Are you wondering how flash chrome plating can elevate the quality of your metal products? This technique enhances durability and overall excellence, going beyond surface appeal.
With years of experience and deep knowledge, we understand the transformative impact of flash chrome plating on product quality and industrial efficiency. Trust us for actionable industry insights.
Flash chrome plating is not merely a finishing touch; it’s a critical enhancement that offers both aesthetic and functional benefits to metal products. This process ensures superior strength and a stylish finish, essential for high-quality manufacturing.
In this guide, we will explore the ins and outs of flash chrome plating, revealing its advantages, applications, and best practices to elevate the quality and appeal of your products.
Read on for key insights into this innovative technique.
1. Overview of Flash Chrome Plating
Flash chrome plating is a precise process that applies a thin layer of chromium onto metal objects, enhancing their durability and visual appeal. This method, integral in modern manufacturing, is notable for its ability to create a hard, protective surface for various metals. The outcome is a stylish, shiny finish that not only looks good but also extends the lifespan of the metal components.
This process is highly valued for its adaptability, finding applications in numerous industries. It stands out for delivering a consistently smooth and even coating, critical for parts where precision is essential. Flash chrome plating represents a perfect blend of aesthetic quality and practical utility, making it a vital technique in the field of metal fabrication.
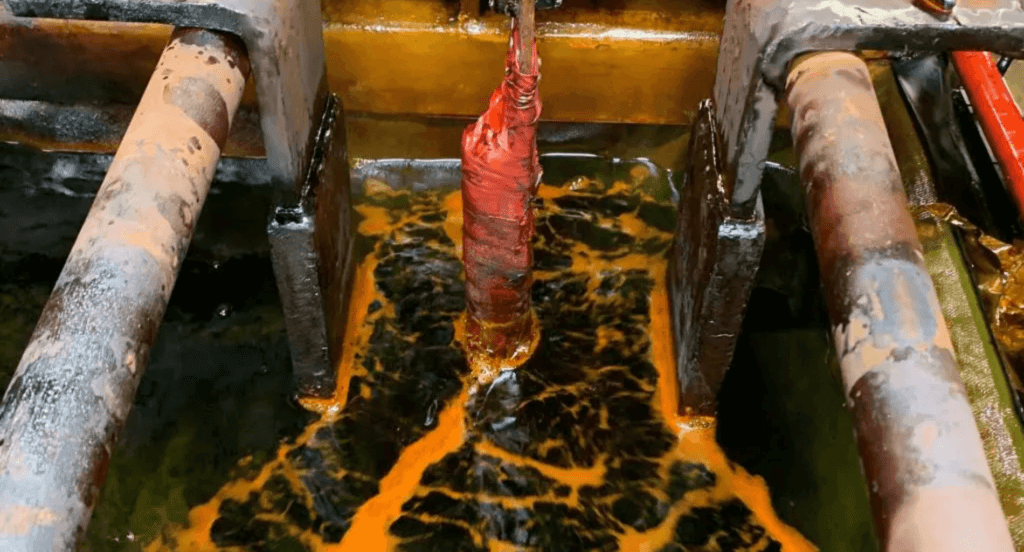
2. Benefits of Flash Chrome Plating
Building on the overview of flash chrome plating, it’s clear that this process offers various benefits for a wide range of applications. Here are its key advantages:
- Resistance to High Temperatures: Flash chrome plating offers exceptional resistance to high temperatures, making it ideal for components used in heat-intensive environments. It preserves component integrity and function under extreme heat, crucial in aerospace manufacturing.
- Improved Durability and Wear Resistance: Flash chrome plating is renowned for its ability to significantly enhance the strength of metal components. By adding a thin yet hard layer of chromium, it reduces wear and tear, making it an ideal solution for high-stress parts, extending product lifespan.
- Electrical Conductivity: Its conductivity properties are particularly beneficial in the electrical and electronics industries.This process can improve the electrical conductivity of components, making it a popular choice for applications that require efficient energy transmission and reduced resistance.
3. Flash Chrome Plating Techniques
After exploring the benefits of flash chrome plating, it’s vital to understand the various techniques that make these advantages possible. Here are some key methods employed in flash chrome plating:
Rack Plating
Rack plating involves attaching components to a metal rack, which is then submerged in the plating solution. This method is ideal for larger or more complex parts, allowing for uniform coating and reducing the risk of defects. It ensures precise control over the plating process, crucial for parts that require consistent quality and appearance.
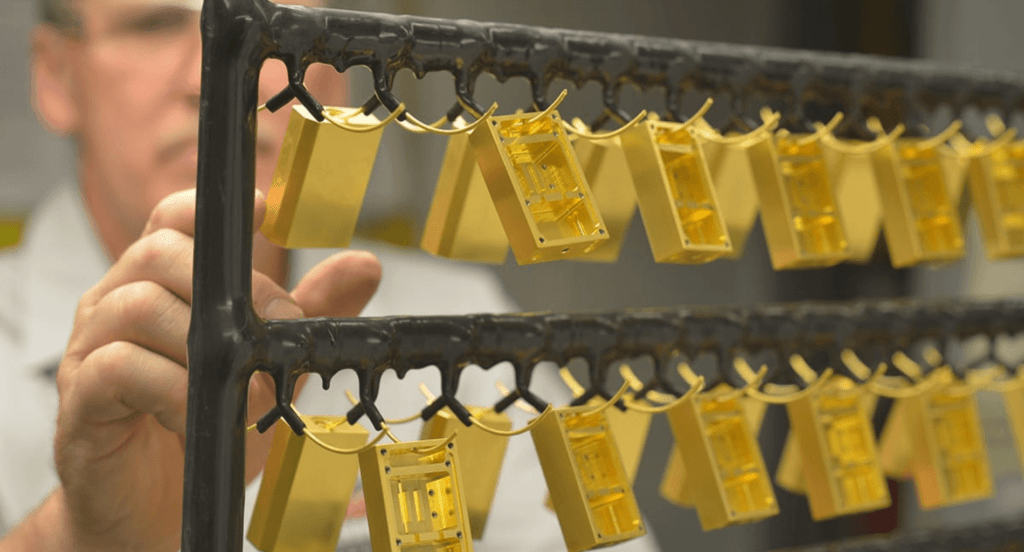
Barrel Plating
Barrel plating is used for smaller, more durable parts, involves placing components in a rotating barrel with the plating solution to achieve uniform coverage. This is efficient for high-volume production, offering a cost-effective solution for plating numerous small parts simultaneously while maintaining quality. It’s a great choice for those who value both efficiency and uniformity in their plating processes.
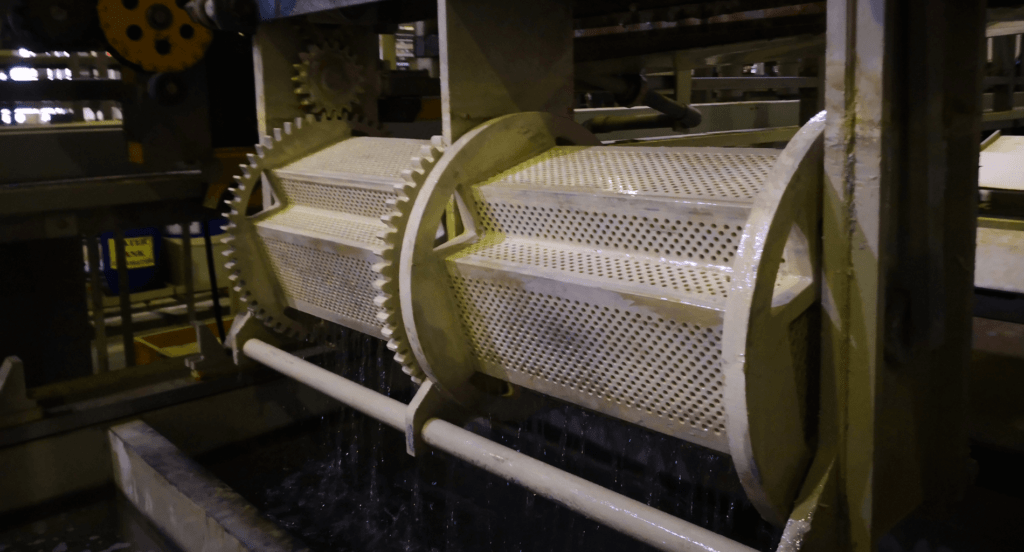
Selective Brush Plating
Selective brush plating is a precision technique where a brush soaked in plating solution is used to apply chrome to specific areas of a metal component. It’s perfect for repairs, touch-ups, or precise chrome plating of specific metal parts in custom or complex metalwork. Utilizing such specialized techniques, Zemetal prides itself on delivering tailored and high-quality chrome plating solutions.
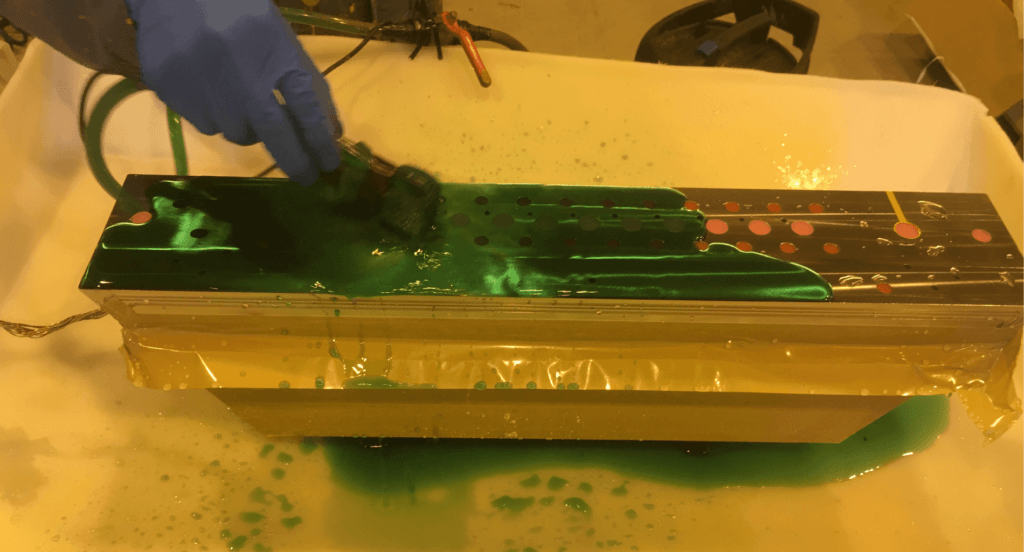
Hot Dip Plating
Hot dip plating involves dipping the metal component in molten chromium, creating a strong and thick chrome layer. This method is suited for metals requiring a heavy-duty protective coating, offering exceptional corrosion resistance and durability. It’s a preferred technique for industrial metal components exposed to harsh environments.
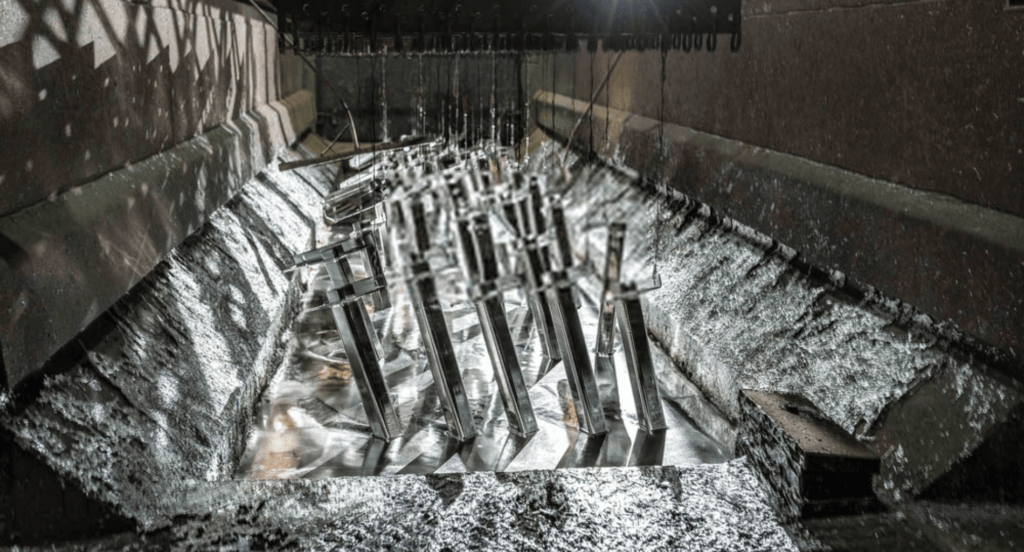
4. The Flash Chrome Plating Process
Followed by the various techniques, it’s vital to dive into the actual process itself. These steps expertly convert raw metal into a shiny chrome-plated finish. Here are the key steps involved:
Step#1 Surface Preparation
The inital step in flash chrome plating involves thorough cleaning of the metal surface. This typically includes degreasing, to remove any oils or contaminants, and may involve mechanical or chemical cleaning methods to ensure a clean, smooth surface. Proper surface preparation is crucial as it affects the adhesion and overall quality of the final chrome layer.
Step#2 Base Layer Application
Before the actual chrome plating, a base layer is often applied to enhance the adhesion of the chrome. This layer could be made of materials like copper or nickel. The choice of the base layer depends on the properties desired in the final product, such as increased corrosion resistance or enhanced bonding strength.
Step#3 Electroplating Process
In the electroplating process, the metal workpiece is submerged in a chromic acid solution and used as the negative electrode. A current is passed through the solution, causing chromium ions to deposit on the workpiece’s surface. The duration and strength of the current dictate the thickness and quality of the chrome layer.
Step#4 Thickness Control and Quality Check
Controlling the thickness of the chrome layer is a critical aspect of flash chrome plating. This is achieved by adjusting the electroplating time and monitoring the current density. After plating, the thickness is measured, often using non-destructive testing methods, to ensure it meets specific industry standards.
Step#5 Post-Plating Treatments
After the chrome layer is applied, post-plating treatments such as rinsing, drying, and polishing are performed. Rinsing removes any residual chemicals, while drying is crucial to prevent water spots or corrosion. Polishing enhances the aesthetic appeal of the chrome finish, giving it a characteristic shine.
Step#6 Final Inspection and Quality Assurance
The final step involves a comprehensive inspection to ensure the quality of the chrome plating. This may include visual inspections for uniformity and defects, as well as tests for adhesion, corrosion resistance, and hardness. Only after passing these strict quality checks is the product considered ready for use or shipment.
5. Applications of Flash Chrome Plating
Moving beyond the detailed process, its versatility becomes evident considering its wide range of applications in various industries. Here are some distinct sectors that greatly benefit from this:
Marine Industry
In the marine industry, flash chrome plating is extensively used on ship components such as propellers and shafts. The process provides a crucial barrier against saltwater corrosion, essential for maintaining structural integrity and longevity in harsh marine environments.
Construction Equipment
Flash chrome plating is essential, given the projected 6% CAGR growth in construction equipment from 2023 to 2032, as per Precedence Research. It offers enhanced wear resistance, critical for equipment like hydraulic pistons and heavy-duty machinery parts subjected to abrasive and tough conditions on construction sites. This extends the operational life and reliability of construction machinery.
Textile Machinery
In the textile industry this is primarily used on components such as loom needles and rollers. It provides these parts with the necessary resistance to wear and friction, essential in the continuous and high-speed operations of textile manufacturing. Zemetal’s expertise in flash chrome plating guarantees optimal performance of textile components.
6. Flash Chrome Plating vs. Traditional Chrome Plating
Transitioning from its diverse applications, the focus shifts to uncovering the unique characteristics that set this method apart from traditional chrome plating. Here are the key differences:
Thickness and Application
Flash chrome plating involves a thinner layer of chromium compared to traditional chrome plating. This thinner coating means quicker processing times and is ideal for parts that require a delicate balance between aesthetic appeal and functional durability. In contrast, traditional chrome plating, with its thicker layer, is better suited for parts that need more protection and can accommodate the increased size.
Cost Efficiency
Flash chrome plating is more cost-effective due to the reduced amount of chromium used and the faster processing time. This makes it a go-to option for projects requiring a high-quality finish without significant cost implications. Traditional chrome plating, on the other hand, with its higher material and labor costs, is often reserved for specialized applications where the thicker coating is necessary.
Maintenance and Longevity
In terms of maintenance, flash chrome plating is easier to maintain due to its smoother and non-absorbent surface, which is less prone to accumulating dirt and grime. However, traditional chrome plating, with its thicker layer, typically offers a longer lifespan, especially in harsh environments, may require more meticulous maintenance to preserve its appearance over time.
Wear Resistance
While both methods improve wear resistance, the thicker layer in traditional chrome plating offers greater protection against abrasion and corrosion. This makes it suitable for heavy-duty applications where durability is crucial. Flash chrome plating, though less resistant to extreme wear conditions, provides sufficient protection for most general applications, along with a more attractive finish.
7. Quality Control in Flash Chrome Plating
Bridging the insights between flash chrome plating and traditional chrome plating, the emphasis on quality control in the flash chrome plating becomes vital. Here are the key aspects:
Surface Defect Analysis
Before and after the flash chrome plating process, a detailed analysis of the metal surface for any defects is essential. This involves inspecting for pits, bumps, or irregularities that could affect the plating quality. Utilizing advanced imaging techniques, this ensures the base material is in optimal condition for plating and confirms the integrity of the final finish.
Salt Spray Testing
Salt spray testing is a rigorous method used to assess the corrosion resistance of flash chrome-plated surfaces. In this test, the plated components are exposed to a highly corrosive salt mist environment for a predetermined period. The duration of resistance before signs of corrosion appear is measured, providing a quantitative assessment of the plating’s durability against environmental factors.
Hardness Testing
Hardness testing is essential to determine the mechanical strength of the chrome plating. For example, Vickers hardness test is used to measure the resistance of the plated layer to changes in shape or damage. The hardness level indicates the wear resistance and durability of the chrome-plated layer, which is critical for components used in high-stress applications.
ISO 9001 Compliance
Adherence to ISO 9001 standards is a comprehensive approach to quality control in flash chrome plating. This international standard focuses on various aspects of quality management and operational procedures. Compliance with ISO 9001 ensures systematic quality control throughout the plating process, from raw material handling to the final inspection of the plated components.
The table below outlines the key aspects of ISO 9001 standards as applied to the flash chrome plating process, emphasizing the comprehensive nature of quality control measures.
ISO 9001 Aspect | Application in Flash Chrome Plating |
Quality Management System | Ensures structured processes from material to final inspection |
Customer Focus | Aligns plating services with customer requirements |
Continuous Improvement | Promotes ongoing enhancements in plating efficiency and quality |
Process Approach | Integrates all steps of plating for consistent quality |
Evidence-based Decision Making | Utilizes data from plating outcomes to inform practices |
8. 4 Tips for Maintaining Chrome-Plated Surfaces
The quality control measures used during the creation of flash chrome-plated surfaces is as vital as ensuring its longevity and appearance. Here are key tips to help maintain these surfaces effectively:
#1 Routine Cleaning
Regular cleaning is key to maintaining the shine and preventing buildup on chrome-plated surfaces. Use a soft cloth and mild soap solution to gently wipe the surface, avoiding abrasive materials that could scratch the chrome. This simple practice can significantly prolong the aesthetic appeal and structural integrity of the chrome plating.
#2 Avoiding Harsh Chemicals
It’s crucial to avoid harsh chemicals and solvents when cleaning chrome-plated surfaces. These substances can cause damage, leading to dullness and corrosion over time. Instead, opt for pH-neutral cleaners that are specifically designed for chrome to ensure that the surface remains in excellent condition and prevent any damage.
#3 Immediate Repair of Damages
In case of damage, like scratches or chips, quick repair is essential. For example, a chrome-plated hydraulic rod that gets scratched can significantly compromise its function and durability. Ignoring minor damages can lead to more significant issues, such as rust formation or plating peel-off. Professional repair or re-plating services can restore the surface to its original condition, ensuring its longevity.
#4 Proper Handling and Usage
Careful handling and usage of chrome-plated items are essential to prevent physical damage. Avoid dropping or placing heavy objects on chrome-plated surfaces, and ensure that they are used as intended. Proper handling can significantly reduce the risk of scratches and dents, keeping the chrome finish in best condition.
Conclusion
Flash chrome plating represents a significant advancement in metalworking techniques, essential for those seeking superior quality and durability in metal products. This guide has provided valuable insights, equipping you with the knowledge to make informed decisions about improving your projects.
If you’re looking to elevate your metal products with the latest in flash chrome chrome plating, Zemetal is your ideal partner. Contact us to explore how our specialized services can benefit your business.
Dive Deeper Into Our Resources
Looking for more diverse service options? Browse through our handpicked selections:
For some insightful reads, we’ve curated a list of recommended articles just for you:
Still haven’t found what you’re looking for? Don’t hesitate to contact us. We’re available around the clock to assist you.