’re available around the clock to assist you.