Anodising Services
Dive into our selection of top-tier metal services, where unparalleled quality meets innovative design. Each item in our range is a testament to our commitment to excellence in metal fabrication.
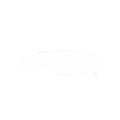
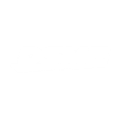
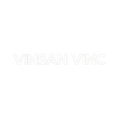
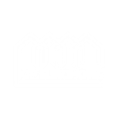
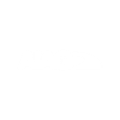
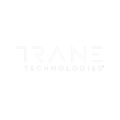
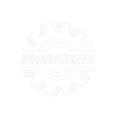
Explore Our Premium Metal Fabrication Range
Seeking top-tier anodizing services that elevate the durability and aesthetics of metal products? In the right place, indeed.
Â
Zemetal, a standout leader in the realm of anodizing finish and anodized sheet metal.The mission here is to deliver unparalleled quality in the metal fabrication industry. We taks pride in its cutting-edge techniques and unwavering commitment to excellence.
Â
Tailored to meet the needs of businesses in the metal fabrication sector, including wholesalers, distributors, and small business owners, our services are crafted to support and enhance operational efficiency.
Â
Trust in our exceptional anodizing services as a reliable partner for business advancement.
Zemetal: Who We Are
Our Founding Journey
Established with a vision to revolutionize the sheet metal processing industry, our journey reflects a blend of innovation, precision, and dedication. From our humble beginnings, we’ve evolved into a leader in sheet metal processing and batch production. Our success is built on a commitment to quality and relentless technological advancement, setting new standards in the industry.
Inside Our Facility
Step into our state-of-the-art factory, where advanced technology meets skilled craftsmanship. Optimally designed for efficiency, our facility is the heart of our sheet metal production. We handle intricate designs and large-scale outputs with precision, ensuring every product meets the highest quality benchmarks. Our factory is a testament to our capability to handle diverse, high-volume demands with precision.
Innovation & Development
At the core of our operation is a robust Research & Development wing, pushing the frontiers of sheet metal processing. Our R&D team, equipped with cutting-edge tools and driven by innovation, continually develops new methods to enhance efficiency and product quality. This relentless pursuit of improvement sets us apart and ensures we stay ahead in a rapidly evolving industry.
Certification Excellence
Our commitment to excellence is affirmed by our comprehensive range of industry certifications. Each certificate represents our adherence to stringent quality standards, environmental practices, and safety protocols. These certifications are a promise to our clients that every sheet metal product we deliver is crafted to perfection, adhering to the highest industry benchmarks. Trust and quality are the pillars of our service.
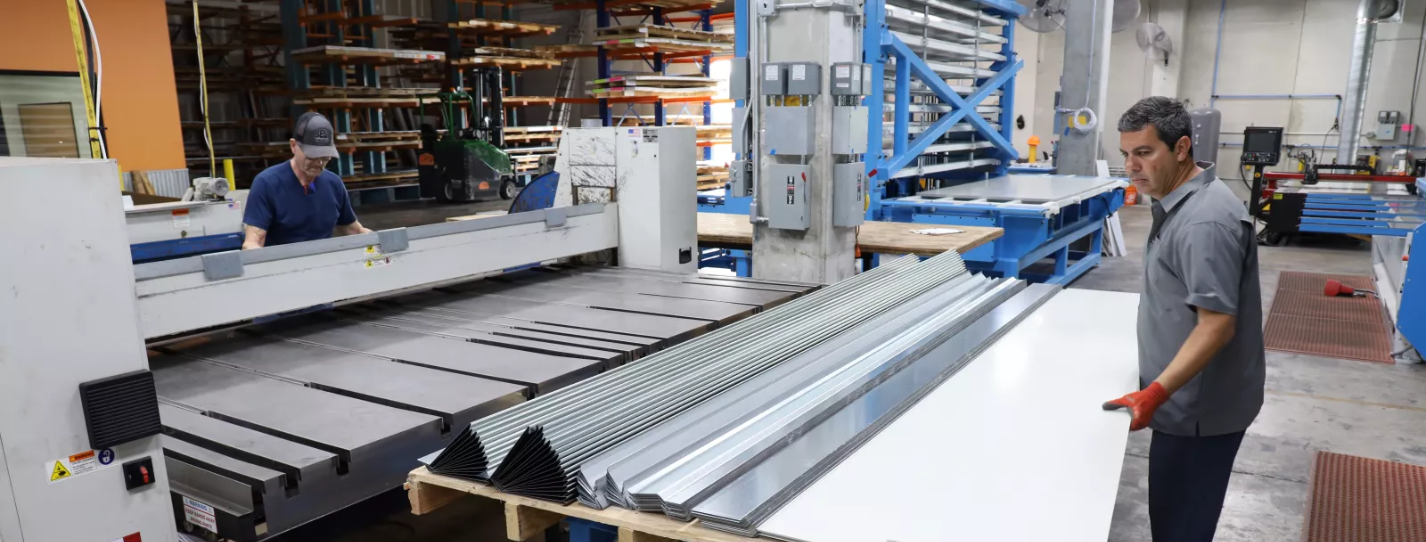
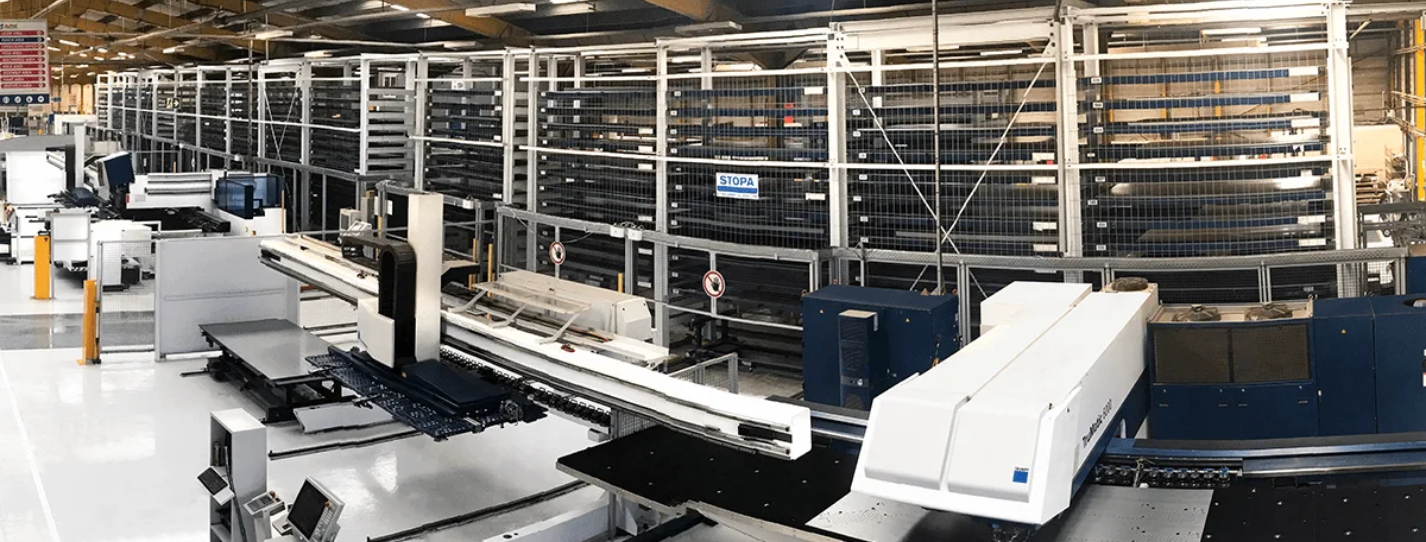
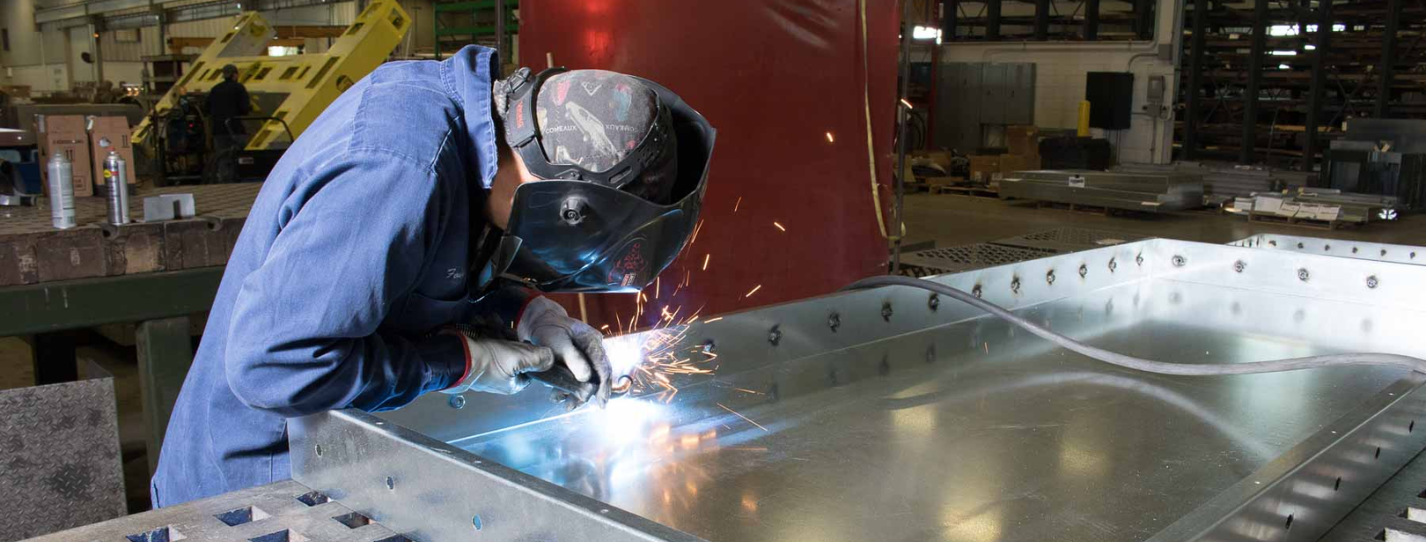
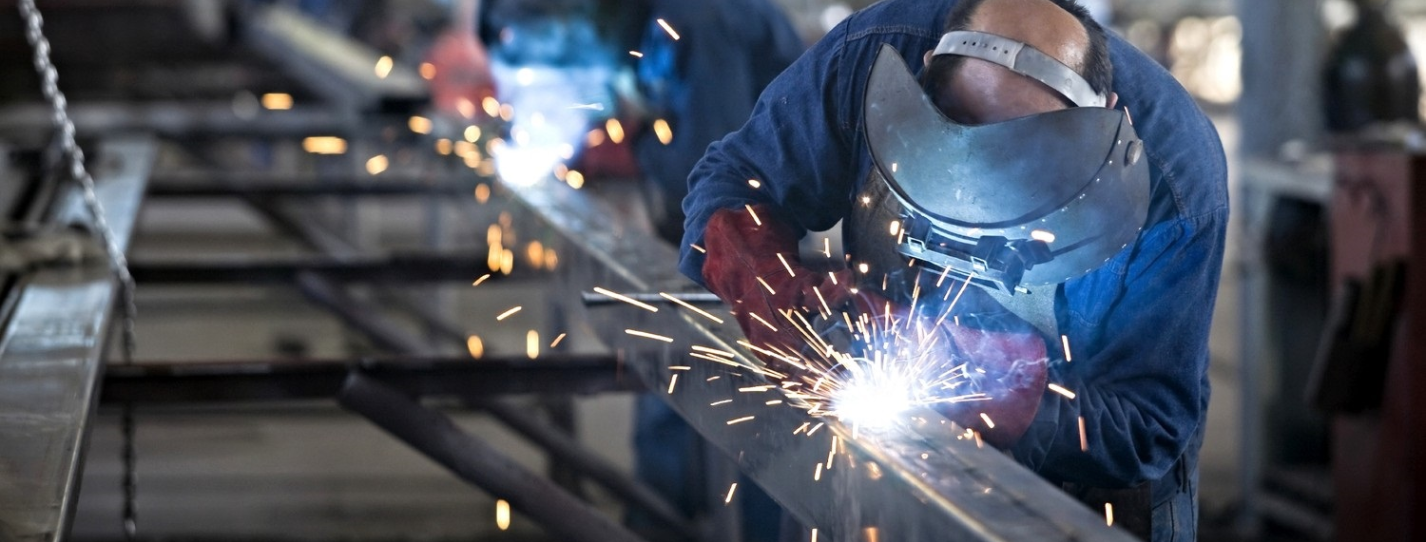
Meet the Experts Behind Zemetal
01
Media Team
For content collaborations or to join our blog contributors, please contact [email protected]. We welcome fresh perspectives and are committed to enriching our metal sheet fabrication industry platform with diverse insights. Let’s innovate together.
02
Quality Assurance Team
In our Quality Assurance Team, we meticulously ensure a 99.8% precision rate in every project, embodying our dedication to superior quality and a zero-error approach in metal sheet fabrication.
03
Research & Development Team
Leading with over 30 innovative techniques, our R&D Team enhances fabrication efficiency and precision by 25%, constantly redefining creativity and scientific accuracy in metal sheet fabrication.
04
Engineering & Design Team
Our Engineering & Design Team, with over 500 bespoke projects, expertly fuses creative design with engineering precision, ensuring each fabrication project excels in functionality and aesthetics.
Empowering Goals With Us
At Zemetal, our partnership with a pioneering electric vehicle firm is a testament to our dedication to precision, sustainability, and efficiency. Utilizing our cutting-edge fabrication skills and eco-friendly practices, we played a pivotal role in addressing critical challenges faced by Mr. Frazier's company. This collaboration resulted in a staggering 30% enhancement in vehicle performance, marking a significant milestone in our journey towards innovative excellence.
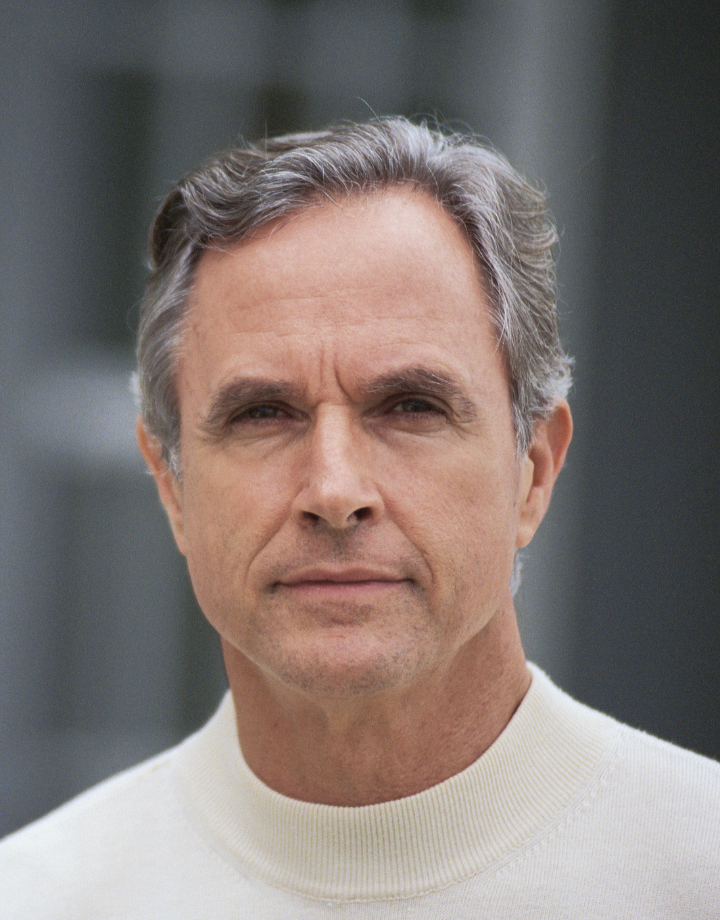
Our collaboration with Mr. Virden's HVAC company is a shining example of Zemetal's commitment to delivering bespoke metal fabrication solutions that are both innovative and efficient. By embracing and solving unique architectural challenges, we not only improved the functionality of their HVAC systems but also seamlessly integrated them into the desired aesthetics. This strategic partnership led to substantial growth for our client, showcasing the transformative impact of our tailored solutions.
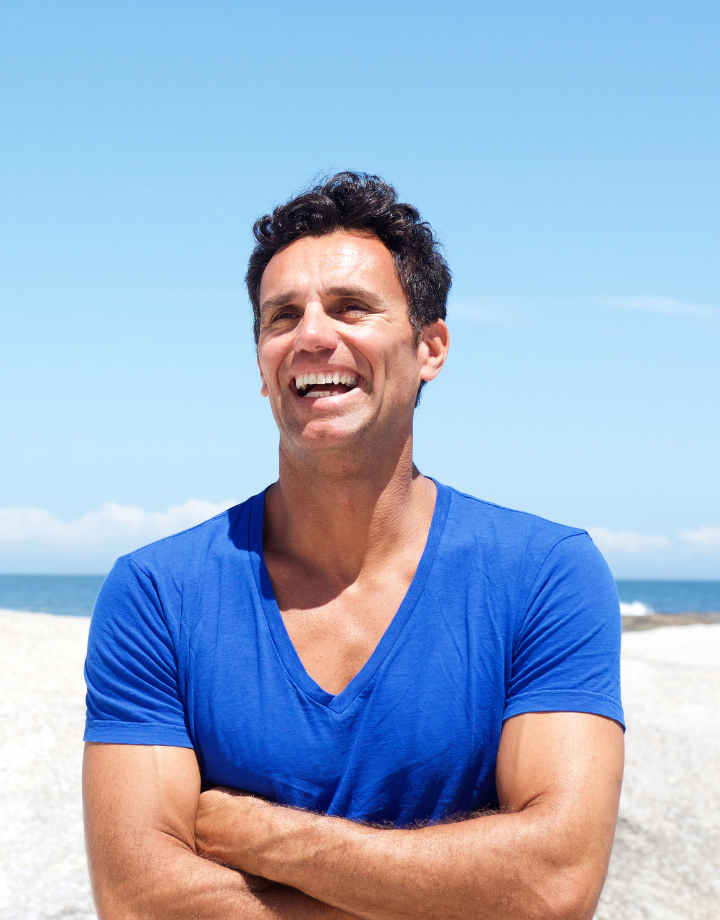
Working with Mr. Park and his team at the automotive company highlighted Zemetal's unwavering commitment to precision, innovation, and efficiency. By confronting their complex challenges with our advanced manufacturing techniques, we didn't just meet their high standards; we played a crucial role in significantly boosting their vehicle performance. This collaboration underscores our dedication to pushing the boundaries of what's possible in automotive excellence.

Previous
Next
Your Manufacturing Demands, Our Expert Solutions
Comprehensive Fabrication Services
Offering a wide range of metal fabrication services, from cutting and bending to welding and assembling, tailored
to your specific requirements.
Advanced Technology & Equipment
Utilizing state-of-the-art machinery and technology to ensure high precision and quality in every project, meeting the
most demanding manufacturing standards.
Expert Team & Quality Assurance
Our skilled professionals are committed to delivering excellence. We adhere to strict quality control protocols to
ensure top-notch results.
Flexible Production Capacity
Whether you need a single prototype or large-scale production, our flexible manufacturing processes can adapt to your project’s scale and complexity.
Timely Delivery & Customer Support
We understand the importance of deadlines. Our efficient processes and dedicated support team ensure timely delivery and ongoing communication throughout your project.
Sustainable Practices & Material Options
Committed to environmental responsibility, we offer sustainable manufacturing practices and a variety of material choices, including eco-friendly and recycled options, to meet both
your project needs and environmental goals.
Applicable Materials for Anodising Services
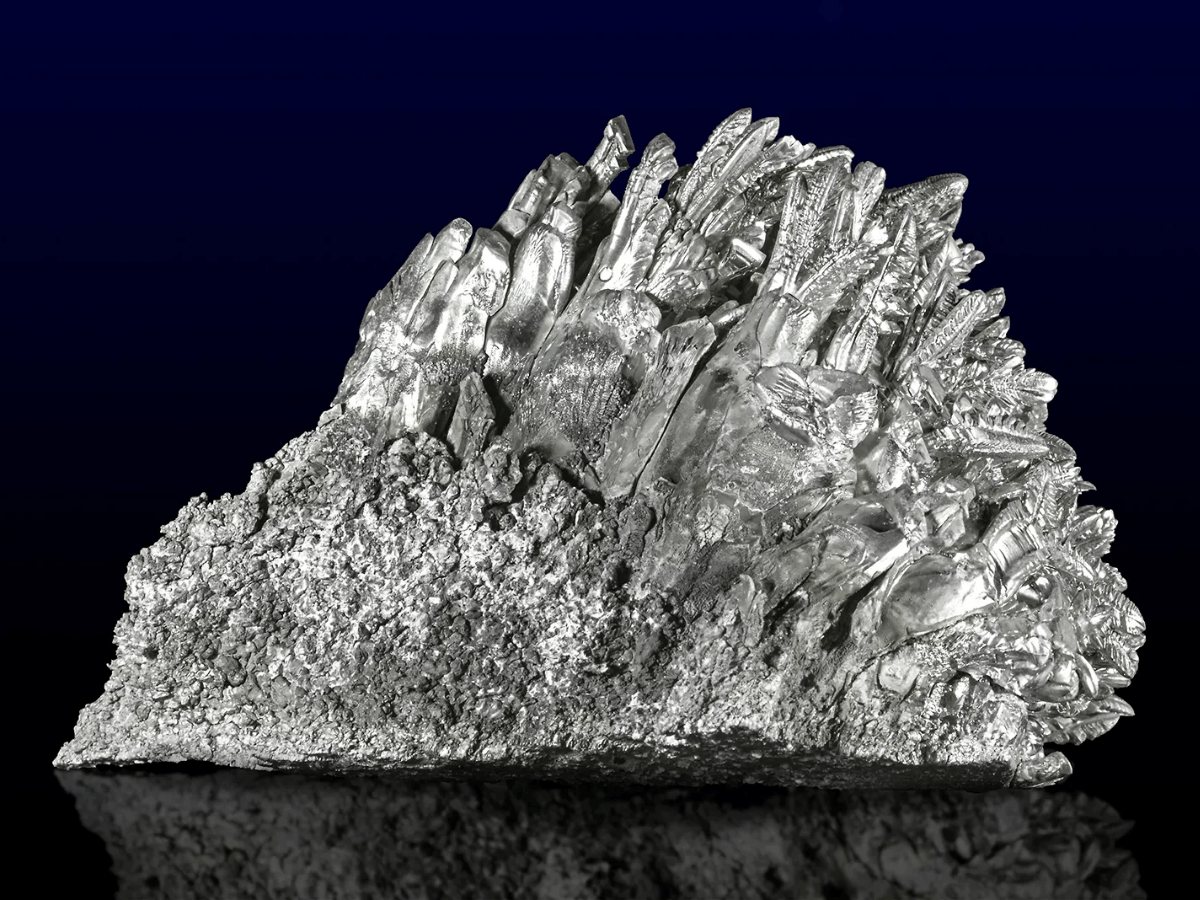
Magnesium
Although less common, magnesium can be anodized to improve its corrosion resistance and surface hardness. This makes it valuable for lightweight components in automotive and aerospace sectors, where strength and durability are paramount. Exploring the potential of magnesium through anodizing unveils new horizons for advanced, lightweight designs.
Zinc
Zinc, when anodized, benefits from increased corrosion resistance and a variety of finish options. This makes it ideal for protective coatings in harsh environments, such as marine or industrial settings. For example, anodized zinc is often used in the manufacturing of marine hardware and industrial machinery, where its enhanced durability is crucial.
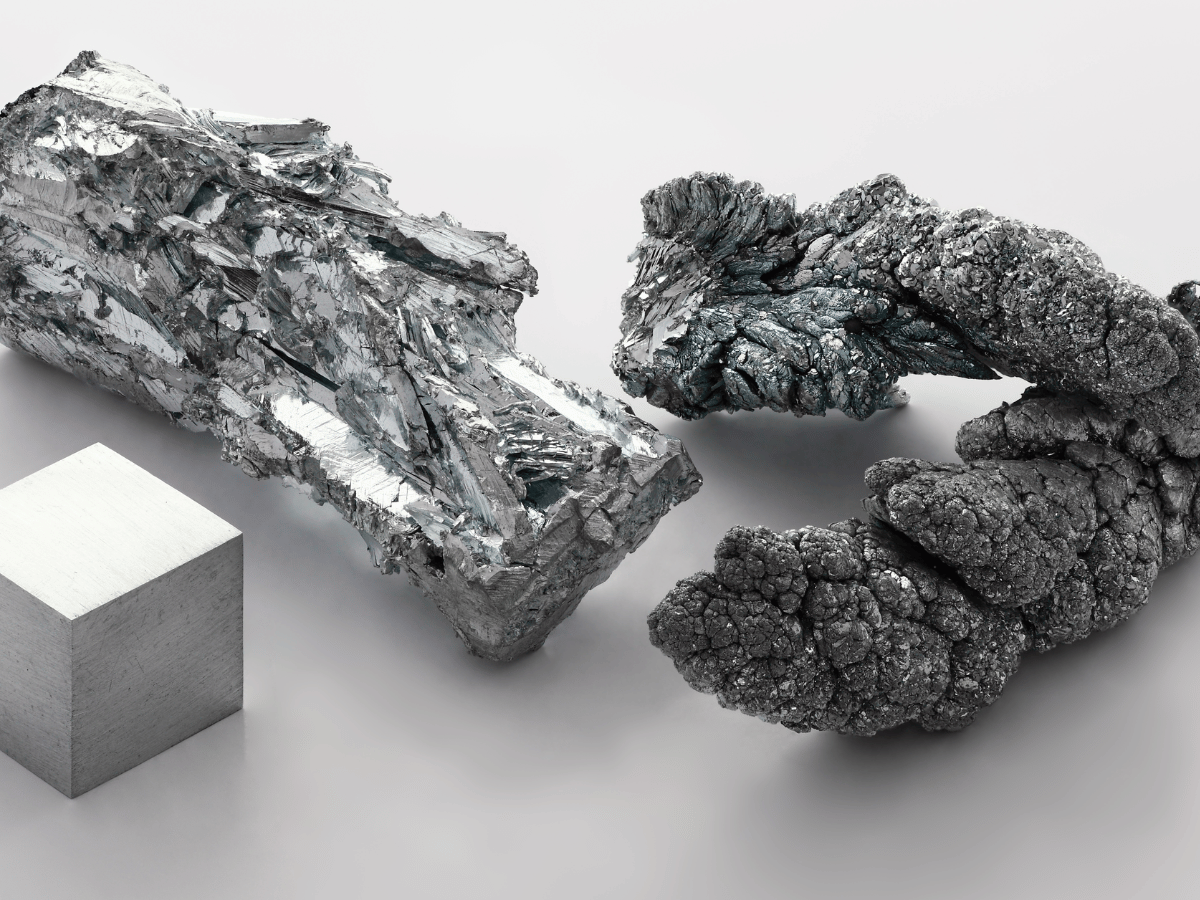
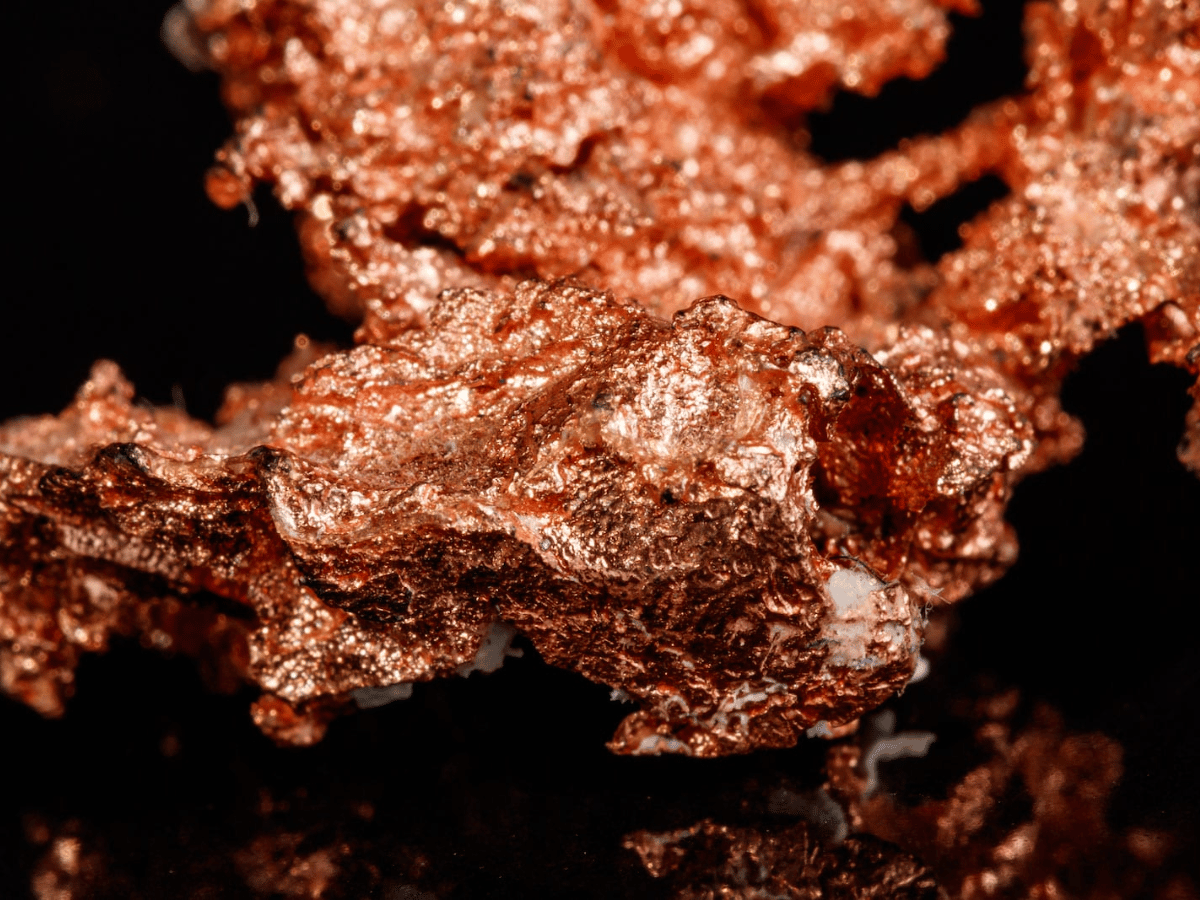
Copper
Copper anodising is less common due to its challenging nature but offers unique aesthetic finishes. It’s used in decorative applications and in situations where the natural beauty of copper is desired with added durability. This process is particularly beneficial for architectural elements, where the appearance of copper is sought after, but with increased resistance to environmental factors.
Nickel
Nickel is suitable for anodising, especially for creating wear-resistant surfaces. The process enhances nickel’s natural corrosion resistance, making it a choice for components in high-wear environments like machinery and electronic devices. Anodised nickel is often utilized in the automotive industry for parts that require a tough, long-lasting surface under rigorous conditions.
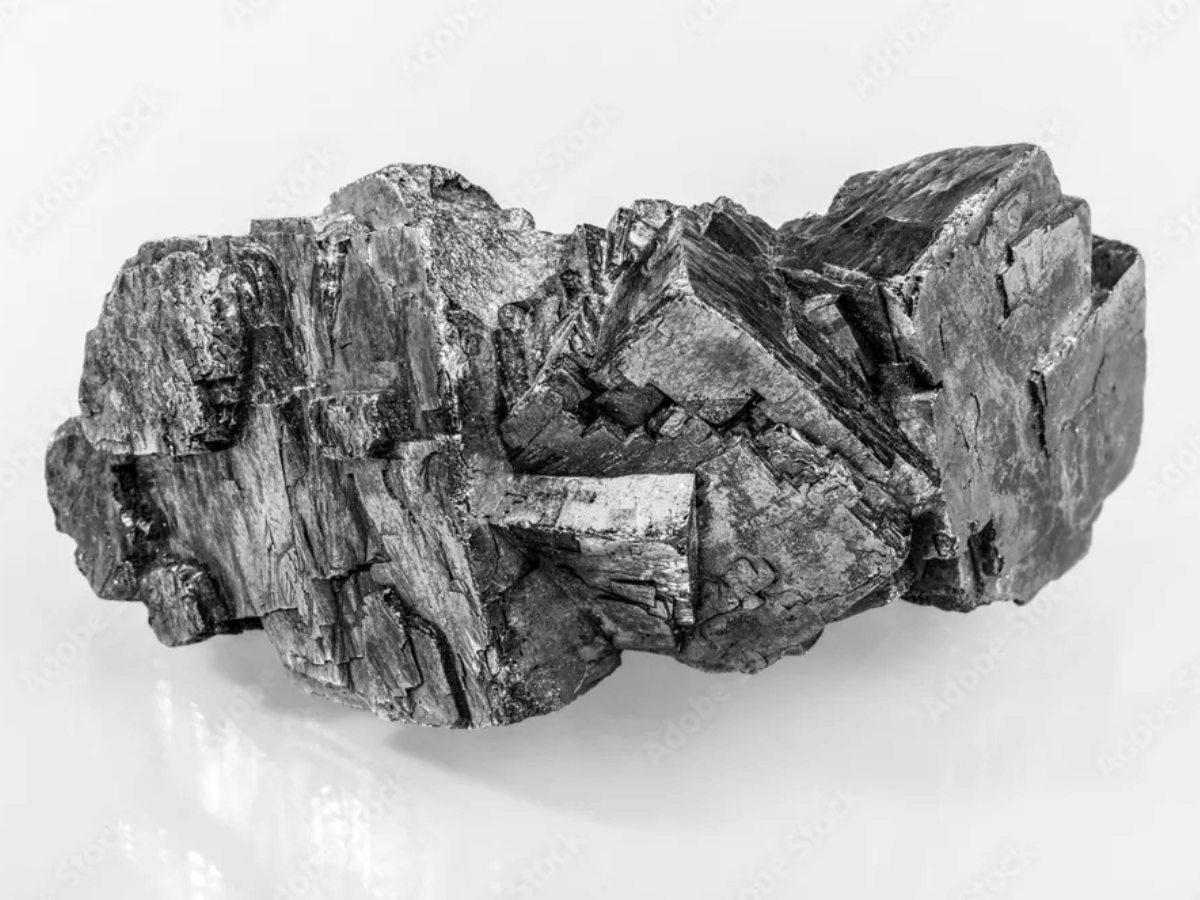
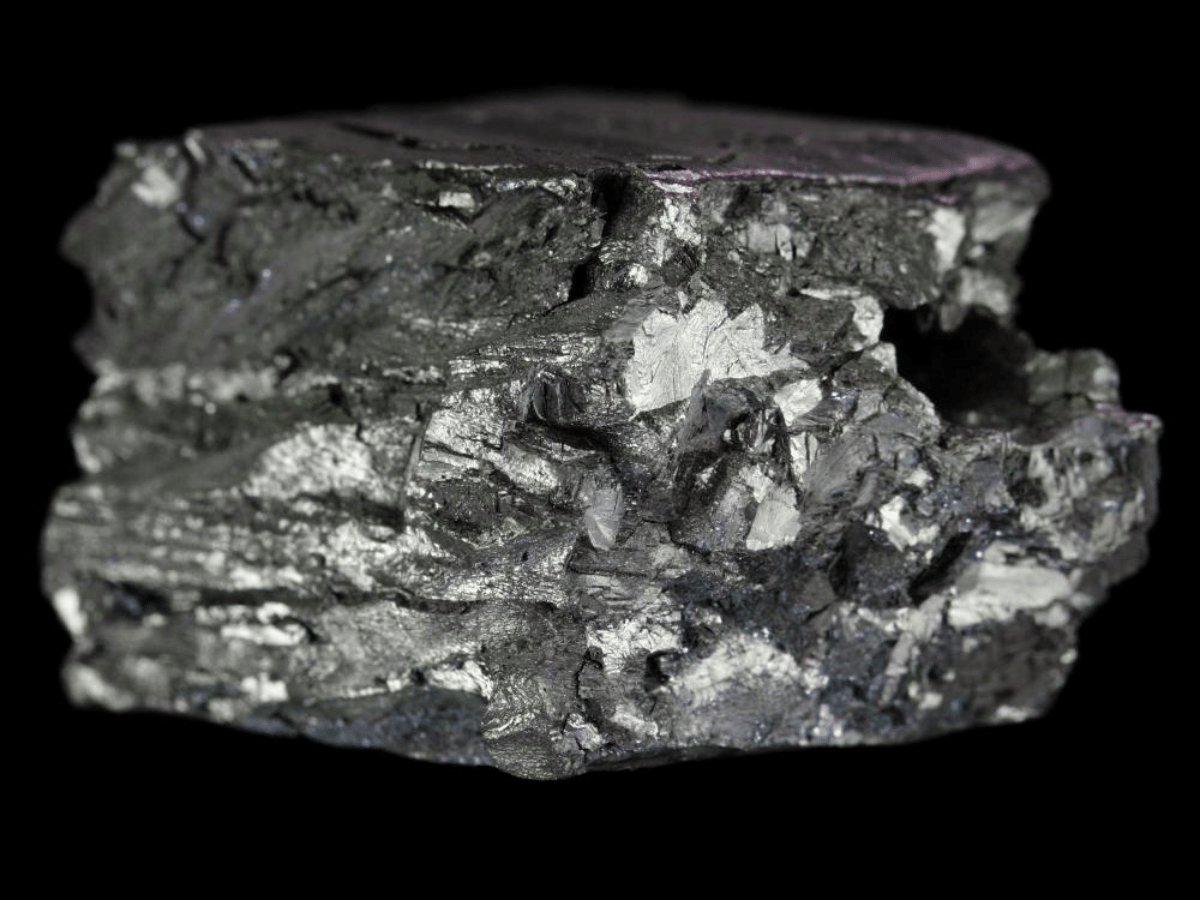
Beryllium
Beryllium is a rare choice for anodising but offers exceptional results in terms of enhancing its thermal and electrical properties. It is mainly used in specialized applications, such as aerospace and military, where its unique characteristics are essential. Zemetal leverages the distinctive properties of beryllium in anodising to meet the demanding requirements of these specialized sectors.
Features of Anodising Services
Corrosion Resistance
Through anodising, a protective layer is formed on the metal surface, offering remarkable resistance to corrosion. This feature is crucial for metals exposed to harsh environments, like marine or industrial settings, ensuring longevity and maintaining structural integrity. This transformative process effectively shields metals, empowering them to withstand even the most challenging conditions with ease.
Â
Improved Adhesion
Anodised surfaces offer better adhesion for paints and primers, making them an excellent choice for further coating processes. This feature is vital for industries where both durability and aesthetics are important, like automotive or architectural sectors. Moreover, this improved adhesion contributes to a longer-lasting and more visually appealing finish, crucial in consumer-facing products.
Â
Electrical Insulation
Anodising also enhances the electrical insulation properties of metals. This is particularly beneficial for components used in electrical and electronic applications, where non-conductive properties are essential. This added insulation capacity is key in preventing short circuits and enhancing the overall safety of electronic devices.
Benefits of Anodising Services
Increased Lifespan of Products
By enhancing the durability and corrosion resistance of metals, anodising services significantly increase the lifespan of the products. This leads to reduced maintenance and replacement costs over time, a vital factor for businesses looking to maximize their investment. The extended lifespan also translates to a more sustainable approach, reducing the need for frequent material replacements.
Â
Enhanced Safety
Anodised metals are safer to handle due to their increased resistance to heat and less likelihood to corrode. This is particularly important in industries where worker safety is paramount, like in construction or manufacturing. The non-toxic nature of the anodising process ensures that the metals are safe for use in environments where health and safety are critical concerns.
Â
Improved Product Performance
With enhanced properties like increased hardness and electrical insulation, anodised metals offer improved performance. This is crucial in sectors where reliability and efficiency are key, such as in aerospace or automotive industries. Zemetal specializes in tailoring these properties to meet the specific demands of each industry, ensuring optimal functionality and performance.
Types of Anodized Metals
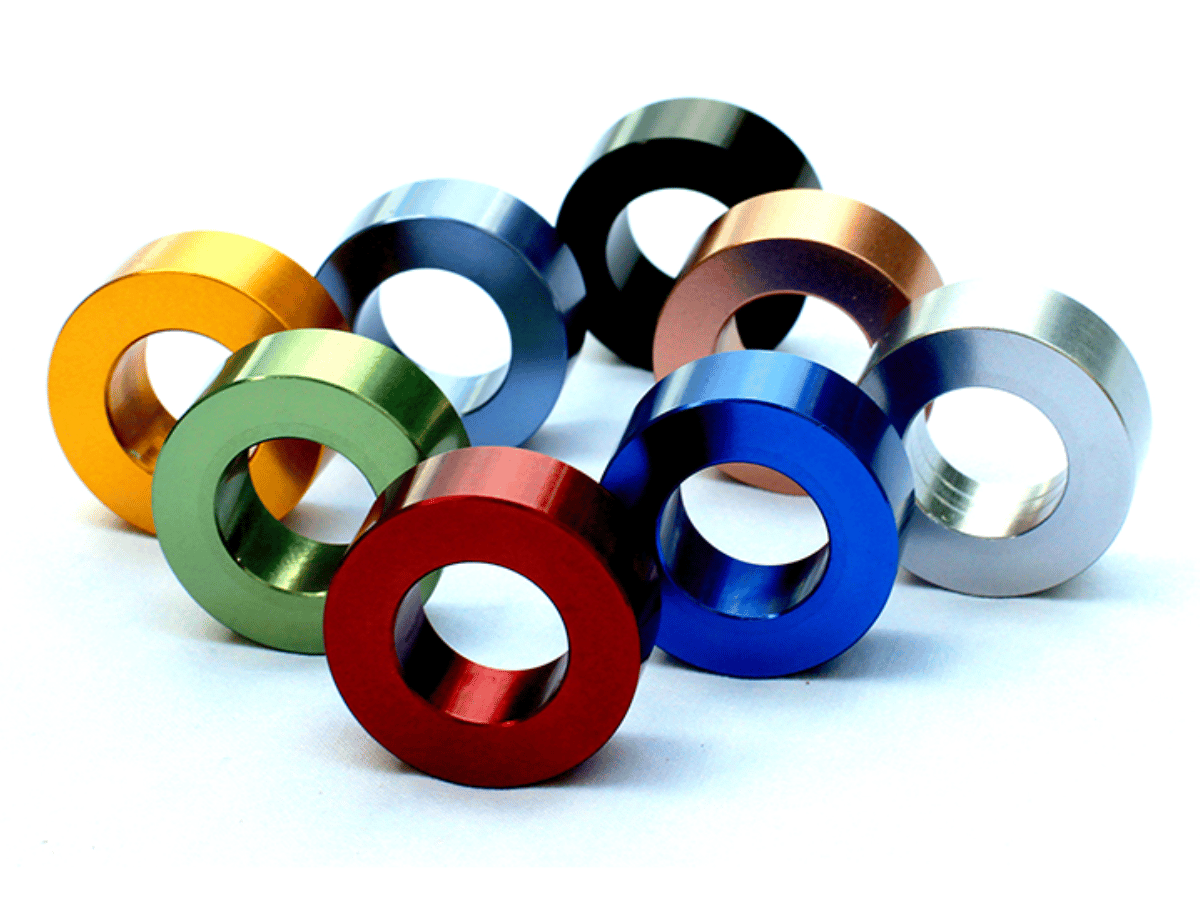
Anodized Aluminum
Anodized aluminum features an enhanced oxide layer, providing superior durability and corrosion resistance. Ideal for architectural and automotive applications, it offers a wide range of color options while maintaining the lightweight properties of aluminum. This makes it a versatile choice for both functional and decorative purposes.
Anodized Titanium
Anodizing titanium results in a highly durable and corrosion-resistant finish. Unique to titanium anodizing is the ability to create vibrant, iridescent colors through thickness variations of the oxide layer. This process is particularly popular in medical devices and jewelry due to its biocompatibility and aesthetic appeal. Zemetal excels in this specialized technique, ensuring top-quality results.
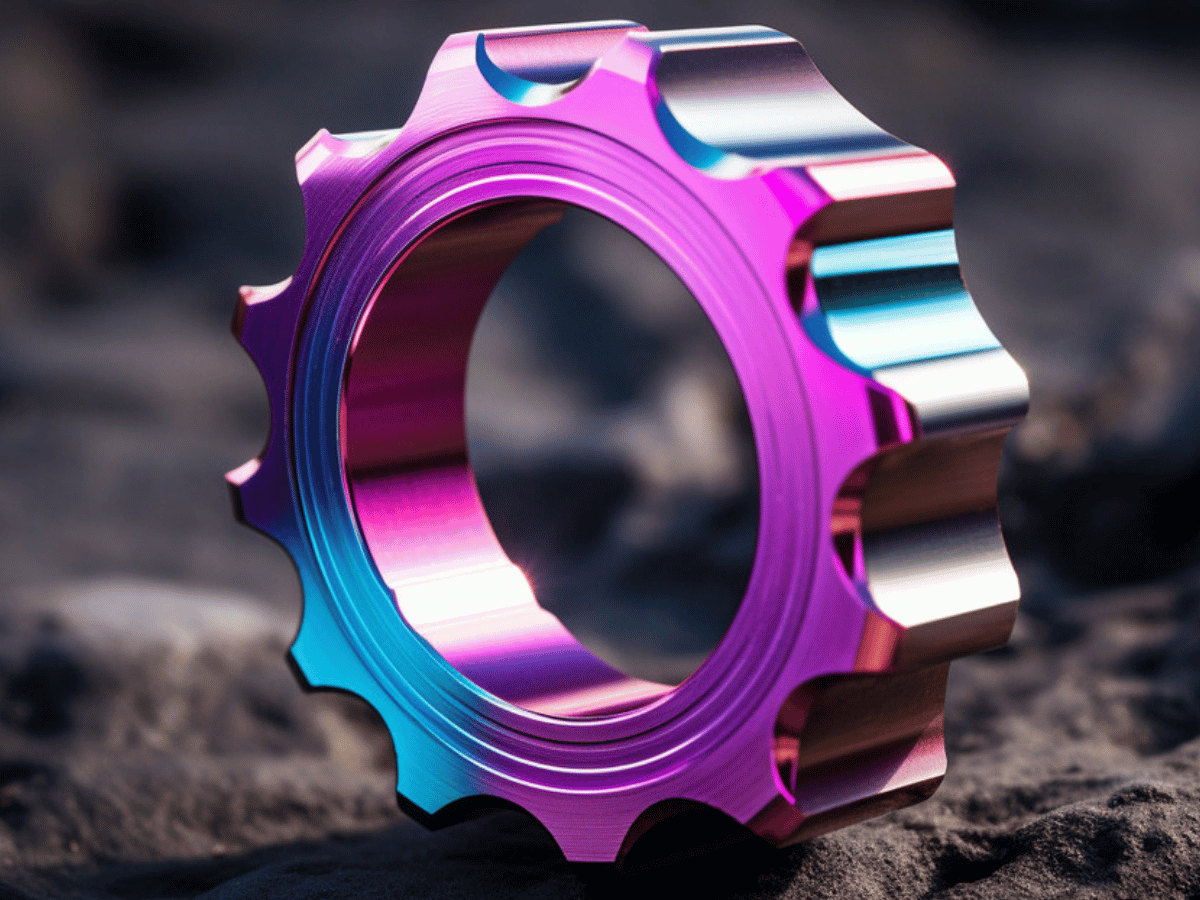
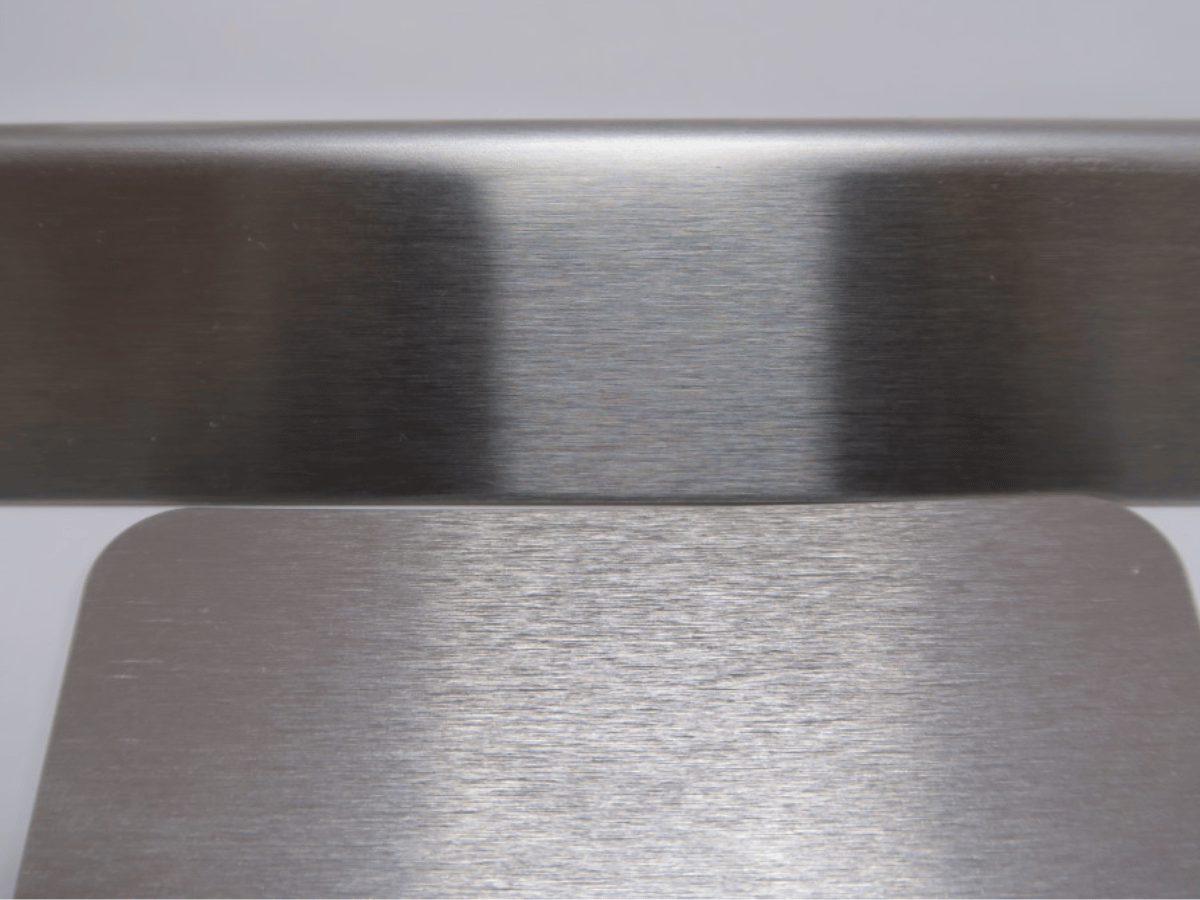
Anodized Steel
Anodized steel benefits from increased resistance to corrosion and wear, extending its usability in harsh environments. Anodized steel is ideal for specific industrial machinery, combining steel’s strength with anodizing’s benefits. For instance, anodized steel is often employed in the construction of heavy-duty equipment and tools in the manufacturing sector, where resilience is key.
Anodized Bronze
Anodized bronze offers a robust finish while retaining the distinct appearance of bronze. It’s highly resistant to wear and corrosion, making it suitable for historical restorations or decorative architectural elements where maintaining the bronze aesthetic is essential. This finish is often chosen for outdoor sculptures and fittings, where its weather resistance is as important as its visual appeal.
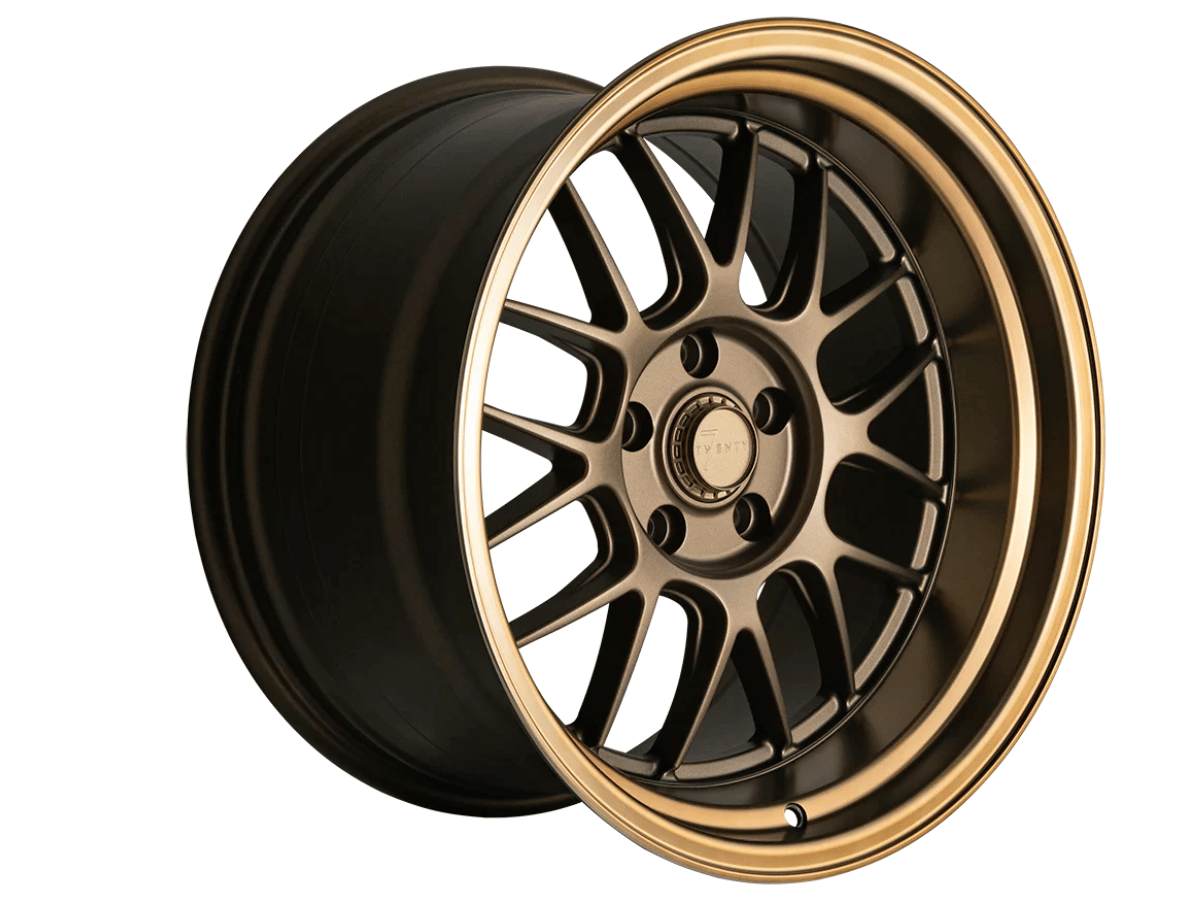
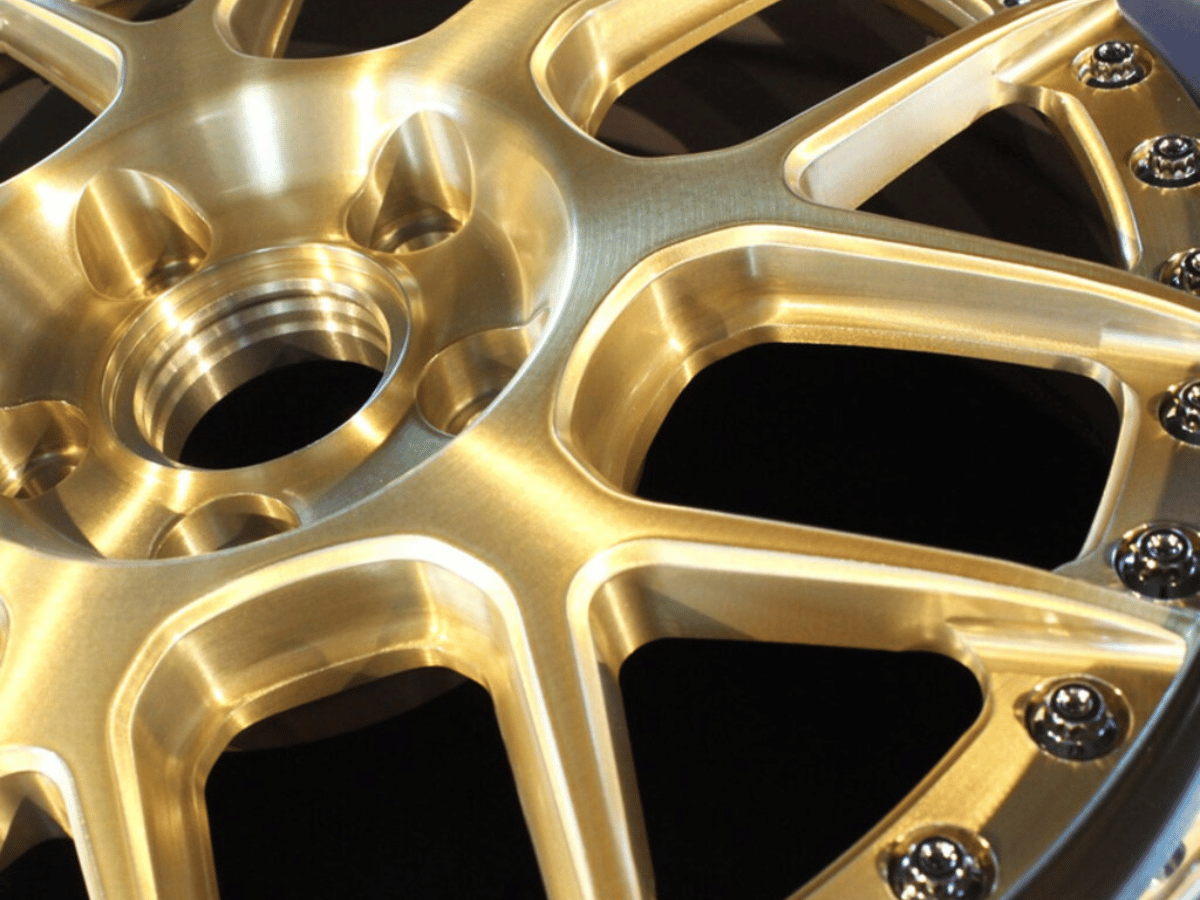
Anodized Brass
Anodising brass enhances its natural corrosion resistance and results in an attractive, durable finish. This process is often used in decorative applications, including fixtures and musical instruments, where the golden hue of brass is desired along with added durability. It’s also popular in marine environments, where its resistance to saltwater corrosion is highly valued.
Anodized Niobium
Anodized niobium is notable for its ability to take on a wide range of colors without dyes, due to the refractive properties of its oxide layer. This makes it a popular choice in jewelry making and in applications where hypoallergenic properties are important, such as body piercings. Its unique coloring technique also makes it a favorite for artists and designers seeking unique, vibrant hues.
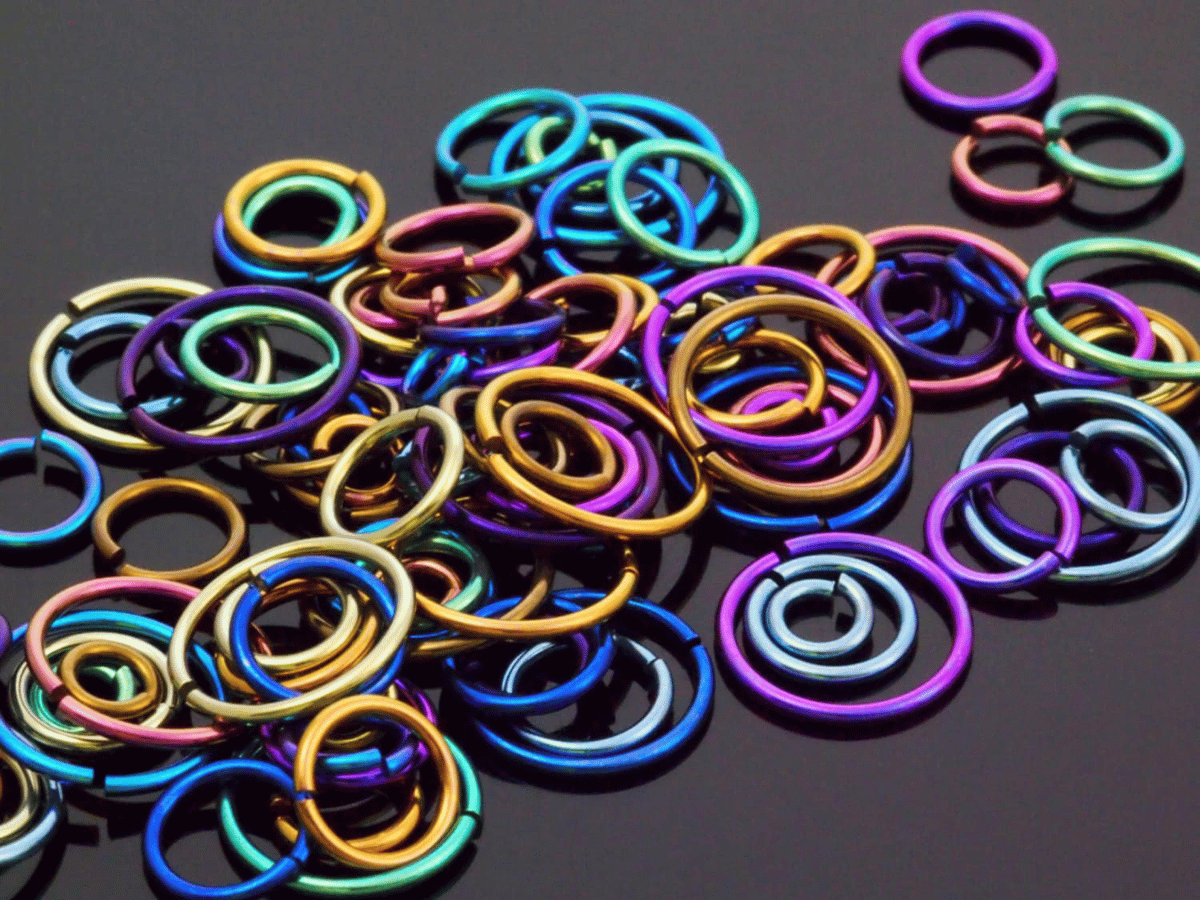
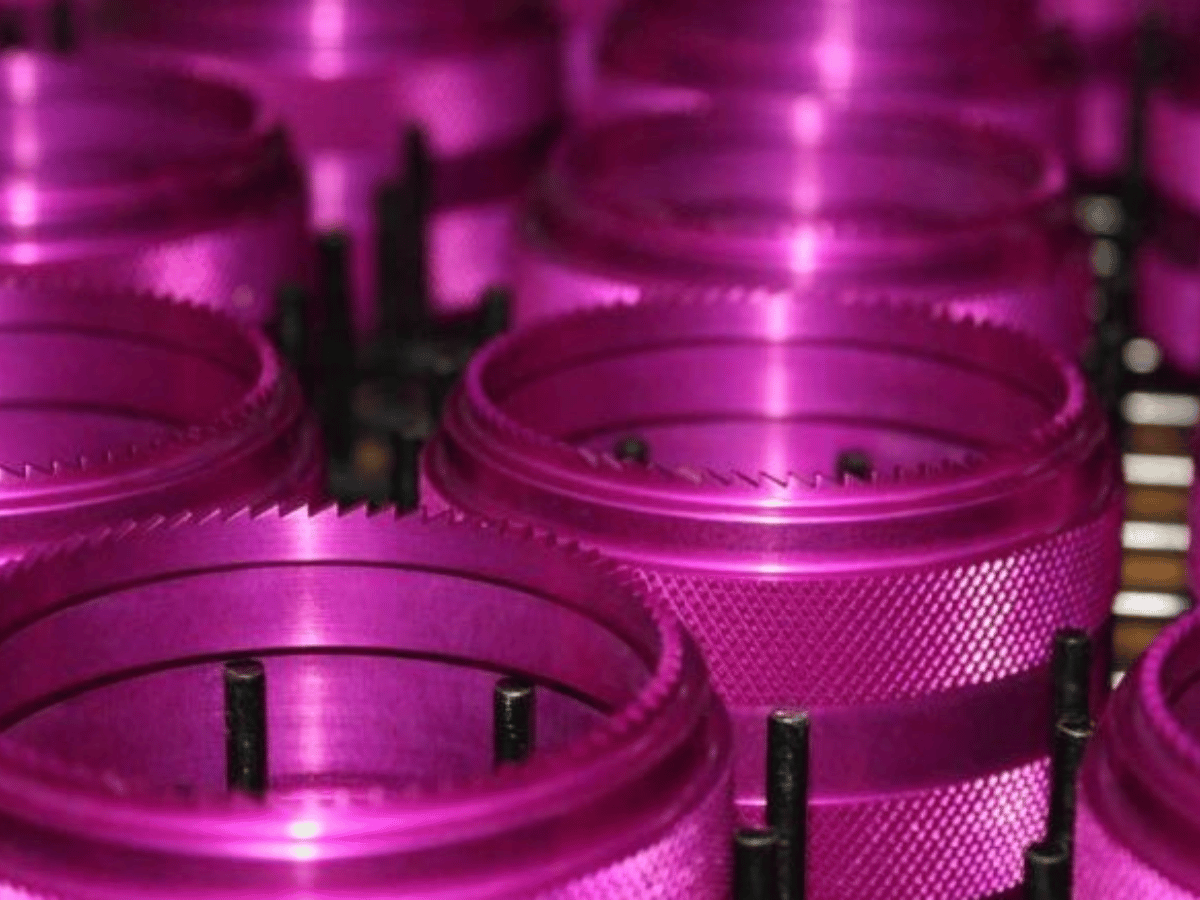
Anodized Magnesium
Anodizing magnesium improves its corrosion resistance and surface hardness, making it ideal for lightweight components in automotive and aerospace applications. However, magnesium anodizing is more complex due to the metal’s reactivity, requiring specialized processes. This treatment is particularly beneficial in high-performance automotive applications where weight reduction is crucial.
Anodized Nickel
Anodizing nickel enhances its natural corrosion resistance and provides a harder surface. This process is valuable in manufacturing components for high-wear environments, such as in certain machinery parts and tools, where nickel’s properties are beneficial. The transformation of nickel through anodizing opens up new possibilities for durable, long-lasting components.
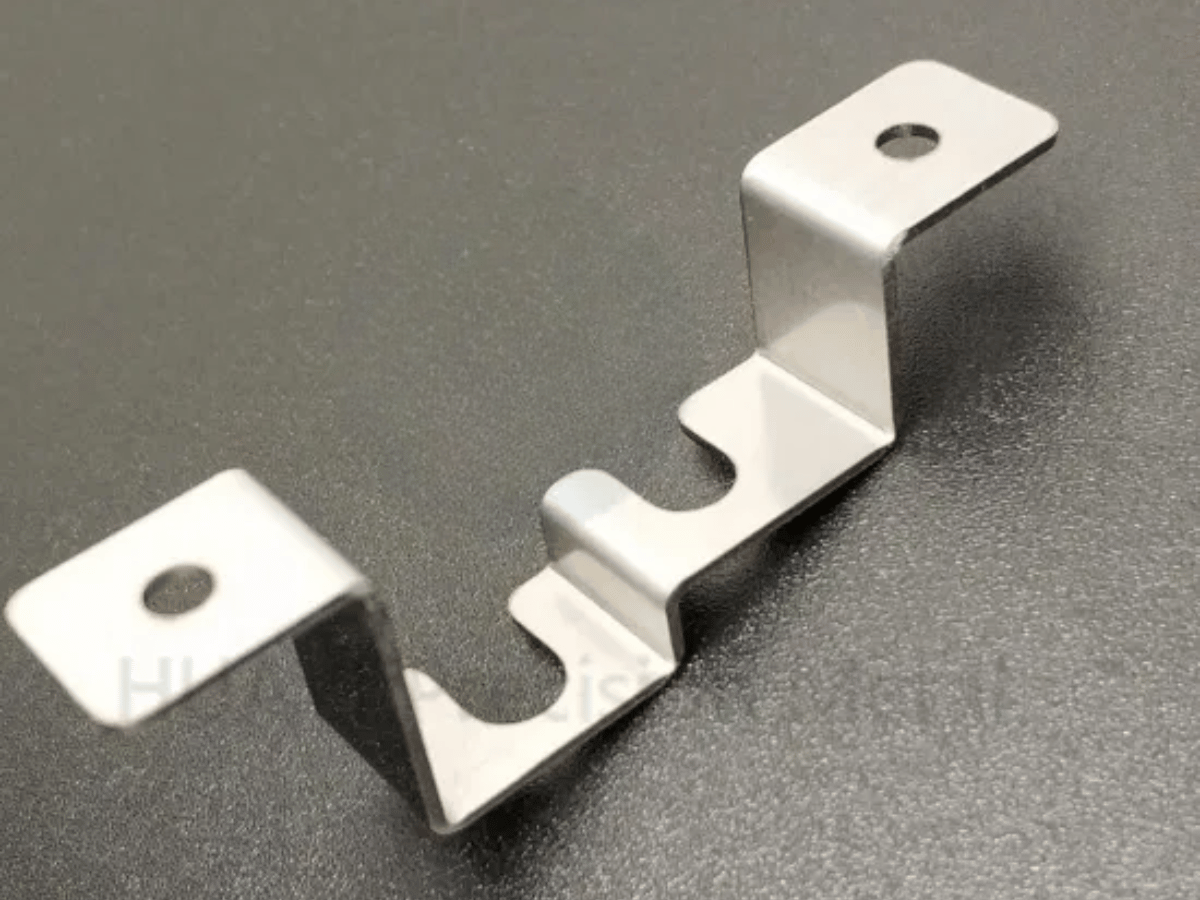
Anodising Techniques and Finishes
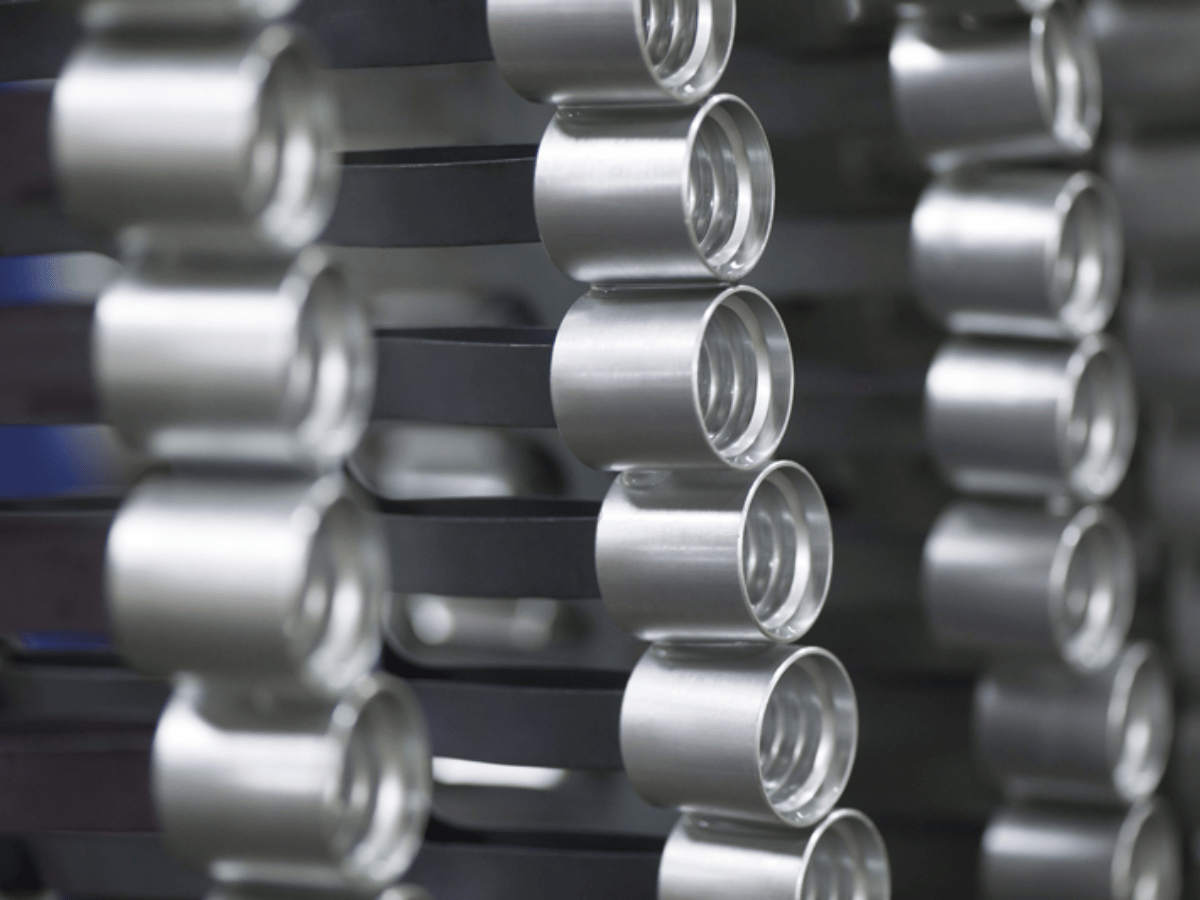
Clear Anodizing
Clear anodizing involves creating a transparent oxide layer that retains and protects the metal’s natural appearance. It provides a protective coating without altering the metal’s original texture or color. This technique is ideal for maintaining the raw, metallic look while offering increased durability and corrosion resistance.
Hard Anodizing
Hard anodizing creates a thick, hard, and extremely durable oxide layer on the surface of the metal. This technique is typically used to improve wear and corrosion resistance, especially for parts subjected to high stress or harsh environments, like industrial machinery components. This process transforms metals into resilient powerhouses, capable of enduring the most demanding conditions.
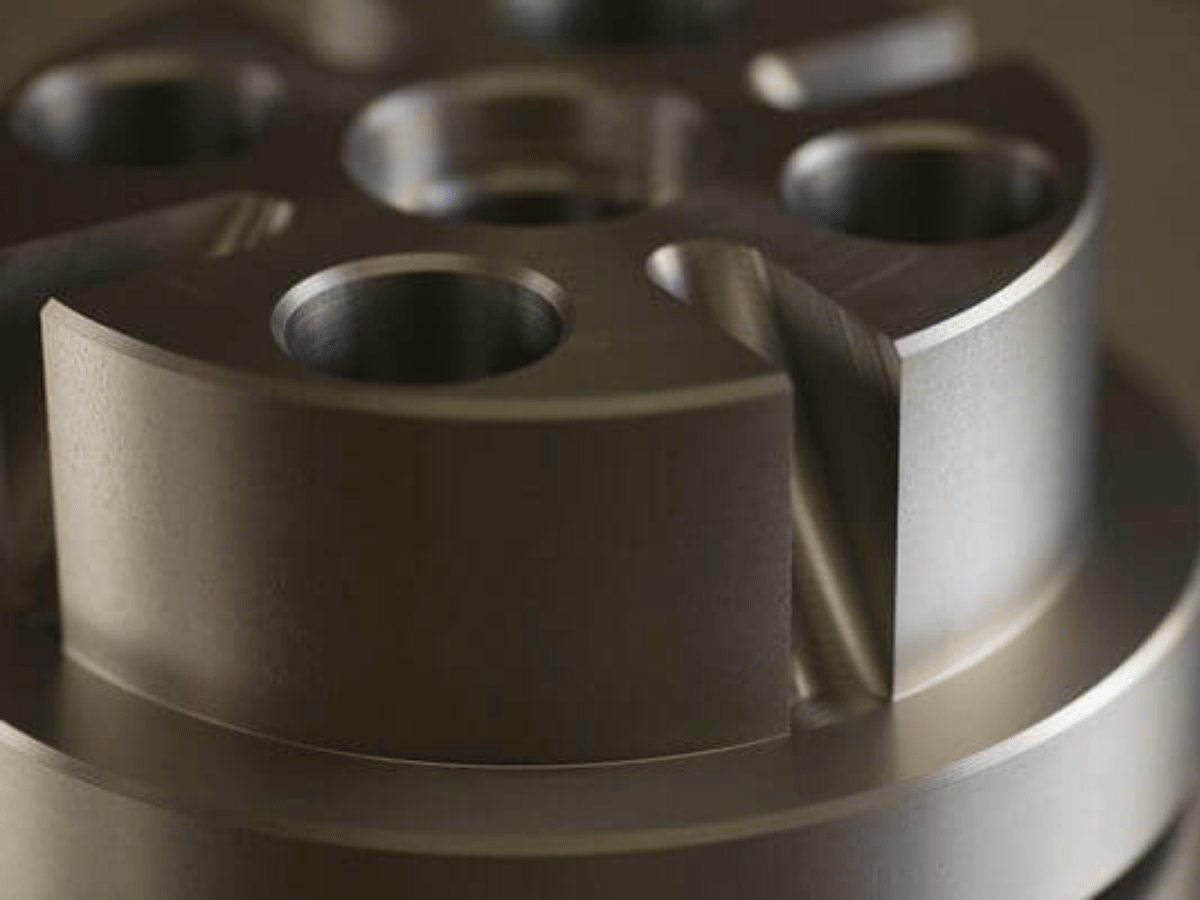
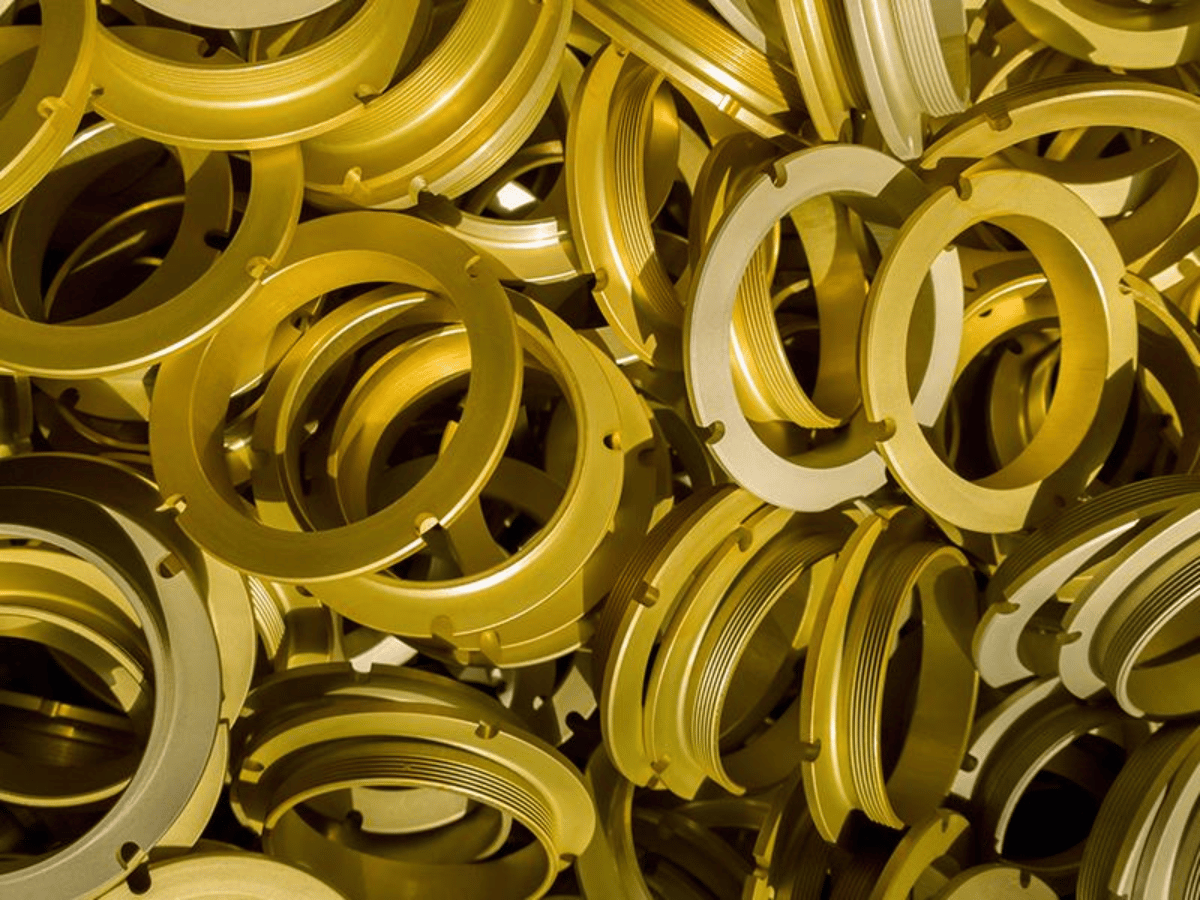
Chromic Acid Anodizing
Chromic acid anodizing uses chromic acid to create a thinner oxide layer, offering good corrosion resistance and minimal dimensional impact. This method is often used for aerospace components where precise dimensions and corrosion resistance are critical. It is essential for applications like aircraft skins where weight and structural integrity are paramount.
Quickturn Anodizing
Quickturn anodizing is designed for rapid processing, delivering faster turnaround times than traditional methods. It’s suitable for projects with tight deadlines, offering the standard benefits of anodizing without extended processing times. This makes it a go-to option for prototype development and urgent production needs.
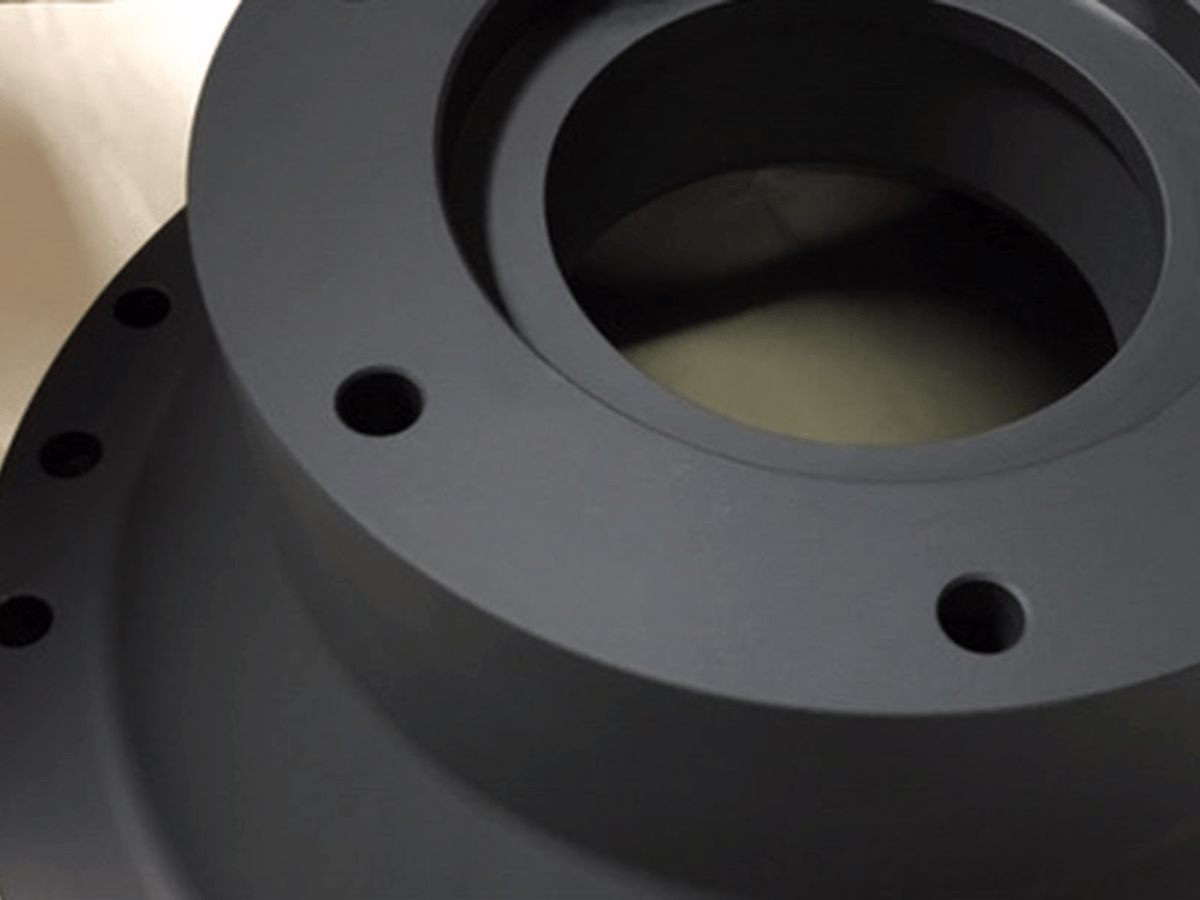
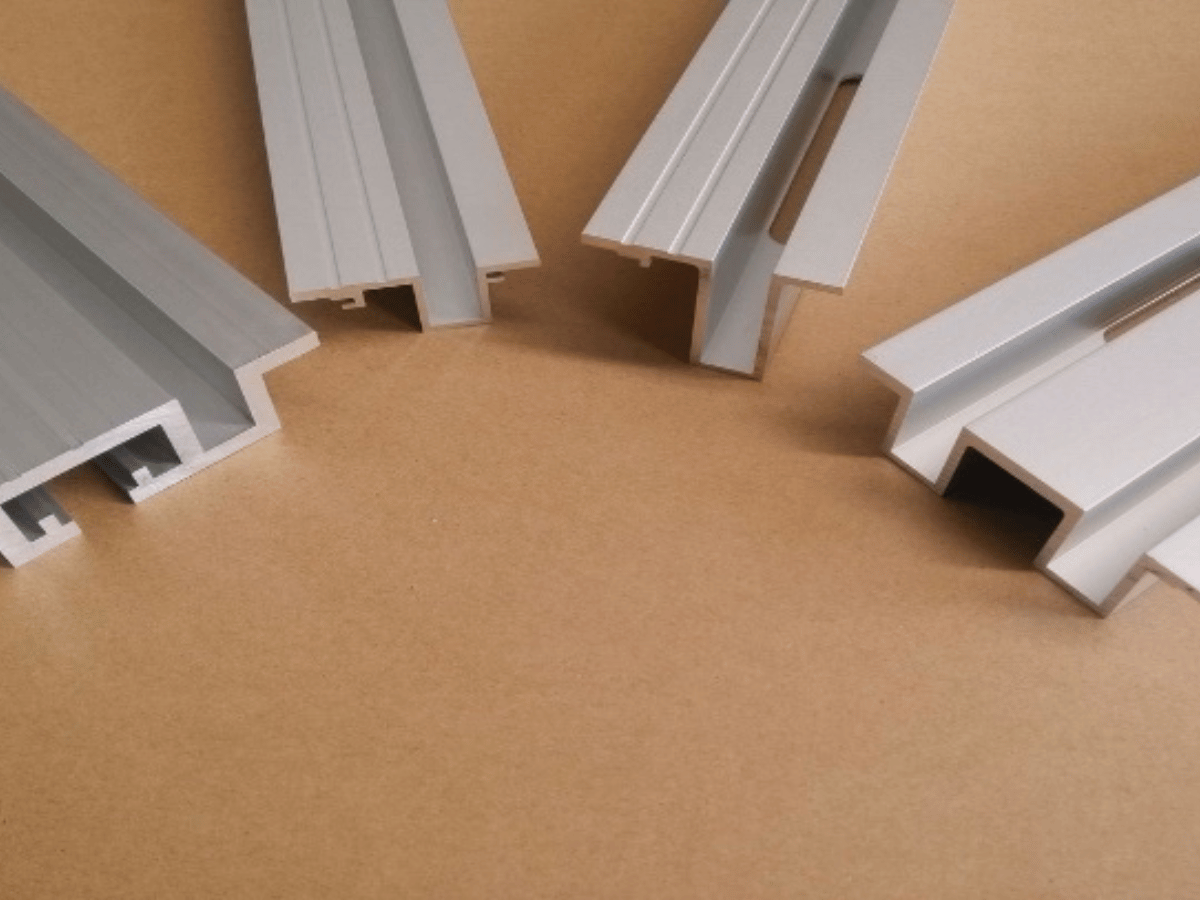
Natural Anodizing
Natural anodised finishing maintains the metal’s natural color while providing an enhanced protective layer. It’s often chosen for architectural applications where the beauty of the original metal is a key aesthetic consideration. This method is also favored for products where maintaining a natural metallic look is essential, without compromising on protection.
Type II Anodizing
Type II anodizing, commonly using sulfuric acid, is the standard for creating decorative, durable, corrosion-resistant finishes. It’s versatile and can be used on various metals, offering a wide range of color options for aesthetic purposes. This finish is also used in automotive applications for both aesthetic appeal and enhanced resistance to environmental elements.

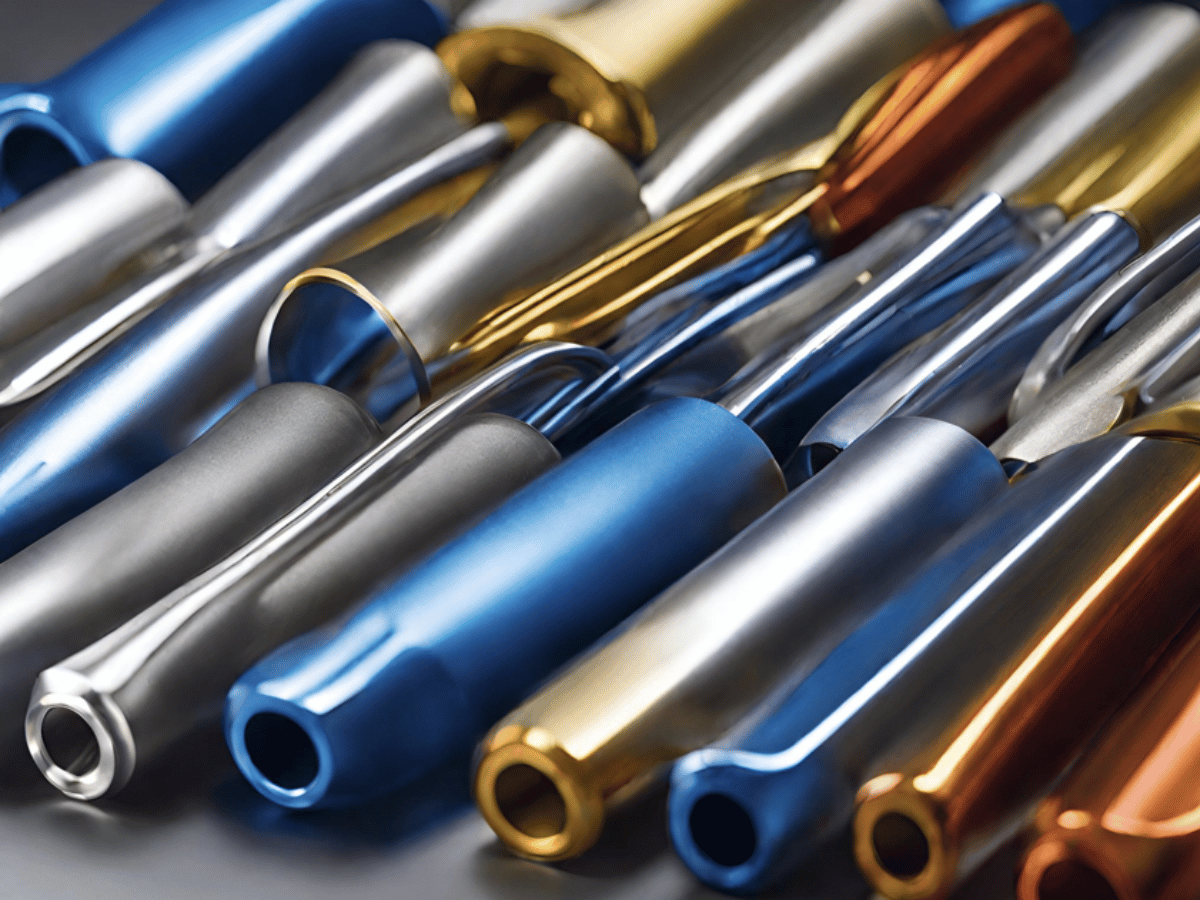
Bright Dip Anodizing
Bright dip anodizing involves pre-polishing the metal to achieve a mirror-like finish before the anodizing process. This technique is often used for decorative items or components where a shiny, reflective surface is desired. It is ideal for creating eye-catching pieces in retail displays and high-end decorative elements. This process is perfect for custom car parts and motorcycle components, where a high-gloss finish is highly valued.
Satin Anodizing
Satin anodized finishes provide a smooth, matte surface, offering an understated and elegant appearance. This finish is popular in architectural and design applications where a non-reflective surface is preferred. It’s a favorite for interior design elements and modern building facades. This type of finish is also sought after in the production of high-end electronic devices, where a subtle yet premium look is desired.
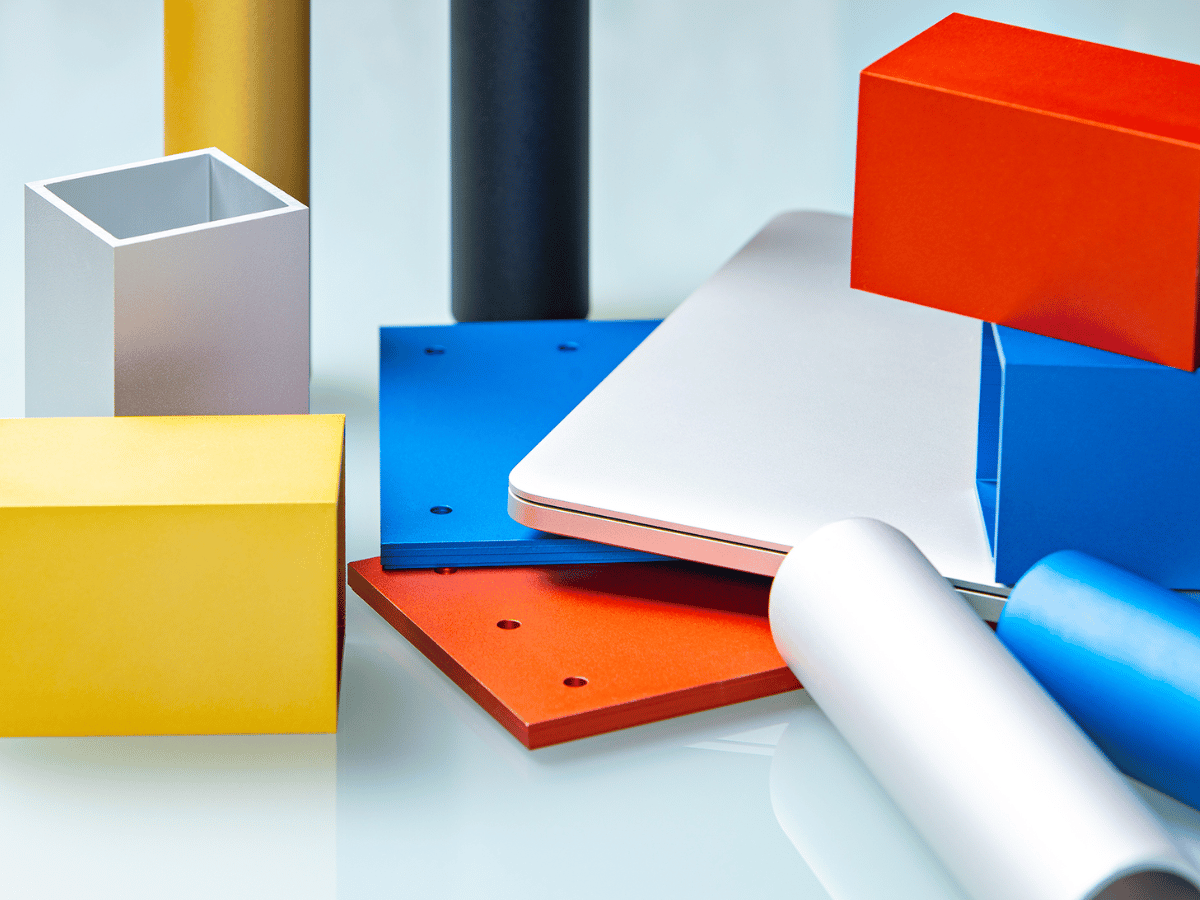
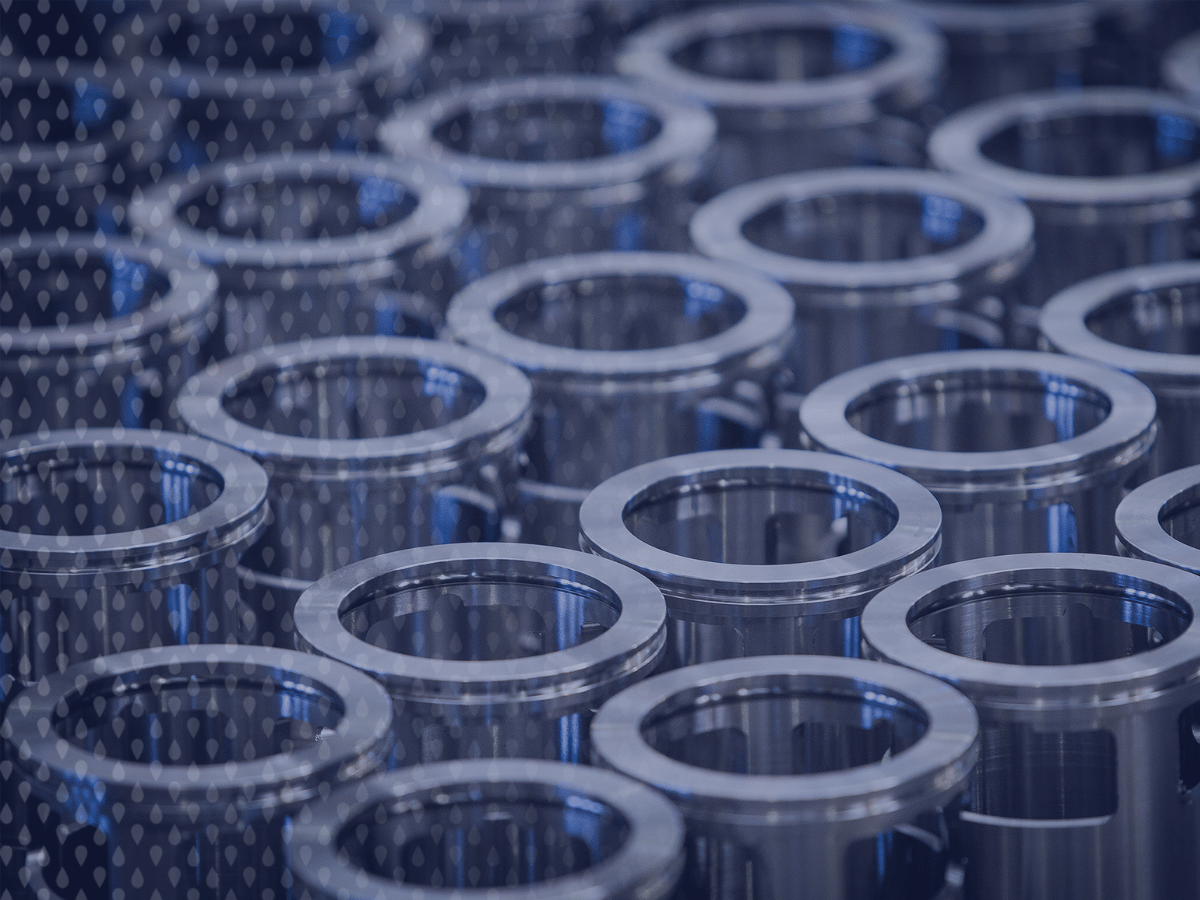
Sulphuric Acid Anodizing
Sulphuric acid anodising is a common technique that creates a thicker and more durable oxide layer. This method is widely used due to its effectiveness in enhancing wear and corrosion resistance in various applications. Zemetal specializes in this technique, ensuring optimal quality and durability for a diverse range of industrial needs.
PTFE Impregnated Anodizing
PTFE impregnated anodizing incorporates PTFE (Teflon) particles into the anodized layer, enhancing its non-stick and low-friction properties. This is especially beneficial for parts requiring reduced surface friction, like gears and moving components. It’s often used in the food industry for cookware due to its non-toxic and easy-clean properties.
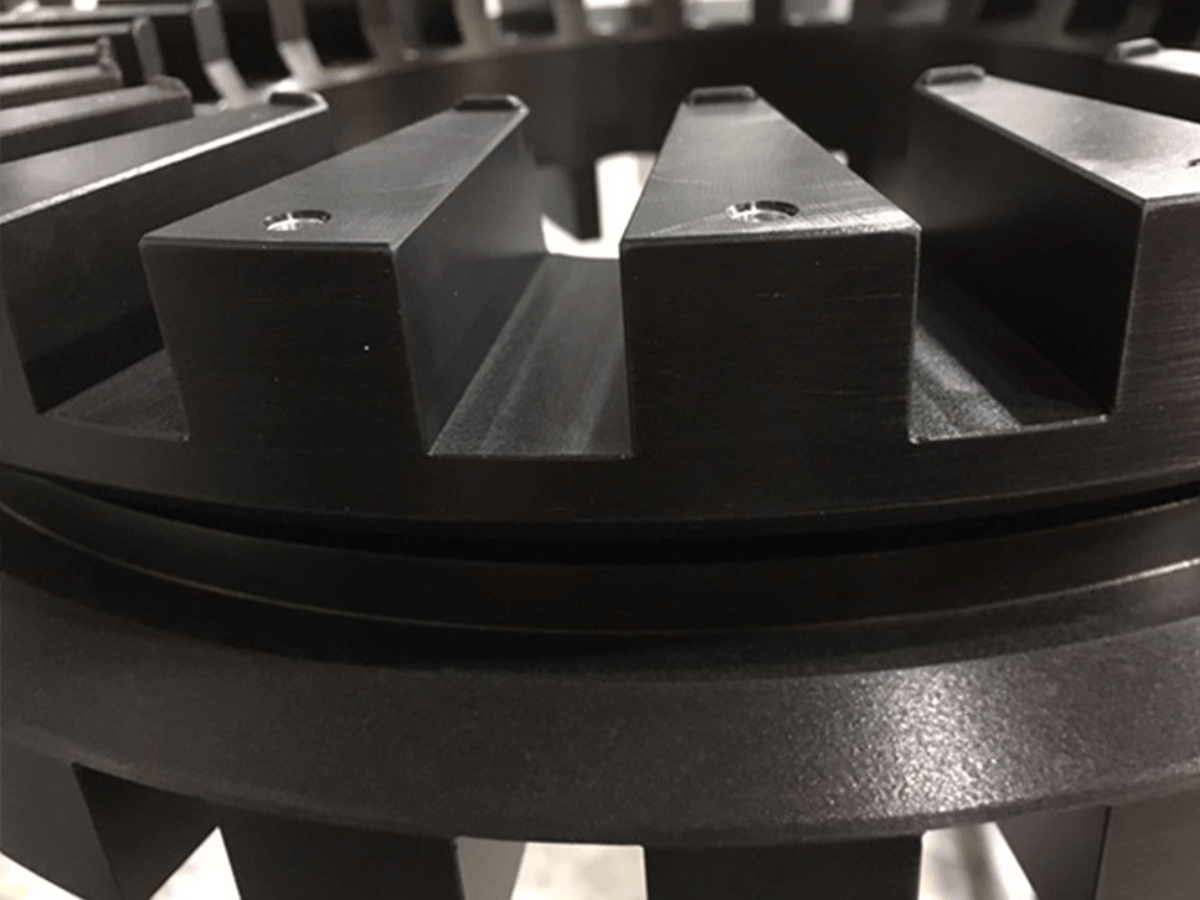
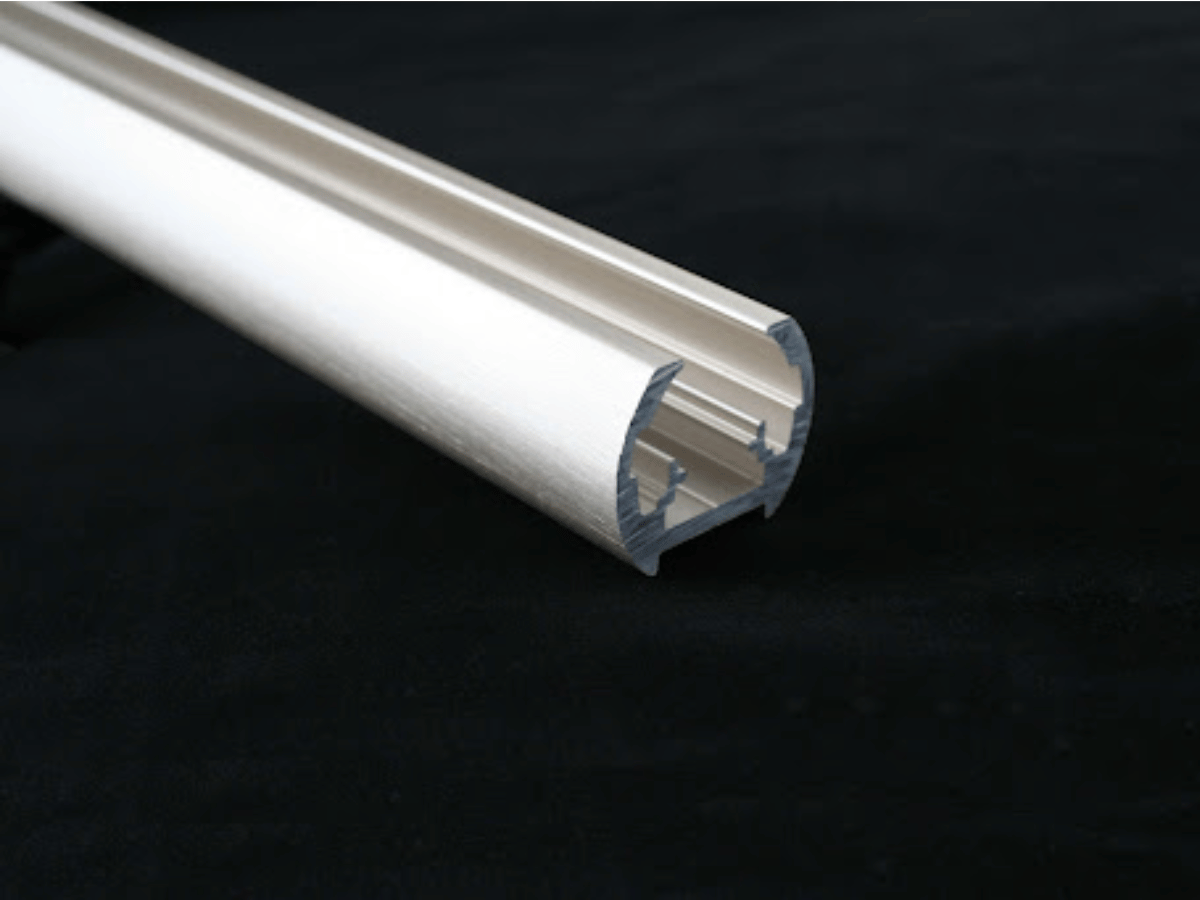
Electrochemical Anodizing
Electrochemical anodization is a broad term encompassing various anodizing processes that use electrochemical means to create the oxide layer. This method is adaptable to different metals and applications, providing a range of finishes based on the specific electrochemical technique used. For example, this technique is applied in creating durable and colorful finishes on aluminum bike frames and car parts.
Applications of Anodising Services
Architectural and Building Construction
In the architectural sector, anodising services are employed to treat aluminum panels, window frames, and facade elements. This not only augments the aesthetic appeal with varied colors and finishes but also provides a weather-resistant coating, essential for long-lasting architectural designs. Zemetal excels in delivering these specialized finishes, catering to the unique requirements of modern architecture.
Â
Consumer Electronics
Anodising is widely used in the consumer electronics industry to create durable and attractive finishes on products such as smartphones, laptops, and cameras. This process not only provides a scratch-resistant and durable surface but also allows for a variety of color options, meeting both the functional and aesthetic demands of the electronics market.
Â
Medical Equipment and Devices
Anodising services are critical in the medical field for treating equipment and devices that require high biocompatibility and corrosion resistance. Instruments, implants, and surgical tools often undergo anodising to ensure they are non-toxic, easy to sterilize, and durable. This process is pivotal in safeguarding patient health, offering reliability and safety in every medical procedure.
4 Things to Consider When Choosing Anodising Services
#1 Quality of Anodising
When selecting anodising services, the quality of the anodising process is paramount. Ensure that the service provider adheres to industry standards and offers consistent, high-quality finishes. Anodized product quality hinges on the anodising process’s excellence. Choosing a provider with a reputation for excellence can make all the difference in the longevity and appeal of the anodized products.
Â
#2 48-Hour Turnaround Time
For batch orders, a 48-hour turnaround time is a critical benchmark to consider. Assess the provider’s capability to meet such specific deadlines without sacrificing quality. This swift processing is crucial in fast-paced industries where rapid time-to-market gives a competitive edge. Zemetal consistently meets these tight deadlines, ensuring both speed and quality in their services.
Â
#3 Technical Expertise and Experience
Assess the technical expertise and industry experience of the anodising service provider. Experience in handling various metals and understanding their unique properties ensures that the anodising is done correctly and efficiently, adapting to the specific needs of each batch. This expertise is crucial in achieving the desired quality and specifications, especially for complex or large-scale projects.
Â
#4 Compliance with ISO 14001 Environmental Standards
Ensure that the anodising service complies with ISO 14001 environmental and safety regulations. This standard ensures responsible handling of chemicals and processes used in anodising to minimize environmental impact and maintain workplace safety, a critical aspect when processing large batches. Adherence to this standard signals a provider’s dedication to sustainability and employee safety.
Dive Deeper Into Our Resources
For some insightful reads, we’ve curated a list of recommended articles just for you:
Still haven’t found what you’re looking for? Don’t hesitate to contact us. We’re available around the clock to assist you.
Meet Our Best Sheet Metal Fabrication Laser Cutting Blanking Stamping Weilding Bending Services
Connect with Us
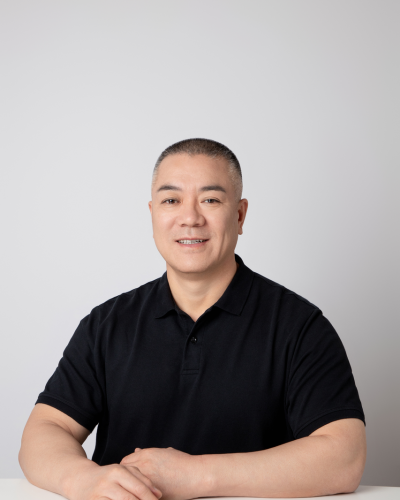
Zemetal is committed to ensuring your privacy and promises prompt, secure responses to all your inquiries.