Ever wondered what goes into shaping the metal components we use daily? The answer lies in the meticulous sheet metal fabrication process.
Understanding this process is crucial for businesses and professionals in the metal industry.
The sheet metal fabrication process is an intricate journey from raw metal to a finished product. It involves various steps, ensuring the final product meets specific standards and functions.
In this article, we’ll explore the nine vital steps in sheet metal fabrication, providing valuable insights for businesses and industry professionals.
Keep reading into the fascinating world of metal transformation.
Step #1: The Design Phase
The beginning of the sheet metal fabrication journey is marked by the critical design phase, which establishes the basis for the future production of a tangible metal item. It’s also important to mention that, according to Market Research, the global market for sheet metal fabrication services is expanding at a compound annual growth rate (CAGR) of 3.1%. Here are four key points outlining how the design process unfolds:
- Conceptualization: The process starts with an idea or a need. This could be a new product, a part of a larger assembly, or a custom solution for a specific requirement. Designers and engineers brainstorm, discussing functionalities, dimensions, and the overall purpose of the piece.
- Design Software Utilization: Utilizing advanced computer-aided design (CAD) software, designers create detailed and precise drawings of the product. This software allows for the manipulation of dimensions and shapes, ensuring that the final design is both practical and manufacturable.
- Material Selection: Based on the product’s intended use, environment, and required durability, the appropriate sheet metal material is selected. This could range from aluminum and stainless steel to brass and copper, each offering different characteristics.
- Feasibility Analysis: Before finalizing the design, a feasibility study is conducted. This includes assessing the design for manufacturability, considering factors like cost-effectiveness, material availability, and the complexity of the fabrication steps required.
Step #2: Material Selection
Following the design phase in sheet metal fabrication, the next critical step is selecting the appropriate material. Here are three key aspects of how material selection is carried out:
- Evaluating Material Properties: The chosen material must align with the specific requirements of the product. This includes considering factors like strength, weight, corrosion resistance, and thermal conductivity. For instance, stainless steel might be chosen for its durability and corrosion resistance, while aluminum could be preferred for its lightweight and malleability.
- Considering the Application Environment: The environment where the product will be used plays a significant role in material selection. Outdoor applications may require materials with higher corrosion resistance, like galvanized steel, whereas indoor applications might allow for more variety in material choices.
- Budget and Availability: Cost-effectiveness and material availability are also crucial considerations. The selection process involves balancing the quality and characteristics of the material with the project’s budget constraints and the availability of the material in the market.
Step #3: Cutting the Metal
After meticulous material selection, the next stage in sheet metal fabrication is cutting the metal into the desired shape and size as per the design specifications. This step is vital for setting the foundation of the final product. Here are three key steps in the metal cutting process:
- Transferring Design to Metal: The precise measurements and patterns from the design phase are transferred onto the selected sheet metal. This is often done using computer-aided manufacturing (CAM) software, which ensures accuracy and minimizes the risk of errors.
- Choosing the Cutting Method: Depending on the thickness of the metal and the complexity of the design, an appropriate cutting method is selected. Common techniques include laser cutting for its precision and efficiency, waterjet cutting for complex shapes, or traditional methods like shearing for simpler cuts.
- Executing the Cut: The chosen cutting technique is then applied to the metal. This process must be carried out with precision and care to ensure clean edges and accurate dimensions, which are crucial for the subsequent steps in the fabrication process.
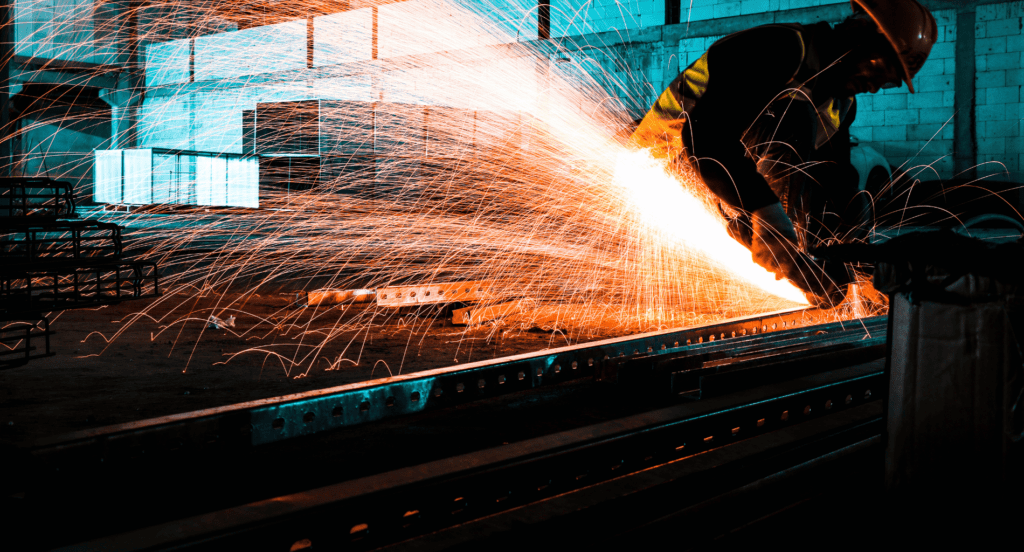
Step #4: Forming and Shaping
After the precise cutting of metal sheets, the subsequent stage in sheet metal fabrication is the forming and shaping process. This phase is essential for giving the flat metal pieces their desired three-dimensional form. Here’s how this process unfolds step by step:
- Bending as the Initial Step: The first step in shaping is typically bending. For example, this involves using press brakes or similar machinery to fold the metal at predetermined angles. The accuracy of this bending process is crucial, as it sets the foundation for the overall shape of the final product.
- Rolling for Curves and Cylinders: Following bending, rolling is often employed, especially when the design calls for cylindrical shapes or curves. In this step, the metal sheet is gradually formed into the desired curve by passing it through rollers that exert controlled pressure.
- Stamping for Detailed Shapes: Then, the metal may undergo stamping. At Zemetal, this process is particularly useful for intricate shapes, patterns, or textures. The metal is placed in a press, where a die stamps the metal into a specific shape in a single powerful motion.
- Stretching to Finalize the Shape: Finally, stretching is used if the metal needs to be elongated or formed over a complex shape, common in automotive and aerospace parts. This involves anchoring the metal sheet’s edges and stretching it over a form or die to achieve the final shape.
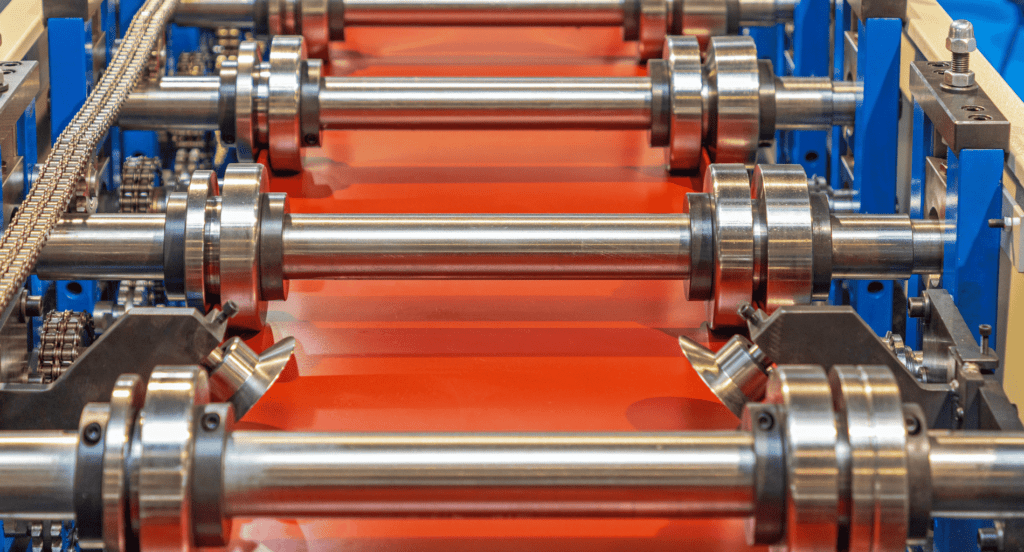
Step #5: Joining the Pieces
Following the forming and shaping of individual metal components, the next critical step in sheet metal fabrication is joining these pieces together. Here are the steps involved in the joining process:
- Alignment and Clamping: Initially, the formed metal pieces are meticulously aligned according to the design specifications. They are then clamped together to maintain their position. This step is crucial for ensuring that the pieces are joined accurately and that the final assembly matches the intended design.
- Welding: Once aligned and clamped, welding is the most common method used for joining the pieces. Various welding techniques, such as MIG, TIG, or spot welding, are selected based on the type of metal and the requirements of the project. This process involves fusing the metal pieces together by applying heat and, in some cases, additional metal.
- Riveting or Bolting for Non-Fused Joints: In cases where welding is not suitable or a non-permanent joint is required, riveting or bolting is used. These methods provide strong mechanical joins without permanently altering the metal structure, allowing for disassembly if needed.
Step #6: Finishing Touches
After the pieces of sheet metal have been expertly joined together, the focus shifts to the final phase: applying the finishing touches. This stage is critical for enhancing the appearance, durability, and functionality of the product. Here are the key steps in the continuous process of adding finishing touches:
- Grinding and Sanding: The first step in finishing involves grinding and sanding down any rough edges or weld marks left from the joining process. This smooths the surface and prepares it for further finishing, ensuring that the final product is not only functional but also aesthetically pleasing.
- Surface Treatment and Coating: Following the smoothing process, surface treatments are applied. This might include painting, powder coating, or anodizing, depending on the metal type and the intended use of the product. These coatings not only improve the visual appeal but also add a layer of protection against corrosion, wear, and tear.
- Quality Inspection and Testing: The final step in the finishing process is a thorough quality inspection and testing. This ensures that the final product meets all the design specifications, quality standards, and functional requirements. Any defects or issues are identified and rectified in this stage, guaranteeing that the product is ready for use or delivery.
Step #7: Assembly and Quality Control
With the finishing touches complete, the next crucial stage in sheet metal fabrication is the assembly of the components and rigorous quality control. Here are the key aspects of the assembly and quality control process:
- Assembly of Components: The first step involves carefully assembling the finished pieces into the final product. At Zemetal, this may include attaching additional parts, hardware, or accessories that were not part of the initial metal fabrication. The assembly process is guided by the project’s detailed design specifications to ensure accuracy.
- Comprehensive Quality Checks: After assembly, the product undergoes a series of quality control checks. These checks are designed to ensure that every aspect of the product, from dimensions and strength to functionality and appearance, aligns with the predefined standards and customer expectations.
- Functional Testing: The final step in this phase is functional testing, where the product is tested under conditions that mimic its intended use. This is to verify that it operates correctly, safely, and efficiently. Any issues found during testing are addressed and corrected to ensure the product’s reliability and longevity.
This table outlines the key aspects of functional testing, highlighting its role in verifying the correct, safe, and efficient operation of a product, as well as the importance of identifying and correcting any issues to ensure the product’s reliability and longevity.
Step | Description | Purpose |
Mimicking Intended Use | Testing the product under conditions similar to actual use. | Ensures the product performs as expected in real-world scenarios. |
Verifying Operation | Checking that the product operates correctly. | Confirms functionality and usability, aligning with design specifications. |
Safety Testing | Ensuring the product operates safely. | Prevents potential harm to users and meets safety standards. |
Efficiency Evaluation | Assessing the product’s efficiency during operation. | Guarantees optimal performance and resource utilization. |
Issue Identification and Correction | Detecting and addressing any problems found during testing. | Enhances the product’s reliability and longevity by resolving issues before release. |
Step #8: Packaging and Shipping
Following the assembly and stringent quality control processes, the sheet metal products are ready for the final stage: packaging and shipping. Here are the key steps involved in the packaging and shipping process:
- Secure Packaging: The first step is to securely package the assembled products to protect them during transit. This involves using appropriate materials like bubble wrap, foam, or custom crates, depending on the size, shape, and fragility of the products. The goal is to minimize movement and prevent damage, ensuring the product arrives in the same condition as it left the facility.
- Labeling and Documentation: Once packaged, each item is labeled with shipping and handling instructions. Additionally, essential documentation such as packing lists, invoices, and any necessary customs paperwork are prepared and attached. This step is vital for smooth logistics and compliance with shipping regulations.
- Choosing the Right Shipping Method: The final step involves selecting the most appropriate shipping method based on the destination, time frame, and nature of the products. Whether it’s local delivery, national shipping, or international freight, the choice of carrier and service level is crucial to ensure timely and safe delivery of the products.
Conclusion
As we’ve seen, each step in the sheet metal fabrication process is vital, contributing to the overall quality and functionality of the final product. From cutting and bending to assembly and finishing, understanding these steps helps businesses make informed decisions, ensuring quality and efficiency.
For businesses looking for top-notch metal fabrication services, look no further than Zemetal. Our team is dedicated to delivering precision, quality, and excellence in every project. Contact us today.
Dive Deeper Into Our Resources
Looking for more diverse service options? Browse through our handpicked selections:
Still haven’t found what you’re looking for? Don’t hesitate to contact us. We’re available around the clock to assist you.