Is your project reaching its full potential? Discover how custom bent sheet metal is not just a component, but a driving force for innovation and efficiency in the industry.
As seasoned experts in metal fabrication, our insights and recommendations come from a place of deep industry knowledge and a commitment to quality.
Custom bent sheet metal is more than just a material; it’s a pivotal element in design and functionality. It brings visions to life by offering adaptability and strength, opening a world of possibilities for impactful projects.
In this guide, we’ll uncover the secrets behind custom bent sheet metal, detailing its materials, uses, and why it’s a critical component for any forward-thinking business in the industry.
Read on to unlock the full potential of custom bent sheet metal.
1. Understanding the Basics of Custom Bent Sheet Metal
Custom bent sheet metal is a pivotal element in modern construction and design, reshaping flat sheets into precise forms that fulfill specific design needs. This method involves a series of techniques, including cutting, bending, and assembling, to produce components that are both functional and visually striking. Accuracy is paramount, as minor errors can result in substantial complications.
Understanding these basics is essential for industry professionals, as it forms the foundation for more advanced techniques and new developments. Supporting the significance and growth of this sector, Technavio reports that the bending machine market is projected to grow by USD 1.83 billion from 2021 to 2026, indicating a robust and expanding market for custom bending solutions.
2. Materials and Tools for Custom Bending
Transitioning from the fundamental principles of custom bent sheet metal, it’s crucial to delve into the materials and tools that bring these concepts to life. Let’s explore the key elements that contribute to the art and science of custom bending:
- Metal Sheets: The foundation of custom bending. Common materials include aluminum, stainless steel, and copper, each offering unique properties like corrosion resistance or flexibility.
- Bending Brakes: Tools crucial for making precise bends. Depending on the project’s complexity, these can range from simple manual brakes to sophisticated CNC machines.
- Rollers: Essential for creating curves and circular shapes in metal sheets. The size and type of roller will depend on the thickness and material of the metal.
- Measuring Tools: Accuracy is paramount in custom bending. Tools like protractors, calipers, and angle finders ensure that each bend meets the exact specifications.
- Cutting Tools: From shears to laser cutters, these tools are used to cut metal sheets into the desired size before bending. Having seen these tools in action, it’s impressive how they handle metal with such precision and ease.
3. Techniques in Bending Sheet Metal
Diving deeper into the world of custom bent sheet metal, it’s essential to understand the techniques that shape this versatile material. Here are some of the primary methods used in the industry:
Rotary Bending
Rotary bending is a versatile technique where the sheet metal is shaped around a rotating form or die. This method is known for its gentle handling of the material, minimizing scratches or deformities. It’s fascinating how this method can create precise bends while preserving the metal’s integrity.
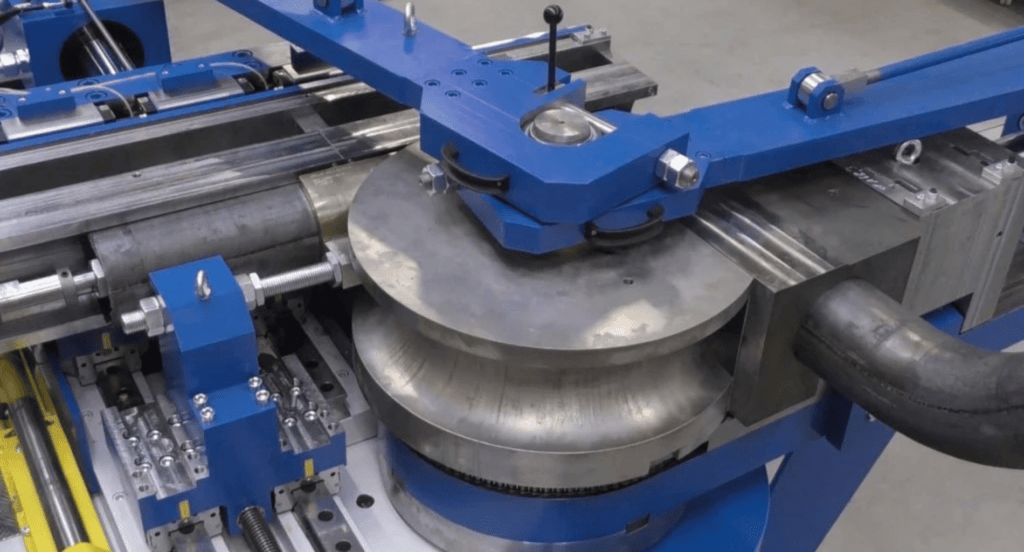
Coining
Coining is a process where the metal sheet is firmly pressed between a punch and a die, creating a lasting bend. This approach ensures that each angle is crisply defined and exact. It’s particularly adept at delivering consistent and dependable bends, reflecting a commitment to high-quality output. For example, in automotive parts, coining results in sharp, clean lines essential for both aesthetics and function.
Three-Point Bending
Three-point bending is a method where the metal is bent over three points of contact, providing excellent control over the angle and radius of the bend. This technique is particularly useful for creating consistent and precise bends across different materials. Witnessing the transformation from a flat sheet to a perfectly contoured piece is a clear demonstration of this technique’s precision.
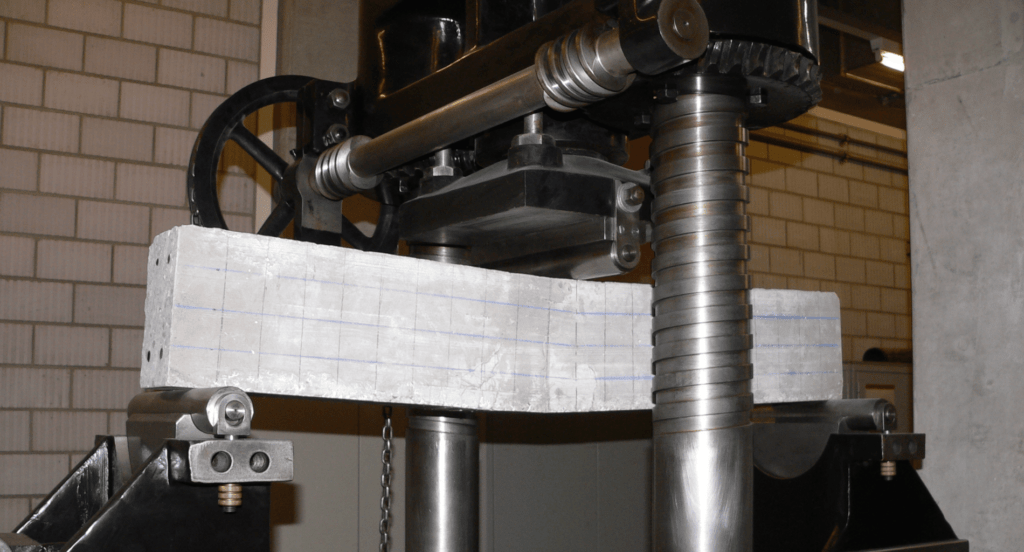
4. Design Considerations for Custom Bending
Navigating the detailed of custom bending requires a keen understanding of the design aspects that influence the process and outcome. Here’s a deeper dive into some critical considerations:
Material Selection
Choosing the right material is vital for successful custom bending. Factors like thickness, type of metal, and intended use all influence the bending process and final outcome. For example, thinner materials might be more pliable but could require more delicate handling to prevent damage.
Compatibility with Other Components
In custom bending, ensuring that each bent component seamlessly integrates with other parts is crucial. This is particularly important in complex assemblies like automotive engines or aircraft fuselages, where every curve and angle must align perfectly to maintain functionality and safety. Precision in this aspect ensures the overall integrity and performance of the final product.
The following table highlights key aspects of custom bending, emphasizing the importance of precision in integrating components for complex assemblies such as automotive engines or aircraft fuselages.
Aspect | Importance |
Material Compatibility | Ensures materials can be bent without compromising their structural integrity or causing defects. |
Bend Angle Accuracy | Critical for the components to fit together seamlessly, maintaining the assembly’s functionality. |
Tolerance Adherence | Minimizes the risk of misalignment in parts, ensuring safety and performance. |
Surface Finish Quality | Affects the assembly’s aesthetics and can influence the friction between moving parts. |
Dimensional Consistency | Guarantees that each component will fit precisely with others, regardless of production batch. |
Bend Radius
The bend radius is a critical aspect that impacts both the look and structural integrity of the piece. Too sharp a bend for a given material can lead to cracking or weakening. It’s always a balance between the desired aesthetic and the physical limits of the material.
5. Custom Bending for Different Industries
Understanding the design considerations for custom bending provides a foundation for appreciating its varied applications across industries. Now, let’s explore the specific ways different sectors utilize this versatile technique to meet their unique needs and challenges:
Energy Industry
For the energy sector, particularly in wind and solar installations, custom bending is vital. Components like turbine blades and solar panel frames demand precise curvature to maximize efficiency. Zemetal’s expertise ensures that each bend contributes to the optimal performance of these renewable energy sources, reflecting a commitment to both innovation and sustainability.
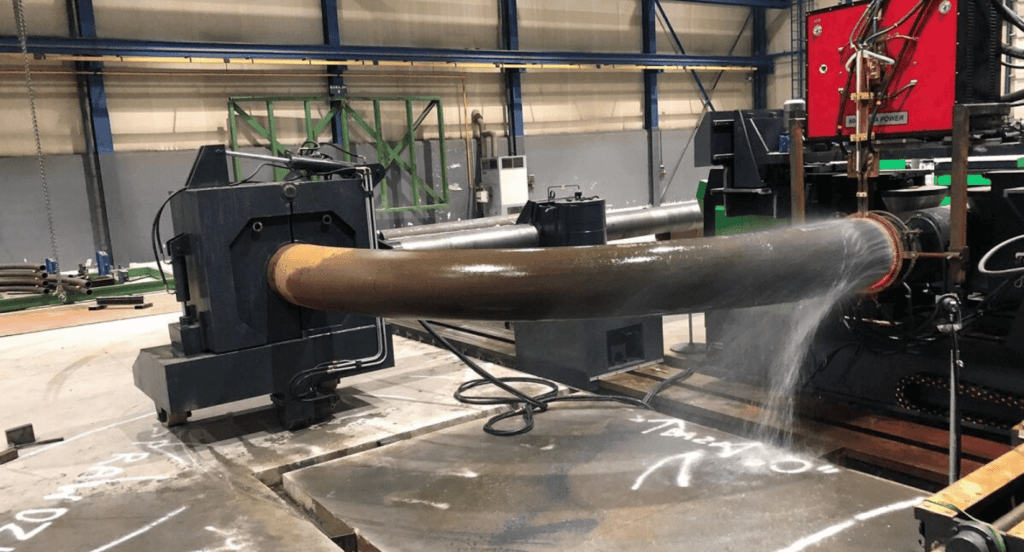
Marine Industry
The marine industry relies on custom bending for everything from the structural components of vessels to intricate onboard fixtures. The bends must not only be aesthetically pleasing but also able to withstand harsh marine environments. Precision in custom bending ensures the durability and performance of these components, crucial for safety and functionality at sea.
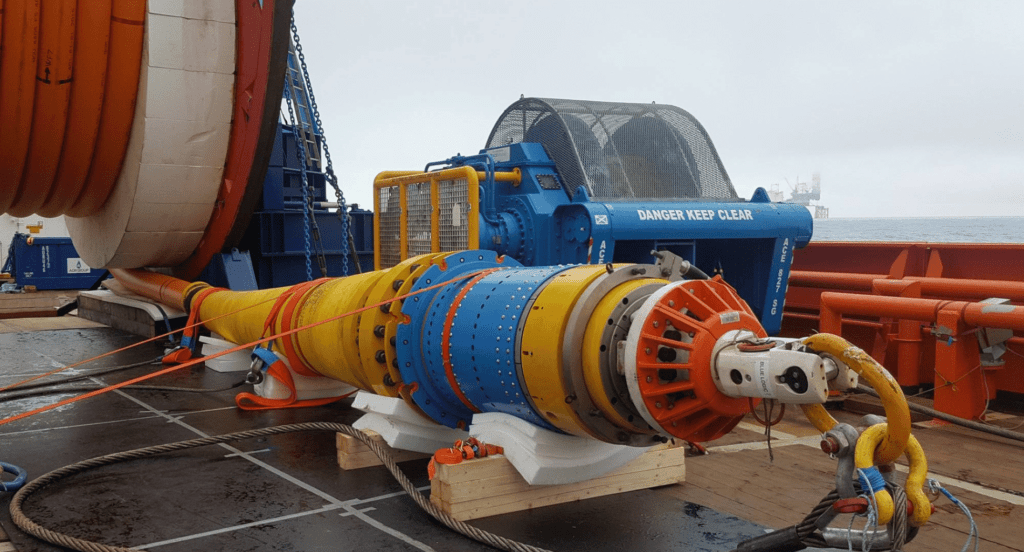
Medical Industry
In the realm of medical equipment manufacturing, custom bending is essential for creating components of advanced diagnostic machines and surgical tools. Precision bends are vital for the intricate parts of MRI machines and compact, ergonomic designs of handheld surgical instruments. The exactness ensures functionality and safety, a non-negotiable in the medical field.
6. Challenges and Solutions in Custom Bending
Custom bending is a field where precision meets creativity, with each project presenting its own set of unique challenges and opportunities for innovation. Here are some insights into common issues faced in this detailed process and the practical solutions that industry professionals employ:
Maintaining Material Integrity During Bending
The primary challenge in custom bending is ensuring the material maintains its integrity. During the bending process, metals are subjected to stress, which can lead to warping or cracking, especially in materials that are not suited for extensive bending. To mitigate this, it’s crucial to select the appropriate material and pre-treatment methods. Choosing flexible, strong metals and employing heat treatments reduces damage risks.
Balancing Aesthetics with Structural Requirements
In custom bending, the challenge often lies in creating pieces that look good while being strong enough to serve their purpose. This balance is tricky, especially when the designs are complex and the expectations are high. To address this, professionals use advanced design software to simulate both the appearance and performance of the bend. This enables pre-bending tweaks, ensuring the end product is attractive and sturdy.
Adapting to Varied Material Thickness and Types
One of the main challenges in custom bending is dealing with different material types and thicknesses.Each material reacts uniquely to stress, with varying thicknesses needing distinct bending forces and methods, challenging consistency and accuracy. The solution lies in detailed planning and advanced technology, using precise calculations and CAD software to predict material responses in bending.
7. 3 Factors to Consider in Custom Sheet Metal Bending
Having explored the challenges and solutions in custom bending, it’s clear that success hinges on several critical factors. Understanding these elements is key to achieving the desired results in any project. Let’s dive into what professionals need to consider when embarking on custom sheet metal bending:
#1 Bending Methods
Choosing the right bending method is crucial and depends on the project specifics. Zemetal offers various techniques tailored to different needs, ensuring precision and quality. Whether it’s air bending for flexibility or coining for sharp, repeatable bends, selecting the appropriate method is a decision that profoundly affects the final product.
#2 End-Use Application
The intended use of the bent metal piece plays a significant role in the bending process. Factors like environmental exposure, load-bearing requirements, and aesthetic considerations all influence decisions about materials, bending techniques, and finishing processes. Understanding the end-use is essential for delivering a product that not only looks good but performs well over time.
#3 Finishing and Post-Processing
After bending, the finishing and post-processing steps can significantly affect the appearance and performance of the metal piece. Factors like painting, coating, or additional machining must be considered to ensure the final product meets all aesthetic and functional requirements. These finishing touches are what make the piece suitable for its intended application and environment.
Conclusion
This guide has provided a comprehensive look into the precise and demanding world of custom sheet metal bending, equipping you with the knowledge to tackle your projects with confidence. The journey from concept to creation is now clearer and more attainable.
Step forward with Zemetal as your trusted partner. Harness our expertise and cutting-edge technology to bring your visions to life. For any questions or to begin crafting your project, contact us today to learn more.
Dive Deeper Into Our Resources
Looking for more diverse service options? Browse through our handpicked selections:
For some insightful reads, we’ve curated a list of recommended articles just for you:
Sheet Metal Fabrication Processes​
Still haven’t found what you’re looking for? Don’t hesitate to contact us. We’re available around the clock to assist you.