Wet Blasting​
Dive into our selection of top-tier metal services, where unparalleled quality meets innovative design. Each item in our range is a testament to our commitment to excellence in metal fabrication.
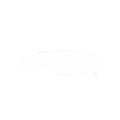
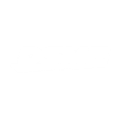
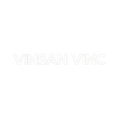
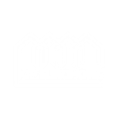
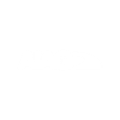
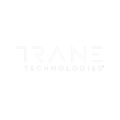
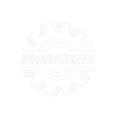
Explore Our Premium Metal Fabrication Range​
Zemetal stands at the forefront of metal fabrication, revolutionizing the industry with our advanced wet blasting technology. Our expertise in water sandblasting, a cutting-edge process, ensures a superior finish and precision on every project. This technique reduces dust and enhances efficiency, making it an ideal choice for businesses seeking environmentally friendly and health-conscious solutions.
Â
We understand the diverse needs of metal fabrication businesses, wholesalers, distributors, and small business owners. Our services cater specifically to these demands, offering tailored solutions that drive your projects forward. We believe in creating partnerships that go beyond transactions, shaping a future where your vision and our technology converge.
Zemetal: Who We Are
Our Founding Journey
Established with a vision to revolutionize the sheet metal processing industry, our journey reflects a blend of innovation, precision, and dedication. From our humble beginnings, we’ve evolved into a leader in sheet metal processing and batch production. Our success is built on a commitment to quality and relentless technological advancement, setting new standards in the industry.
Inside Our Facility
Step into our state-of-the-art factory, where advanced technology meets skilled craftsmanship. Optimally designed for efficiency, our facility is the heart of our sheet metal production. We handle intricate designs and large-scale outputs with precision, ensuring every product meets the highest quality benchmarks. Our factory is a testament to our capability to handle diverse, high-volume demands with precision.
Innovation & Development
At the core of our operation is a robust Research & Development wing, pushing the frontiers of sheet metal processing. Our R&D team, equipped with cutting-edge tools and driven by innovation, continually develops new methods to enhance efficiency and product quality. This relentless pursuit of improvement sets us apart and ensures we stay ahead in a rapidly evolving industry.
Certification Excellence
Our commitment to excellence is affirmed by our comprehensive range of industry certifications. Each certificate represents our adherence to stringent quality standards, environmental practices, and safety protocols. These certifications are a promise to our clients that every sheet metal product we deliver is crafted to perfection, adhering to the highest industry benchmarks. Trust and quality are the pillars of our service.
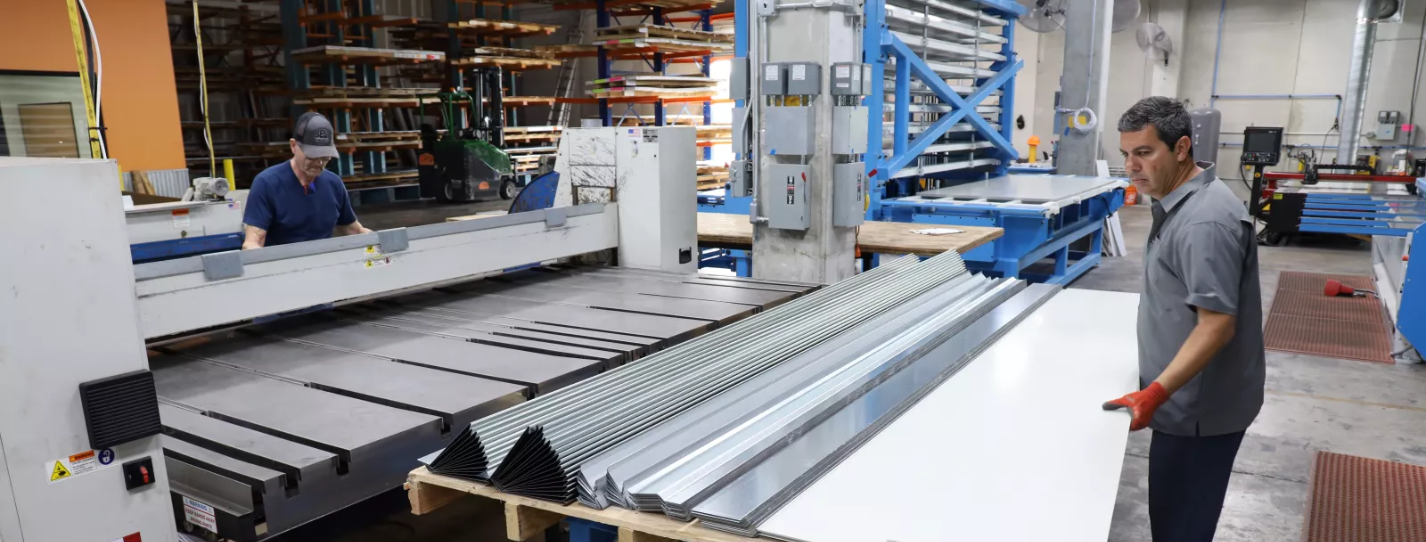
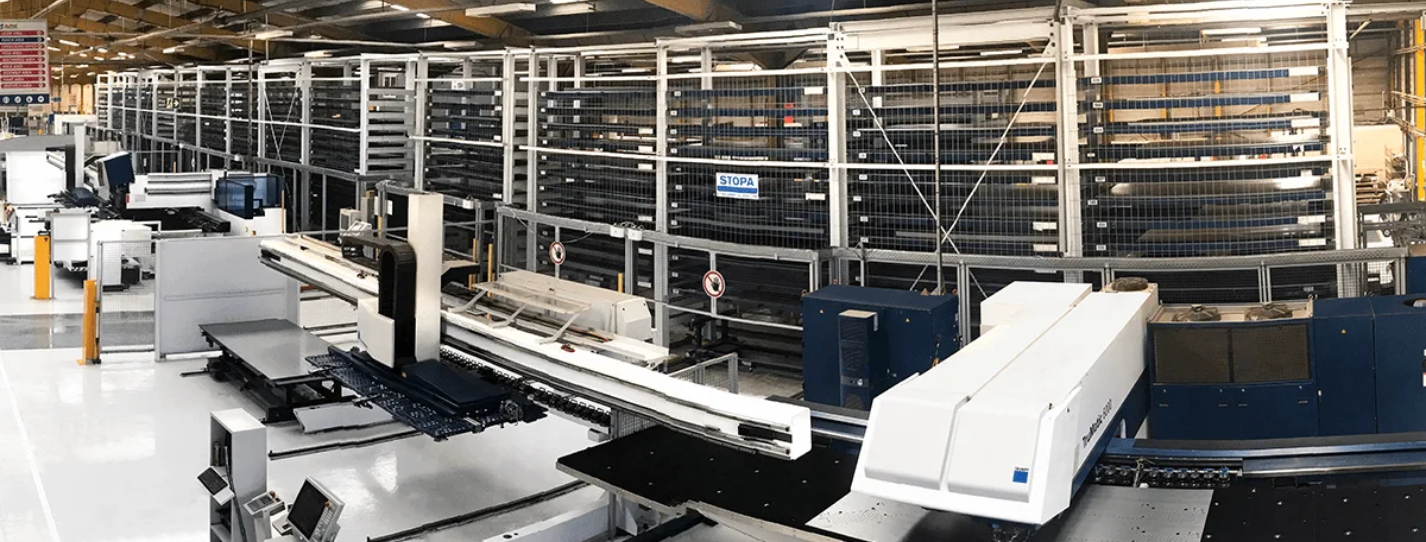
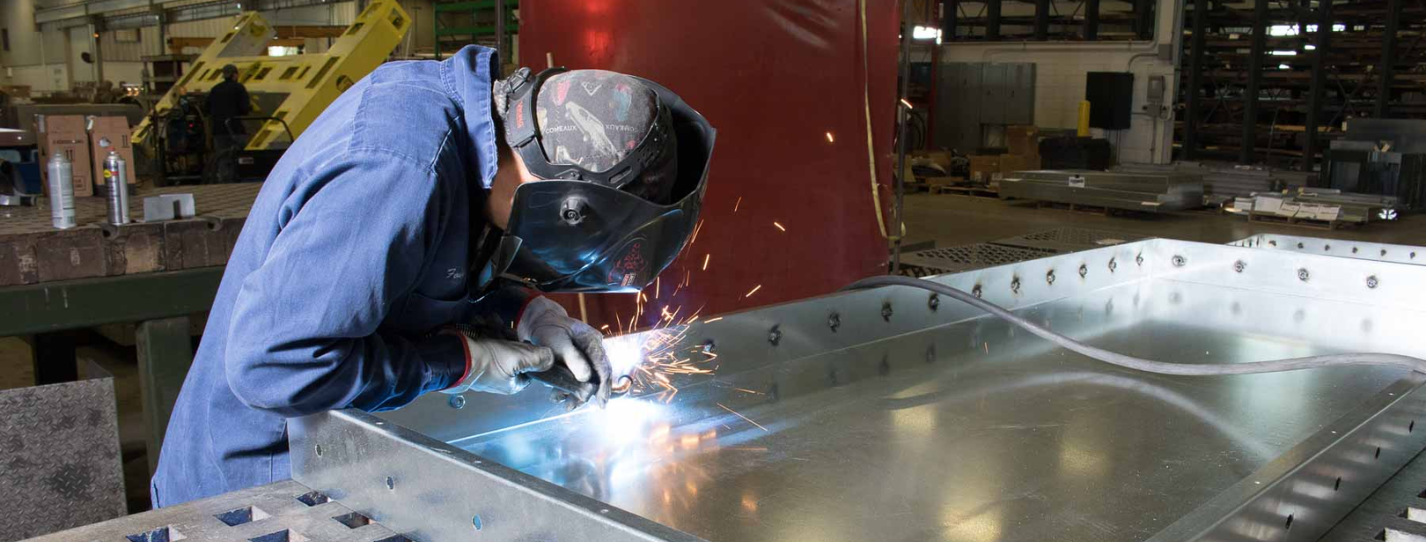
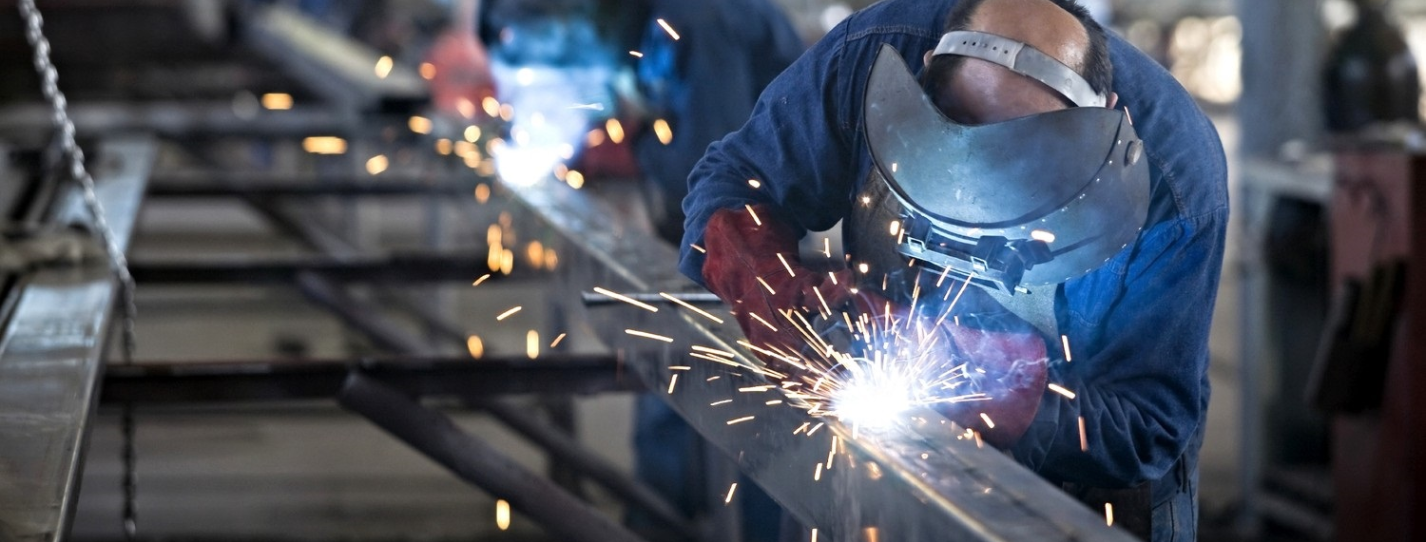
Meet the Experts Behind Zemetal
01
Media Team
For content collaborations or to join our blog contributors, please contact [email protected]. We welcome fresh perspectives and are committed to enriching our metal sheet fabrication industry platform with diverse insights. Let’s innovate together.
02
Quality Assurance Team
In our Quality Assurance Team, we meticulously ensure a 99.8% precision rate in every project, embodying our dedication to superior quality and a zero-error approach in metal sheet fabrication.
03
Research & Development Team
Leading with over 30 innovative techniques, our R&D Team enhances fabrication efficiency and precision by 25%, constantly redefining creativity and scientific accuracy in metal sheet fabrication.
04
Engineering & Design Team
Our Engineering & Design Team, with over 500 bespoke projects, expertly fuses creative design with engineering precision, ensuring each fabrication project excels in functionality and aesthetics.
Empowering Goals With Us
At Zemetal, our partnership with a pioneering electric vehicle firm is a testament to our dedication to precision, sustainability, and efficiency. Utilizing our cutting-edge fabrication skills and eco-friendly practices, we played a pivotal role in addressing critical challenges faced by Mr. Frazier's company. This collaboration resulted in a staggering 30% enhancement in vehicle performance, marking a significant milestone in our journey towards innovative excellence.
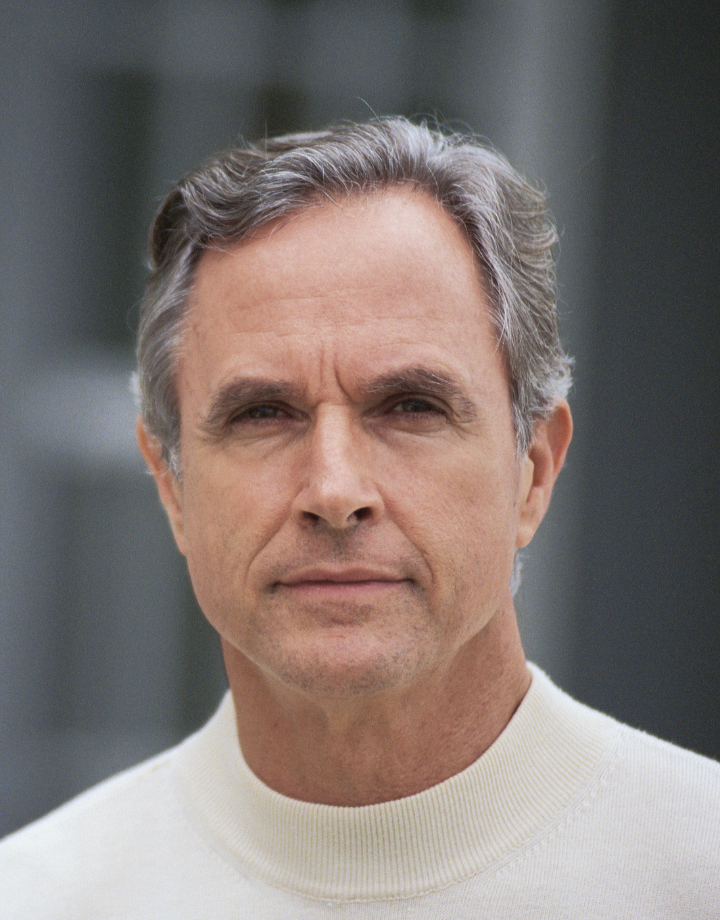
Our collaboration with Mr. Virden's HVAC company is a shining example of Zemetal's commitment to delivering bespoke metal fabrication solutions that are both innovative and efficient. By embracing and solving unique architectural challenges, we not only improved the functionality of their HVAC systems but also seamlessly integrated them into the desired aesthetics. This strategic partnership led to substantial growth for our client, showcasing the transformative impact of our tailored solutions.
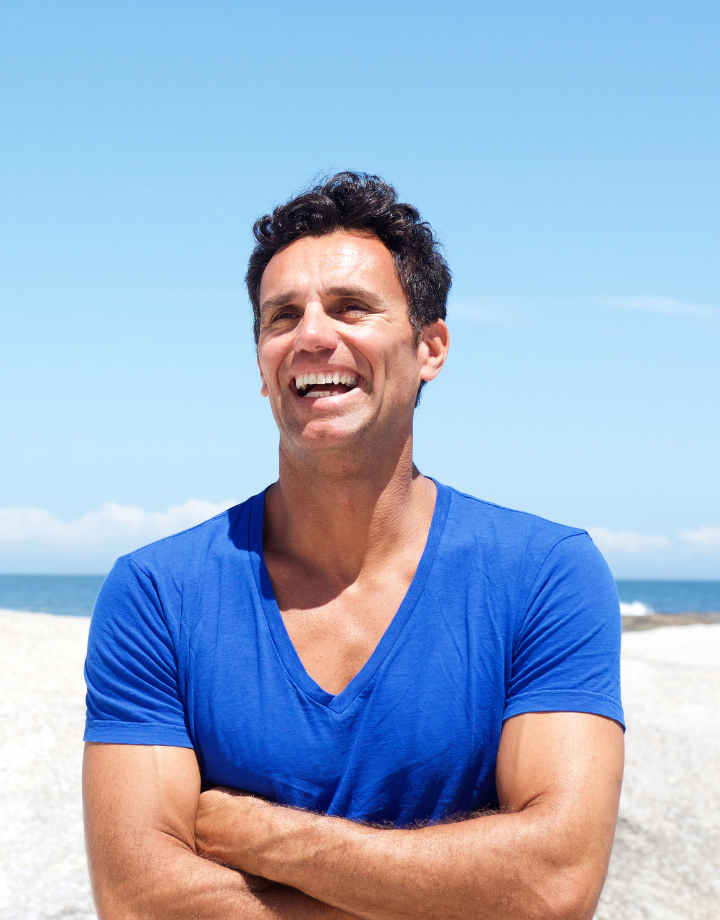
Working with Mr. Park and his team at the automotive company highlighted Zemetal's unwavering commitment to precision, innovation, and efficiency. By confronting their complex challenges with our advanced manufacturing techniques, we didn't just meet their high standards; we played a crucial role in significantly boosting their vehicle performance. This collaboration underscores our dedication to pushing the boundaries of what's possible in automotive excellence.

Previous
Next
Your Manufacturing Demands, Our Expert Solutions
Comprehensive Fabrication Services
Offering a wide range of metal fabrication services, from cutting and bending to welding and assembling, tailored
to your specific requirements.
Advanced Technology & Equipment
Utilizing state-of-the-art machinery and technology to ensure high precision and quality in every project, meeting the
most demanding manufacturing standards.
Expert Team & Quality Assurance
Our skilled professionals are committed to delivering excellence. We adhere to strict quality control protocols to
ensure top-notch results.
Flexible Production Capacity
Whether you need a single prototype or large-scale production, our flexible manufacturing processes can adapt to your project’s scale and complexity.
Timely Delivery & Customer Support
We understand the importance of deadlines. Our efficient processes and dedicated support team ensure timely delivery and ongoing communication throughout your project.
Sustainable Practices & Material Options
Committed to environmental responsibility, we offer sustainable manufacturing practices and a variety of material choices, including eco-friendly and recycled options, to meet both
your project needs and environmental goals.
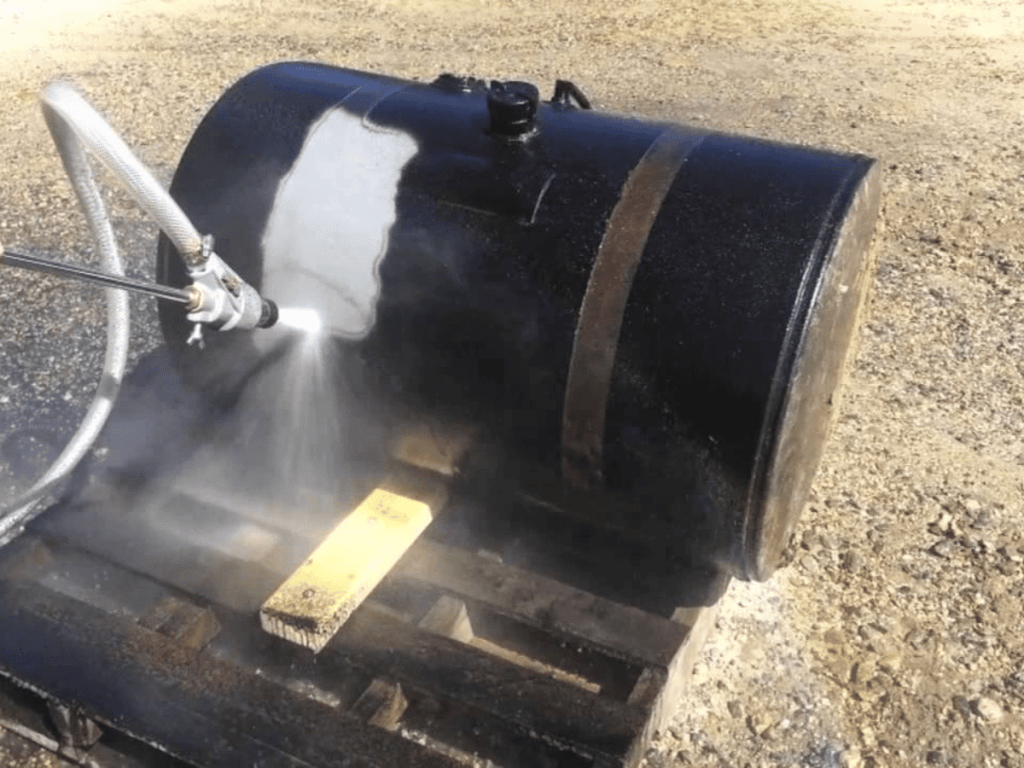
Sandblasting with Water
Sandblasting with water, a sophisticated technique highly effective in removing coatings, rust, and contaminants from various surfaces. Zemetal harnesses the power of sandblasting with water to offer unparalleled quality in metal surface treatment. This approach not only ensures a cleaner work environment but also delivers superior results compared to traditional dry blasting methods.
Applicable Materials for Wet Blasting
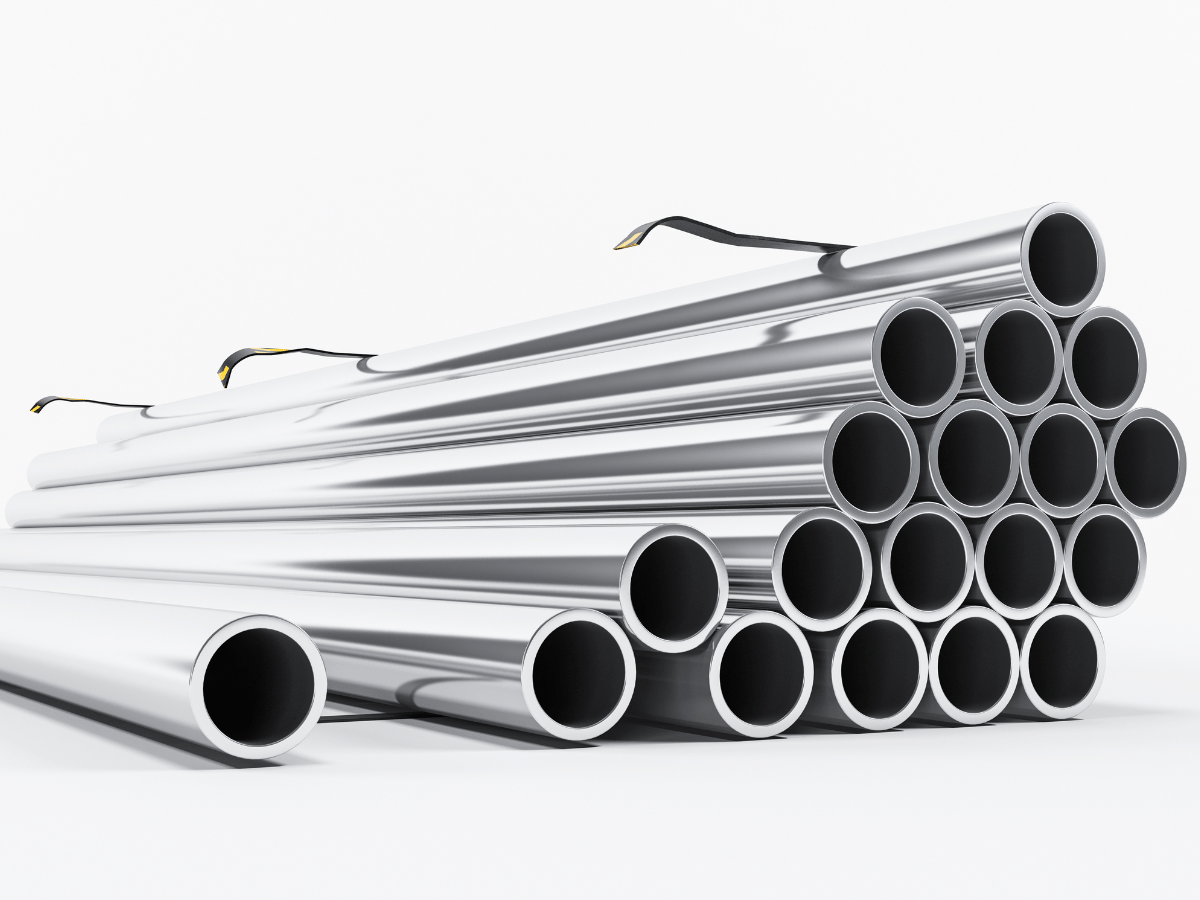
Stainless Steel
Wet blasting is highly effective on stainless steel, often used for cleaning, deburring, or to prepare surfaces for coating. The process gently removes surface contaminants without compromising the integrity of the stainless steel, ensuring a smooth and clean finish. This is crucial in applications where both aesthetics and corrosion resistance are important.
Aluminum
Aluminum benefits from wet blasting due to its softer nature compared to other metals. Zemetal’s wet blasting services can efficiently remove surface impurities, oxidation, or old coatings without inducing warping or altering the metal’s dimensional properties. This is particularly useful in the automotive and aerospace industries, where precise dimensions and surface quality are paramount.
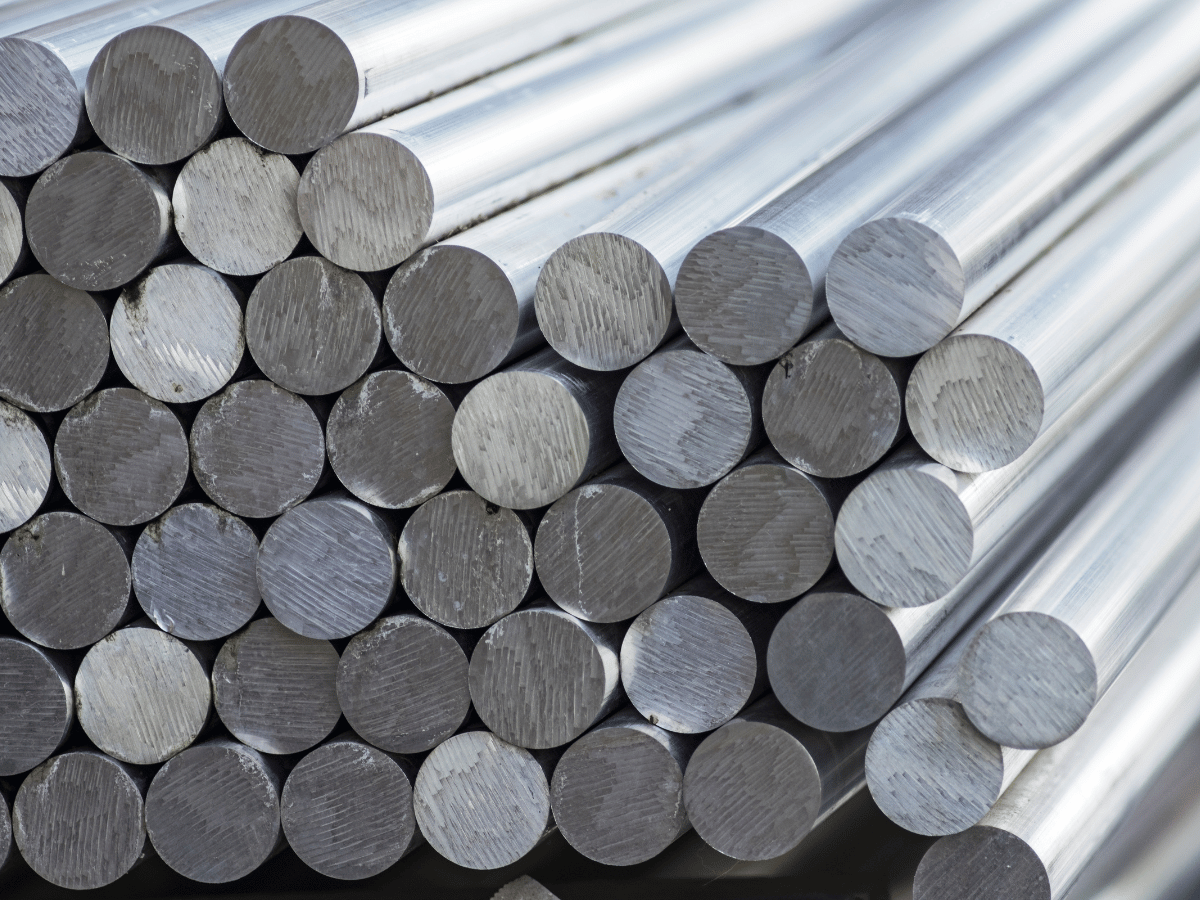
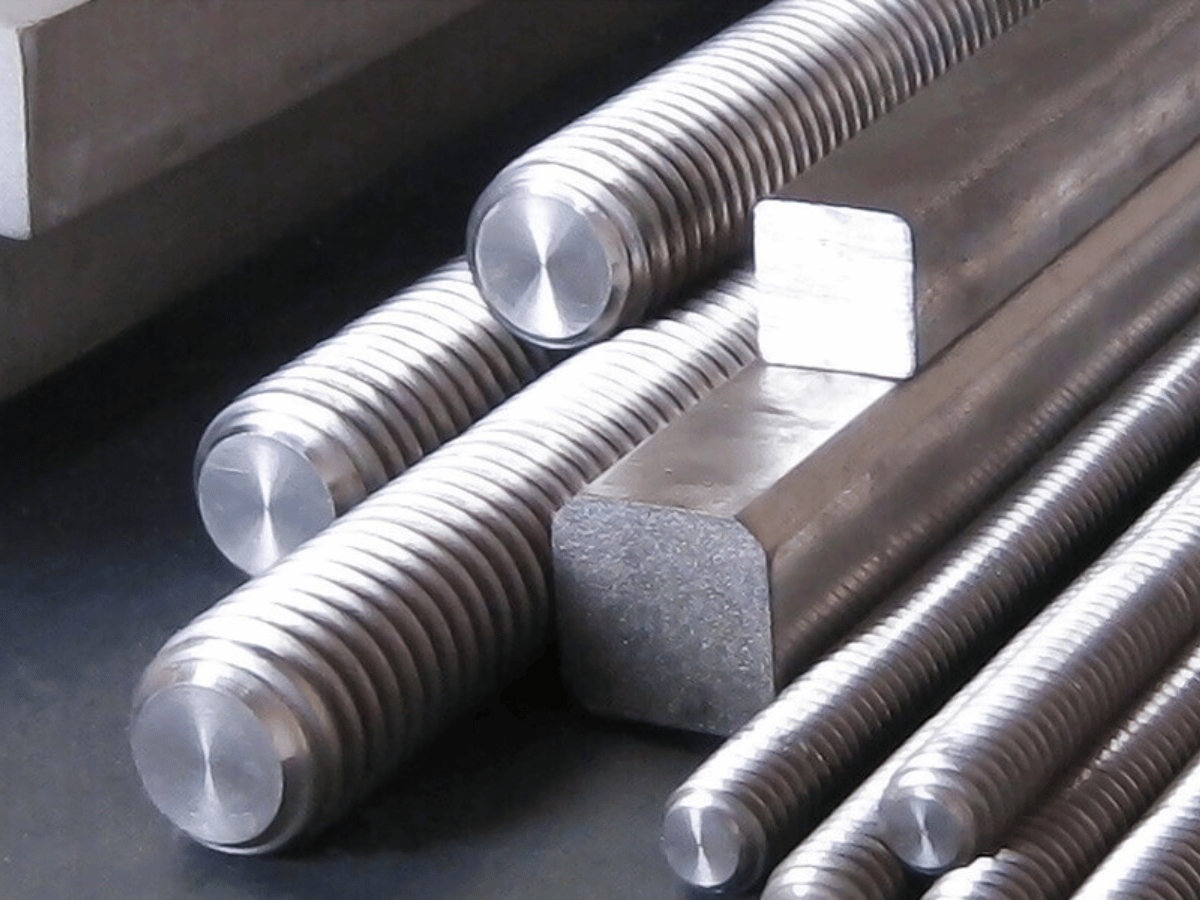
Titanium
Known for its strength and corrosion resistance, titanium is often used in high-performance and medical applications. Wet blasting can effectively clean and finish titanium surfaces, preparing them for further processing or direct use. This method ensures that the natural properties of titanium, such as biocompatibility and strength-to-weight ratio, are not adversely affected during the finishing process.
Features of Wet Blasting
Precision and Control
Wet blasting, often known as hydro sandblasting, offers exceptional precision and control. The addition of water allows for a finer and more controlled abrasive impact, enabling detailed surface finishes. This level of control is particularly beneficial for delicate or precision components.
Dust Reduction
A key feature of wet blasting service is its ability to significantly reduce dust. For instance, incorporating water into the blasting process which results to dust particles are contained and settled more effectively. This results in a cleaner working environment, which is safer for operators and reduces the need for extensive clean-up.
Versatility in Media and Pressure
Wet blasting services are versatile, accommodating a wide range of abrasive media and pressure settings. This adaptability allows it to be used on various materials, from soft metals to harder alloys. Zemetal leverages this versatility of wet blasting to achieve optimal results for different types of metal projects.
Benefits of Wet Blasting
Improved Surface Finish
One of the primary benefits of water abrasive blasting is the improved surface finish it delivers. The combination of water and abrasive media smoothens surfaces more evenly, resulting in a superior finish. This is crucial for metal parts that require a high-quality aesthetic or need to adhere to strict dimensional tolerances.
Â
Enhanced Safety and Health
Wet blasting service enhances safety and health in the workplace. The reduction of airborne dust particles minimizes respiratory hazards and improves visibility during operation. This aspect is particularly beneficial for workers’ health and contributes to a safer, more compliant work environment.
Â
Reduced Surface Warping
A significant benefit of wet blasting service is the reduced risk of surface warping. The water acts as a buffer, dissipating heat and preventing thermal distortion on metal surfaces. This is essential for maintaining the structural integrity of metal parts, especially those with thin or delicate profiles.
Application of Wet Blasting
Automotive Industry
The automotive industry heavily relies on wet blasting for preparing and finishing metal components. This service ensures a smooth surface finish essential for paint adhesion on car bodies and parts. Wet blasting is used to remove rust, old paint, and contaminants from vehicle components, enhancing their longevity. It’s crucial for manufacturing high-quality, durable automotive parts with aesthetic appeal.
Â
Aerospace Industry
In the aerospace industry, precision and safety are paramount. Wet blasting is for cleaning and finishing aircraft components, ensuring they meet strict industry standards. This method effectively removes oxides and prepares surfaces for coating, crucial for aircraft performance and safety. Zemetal offers wet blasting service in their aerospace projects, ensuring components meet the rigorous standards of the industry.
Â
Manufacturing and Metal Fabrication
Â
Wet blasting is integral in general manufacturing and metal fabrication industries. It’s used for cleaning and preparing metal surfaces before welding or coating. This process ensures that products have the required surface texture and cleanliness for further processing. Wet blasting’s versatility makes it suitable for a wide range of manufacturing materials and applications.
Â
Marine Industry
Â
The marine industry utilizes wet blasting for maintaining and repairing ships and marine equipment. This method effectively removes barnacles, rust, and old coatings from ship hulls. For example, it’s often used in refurbishing old vessels, helping to extend their service life and maintain their structural integrity. Wet blasting is less abrasive than traditional methods, preserving the integrity of the ship’s metal.
Automotive Industry
Aerospace Industry
Manufacturing and Metal Fabrication
Marine Industry
4 Things to Consider When Choosing Wet Blasting Services
#1 Advanced Equipment and Technology
When purchasing wet blasting services, it’s essential to assess the quality of the equipment and technology used. Zemetal’s services utilize advanced wet blasting machines with features like precise pressure controls and efficient abrasive recycling systems. Modern equipment ensures higher efficiency, better results, and can often handle a wider range of materials and surface conditions.
#2 Customization Capabilities
An ideal wet blasting service provider should offer customization options tailored to your specific needs. They should have the capability to adjust variables like pressure, abrasive type, and water flow to suit different materials and desired finishes. Customization ensures that the wet blasting process aligns perfectly with your project requirements, be it for delicate components or heavy-duty materials.
#3 Specialized Knowledge in Surface Finishing
When choosing a wet blasting service provider, prioritize those with specialized knowledge in surface finishing. Ideal providers should demonstrate a deep understanding of how different abrasives interact with various materials. They should be able to tailor the wet blasting process to achieve specific surface textures or prepare surfaces for subsequent treatments like painting or coating.
#4 Cost-Effectiveness
Cost-effectiveness is a significant consideration when purchasing wet blasting services. Compare the pricing of different providers, but also consider the value they offer in terms of quality and turnaround time. A lower upfront cost might not always translate to long-term savings if it compromises on quality or leads to frequent delays. Evaluate the total cost of ownership, including maintenance, operation, and potential downtime.
Dive Deeper Into Our Resources
Looking for more diverse service options? Browse through our handpicked selections:
Still haven’t found what you’re looking for? Don’t hesitate to contact us. We’re available around the clock to assist you.
Meet Our Best Sheet Metal Fabrication Laser Cutting Blanking Stamping Weilding Bending Services
Connect with Us
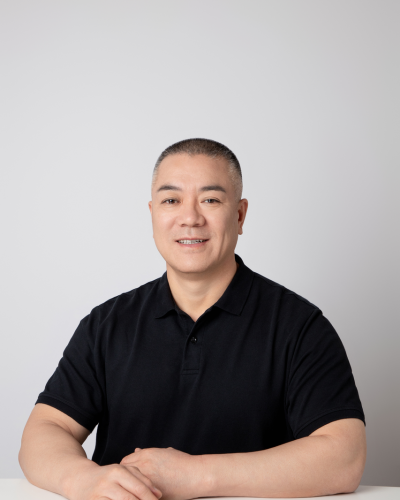
Zemetal is committed to ensuring your privacy and promises prompt, secure responses to all your inquiries.