Faced with the crucial decision of anodizing vs galvanizing for metal finishing? Businesses must consider how this choice impacts product durability and appearance.
As a specialist in metal fabrication services, I understand the complexities and impact of this choice. Your metal’s longevity and appearance depend on it.
Anodizing offers enhanced aesthetics and durability for a sleek finish, while galvanizing provides strong corrosion resistance, ensuring product longevity.
In this article, we’ll explore the pros and cons of both methods, helping you make an informed decision for your business needs.
Keep reading to explore anodizing style and durability and galvanizing corrosion resistance.
1. Importance of Metal Coatings
Metal coatings are crucial for protecting materials from environmental damage like rust, corrosion, and wear. These coatings, like anodizing and galvanizing, act as a shield, significantly prolonging the life of the metal. They also enhance the metal’s resistance to harsh conditions, ensuring it remains durable and reliable for various applications. It’s like giving metal armor to face the world’s challenges.
The significance of metal coatings is also reflected in their market demand. According to Vantage Market Research, the global metal coatings market is valued and projected to grow at a CAGR of 6.5% over the forecast period. This growth is driven by the increasing demand for durable and long-lasting metal products in various industries. It shows how vital these coatings are in our ever-evolving industry.
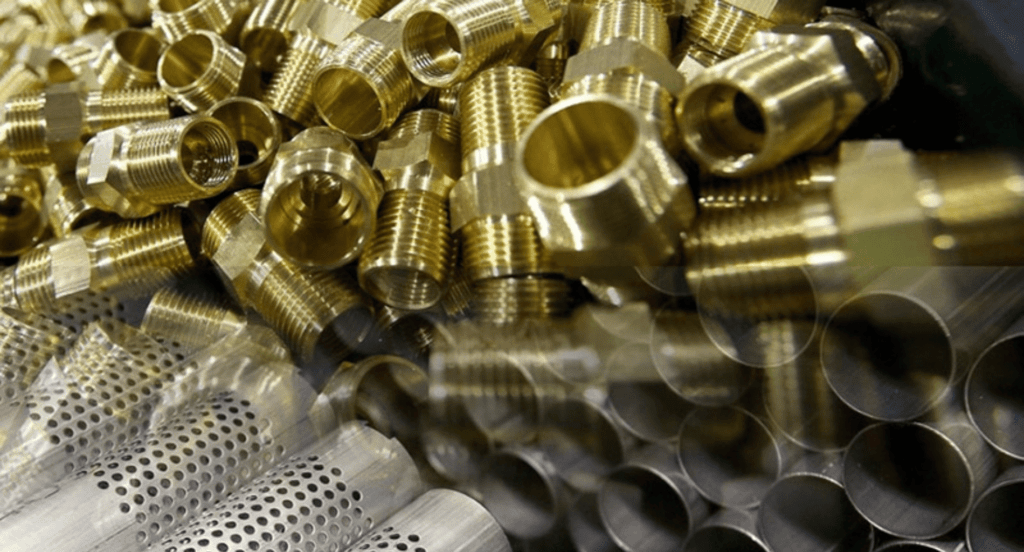
2. Understanding Anodizing
Anodizing is an electrochemical procedure that transforms the metal surface into a tough, corrosion-resistant anodic oxide finish. This process is predominantly applied to aluminum, enriching the metal’s texture and providing an enhanced surface for further treatment. Anodizing is more than a process; it’s a gateway to innovation and creativity in metal usage.
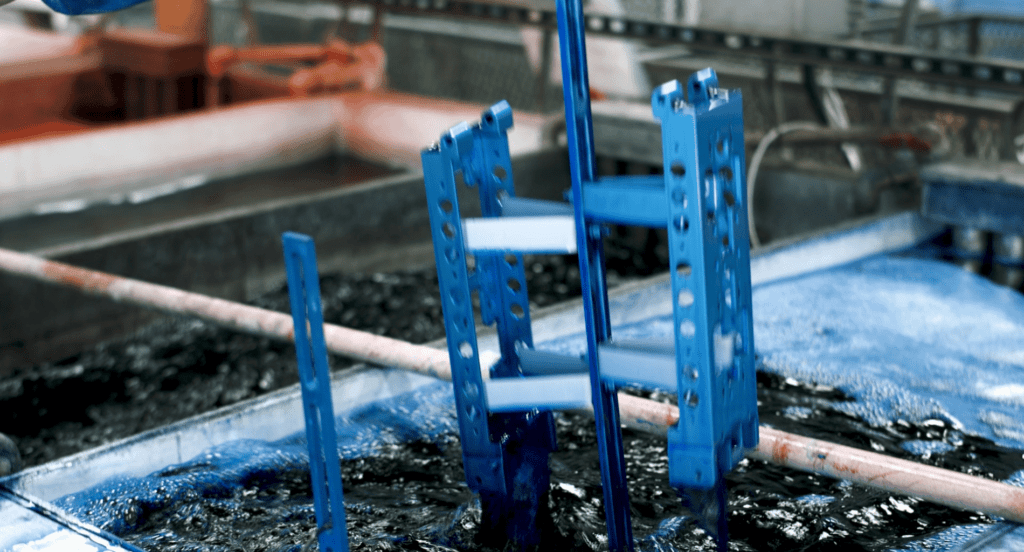
Benefits of Anodizing
- Increased Durability: Anodizing creates a hard, wear-resistant layer that prolongs the metal’s lifespan, making it resilient to daily wear and tear.
- Corrosion Resistance: It forms a protective barrier against rust and environmental damage, ensuring longevity and maintaining the metal’s integrity over time.
- Aesthetic Appeal: Anodizing allows for a variety of colors and finishes, making it versatile for design purposes and enabling customization to suit any style.
- Improved Adhesion: It provides an excellent foundation for subsequent paint and coating applications, enhancing overall quality and ensuring a long-lasting finish.
Applications of Anodized Metals
- Architectural Structures: Used for creating weather-resistant and aesthetically pleasing building surfaces, anodizing is particularly favored in facade and roofing applications for its visual appeal and endurance.
- Aerospace Components: Essential for parts where strength, durability, and light weight are paramount, anodizing is crucial in enhancing the performance and longevity of aerospace materials.
- Consumer Electronics: Ideal for giving gadgets a sleek, durable, and attractive finish, anodizing is widely used in mobile phones, laptops, and other personal devices for its premium look and feel.
- Kitchenware: Safe and resilient, perfect for long-lasting cooking equipment, anodized materials are also preferred for their non-toxic and heat-resistant properties, making them ideal for culinary use.
3. Exploring Galvanizing
Galvanizing involves coating steel or iron with a layer of zinc, primarily through hot-dip galvanizing, where metals are submerged in molten zinc. This process not only prevents rusting but also enhances the metal’s overall resilience against environmental factors. Galvanizing not only preserves but also empowers metals to withstand the test of time and nature.
Benefits of Galvanizing
- Exceptional Corrosion Protection: Offers a robust defense against rust, greatly extending the life of metal structures in various environments.
- Longevity: The galvanized coating significantly extends the lifespan of metal structures, making them a reliable choice for long-term projects.
- Economical: It’s cost-effective in the long run due to reduced maintenance and replacement costs, offering great value for money.
- Sustainable: Zinc, used in galvanizing, is recyclable and environmentally friendly, aligning with eco-conscious manufacturing practices.
Applications of Galvanized Metals
- Infrastructure: Widely used in constructing durable bridges, railings, and public utilities that withstand harsh conditions.
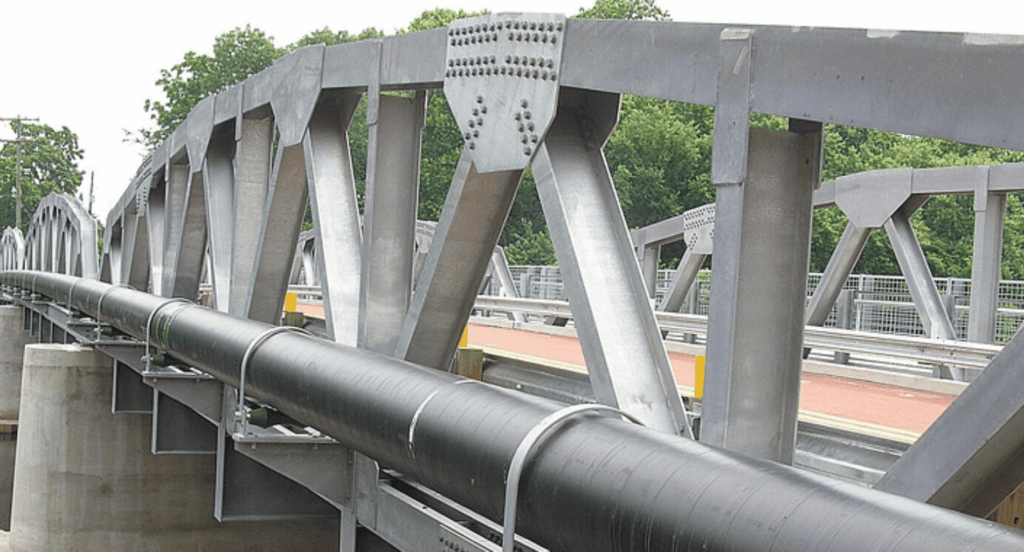
- Automotive Industry: Critical for vehicle bodies and components, ensuring they resist rust and maintain structural integrity.
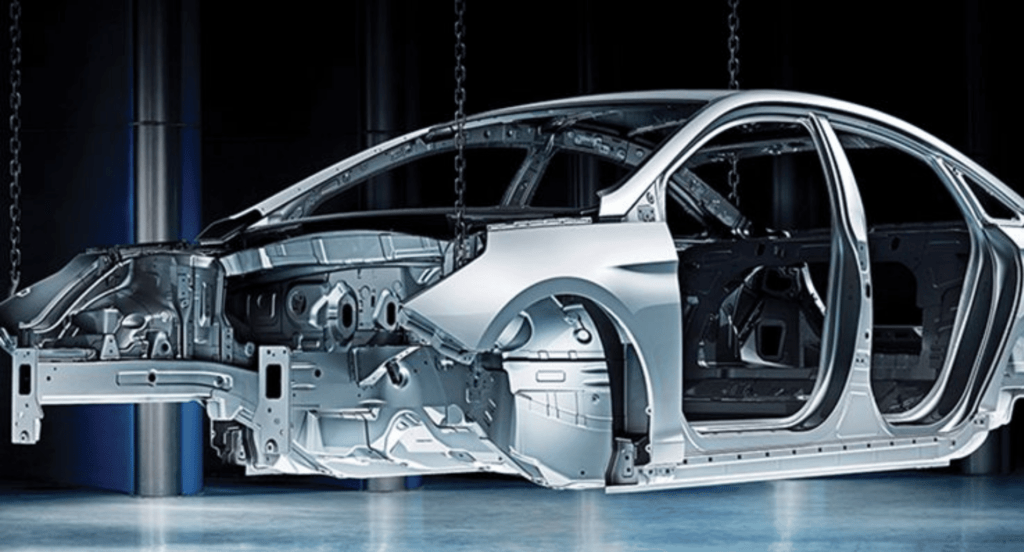
- Outdoor Constructions: Perfect for fences, balconies, and gates, providing long-lasting protection against weather elements.
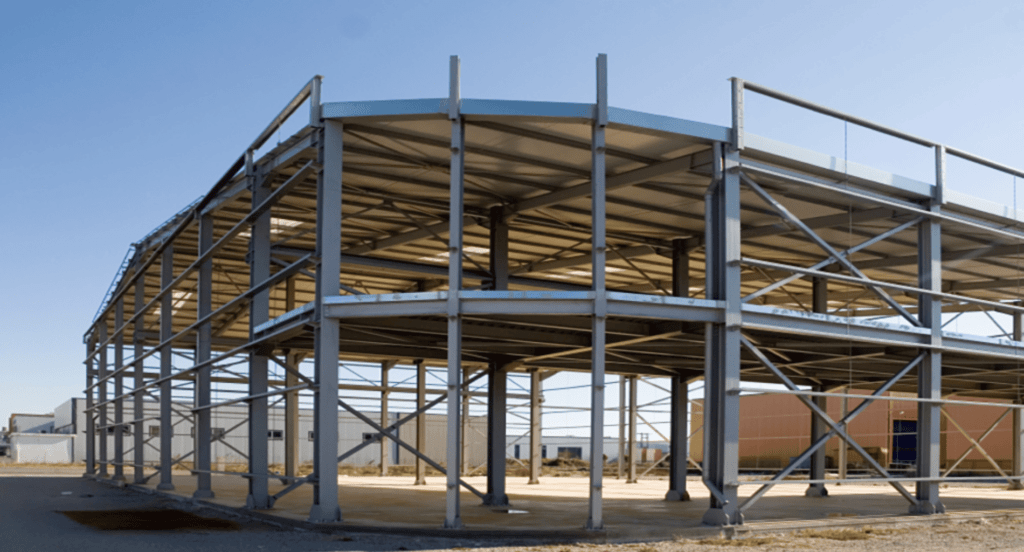
- Agricultural Equipment: Protects machinery and structures in challenging farm environments, enhancing their durability and functionality.
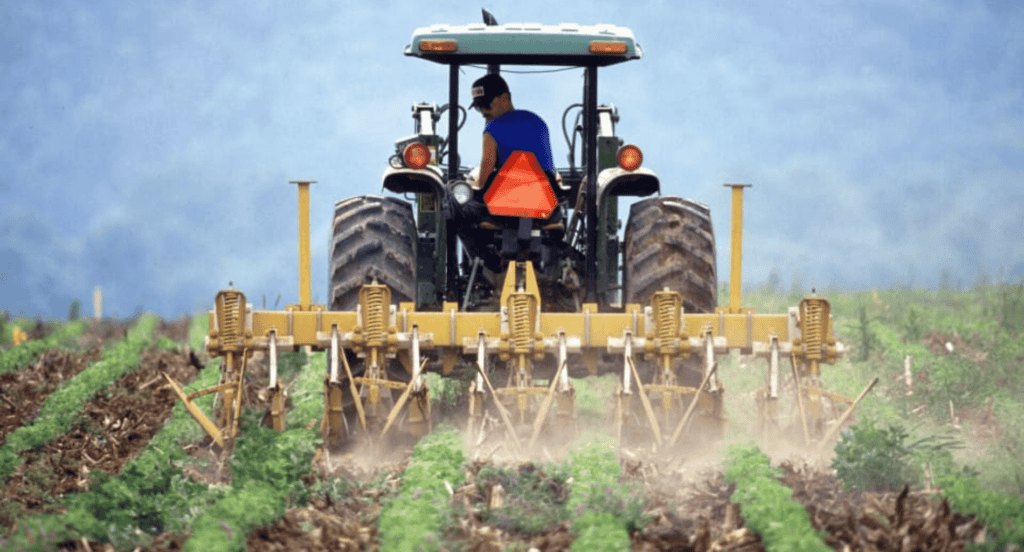
4. Anodizing vs. Galvanizing: A Comparative Analysis
Following our exploration of galvanizing, it’s time to compare it with anodizing in a comparative analysis. Below are the aspects where the difference between anodizing and galvanizing is shown:
Process Differences
Anodizing involves an electrochemical process that enhances the natural oxide layer, primarily on aluminum. In contrast, galvanizing coats iron or steel with a layer of zinc through hot-dipping or electroplating. Each process has its unique approach and suitability depending on the metal type. It’s like choosing the perfect outfit for your metal – each method dresses it up differently.
Analogous to choosing outfits, anodizing and galvanizing methods ‘dress up’ metals distinctively, as depicted in the table below.
Metal Type | Anodizing | Galvanizing |
Aluminum & Alloys | Enhances natural oxide layer, providing durability. | Coats with a layer of zinc, offering corrosion resistance. |
Iron & Steel | Not applicable; primarily suited for aluminum. | Protects against corrosion through zinc coating. |
Copper & Brass | Not commonly applicable due to the electrochemical process specifics. | Galvanizing is rare due to metal composition. |
Stainless Steel | Limited application due to its natural corrosion resistance. | Galvanizing uncommon due to the steel’s inherent properties. |
Zinc | Not necessary; zinc is already highly resistant to corrosion. | Not typically applicable as it’s already zinc-coated or composed of zinc. |
Durability and Protection
While both anodizing and galvanizing improve durability, their protection levels vary. For example, anodizing provides a hard, wear-resistant surface ideal for aluminum, whereas galvanizing offers superior rust protection for steel and iron. This difference in protection makes each process suitable for specific environmental and functional requirements.
Aesthetic and Design Flexibility
Anodizing stands out for its aesthetic versatility, offering a range of colors and finishes, making it perfect for projects where visual appeal is a priority. Galvanizing, on the other hand, is more limited in appearance but gives a consistent, rugged look that’s ideal for industrial applications, especially where functionality takes precedence over aesthetics.
Environmental Impact
Both processes have different environmental impacts. Anodizing is generally more environmentally friendly and produces less hazardous waste compared to galvanizing, which involves the use of zinc and potentially toxic air pollutant. Zemetal, a leading company in the industry, has been actively working towards making galvanizing more eco-friendly through innovative techniques.
Cost Considerations
In terms of cost, anodizing can be more expensive due to its aesthetic options and the complexity of the process, which might impact smaller projects with limited budgets. Galvanizing is often more economical, especially for large-scale industrial projects where durability is the primary concern and cost-effectiveness is crucial.
5. 5 Factors to Consider When Choosing Between Anodizing and Galvanizing
After our detailed comparative analysis, it becomes clear that choosing between anodizing and galvanizing requires careful consideration. Below are the key factors to consider when choosing between anodizing and galvanizing:
#1 Type of Metal
Anodizing is specifically suited for aluminum and its alloys, enhancing its natural oxide layer, perfect for applications like aluminum window frames or automotive parts. Galvanizing, however, is ideal for steel and iron, providing robust protection against rust, which is crucial for structures like steel bridges or outdoor railings.
#2 Environmental Exposure
Consider the environment in which the metal will be used. Anodizing is preferable for metals exposed to abrasive conditions, while galvanizing is better for metals that need to withstand outdoor elements, especially moisture. Zemetal often recommends galvanizing for outdoor constructions due to its superior resistance to weather-induced corrosion.
#3 Aesthetic Requirements
If aesthetic appeal and color customization are important, anodizing offers more versatility, allowing for a broad spectrum of colors and finishes to match specific design requirements. For instance, for projects where appearance is less critical, and a rugged, industrial look is acceptable, galvanizing is a suitable choice, offering a classic, metallic finish that is both practical and durable.
#4 Long-Term Maintenance and Durability
Evaluate the longevity and maintenance requirements of the finish. Anodizing typically requires less maintenance but may be less durable in harsh conditions, whereas galvanized metals are very durable but may require periodic inspection and maintenance. Making the right choice between anodizing and galvanizing can significantly impact the performance and longevity of your metal products.
#5 Cost Implications
Lastly, consider the budget. Anodizing can be more costly due to its elaborate process and customization options, making it a preferred choice for specialized, high-end applications or smaller projects where unique aesthetics are paramount. In contrast, galvanizing is generally more budget-friendly, especially for large-scale or industrial applications, where the sheer volume and functional requirements make cost-efficiency crucial.
Conclusion
In conclusion, understanding the differences between anodizing and galvanizing is vital for making informed decisions in metal fabrication. This guide aims to assist businesses in selecting the right finishing process for their specific needs.
If you’re considering anodizing or galvanizing for your next project, Zemetal is here to provide expert guidance and high-quality services. For more information or to discuss your project, please contact us today.
Dive Deeper Into Our Resources
Looking for more diverse service options? Browse through our handpicked selections:
- Discover the
- secret to succe
- ss with Nako Co
- smetic case st
- udies. From a
- nalyzing clien
- t needs to overcoming c
- hallenges, see
- how we’ve he
For some insightful reads, we’ve curated a list of recommended articles just for you:
Still haven’t found what you’re looking for? Don’t hesitate to contact us. We’re available around the clock to assist you.