Are you constantly on the hunt for the most efficient and cost-effective brass sheet for your deep drawing needs? Selecting the right brass sheet is not just a technical decision; it’s a business strategy that impacts your bottom line.
As a seasoned expert in the metal fabrication industry, I understand the critical role material selection plays in manufacturing success. My insights are grounded in years of hands-on experience and a deep understanding of the metal fabrication market.
Here is a sneak peek at 2 of the most effective brass types for deep drawing:
- Cartridge Brass (C26000)
- Yellow Brass (C26800)
In this guide, we will explore the unique properties of the 10 types of brass sheets, highlighting why they stand out as top choices for deep drawing applications.
To unlock the potential of these materials, keep reading.
1. Cartridge Brass (C26000)
Cartridge brass, designated as C26000, is a brass alloy known for its high ductility and strength. It contains about 70% copper and 30% zinc, a composition that grants it superior formability. This alloy is particularly favored in the metal fabrication industry for its versatility and durability.
Characteristics
- High Ductility: Cartridge brass boasts remarkable ductility, making it highly malleable under pressure. This property is essential for manufacturing processes that involve intricate shaping, such as deep drawing or bending. Its ability to withstand significant deformation without cracking ensures its suitability for complex fabrications.
- Excellent Corrosion Resistance: One of the key strengths of cartridge brass is its resistance to corrosion. It maintains its integrity over time, ensuring the longevity of components made from this material. Zemetal utilizes cartridge brass in their metal fabrication services for this reason, ensuring durable and long-lasting metal products.
- Good Conductivity: While not as conductive as pure copper, cartridge brass still exhibits good electrical and thermal conductivity. This characteristic is beneficial in components that require a certain level of heat or electrical transmission. It strikes a balance between functionality and cost-effectiveness in such applications.
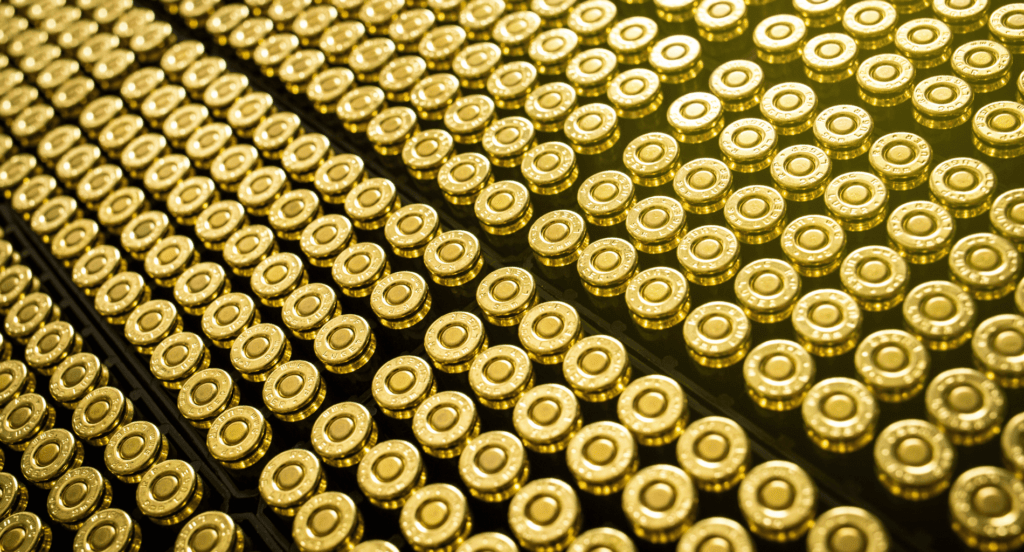
2. Yellow Brass (C26800)
Yellow Brass, identified as C26800, is a widely used brass alloy characterized by its distinctive yellow color. It is composed of roughly 65% copper and 35% zinc, a blend that offers a balance between strength and ductility. This alloy is especially popular in applications that require both aesthetic appeal and functional durability.
Characteristics
- Strength and Ductility Balance : Yellow brass strikes a perfect balance between strength and ductility, which is crucial for deep drawing processes. This balance allows the material to be stretched into complex shapes without losing its structural integrity. It’s particularly useful in applications where both form and function are critical.
- Excellent Surface Finish: One of the notable features of yellow brass is its ability to achieve a superior surface finish. When deep drawn, it maintains a smooth and consistent surface, which is essential for both aesthetic and practical applications. This quality reduces the need for extensive finishing work, saving time and resources.
- Resistance to Cracking: During the deep drawing process, yellow brass exhibits a high resistance to cracking. This resilience is vital for creating precise and reliable components, especially when working with intricate designs. Its ability to maintain shape under stress ensures fewer defects and a higher quality end product.
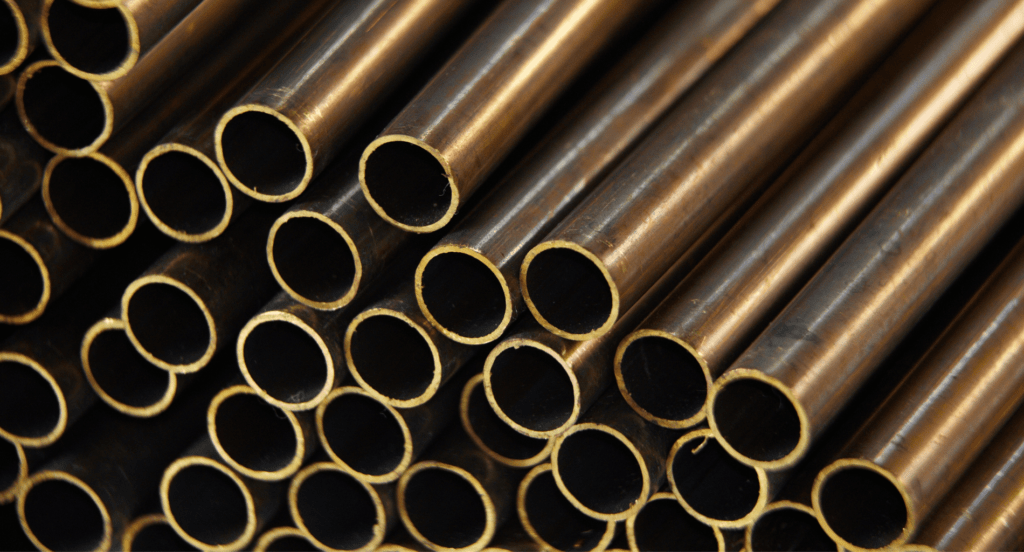
3. Naval Brass (C46400)
Naval brass, designated as C46400, is a highly durable brass alloy renowned for its strength and corrosion resistance, particularly in marine environments. This alloy typically comprises 60% copper, 39.2% zinc, and a small percentage of tin, enhancing its resistance to seawater corrosion. It’s a preferred material in applications demanding both resilience and exposure to harsh conditions.
Characteristics
- Exceptional Corrosion Resistance: The standout feature of naval brass is its exceptional resistance to corrosion, especially against saltwater. This quality is crucial in maritime applications where materials are constantly exposed to harsh, corrosive environments.
- High Tensile Strength: Naval brass is known for its high tensile strength, making it capable of withstanding significant stress without deformation. This strength is vital in Zemetal’s deep drawing processes, as it allows the material to be stretched and formed into complex shapes without compromising its structural integrity.
- Good Malleability and Ductility: Naval brass’ good malleability and ductility are essential for deep drawing. These enable the material to be shaped into detailed forms without cracking or breaking. This balance of strength and flexibility makes it versatile for various fabrication methods.
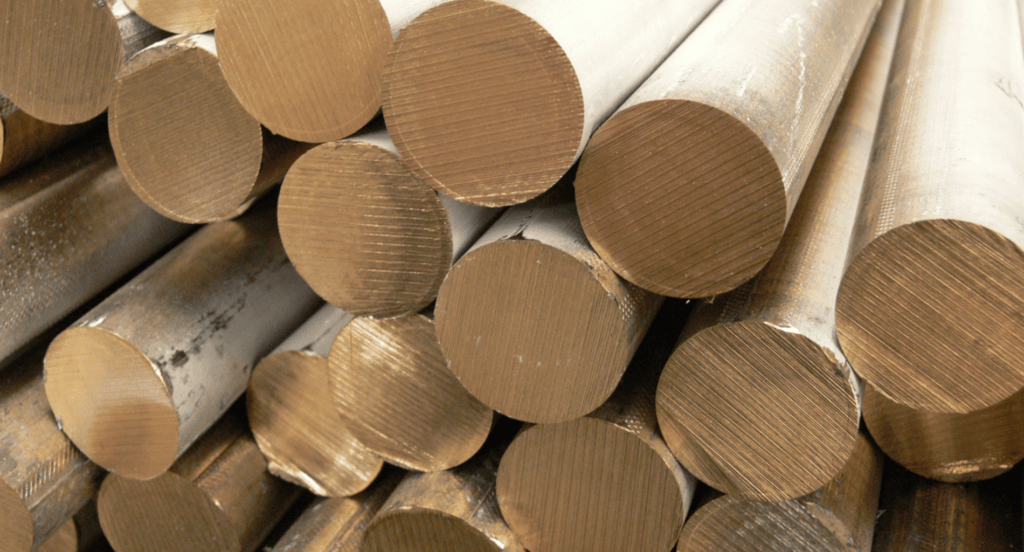
4. Free Cutting Brass (C36000)
Free cutting brass, known as C36000, is a brass alloy specifically engineered for high machinability without compromising strength. It typically consists of around 61.5% copper, 35.5% zinc, and a small percentage of lead, which enhances its cutting properties. This alloy is renowned for its ease of use in machining operations, making it a popular choice in various fabrication processes.
Characteristics
- High Machinability: The defining characteristic of free cutting brass is its exceptional machinability. The presence of lead in the alloy creates a dispersed microstructure, allowing for easier cutting and shaping. This property is particularly beneficial in high-speed machining processes, reducing wear on tools.
- Good Strength and Ductility: Despite its ease of machining, free cutting brass does not sacrifice strength or ductility. These properties are vital for deep drawing, as they allow the material to be formed into complex shapes without losing its structural integrity.
- Fine Surface Finish: Free cutting brass is capable of achieving a fine surface finish, an essential attribute for aesthetic purposes. After deep drawing, the material presents a smooth and clean surface, minimizing the need for additional finishing. This quality is advantageous for components where surface appearance is as important as performance.
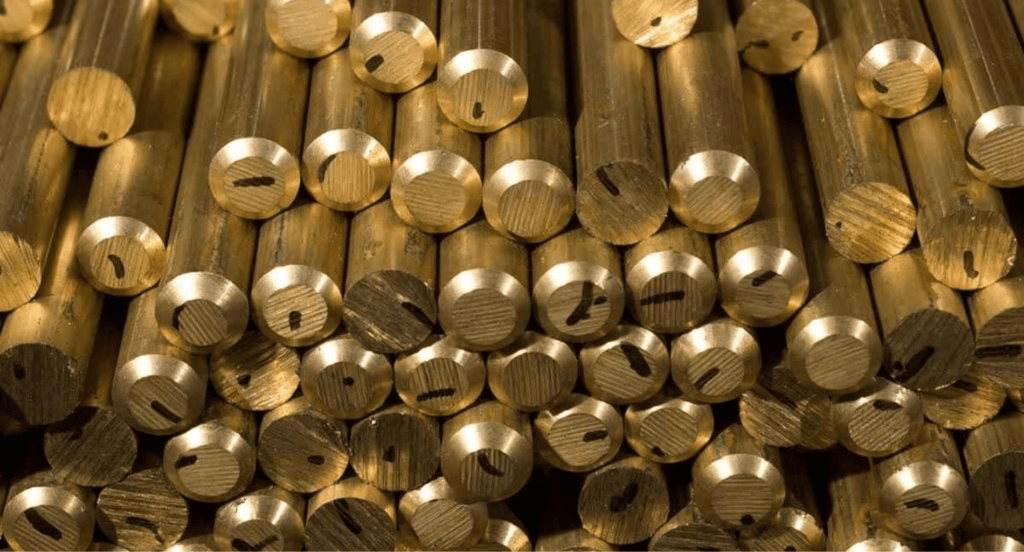
5. High Tensile Brass (C67820 or C68800)
High tensile brass, with designations C67820 or C68800, is an alloy known for its exceptional strength and resilience. This brass type typically contains a combination of copper, zinc, and small amounts of aluminum, iron, and manganese, which significantly enhance its tensile strength. It’s engineered for applications where durability and resistance to wear are paramount.
Characteristics
- Outstanding Tensile Strength: The primary attribute of high tensile brass is its superior tensile strength, which is significantly higher than standard brasses. This strength is crucial for deep drawing processes, as it allows the material to endure high levels of stress without failing.
- Excellent Wear Resistance: High tensile brass exhibits remarkable wear resistance, a vital feature for parts exposed to friction and abrasion. This durability ensures that components retain their integrity and functionality over extended periods, even under demanding conditions.
- Good Corrosion Resistance: In addition to its strength, this alloy also offers good corrosion resistance. It withstands environmental factors like moisture and chemicals, preserving its quality and appearance over time. This property is essential for components used in harsh or variable environments.
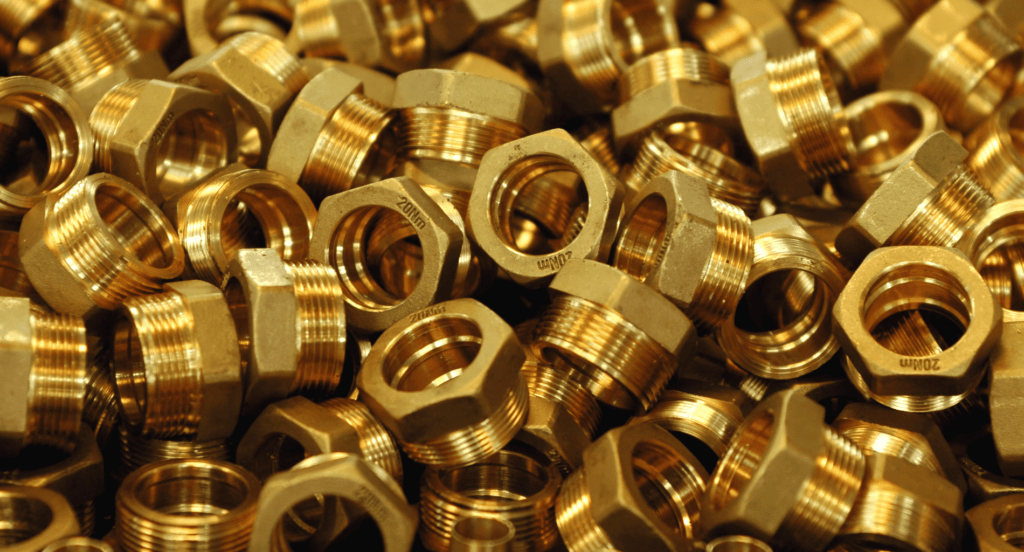
6. Manganese Brass (C67500)
Manganese brass, designated as C67500, significantly enhances the alloy’s strength and resistance to wear. According to Medium, this material contains a high content of manganese, typically ranging from 10% to 40% It’s favored for its combination of durability and formability, making it a versatile material in various demanding applications.
Characteristics
- Enhanced Strength and Hardness: Manganese brass is characterized by its increased strength and hardness, thanks to the manganese content. This enhanced durability makes it suitable for deep drawing, as it can withstand the high stress and strain involved in this process.
- Resistance to Corrosion and Erosion: This alloy exhibits a good resistance to both corrosion and erosion. For instance, the presence of manganese improves its ability to withstand environmental factors like moisture and chemicals. This quality is crucial for parts used in corrosive environments, ensuring their longevity and reliability.
- Improved Wear Resistance: Another key feature of manganese brass is its improved wear resistance. This trait is particularly beneficial in applications involving repeated mechanical contact or friction. The material maintains its dimensions and functionality over time, reducing the need for frequent maintenance or replacement.
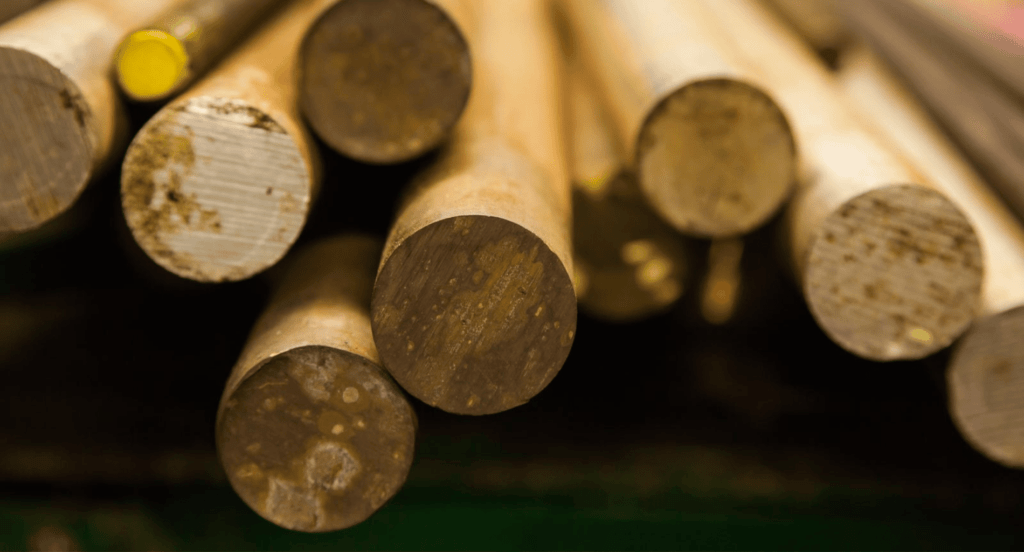
7. Eco Brass (C69300)
Eco Brass, referred to as C69300, is an environmentally friendly brass alloy, notable for being lead-free. It primarily consists of copper, zinc, and a small amount of silicon, which enhances its machinability and strength. This alloy is gaining popularity due to its reduced environmental impact and compliance with stricter health and safety standards.
Characteristics
- Lead-Free Composition: The defining feature of eco brass is its lead-free composition, making it safer for use in applications where lead contamination is a concern. This aspect is particularly important in potable water systems and food-related applications, aligning with health and environmental regulations.
- Excellent Machinability and Formability: Despite being lead-free, eco brass maintains excellent machinability and formability. These properties are essential for deep drawing, allowing the material to be shaped into complex forms without compromising its integrity.
- Good Corrosion Resistance: Eco brass offers good corrosion resistance, making it durable in various environments. This trait ensures the longevity of components, especially in applications exposed to corrosive substances or conditions. Its resistance to corrosion also contributes to its overall sustainability.
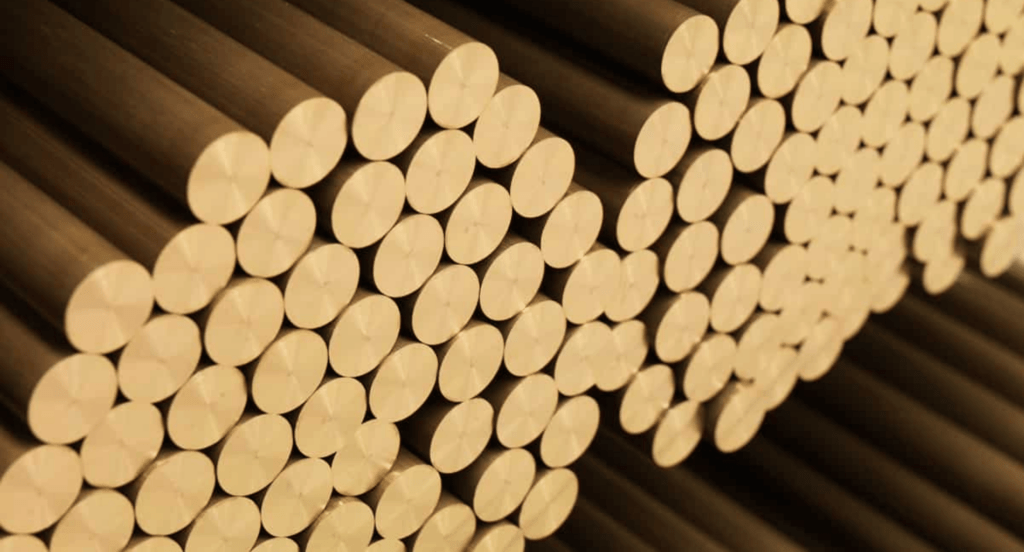
8. Dezincification Resistant Brass
Dezincification resistant brass is a specialized brass alloy formulated to resist dezincification, a process where zinc is leached out from the brass in corrosive environments. This type of brass typically contains elements like arsenic, antimony, or phosphorus, which enhance its resistance to corrosion and zinc loss. It is specifically engineered for applications where standard brass would suffer degradation due to chemical exposure.
Characteristics
- Enhanced Corrosion Resistance: The key attribute of dezincification resistant brass is its heightened resistance to corrosion, especially in environments prone to causing dezincification. This property is crucial for maintaining the integrity and longevity of components in corrosive conditions.
- Good Strength and Ductility: Despite its specialized composition, this brass maintains good strength and ductility. These characteristics are essential for deep drawing, as they allow the alloy to be formed into complex shapes without cracking or losing strength.
- Stability in Varied Environments: Dezincification resistant brass exhibits stability in a wide range of environmental conditions. For example, its ability to withstand different types of corrosion makes it versatile for use in various industries. This stability is especially important in applications where the material is exposed to fluctuating or extreme conditions.
This table highlights the key features of dezincification resistant brass, focusing on its corrosion resistance and stability in varied environmental conditions, and outlines its importance across multiple industries, especially in applications exposed to harsh or fluctuating conditions.
Feature | Description | Importance in Industries |
Corrosion Resistance | Withstands different types of corrosion such as pitting, crevice, and stress corrosion. | Essential in marine, chemical, and industrial applications where corrosion resistance is crucial. |
Stability in Fluctuating Conditions | Maintains integrity in environments with varying temperatures and humidity. | Vital for use in outdoor applications, HVAC systems, and construction. |
Resistance to Extreme Conditions | Performs well under high pressure and temperature extremes. | Important in aerospace, automotive, and oil & gas industries for reliable performance. |
Versatility | Suitable for a wide range of applications due to its stability. | Enables use in diverse sectors, from plumbing and water treatment to electrical and electronic components. |
Longevity | Longer lifespan in challenging environments. | Reduces maintenance and replacement costs, beneficial for infrastructure and industrial applications. |
9. Lead-Free Brass
Lead-Free Brass is a type of brass alloy that omits lead from its composition, making it safer and more environmentally friendly. This alloy typically includes copper, zinc, and often elements like silicon or bismuth to enhance its mechanical properties. It’s increasingly favored in industries where lead exposure can be a concern, particularly in potable water systems and consumer goods.
Characteristics
- Health and Safety Compliance: The most significant feature of lead-free brass is its compliance with health and safety regulations regarding lead content. This aspect is crucial in applications where lead contamination poses a risk, such as in drinking water systems or food-related products.
- Maintained Machinability and Formability: Despite the absence of lead, lead-free brass retains good machinability and formability. These properties are essential for deep drawing processes, allowing the material to be shaped into intricate forms without compromising its structural integrity.
- Good Corrosion Resistance: Lead-free brass also offers good corrosion resistance, an important trait for maintaining the longevity and functionality of components. This resistance to corrosion is particularly beneficial in applications exposed to water or other potentially corrosive substances.
10. Phosphor Bronze
Phosphor bronze is an alloy consisting primarily of copper with a significant addition of tin and a small amount of phosphorus. The phosphorus acts as a deoxidizing agent and improves the alloy’s strength, toughness, and wear resistance. This alloy is renowned for its excellent mechanical properties and corrosion resistance, making it a popular choice in various demanding applications.
Characteristics
- High Fatigue Resistance: Phosphor bronze is notable for its high fatigue resistance, an essential quality for components subjected to repetitive stress. This endurance makes it suitable for deep drawing, as it can withstand the repeated cycles of forming and shaping without losing its mechanical properties.
- Excellent Elasticity: The alloy is characterized by its excellent elasticity, which is crucial for maintaining the shape and form of deep-drawn components. This elasticity allows the material to return to its original shape after being stretched or compressed, making it ideal for spring-like components.
- Superior Corrosion Resistance: Phosphor bronze also exhibits superior corrosion resistance, especially against atmospheric, seawater, and chemical corrosion. This resilience is vital for components used in harsh or outdoor environments, ensuring their longevity and reliability over time.
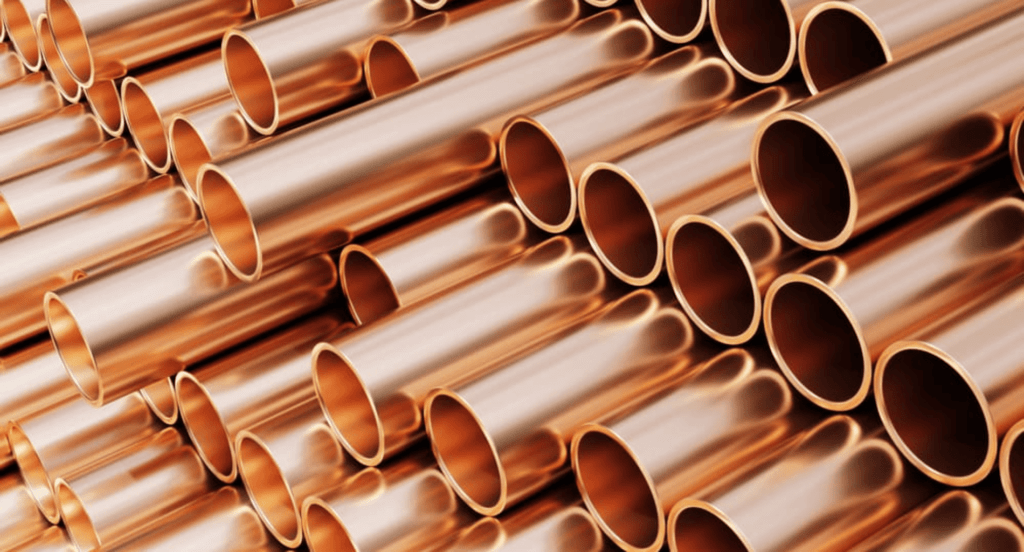
Conclusion
This guide offers a comprehensive overview of various brass types suitable for deep drawing, each with unique properties and applications. Understanding these differences can significantly aid in choosing the right material for your specific needs, enhancing both quality and efficiency.
For businesses seeking a more detailed discussion on selecting the ideal brass sheet for deep drawing, Zemetal is here to assist. Contact us to explore the best options tailored to your unique requirements.
Dive Deeper Into Our Resources
Looking for more diverse service options? Browse through our handpicked selections:
Still haven’t found what you’re looking for? Don’t hesitate to contact us. We’re available around the clock to assist you.