How does the precision of bending aluminum sheet metal impact your offerings? This technique is essential for guaranteeing both the structural integrity and aesthetic appeal of your metal products.
Drawing from extensive industry experience and a deep understanding of metal fabrication, this guide is your trusted resource for mastering the details of bending aluminum sheet metal.
The practice of bending aluminum sheet metal is both an art and a science, vital in the field of metal fabrication. This process not only shapes the metal but also defines the quality and efficiency of the final product, showcasing the importance of precision and expertise.
In this guide, we will uncover the comprehensive aspects of aluminum sheet metal bending, from selecting the right materials and tools to learning various bending techniques and best practices.
Read on to unveil the art of aluminum sheet bending.
1. The Significance of Aluminum Sheet Metal Bending
Aluminum sheet metal bending is crucial in numerous industries, showcasing its versatility and impact on product functionality and design. Here are some of its importance:
- Innovation in Product Design: Bending aluminum sheet metal offers exciting possibilities in product design, enabling creative shapes and arrangements. This design flexibility broadens the potential for creating distinctive and practical products that stand out in the market.
- Enhanced Performance and Functionality: Effective bending techniques enhance the functionality of aluminum sheet metal products by achieving precise angles and curves for perfect component fit in assemblies, ultimately improving the final product’s performance.
- Economic Efficiency in Production: Aluminum sheet metal bending simplifies the manufacturing process, leading to reduced production costs and time. This efficiency arises from the ability to shape metal quickly and accurately, reducing the need for additional processing and assembly steps.
The table below showcases how aluminum sheet metal bending contributes to manufacturing efficiency, highlighting its impact on production costs and time.
Aspect | Impact on Manufacturing Process |
Reduced Production Costs | Lower material wastage and decreased labor costs due to streamlined processes. |
Enhanced Speed | Faster shaping and forming of parts, reducing overall production time. |
Accuracy and Precision | High-quality bends ensure parts fit perfectly, minimizing rework. |
Simplified Assembly | Fewer components are needed, simplifying the assembly process. |
Versatility | Ability to create complex shapes and designs without additional tools. |
2. Types of Aluminum Alloys Suitable for Bending
Building on the significance of aluminum sheet metal bending, it’s vital to recognize how different aluminum alloys impact this process for successful bending. Here are some of its types:
Alloy 1100
Alloy 1100 is known for its excellent ductility, making it highly suitable for bending operations. It’s a pure aluminum alloy, offering superior corrosion resistance and a smooth finish. This alloy is ideal for applications requiring detailed bending without compromising the material’s integrity.
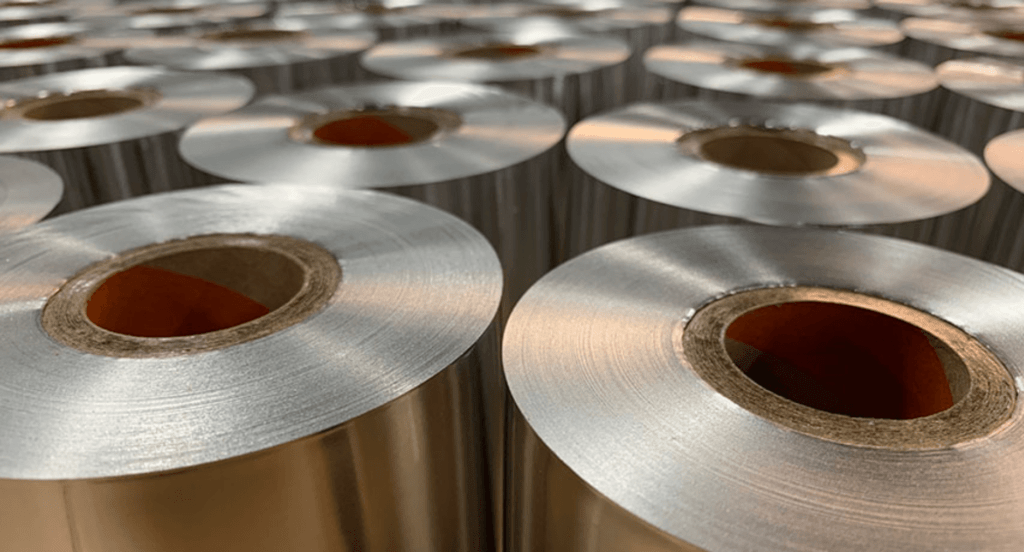
Alloy 3003
Alloy 3003, often used in sheet metal work, stands out for its blend of strength and easy shaping capabilities. This alloy, a mix of aluminum, manganese, and a small amount of copper, offers good resistance to corrosion and is well-suited for moderate bending applications. It’s particularly favored in the manufacturing of tanks, ductwork, and other components where moderate strength is needed.
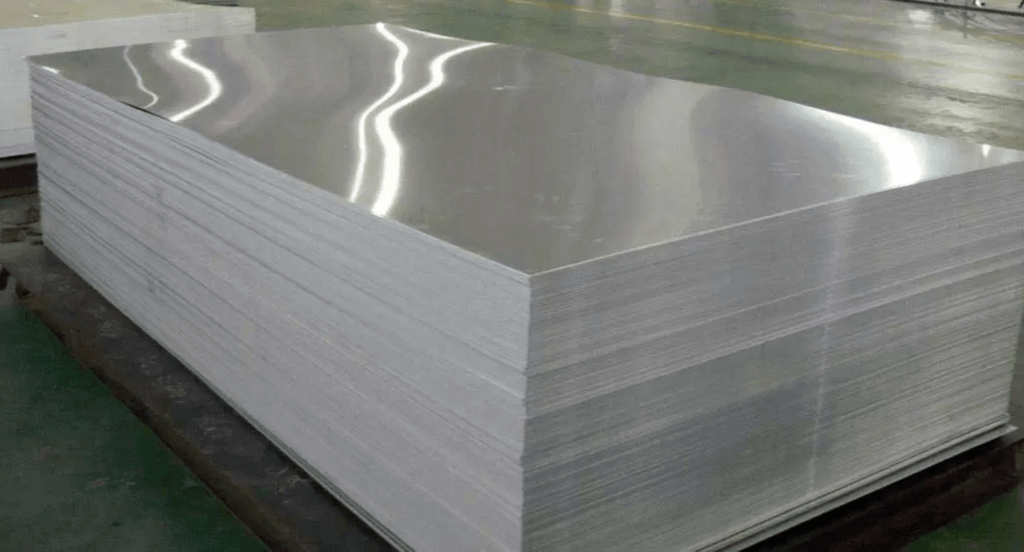
Alloy 5052
Alloy 5052 is renowned for its strength and excellent fatigue resistance, making it a preferred choice for more rigorous bending applications. It combines aluminum with magnesium, offering better corrosion resistance than many other alloys. This alloy is often used in marine environments and is suitable for applications requiring high strength after bending.
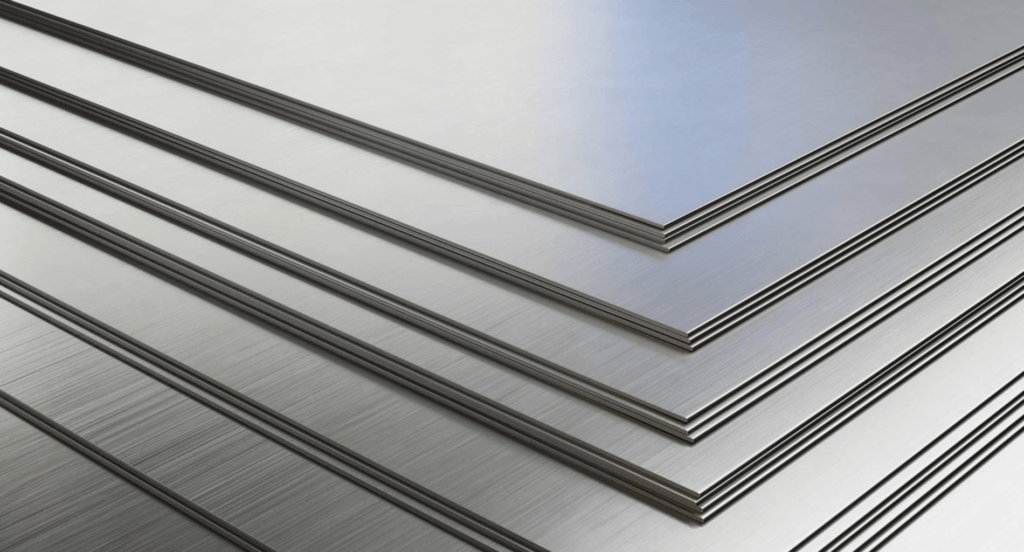
Alloy 7075
Alloy 7075 is one of the strongest aluminum alloys available, primarily used in applications where strength is more critical than the ability to bend. While it offers less bendability compared to other alloys, its high zinc content provides exceptional strength and makes it ideal for aerospace and military applications. This alloy is suitable for bending operations where high stress tolerance is required post-bending.
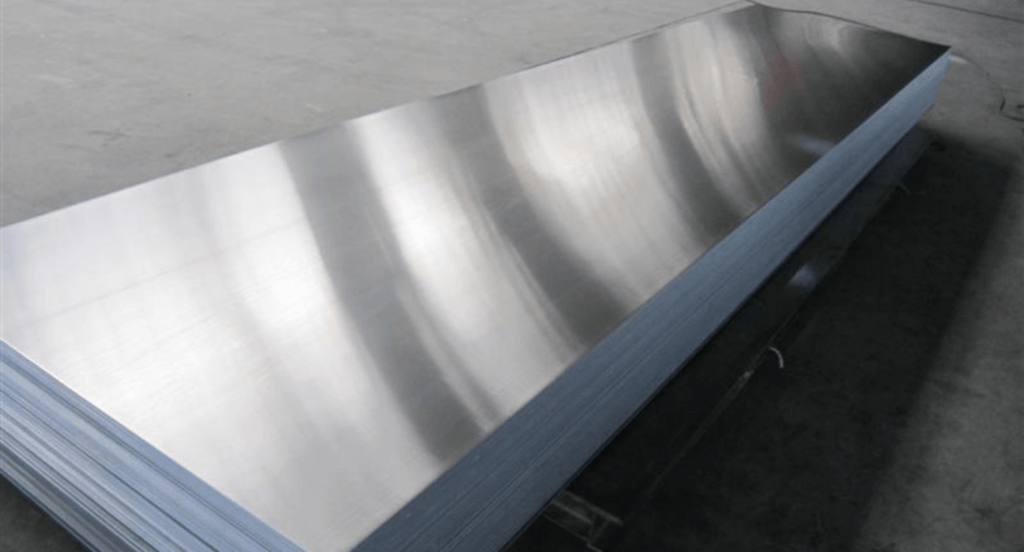
3. Tools and Equipment for Bending Aluminum Sheet Metal
Having explored the types of aluminum alloys, appropriate tools and equipment for bending is vital to achieve precise and effective bending. Here are the essential tools and equipment needed:
Angle Benders
Angle benders are specialized tools designed for creating precise angular bends in aluminum sheet metal. They are particularly effective for small-scale projects or detailed work where specific angles are crucial. These benders offer a combination of precision and ease of use, making them a valuable asset in workshops focusing on custom designs and prototypes.
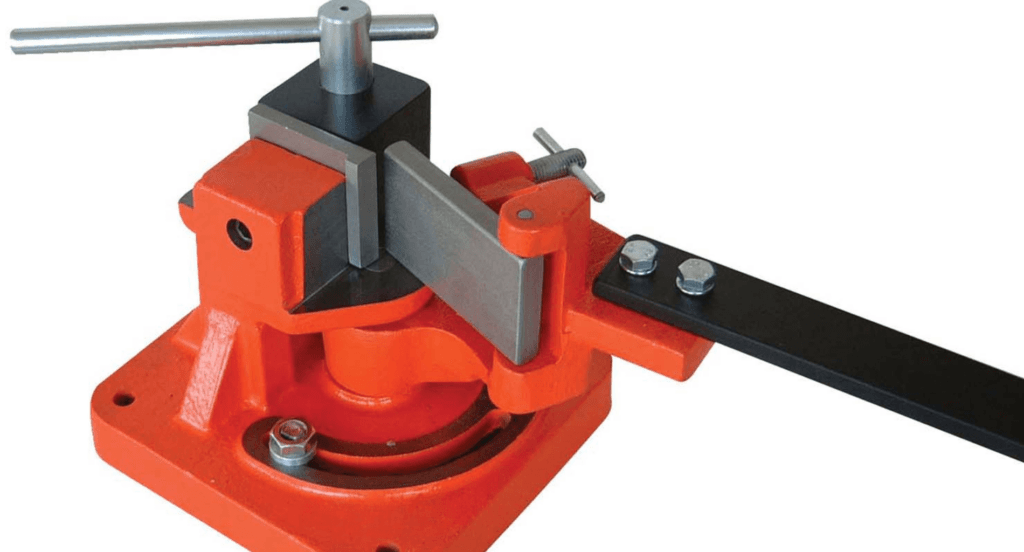
Rotary Bending Machines
Rotary bending machines are versatile tools that enable smooth and consistent bending while preserving the surface quality. They excel at handling delicate aluminum sheets where maintaining surface integrity is a priority. Ideal for medium to high-volume production, these machines ensure a high-quality finish along with uniform bending.
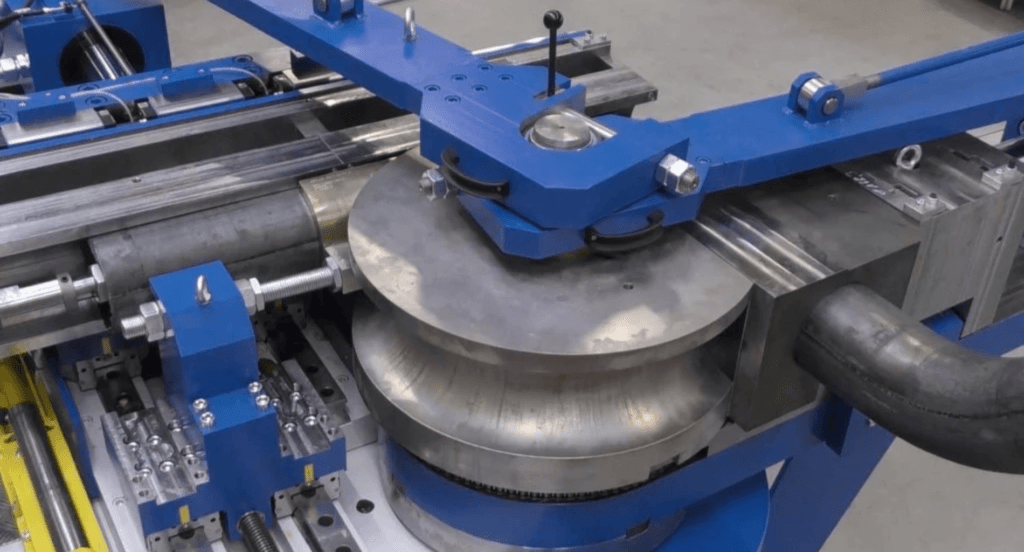
Edge Bending Tools
Edge bending tools are designed for creating clean bends along the edges of aluminum sheets, which is essential in fabricating panels and boxes. They allow for tight control over the bending process, guaranteeing sharp and precise edges. These tools are essential in projects where the accuracy of edges is crucial for both functionality and appearance.
Panel Benders
Panel benders are advanced equipment capable of handling large sheets of aluminum, making them ideal for fabricating large panels and enclosures. They offer high efficiency and consistency, especially beneficial for industrial applications requiring large-scale production with uniform quality. Their capacity to work with large material sizes makes them a crucial part of heavy fabrication industries.
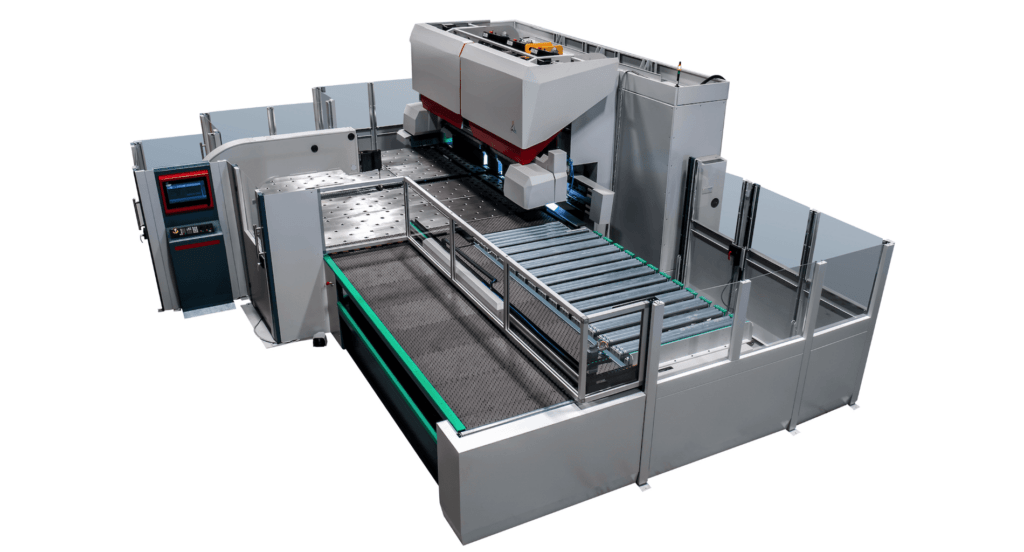
4. Bending Techniques and Methods
Shifting from tools and equipment, the focus moves to the methods of bending aluminum sheet metal, vital for achieving specific shapes and designs. Here are some of the bending techniques:
Cold Bending
Cold bending is a method where aluminum sheet metal is bent at room temperature, preserving its original strength and grain structure. This technique is ideal for creating sharp, precise angles without the risk of changing the metal’s properties. It is commonly used in applications where structural integrity is essential.
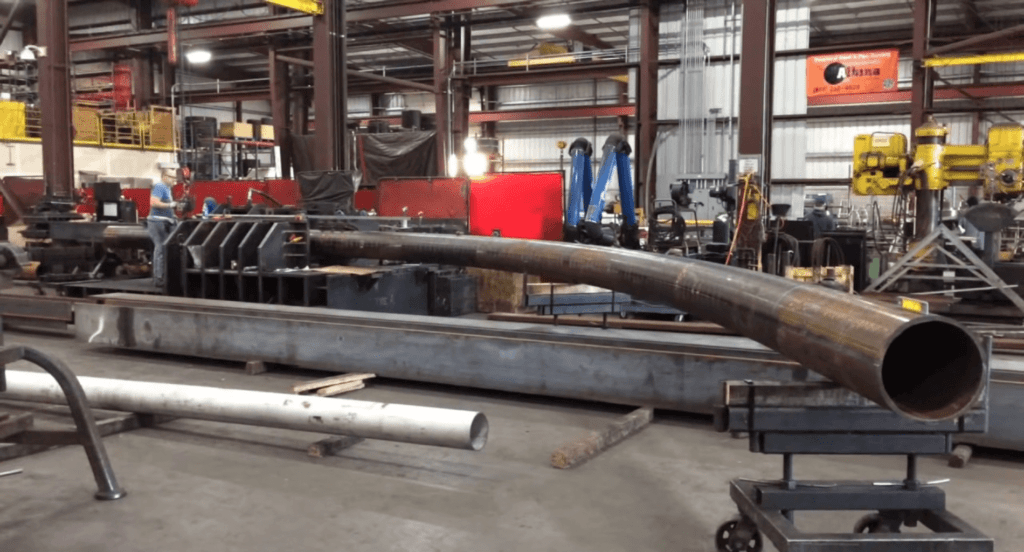
Hot Bending
In hot bending, the aluminum sheet metal is heated to a specific temperature before bending, making it easier to shape. This method allows for more complex shapes and curves, reducing the risk of cracking or breaking the metal. It’s particularly useful for detailed designs and where tight curves are required.
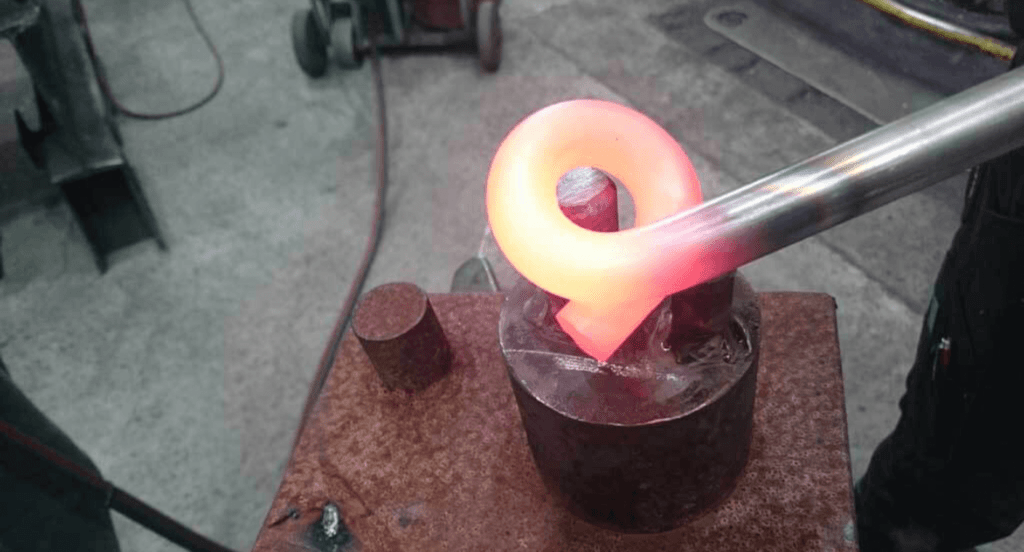
Rotary Draw Bending
Rotary draw bending involves pulling the metal around a rotating bend die to achieve the desired curve. This technique is highly precise, making it suitable for applications requiring consistent, tight-radius bends. It’s widely used in the automotive and aerospace industries.
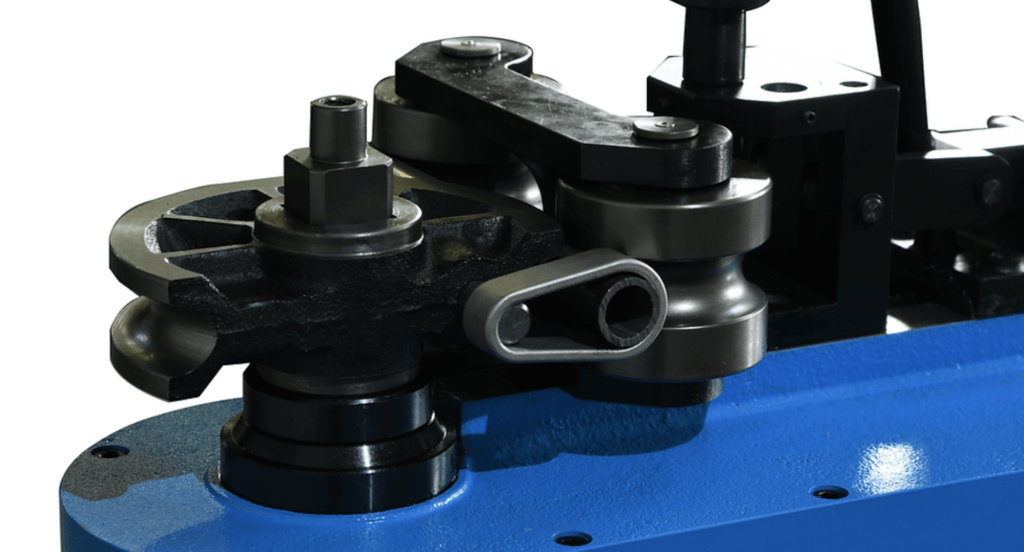
Three-Point Bending
Three-point bending, also known as flexure bending, applies force at a single central point while the metal is supported at two ends. This method is effective for creating gentle, uniform curves and is often used in architectural and decorative applications. At Zemetal, we utilize this technique to ensure precision and aesthetic excellence in our projects.
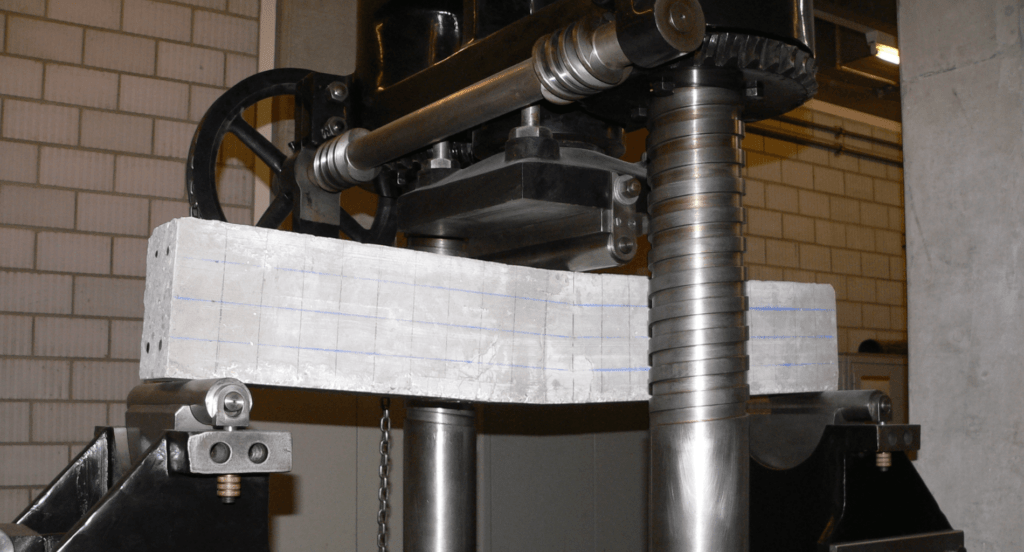
5. Finishing and Post-Bending Treatments
Moving beyond bending techniques, the focus shifts to the finishing and post-bending treatments, essential for enhancing the durability and function of aluminum sheet metal. Here are the vital treatments:
Electroplating
Electroplating is a crucial finishing technique where a metal layer, often zinc or nickel, is electrically bonded to the surface of bent aluminum. This process not only increases the metal’s resistance to corrosion and wear but also can add electrical conductivity. Electroplating is particularly important in extending the lifespan and maintaining the functional integrity of aluminum parts in extreme environments.
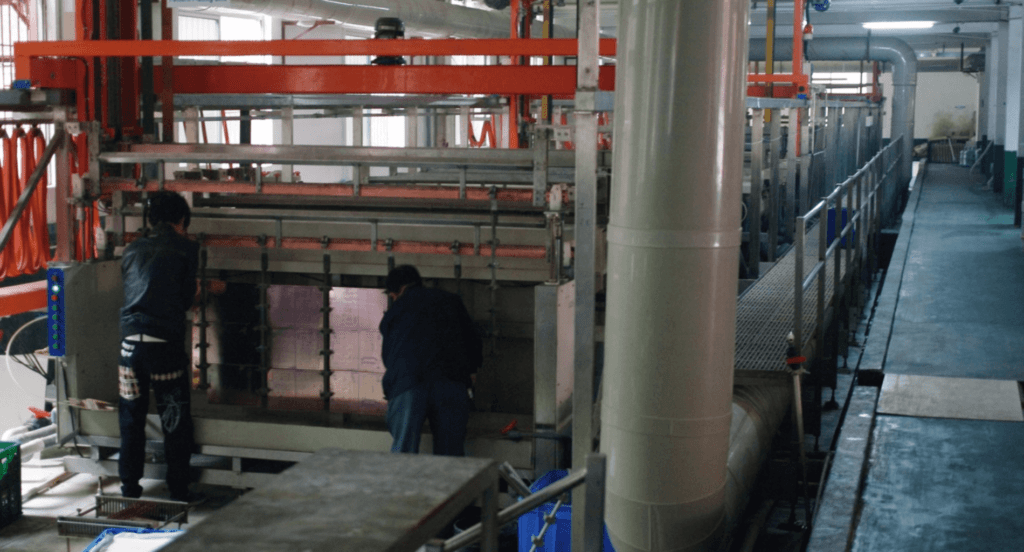
Chemical Finishing
Chemical finishing, including chromate conversion coating, is vital in providing additional surface protection for aluminum sheet metal. This process involves a chemical reaction that creates a protective layer on the metal’s surface, enhancing its corrosion resistance and paint adhesion. It is especially beneficial for outdoor applications where exposure to the elements can cause harm.
Deburring
Deburring involves the removal of sharp edges or burrs created during the bending process. This is achieved using mechanical methods like grinding, sanding, or using specialized deburring tools that carefully shave off the unwanted material. The process ensures a smooth, uniform finish on the metal, enhancing both safety during handling and the overall aesthetic of the final product.
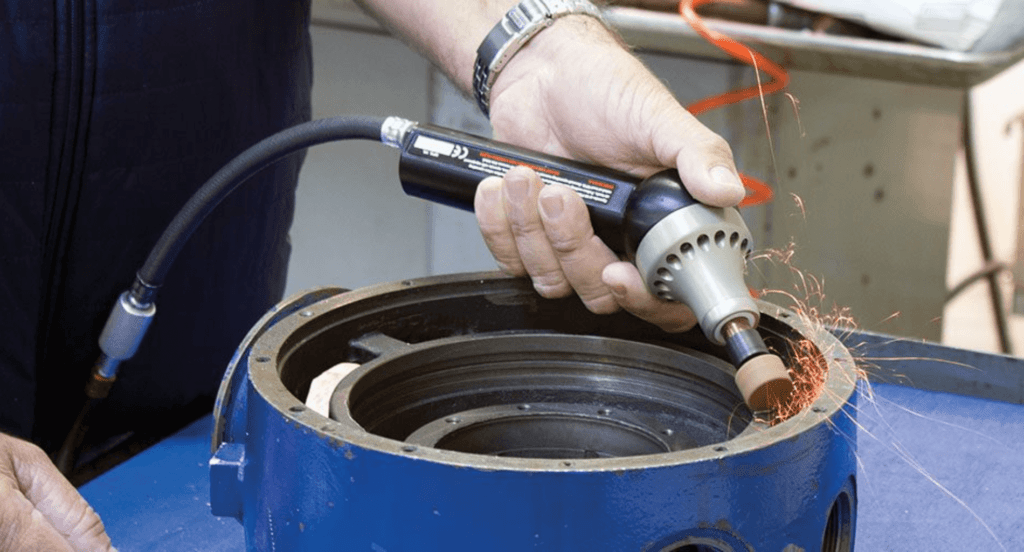
Ultrasonic Cleaning
Ultrasonic cleaning is a finishing treatment that uses high-frequency sound waves to clean bent aluminum sheet metal, effectively removing contaminants, residues, and particles ensuring a spotless surface. Grand View Research predicts 6.8% CAGR in ultrasonic cleaning from 2023 to 2030 due to rising demand for precision cleaning. It’s crucial in medical and food industries where cleanliness matters.
6. Applications of Bent Aluminum Sheet Metal
After understanding the finishing treatments available, the versatility of bent aluminum sheet metal is showcased with its application in various industries. Here are some of those sectors:
Energy Sector
The energy sector, particularly in renewable energy like solar and wind power, utilizes bent aluminum sheet metal in various components. In solar panels, it’s used for framing and mounting structures, while in wind turbines, it’s essential for creating internal supports and housings. Its resistance to corrosion and environmental stressors makes it ideal for these outdoor applications.
Industrial Machinery and Equipment
Bent aluminum sheet metal is a key component in industrial machinery and equipment, valued for its durability and light weight. For example, it’s used in creating protective housings, panels, and structural parts of machines, aiding in reducing overall machine weight without sacrificing strength. Its thermal conductivity also makes it suitable for heat exchange systems and components.
Automotive and Transportation
In the automotive and transportation industries, bent aluminum sheet metal plays a crucial role in enhancing fuel efficiency and reducing vehicle weight. It’s extensively used in the manufacturing of body panels, frames, and structural components, contributing to the overall durability and performance of vehicles. Its recyclability also supports the industry’s shift towards more sustainable practices.
Aerospace and Aviation
The aerospace and aviation sectors heavily rely on bent aluminum sheet metal for constructing airframes, fuselage, and wing structures of aircraft. Its combination of lightness and strength is essential for ensuring fuel efficiency and structural integrity in aircraft. The material’s ability to withstand extreme temperatures and pressures further showcases its importance in these high-demand applications.
7. 4 Factors When Considering Aluminum Sheet Metal Bending Services
Transitioning from its diverse applications, it’s vital to consider factors when selecting the right service to ensure the final product meets project’s specific needs. Here are critical factors to take note of:
#1 Experience and Expertise
The experience and expertise of the bending service are essential. Look for a company with a proven track record in bending aluminum sheet metal, as they are more likely to understand the details of different alloys and possess the skills needed to execute complex bending projects with precision.
#2 Quality Assurance and Compliance Standards
Ensure the service adheres to high-quality standards and compliance with industry regulations. This includes certifications and quality control processes that guarantee the bending services meet the necessary safety, durability, and performance requirements for the specific application. Zemetal sets industry standards with meticulous approach in every project, ensuring compliance.
#3 Technology and Machinery Used
The technology and machinery utilized in aluminum sheet metal bending are crucial for ensuring precision and quality. For example, CNC (Computer Numerical Control) machines offer precise bending, consistent replication, and efficient handling of complex designs. Selecting service with the latest technology ensures that the bending needs are met with utmost accuracy and efficiency.
Below is a table highlighting key technologies and machinery used in aluminum sheet metal bending, emphasizing their roles in achieving precision and quality.
#4 Customization and Flexibility
Choose a service that offers customization and flexibility in their bending processes. This includes the ability to work with various thicknesses, bend curves, and aluminum alloys, as well as accommodating unique design specifications and last-minute changes. Flexibility in service indicates a willingness to tailor their approach to your specific requirements.
Conclusion
Navigating through the comprehensive world of aluminum sheet metal bending showcases a blend of skill, precision, and technical knowledge essential in the fabrication industry. This guide has shed light on key techniques and insights, empowering you with the right knowledge to elevate your fabrication projects.
For businesses looking to improve their product offerings through advanced bending aluminum sheet metal, Zemetal offers the ideal partnership. Contact us for tailored solutions to elevate your business.
Dive Deeper Into Our Resources
Looking for more diverse service options? Browse through our handpicked selections:
For some insightful reads, we’ve curated a list of recommended articles just for you:
Still haven’t found what you’re looking for? Don’t hesitate to contact us. We’re available around the clock to assist you.